- お役立ち記事
- The difference between Surface Mount Technology (SMT) and Through-hole Technology (THT)
月間76,176名の
製造業ご担当者様が閲覧しています*
*2025年3月31日現在のGoogle Analyticsのデータより
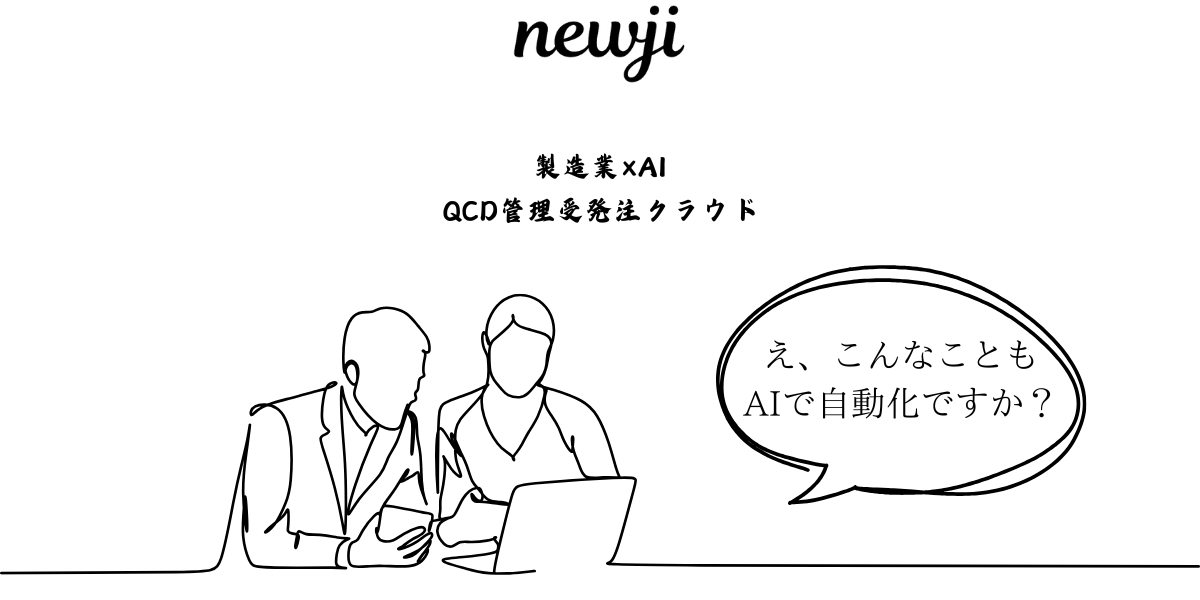
The difference between Surface Mount Technology (SMT) and Through-hole Technology (THT)
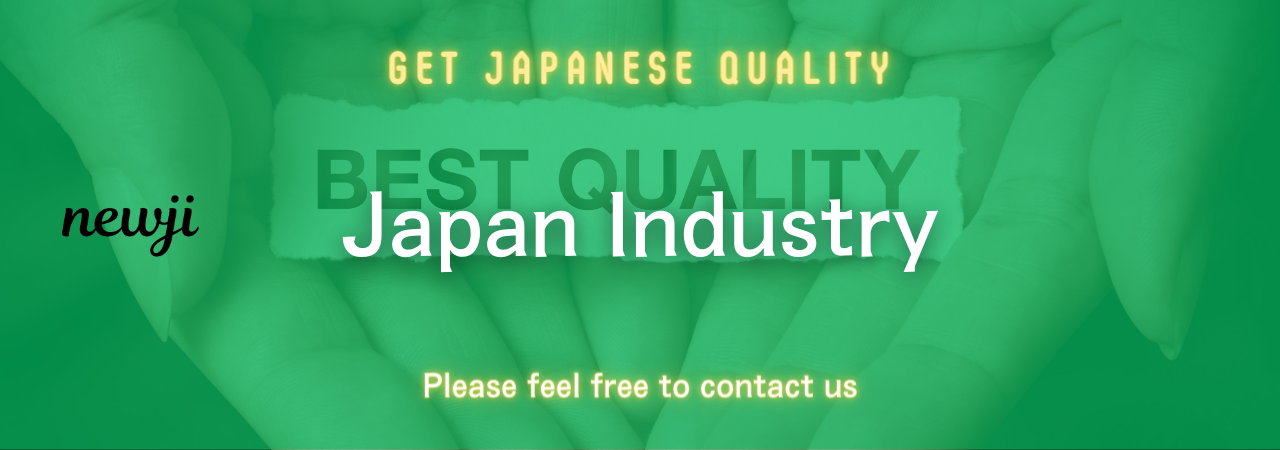
When it comes to electronic assembly manufacturing, two predominant technologies dominate the landscape: Surface Mount Technology (SMT) and Through-hole Technology (THT).
Understanding the differences between SMT and THT can be crucial for making the right choice in electronic assembly.
Let’s explore these differences in detail.
目次
What is Surface Mount Technology (SMT)?
Surface Mount Technology, or SMT, is a method used to create electronic circuits where components are mounted directly onto the surface of printed circuit boards (PCBs).
This technology was developed to reduce the size of assemblies and improve manufacturability and performance.
Advantages of SMT
One of the main advantages of SMT is its ability to save space.
Because components can be placed on both sides of the PCB, it allows for denser and smaller boards.
SMT components are generally smaller and lighter than their THT counterparts, making them ideal for compact devices.
The automation of SMT assembly also leads to faster production rates and lower labor costs.
With precise machinery placing components on the PCB, the likelihood of human error is significantly reduced.
Applications of SMT
SMT is widely used in the manufacturing of consumer electronics, telecommunications, medical devices, and automotive electronics.
Its ability to accommodate complex and densely-packed boards makes it suitable for modern gadgets and devices.
What is Through-hole Technology (THT)?
Through-hole Technology, or THT, is an older method of mounting electronic components through holes drilled in PCBs.
Components have leads that are inserted into these holes and soldered to pads on the opposite side.
Advantages of THT
While THT may appear outdated compared to SMT, it still has several advantages.
THT offers higher mechanical strength.
Components mounted through holes have stronger bonds and are less likely to be dislodged, making THT a good choice for products that will endure physical stress or environmental challenges.
THT is also easier to work with manually.
In prototyping and testing, THT components are easier to swap in and out, making the process more flexible for developers.
Applications of THT
THT is commonly used in the manufacturing of industrial equipment, aerospace, and military applications.
The robust nature of THT components makes them suitable for environments where reliability is critical.
Comparing SMT and THT
Assembly Process
The assembly process for SMT involves the use of automated machinery.
Components are placed onto the PCB’s surface and soldered using a reflow oven.
In contrast, THT requires manual effort or semi-automated machinery.
Leads are inserted into drilled holes, and soldering is done from the opposite side, typically using wave soldering.
Footprint and Density
SMT allows for a higher component density as components can be placed on both sides of the PCB.
This results in a smaller overall footprint of the final product.
THT, however, consumes more space due to the need for holes and leads.
Thus, the PCB size and thickness may increase, making it less suitable for compact designs.
Mechanical Strength
In terms of mechanical strength, THT holds the upper hand.
The through-hole mounting provides a stronger bond between the component and the PCB, making it ideal for applications where vibrations or physical impacts are common.
SMT does not offer the same level of mechanical robustness but is generally sufficient for most consumer electronics.
Cost Considerations
SMT typically results in lower production costs due to automation.
However, the initial investment in machinery can be higher.
THT may have higher labor costs due to its more manual nature but has lower initial equipment costs.
Repair and Prototyping
THT components are easier to replace and rework, which can be advantageous during prototyping and in applications requiring frequent maintenance or upgrades.
SMT components, being smaller and more densely packed, can be challenging to rework or repair manually.
Choosing Between SMT and THT
The choice between SMT and THT hinges on several factors including the application, budget, and design requirements.
For complex, high-density, and compact designs, SMT is generally the preferred choice.
It is suitable for products that do not face substantial physical stress.
For applications where durability, mechanical strength, and ease of manual replacement are prioritized, THT remains a viable option.
Often, a hybrid approach is employed where both SMT and THT are used on the same board to leverage the benefits of both technologies.
Conclusion
Understanding the differences between Surface Mount Technology (SMT) and Through-hole Technology (THT) is critical for making informed decisions in electronic assembly.
Each technology has its distinct advantages and optimal use cases.
By carefully considering the specific needs of your project, you can choose the appropriate technology to ensure reliability, efficiency, and cost-effectiveness.
Whether you lean towards the compact and automated benefits of SMT or the rugged and manual-friendly nature of THT, both methods have their rightful place in the ever-evolving world of electronics.
資料ダウンロード
QCD管理受発注クラウド「newji」は、受発注部門で必要なQCD管理全てを備えた、現場特化型兼クラウド型の今世紀最高の受発注管理システムとなります。
ユーザー登録
受発注業務の効率化だけでなく、システムを導入することで、コスト削減や製品・資材のステータス可視化のほか、属人化していた受発注情報の共有化による内部不正防止や統制にも役立ちます。
NEWJI DX
製造業に特化したデジタルトランスフォーメーション(DX)の実現を目指す請負開発型のコンサルティングサービスです。AI、iPaaS、および先端の技術を駆使して、製造プロセスの効率化、業務効率化、チームワーク強化、コスト削減、品質向上を実現します。このサービスは、製造業の課題を深く理解し、それに対する最適なデジタルソリューションを提供することで、企業が持続的な成長とイノベーションを達成できるようサポートします。
製造業ニュース解説
製造業、主に購買・調達部門にお勤めの方々に向けた情報を配信しております。
新任の方やベテランの方、管理職を対象とした幅広いコンテンツをご用意しております。
お問い合わせ
コストダウンが利益に直結する術だと理解していても、なかなか前に進めることができない状況。そんな時は、newjiのコストダウン自動化機能で大きく利益貢献しよう!
(β版非公開)