- お役立ち記事
- The difference between Stereolithography (SLA) and Selective Laser Sintering (SLS)
The difference between Stereolithography (SLA) and Selective Laser Sintering (SLS)
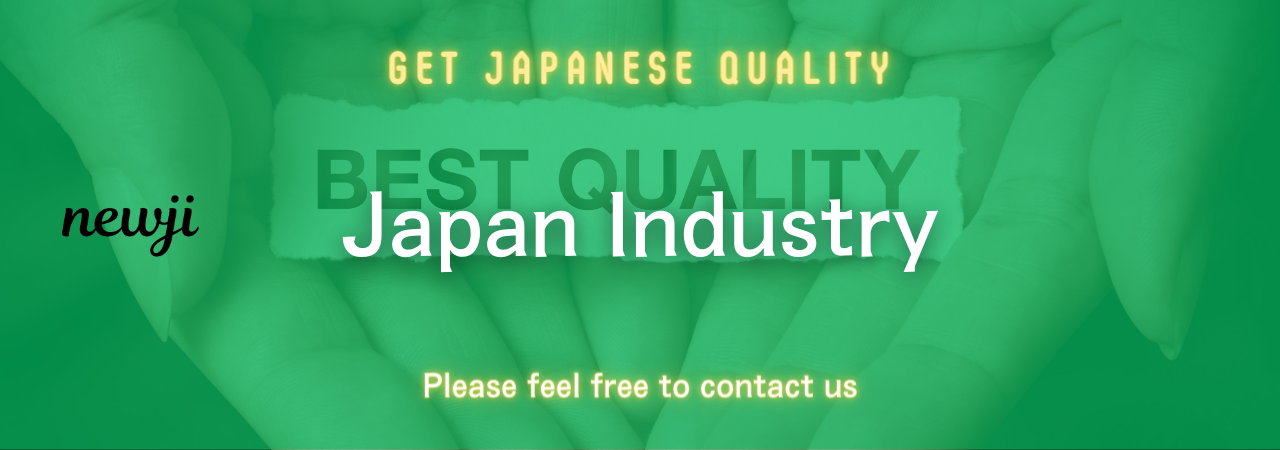
目次
Introduction to 3D Printing Technologies
3D printing has revolutionized how we create objects, offering new possibilities in design, manufacturing, and prototyping. Two popular forms of 3D printing technologies are Stereolithography (SLA) and Selective Laser Sintering (SLS). Understanding the difference between SLA and SLS can help you choose the right method for your needs.
What is Stereolithography (SLA)?
Stereolithography (SLA) is one of the earliest forms of 3D printing technology. It uses a laser to cure liquid resin into solid plastic. Here’s how it works:
How SLA Works
SLA printers have a vat filled with liquid resin. A laser beam traces a pattern on the resin surface, solidifying it layer by layer. As each layer cures, the build platform lowers slightly, and a new layer of resin spreads over the previous one. This process continues until the entire object is formed.
Benefits of SLA
SLA offers high-resolution prints, capable of producing fine details and smooth surfaces. It’s ideal for creating complex geometries, prototypes, and parts that require a high degree of accuracy. Designers and engineers often use SLA for its precision and ability to produce intricate designs.
Common Applications of SLA
SLA is widely used in industries such as dentistry, jewelry, and engineering. It’s excellent for creating dental molds, custom jewelry designs, and intricate prototypes. Additionally, SLA is favored in industries requiring detailed visual models, like architecture and medical modeling.
What is Selective Laser Sintering (SLS)?
Selective Laser Sintering (SLS) is another leading 3D printing technology, which uses a laser to sinter powdered material into solid parts. Unlike SLA, which uses liquid resin, SLS works with powdered materials such as nylon, metals, or ceramics.
How SLS Works
SLS printers have a build chamber filled with powdered material. A laser beam fuses the powder together, layer by layer, to form a solid object. The build platform lowers slightly between each layer, and a spreading mechanism covers the previous layer with a new layer of powder. This process repeats until the object is complete.
Benefits of SLS
SLS offers strong, durable parts with excellent mechanical properties. It doesn’t require support structures, as the surrounding powder provides support during printing. This allows for more complex geometries and interlocking parts. SLS is suitable for functional prototypes, custom products, and low-volume production runs.
Common Applications of SLS
SLS is commonly used in aerospace, automotive, and healthcare industries. It’s ideal for producing lightweight, durable components such as brackets, housings, and medical devices. Engineers use SLS for functional testing, as it provides reliable, high-performance parts.
Comparing SLA and SLS
While both SLA and SLS are effective 3D printing methods, they have distinct differences that make each suitable for specific applications.
Material Differences
SLA uses liquid resins that cure into a hard, brittle plastic, while SLS uses powdered materials, such as nylon or metal, which result in strong, durable parts. Choose SLA for highly detailed and intricate designs, and opt for SLS when strength and durability are priorities.
Print Quality
SLA printers offer superior print resolution and surface finish, making them ideal for detailed prototypes and visual models. SLS printers provide good resolution but excel in producing functional parts with complex geometries, without needing support structures.
Cost Considerations
SLA printers and the required liquid resins can be more expensive than SLS systems and powdered materials. However, the choice depends on your specific needs. For highly detailed, visually appealing parts, investing in SLA may be worthwhile. For robust, functional parts, SLS could offer better value.
Speed and Efficiency
SLA printing can be time-consuming due to the precise curing process of each layer. SLS can be faster, particularly for larger objects, as it builds multiple parts simultaneously in the build chamber. Additionally, SLS doesn’t require post-processing for support removal, saving time.
Conclusion: Choosing the Right Technology
Both Stereolithography (SLA) and Selective Laser Sintering (SLS) offer unique advantages and are suited to different applications. SLA is perfect for detailed, high-resolution models and prototypes, while SLS is ideal for durable, functional parts with complex geometries. Understanding the differences between these technologies can help you select the best 3D printing method for your project needs.
In summary, consider the material requirements, print quality, cost, and efficiency to make an informed decision. Whether you need fine details or robust functional parts, SLA and SLS provide robust solutions to bring your 3D printing projects to life.
資料ダウンロード
QCD調達購買管理クラウド「newji」は、調達購買部門で必要なQCD管理全てを備えた、現場特化型兼クラウド型の今世紀最高の購買管理システムとなります。
ユーザー登録
調達購買業務の効率化だけでなく、システムを導入することで、コスト削減や製品・資材のステータス可視化のほか、属人化していた購買情報の共有化による内部不正防止や統制にも役立ちます。
NEWJI DX
製造業に特化したデジタルトランスフォーメーション(DX)の実現を目指す請負開発型のコンサルティングサービスです。AI、iPaaS、および先端の技術を駆使して、製造プロセスの効率化、業務効率化、チームワーク強化、コスト削減、品質向上を実現します。このサービスは、製造業の課題を深く理解し、それに対する最適なデジタルソリューションを提供することで、企業が持続的な成長とイノベーションを達成できるようサポートします。
オンライン講座
製造業、主に購買・調達部門にお勤めの方々に向けた情報を配信しております。
新任の方やベテランの方、管理職を対象とした幅広いコンテンツをご用意しております。
お問い合わせ
コストダウンが利益に直結する術だと理解していても、なかなか前に進めることができない状況。そんな時は、newjiのコストダウン自動化機能で大きく利益貢献しよう!
(Β版非公開)