- お役立ち記事
- The difference between Thermal Spraying and Plating
月間76,176名の
製造業ご担当者様が閲覧しています*
*2025年3月31日現在のGoogle Analyticsのデータより
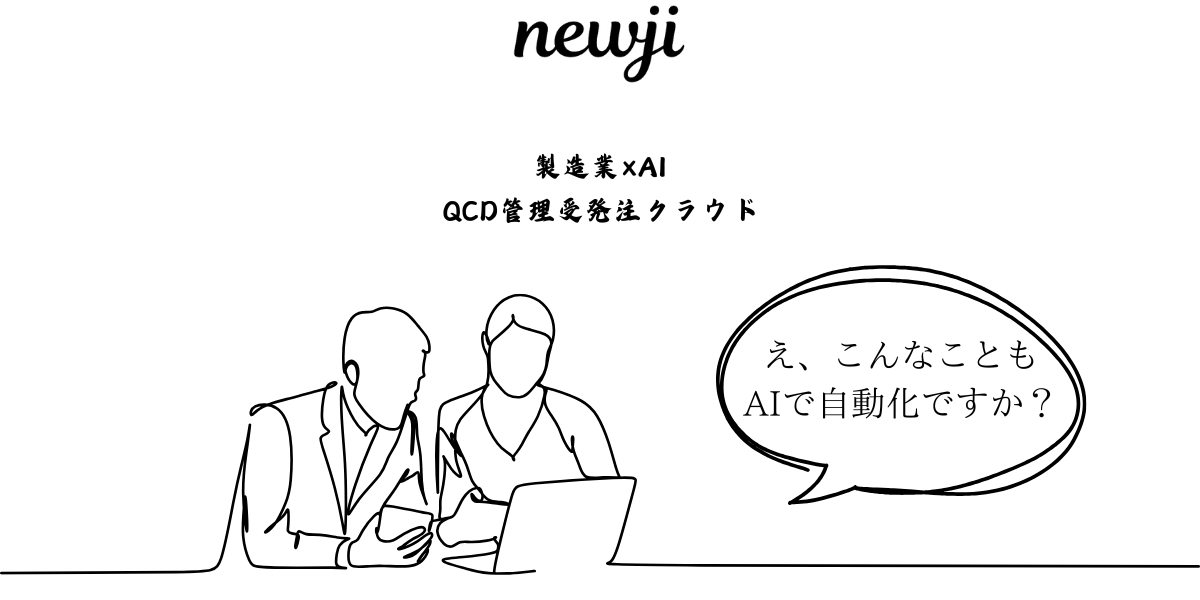
The difference between Thermal Spraying and Plating
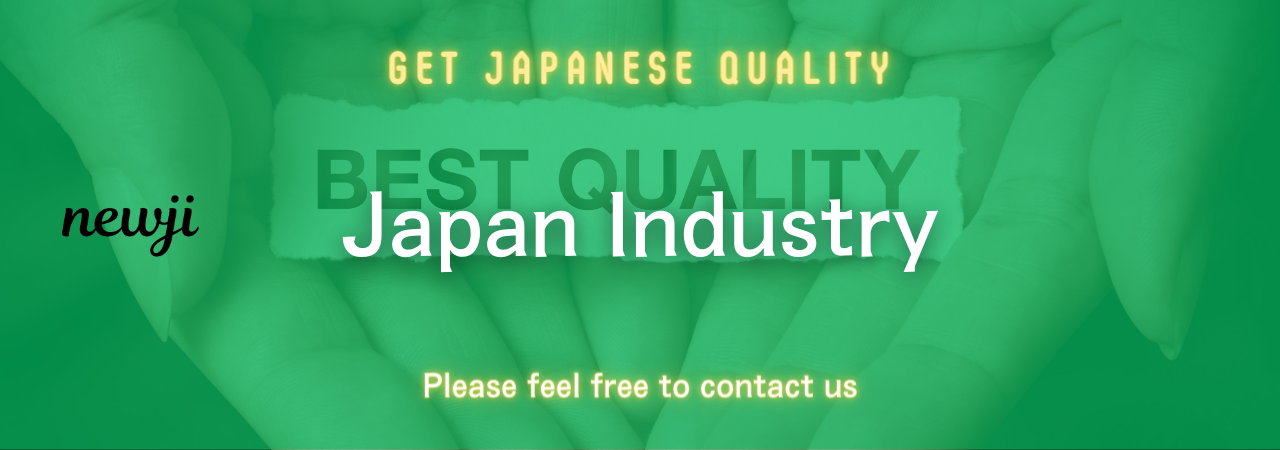
Thermal spraying and plating are two prevalent methods used to enhance the surface properties of materials.
Both techniques serve to protect and improve the performance of a workpiece, but they achieve this in different ways.
Understanding the differences between thermal spraying and plating can help you choose the right method for your specific application.
Let’s dive deeper into what sets these two processes apart.
目次
What is Thermal Spraying?
Thermal spraying is a coating process where melted or heated materials are sprayed onto a surface.
This method is widely used to provide wear resistance, corrosion protection, and to improve the surface properties of a substrate.
The materials used in thermal spraying can be in the form of powder, wire, or rod.
Types of Thermal Spraying
There are several types of thermal spraying, each with its unique set of advantages:
– Flame Spraying: This involves melting the coating material in an oxy-fuel flame and then spraying it onto the surface.
– Plasma Spraying: In this method, the coating material is heated in a high-temperature plasma jet before being sprayed.
– Wire Arc Spraying: This uses an electric arc to melt the wire feedstock material, which is then atomized and sprayed by compressed air.
– High-Velocity Oxygen Fuel (HVOF) Spraying: The coating material is introduced into a combustion chamber where it is heated and accelerated to high velocities before impact.
Applications of Thermal Spraying
Thermal spraying is widely used in various industries due to its versatility.
Some common applications include:
– Aerospace: Used for coating turbine blades and other components to withstand high temperatures and wear.
– Automotive: Enhances the durability of engine components.
– Oil and Gas: Protects drilling equipment from corrosion and wear.
– Medical: Coatings for implants and other medical devices to improve biocompatibility and wear resistance.
What is Plating?
Plating, also known as electroplating, involves depositing a metallic coating onto a substrate through an electrochemical process.
This method is done by immersing the workpiece in an electrolytic solution containing metal ions.
An electric current is then passed through the solution, causing the metal ions to adhere to the substrate.
Types of Plating
There are several types of plating methods, each with its unique characteristics:
– Electroplating: Utilizes an electric current to deposit metal onto a substrate.
– Electroless Plating: This is a chemical process that deposits metal on the substrate without the need for electric current.
– Anodizing: Involves the oxidation of a metal surface to form a protective oxide layer, primarily used for aluminum.
– Galvanizing: Coats steel or iron with zinc to protect against corrosion.
Applications of Plating
Plating is commonly used across various sectors due to its ability to enhance surface properties:
– Electronics: Used for coating connectors, switches, and other components to improve conductivity and prevent corrosion.
– Jewelry: Common in gold and silver plating to enhance appearance and resist tarnish.
– Automotive: Implies chrome plating for bumpers and other parts to improve aesthetics and corrosion resistance.
– Industrial: Enhances the wear resistance and lubricity of machine parts.
Key Differences Between Thermal Spraying and Plating
Process
One of the most significant differences between thermal spraying and plating is the process itself.
Thermal spraying involves the physical application of molten or heated materials onto the substrate.
In contrast, plating relies on chemical or electrochemical deposition to coat a surface.
Materials Used
Thermal spraying can utilize a wider variety of materials compared to plating.
While plating primarily involves metals like nickel, chrome, and gold, thermal spraying can use metals, ceramics, polymers, and even composites.
This allows for greater flexibility in the properties that can be imparted to the coated surface.
Thickness and Uniformity
Plating is generally more suited for applications requiring thin, uniform coatings.
It can produce coatings that are only a few micrometers thick with a high degree of uniformity.
Thermal spraying, on the other hand, is more suitable for thicker coatings, which can range from tens of micrometers to several millimeters.
Adhesion and Bond Strength
Thermal spraying typically results in stronger adhesive and cohesive bond strengths compared to plating.
The high-impact velocity of the sprayed particles creates a stronger mechanical bond with the substrate.
Plated coatings, while sufficient for many applications, generally do not achieve the same level of bond strength.
Surface Preparation
Both methods require surface preparation to ensure good adhesion.
However, thermal spraying often demands more extensive surface preparation, including grit blasting or other mechanical means, to roughen and clean the substrate.
Plating usually requires a clean, smooth surface, and the preparation involves chemical cleaning and sometimes etching.
Cost and Equipment
The cost and equipment required for thermal spraying can be higher compared to plating.
Thermal spraying demands specialized equipment and often skilled labor, which can increase the overall cost.
Plating can be done with relatively simpler equipment, making it more cost-effective for some applications.
Conclusion
Both thermal spraying and plating are valuable techniques for enhancing the surface properties of materials.
Your choice between the two will depend on several factors, including the type of material you are working with, the desired coating thickness, bond strength, and cost considerations.
Thermal spraying offers greater versatility in terms of materials and can produce thicker, more robust coatings.
Plating, on the other hand, excels in applications requiring thin, uniform coatings and can be more cost-effective.
Understanding these differences will help you make an informed decision, ensuring that you select the right method for your specific needs.
資料ダウンロード
QCD管理受発注クラウド「newji」は、受発注部門で必要なQCD管理全てを備えた、現場特化型兼クラウド型の今世紀最高の受発注管理システムとなります。
ユーザー登録
受発注業務の効率化だけでなく、システムを導入することで、コスト削減や製品・資材のステータス可視化のほか、属人化していた受発注情報の共有化による内部不正防止や統制にも役立ちます。
NEWJI DX
製造業に特化したデジタルトランスフォーメーション(DX)の実現を目指す請負開発型のコンサルティングサービスです。AI、iPaaS、および先端の技術を駆使して、製造プロセスの効率化、業務効率化、チームワーク強化、コスト削減、品質向上を実現します。このサービスは、製造業の課題を深く理解し、それに対する最適なデジタルソリューションを提供することで、企業が持続的な成長とイノベーションを達成できるようサポートします。
製造業ニュース解説
製造業、主に購買・調達部門にお勤めの方々に向けた情報を配信しております。
新任の方やベテランの方、管理職を対象とした幅広いコンテンツをご用意しております。
お問い合わせ
コストダウンが利益に直結する術だと理解していても、なかなか前に進めることができない状況。そんな時は、newjiのコストダウン自動化機能で大きく利益貢献しよう!
(β版非公開)