- お役立ち記事
- The difference between Stereolithography (SLA) and Powder Bed Fusion
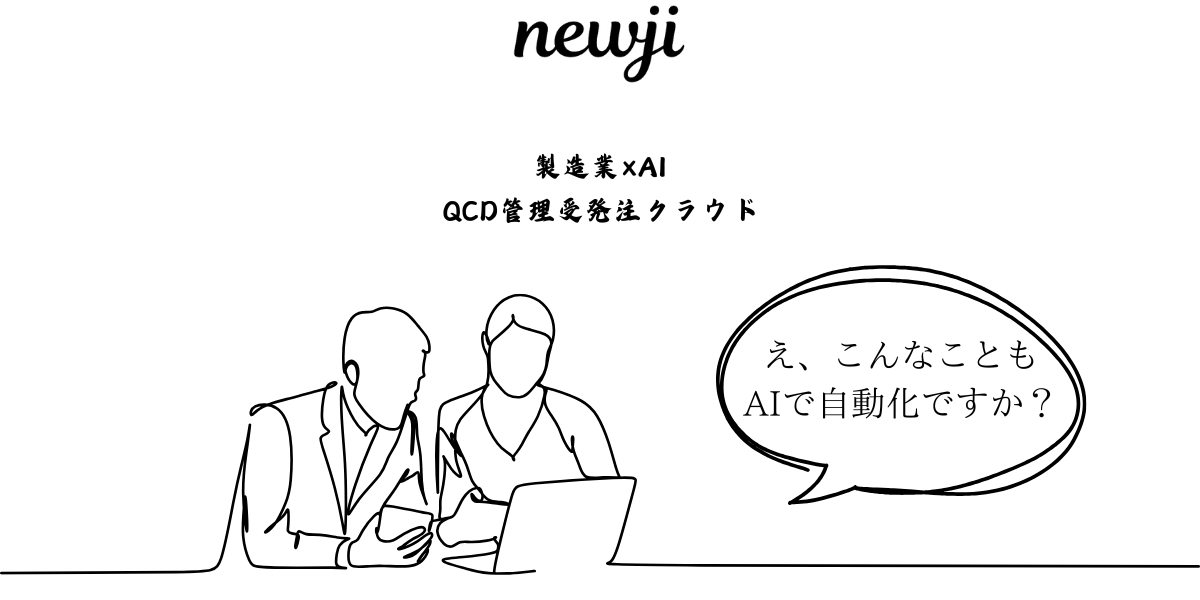
The difference between Stereolithography (SLA) and Powder Bed Fusion
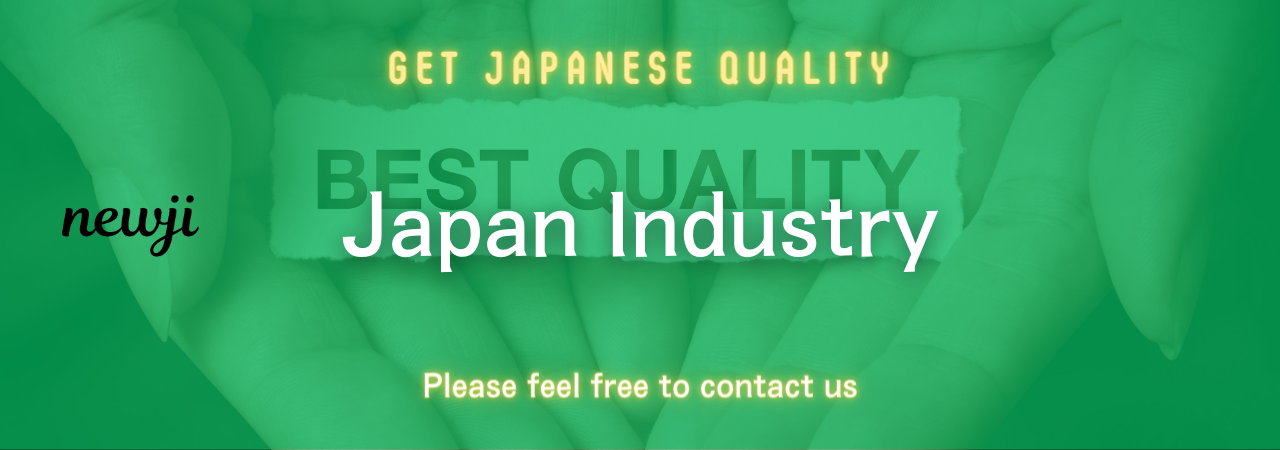
3D printing technology has transformed the manufacturing and prototyping industries by offering diverse methods to create objects with precision and efficiency.
Two of the most popular 3D printing methods are Stereolithography (SLA) and Powder Bed Fusion (PBF).
Although both techniques can produce outstanding results, they differ significantly in their processes, materials, and applications.
This article explores the differences between these two groundbreaking technologies.
目次
Understanding Stereolithography (SLA)
The Basics of SLA
SLA was one of the first 3D printing technologies developed and remains a top choice for creating high-resolution objects.
The process involves curing a liquid photopolymer resin layer by layer using a UV laser.
The UV light solidifies the resin precisely where the object is being formed, producing incredibly detailed and smooth surfaces.
Materials Used in SLA
SLA primarily uses liquid resin, which comes in a variety of types suited for different applications.
Common resins include standard, tough, flexible, and castable.
Each resin type offers unique properties like durability, elasticity, and the ability to burn out cleanly for casting processes.
Advantages of SLA
One of the major benefits of SLA is its ability to produce highly detailed and smooth objects.
This makes it particularly useful for applications requiring fine details, such as jewelry, dental models, and intricate prototypes.
Additionally, the range of resins available makes SLA versatile, catering to various needs from strength to flexibility.
Limitations of SLA
Despite its advantages, SLA has some limitations.
The process can be slower than other 3D printing methods, especially for larger objects.
Furthermore, the materials, specifically the resins, can be costly, and post-processing is often required to remove residual resin and support structures.
Also, SLA prints are generally less durable compared to those produced using other methods.
Understanding Powder Bed Fusion (PBF)
The Basics of PBF
Powder Bed Fusion (PBF) encompasses several 3D printing techniques such as Selective Laser Sintering (SLS), Direct Metal Laser Sintering (DMLS), and Electron Beam Melting (EBM).
The process begins with spreading a thin layer of powder material across a build platform.
A laser or electron beam then fuses the powder particles together, layer by layer, to create a solid object.
The build platform lowers after each layer, allowing a new layer of powder to be applied until the object is completed.
Materials Used in PBF
PBF can utilize a wide range of materials, including plastics, metals, and ceramics.
For example, SLS commonly uses nylon compounded with other materials for added properties, while DMLS and EBM are ideal for metals like titanium, stainless steel, and aluminum.
This flexibility in material usage makes PBF a go-to technique for industries that require strong and heat-resistant materials.
Advantages of PBF
One significant advantage of PBF is its ability to produce functional parts with excellent mechanical properties directly from the printer.
This makes PBF particularly valuable in aerospace, automotive, and medical industries, where parts must endure significant stress and high temperatures.
Another benefit is that PBF allows for the production of complex geometries that would be impossible to create using traditional manufacturing methods.
Limitations of PBF
However, PBF also has its downsides.
The equipment required for PBF can be very expensive, making it less accessible for smaller companies and individual users.
Additionally, the process can be time-consuming, particularly for large builds.
Post-processing steps such as removing excess powder and applying surface finishes can add to the time and cost.
Finally, while PBF parts are generally stronger, achieving highly detailed surface finishes and intricate details can be more challenging compared to SLA.
Comparing SLA and PBF
Precision vs. Strength
SLA excels in producing highly detailed and smooth objects.
Its precision makes it perfect for applications requiring intricate designs and tight tolerances, such as custom jewelry and detailed prototypes.
On the other hand, PBF shines when it comes to strength and functionality.
PBF-produced parts can withstand high mechanical stresses and temperatures, making this method suitable for functional components in aerospace and automotive industries.
Material Versatility
Both SLA and PBF offer versatility in terms of materials, but they differ fundamentally in the types of materials used.
SLA depends on photopolymer resins, which are available in various forms to meet different requirements.
PBF, contrastingly, can use a broader array of materials including metals, plastics, and ceramics.
This makes PBF more suitable for applications demanding materials with high mechanical properties.
Cost Considerations
Cost can be a crucial factor when choosing a 3D printing method.
SLA machinery and materials tend to be more affordable compared to PBF.
However, the overall cost of SLA may increase with the need for post-processing and the more frequent replacement of consumables.
PBF, although initially expensive due to high equipment costs, often becomes cost-effective for large-scale production runs and can produce parts with little to no post-processing required.
Build Speed and Size
When it comes to build speed and size, both methods have their strengths and weaknesses.
SLA can be slower, especially when printing larger objects or objects with high levels of detail.
PBF can handle larger builds more efficiently but may still take considerable time due to the layer-by-layer fusing process.
However, as PBF allows for nesting multiple parts within the build chamber, it can be advantageous for batch production.
Choosing the Right Technology for Your Needs
Determining whether SLA or PBF is the right choice depends largely on your specific needs and priorities.
If you require intricate details, smooth finishes, and a diverse range of resin types, SLA may be the best option for you.
However, if your project demands strong, functional parts with complex geometries made from durable materials, PBF might be the better choice.
Consider the size of your project, budget constraints, and the required material characteristics.
Both technologies have their place in modern manufacturing and prototyping, offering unique benefits and capabilities tailored to various applications.
By understanding the differences between SLA and PBF, you can make an informed decision and leverage the strengths of each method to achieve your desired outcome.
資料ダウンロード
QCD調達購買管理クラウド「newji」は、調達購買部門で必要なQCD管理全てを備えた、現場特化型兼クラウド型の今世紀最高の購買管理システムとなります。
ユーザー登録
調達購買業務の効率化だけでなく、システムを導入することで、コスト削減や製品・資材のステータス可視化のほか、属人化していた購買情報の共有化による内部不正防止や統制にも役立ちます。
NEWJI DX
製造業に特化したデジタルトランスフォーメーション(DX)の実現を目指す請負開発型のコンサルティングサービスです。AI、iPaaS、および先端の技術を駆使して、製造プロセスの効率化、業務効率化、チームワーク強化、コスト削減、品質向上を実現します。このサービスは、製造業の課題を深く理解し、それに対する最適なデジタルソリューションを提供することで、企業が持続的な成長とイノベーションを達成できるようサポートします。
オンライン講座
製造業、主に購買・調達部門にお勤めの方々に向けた情報を配信しております。
新任の方やベテランの方、管理職を対象とした幅広いコンテンツをご用意しております。
お問い合わせ
コストダウンが利益に直結する術だと理解していても、なかなか前に進めることができない状況。そんな時は、newjiのコストダウン自動化機能で大きく利益貢献しよう!
(Β版非公開)