- お役立ち記事
- The difference between Supplier and Vendor
月間76,176名の
製造業ご担当者様が閲覧しています*
*2025年3月31日現在のGoogle Analyticsのデータより
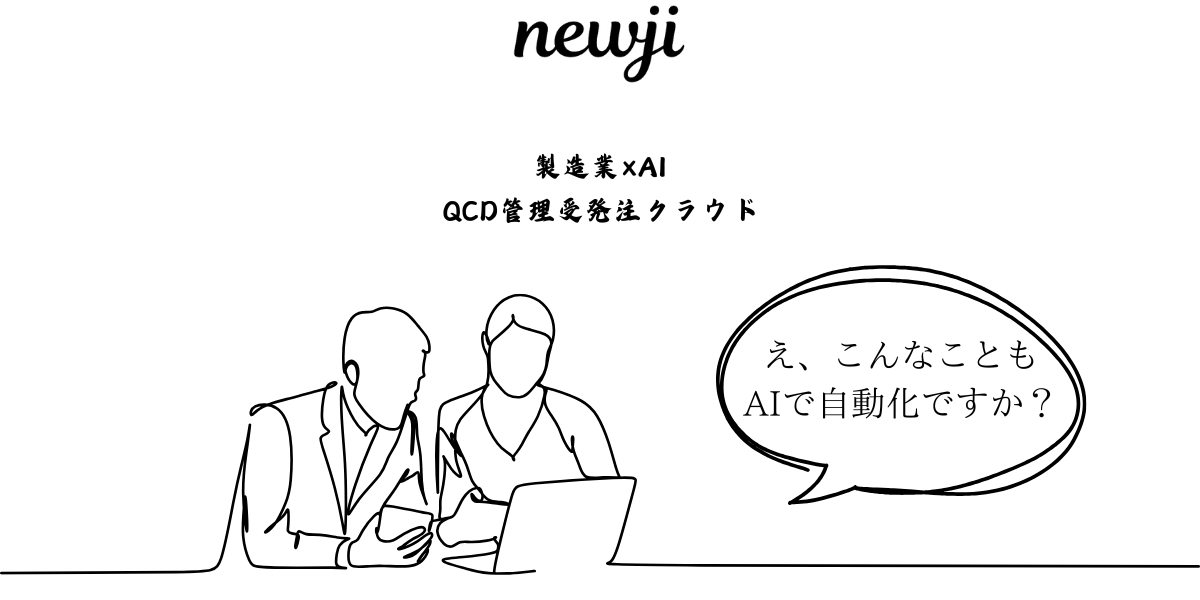
The difference between Supplier and Vendor
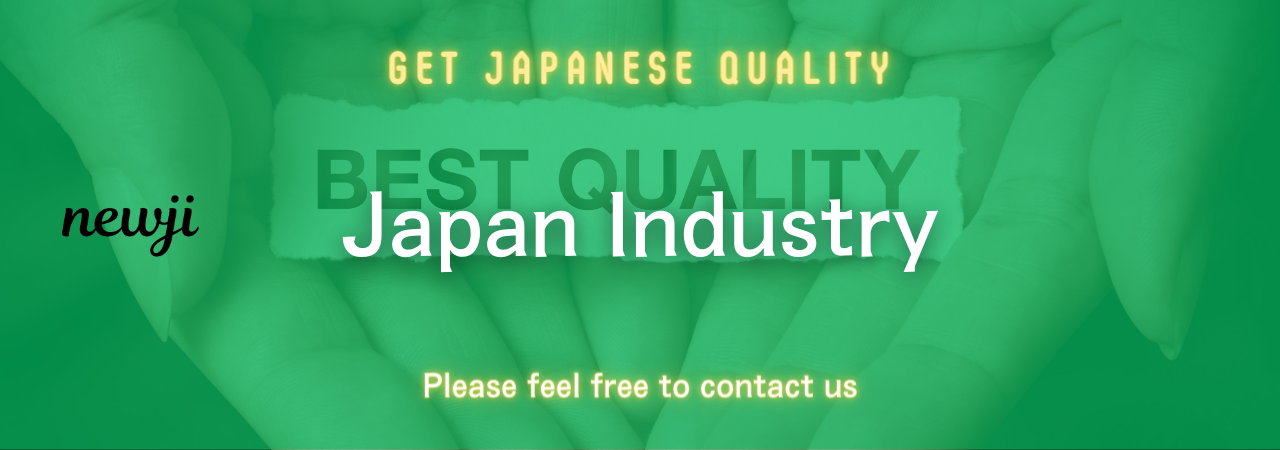
In today’s business world, terms like “supplier” and “vendor” are commonly used but can sometimes be confusing.
While they are often used interchangeably, they have distinct roles within a business’s supply chain.
Understanding these differences is crucial for anyone involved in procurement or supply chain management.
This guide will lay out the key differences between suppliers and vendors, helping you make more informed decisions for your business.
目次
What is a Supplier?
A supplier is a business or individual that provides goods or services to another entity.
The relationship between a supplier and a buyer is often long-term and strategic.
Suppliers are integral to the production process, as they provide the essential raw materials or components required to produce a finished product.
Role and Responsibilities
Suppliers are typically involved in the initial stages of the production process.
They are responsible for providing quality raw materials or components that meet the buyer’s specifications.
Quality control is a significant part of a supplier’s responsibilities, as any defects can impact the final product.
Suppliers often collaborate closely with buyers to forecast demand and adjust supply levels accordingly.
This ensures that there are no disruptions in the production process, thereby maintaining a smooth supply chain.
Types of Suppliers
There are various types of suppliers, depending on the industry and nature of business.
Raw Material Suppliers: These suppliers provide the basic materials needed for production, such as metals, plastics, or chemicals.
Component Suppliers: These suppliers offer specific parts or components that go into the final product.
Service Suppliers: They provide essential services required for the functioning of the business, like logistics, maintenance, or consulting.
What is a Vendor?
A vendor is a person or business that sells finished goods or services to customers.
Unlike suppliers, vendors are usually involved in the final stages of the supply chain, delivering products directly to the consumer.
Role and Responsibilities
Vendors play a crucial role in getting products to the end consumer.
They are responsible for maintaining sufficient stock levels, managing sales, and providing customer service.
Vendors often have a direct relationship with consumers and can offer immediate feedback to manufacturers about consumer preferences and market trends.
Vendors usually focus on sales rather than production.
They may source products from various manufacturers or suppliers to offer a wide range of options to their customers.
Types of Vendors
Retail Vendors: These vendors sell products directly to the public through physical stores or online platforms.
Wholesale Vendors: These vendors purchase products in bulk from manufacturers or suppliers and sell them to retailers or other businesses.
Service Vendors: They provide different types of services directly to consumers, such as cleaning, IT support, or professional consulting.
Key Differences between Supplier and Vendor
While both suppliers and vendors are crucial to the supply chain, they serve different functions that can affect how you manage your business relationships.
Stage in the Supply Chain
Suppliers are generally involved in the earlier stages of the supply chain, providing raw materials or components necessary for production.
Vendors, on the other hand, are usually involved in the final stages, selling the finished product to the end customers.
Nature of the Relationship
The relationship between a buyer and a supplier is often long-term and strategic.
This is because any disruption in the supply of raw materials can halt the entire production process.
Relationships with vendors are usually more transactional and focused on sales rather than production.
Quality Control
Suppliers are responsible for ensuring the quality of raw materials or components.
Any defects can have a cascading effect on the quality of the final product.
Vendors focus more on customer satisfaction and service quality, as they deal directly with the end consumer.
Risk and Responsibility
Suppliers bear significant responsibility as any failure to deliver quality materials can disrupt the production process.
They also have to ensure timely delivery to meet production schedules.
Vendors, on the other hand, deal with the risk of unsold inventory, customer returns, and maintaining a good relationship with end consumers.
How to Choose the Right Supplier or Vendor
Choosing the right supplier or vendor is crucial for your business’s success.
Here are some tips to help you make an informed decision.
For Suppliers
Quality: Always check the quality of the raw materials or components they provide.
A single defective item can disrupt your entire production process.
Reliability: Ensure that the supplier can consistently meet your demand and delivery schedules.
Delays in raw materials can halt production and result in financial losses.
Cost: Analyze the cost of materials relative to the quality and reliability of the supplier.
Sometimes it’s worth paying more for better quality and dependability.
For Vendors
Market Reach: Choose vendors who have a broad market reach and can help you sell more products.
Online platforms and physical stores with high foot traffic are often good options.
Customer Service: Good vendors offer excellent customer service.
This ensures that any issues are quickly resolved, keeping your consumers happy.
Inventory Management: Ensure that the vendor can maintain sufficient stock levels and manage inventory effectively.
This will help avoid stockouts and lost sales.
Conclusion
Understanding the difference between a supplier and a vendor is essential for effective supply chain management.
Suppliers provide the essential raw materials or components needed for production and are crucial for maintaining quality and consistency.
Vendors, on the other hand, focus on selling finished products to end consumers and play a significant role in customer satisfaction.
By recognizing these distinctions and choosing the right suppliers and vendors, businesses can optimize their supply chain, ensuring both efficient production and satisfied customers.
Whether you are sourcing raw materials or looking to improve your sales, understanding these roles will help you make better decisions and ultimately contribute to your business’s success.
資料ダウンロード
QCD管理受発注クラウド「newji」は、受発注部門で必要なQCD管理全てを備えた、現場特化型兼クラウド型の今世紀最高の受発注管理システムとなります。
ユーザー登録
受発注業務の効率化だけでなく、システムを導入することで、コスト削減や製品・資材のステータス可視化のほか、属人化していた受発注情報の共有化による内部不正防止や統制にも役立ちます。
NEWJI DX
製造業に特化したデジタルトランスフォーメーション(DX)の実現を目指す請負開発型のコンサルティングサービスです。AI、iPaaS、および先端の技術を駆使して、製造プロセスの効率化、業務効率化、チームワーク強化、コスト削減、品質向上を実現します。このサービスは、製造業の課題を深く理解し、それに対する最適なデジタルソリューションを提供することで、企業が持続的な成長とイノベーションを達成できるようサポートします。
製造業ニュース解説
製造業、主に購買・調達部門にお勤めの方々に向けた情報を配信しております。
新任の方やベテランの方、管理職を対象とした幅広いコンテンツをご用意しております。
お問い合わせ
コストダウンが利益に直結する術だと理解していても、なかなか前に進めることができない状況。そんな時は、newjiのコストダウン自動化機能で大きく利益貢献しよう!
(β版非公開)