- お役立ち記事
- The difference between Thermal Spraying and Welding
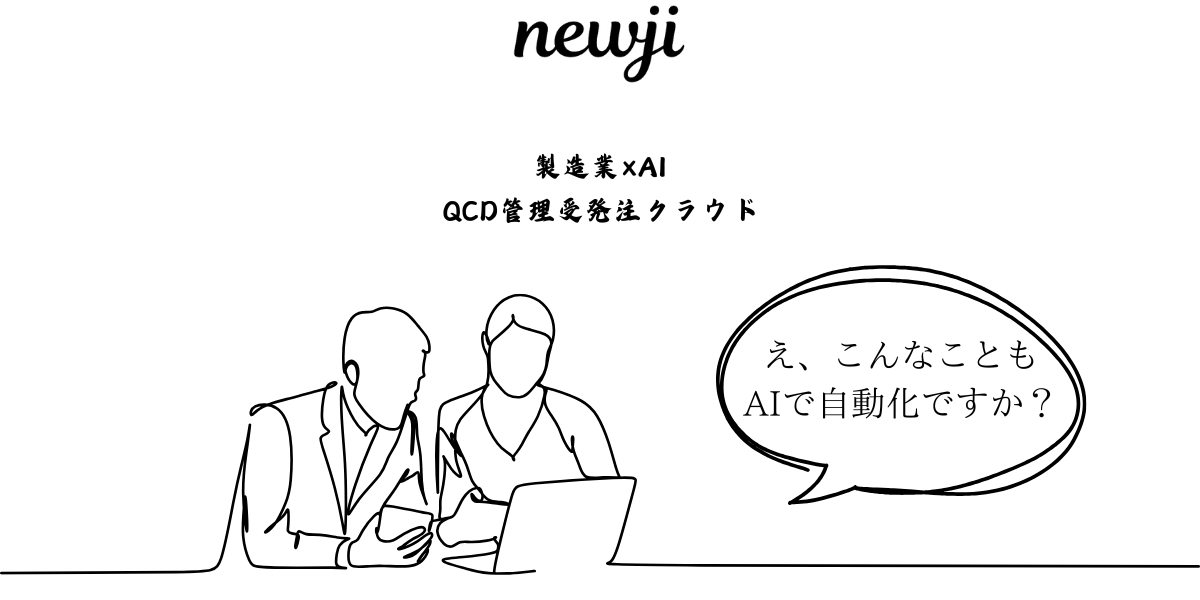
The difference between Thermal Spraying and Welding
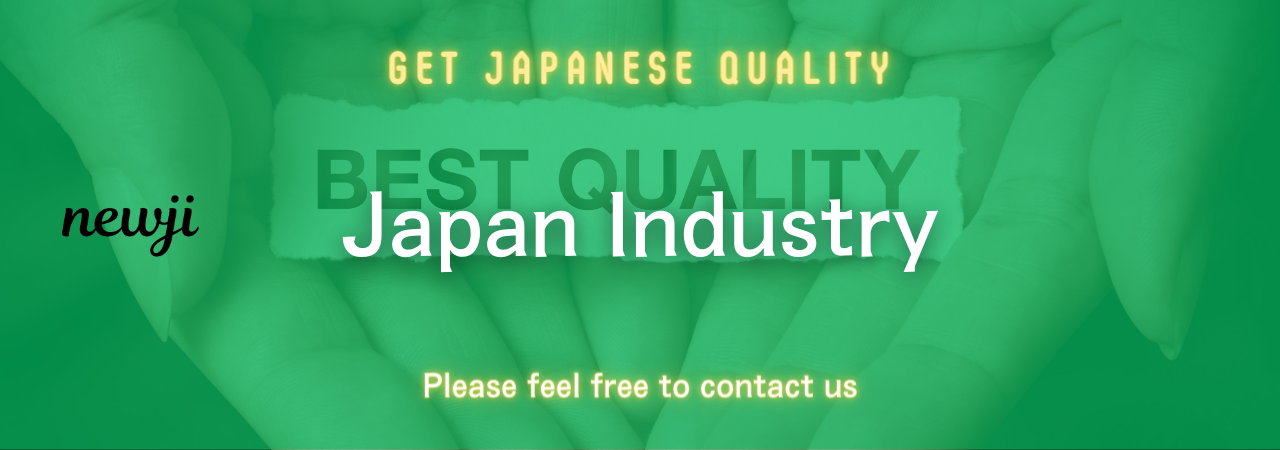
Thermal spraying and welding are two industrial processes commonly used for coating surfaces, repairing equipment, and fabricating structures.
Although they serve some similar functions, they are fundamentally different in their methods, applications, and benefits.
This article will explore the distinctions between thermal spraying and welding, helping you understand which process is suitable for your needs.
目次
What is Thermal Spraying?
Thermal spraying is a coating process where melted or heated materials are sprayed onto a surface.
This surface coating technique is used to improve wear resistance, corrosion resistance, and other surface properties.
Let’s delve deeper into how thermal spraying works, its types, and its benefits.
How Thermal Spraying Works
In thermal spraying, coating materials are heated to a molten or semi-molten state and then propelled toward a substrate using a stream of gas or air.
Once these particles hit the surface, they flatten and rapidly cool, forming a coating.
The bond between the particles and the substrate can vary, but it often involves mechanical interlocking or adherence.
Types of Thermal Spraying
There are several types of thermal spraying techniques, each with unique characteristics:
– **Flame Spraying:** Utilizes an oxy-fuel gas flame to melt the coating material.
– **Plasma Spraying:** Uses a high-temperature plasma jet to melt the material.
– **Arc Spraying:** Involves an electric arc to melt metallic wires, which are then sprayed.
– **High-Velocity Oxy-Fuel (HVOF) Spraying:** Employs high-velocity gas to spray molten particles onto the substrate.
– **Cold Spraying:** Involves spraying fine metallic powders at high speeds without melting them.
Benefits of Thermal Spraying
Thermal spraying offers a multitude of benefits:
– **Versatility:** Can coat a range of materials like metals, ceramics, and polymers.
– **Cost-Effective:** Suitable for large surfaces or parts that would be expensive to manufacture entirely from a resistant material.
– **Reduced Downtime:** Quick application time leads to minimal downtimes for industrial equipment.
– **Enhanced Properties:** Improves the wear, corrosion, and heat resistance of the substrate.
What is Welding?
Welding is the process of joining two or more materials, usually metals or thermoplastics, by applying heat, pressure, or both.
Unlike thermal spraying, welding is used to create a solid bond between separate pieces, forming one continuous material.
Here’s more about how welding works, its types, and its advantages.
How Welding Works
Welding involves melting the workpieces and adding a filler material (if needed) to form a joint.
The process usually requires a heat source like an electric arc, gas flame, or laser.
Once the materials have been melted and joined, they are allowed to cool and solidify, creating a strong bond.
Types of Welding
Several welding techniques are widely used in various industries:
– **Arc Welding:** Uses an electrical arc to create heat for melting the metals.
– **Gas Welding:** Employs a gas flame, usually from an oxy-acetylene torch, to melt the metals.
– **Resistance Welding:** Utilizes electrical resistance and pressure to join metals.
– **Laser Welding:** Uses a laser beam to provide precise and high-energy heat for welding.
– **TIG Welding:** Employs a tungsten electrode to produce the weld, often used with a filler material.
– **MIG Welding:** Uses a continuous wire feed as an electrode and filler material.
Benefits of Welding
Welding offers various advantages:
– **Strong Joints:** Creates durable and robust joints capable of withstanding significant stresses.
– **Versatility in Materials:** Can join different metals, including some plastics and composite materials.
– **Structural Integrity:** Ideal for structural applications that require strong, permanent bonds.
– **Customization:** Allows for the design and fabrication of complex shapes and structures.
Thermal Spraying vs. Welding: Key Differences
While both thermal spraying and welding are crucial industrial processes, they differ significantly in their applications and properties.
Application
Thermal spraying is primarily a surface coating technique.
It is employed to enhance the surface properties of a substrate without altering its bulk characteristics.
In contrast, welding is a joining process used to fuse multiple workpieces into a single, continuous form.
Heat Input and Distortion
Thermal spraying involves localized heat application, which generally means less heat is transferred to the substrate.
This minimizes the risk of thermal distortion and residual stresses.
Welding often subjects materials to high heat, which can induce warping, distortion, and residual stresses in the workpieces.
Materials Used
Thermal spraying offers the flexibility to use a wide range of materials, including metals, ceramics, and polymers.
Welding is typically limited to metals and certain thermoplastics, and it usually requires compatible filler materials.
Bonding Mechanism
The bonding in thermal spraying is usually mechanical, relying on the limited diffusion of the particles to the substrate.
Welding, on the other hand, creates a metallurgical bond, forming a stronger and more cohesive joint between workpieces.
Repair and Maintenance
Thermal spraying is frequently used for repair and maintenance due to its quick application and ability to coat large areas.
This makes it ideal for restoring worn-out parts.
Welding is also used for repairs but is best suited for applications requiring a durable, permanent bond.
Choosing the Right Process
When deciding between thermal spraying and welding, consider the specific needs of your project.
– If you need to enhance surface properties without altering the bulk material, thermal spraying is likely the better choice.
– For applications requiring strong, permanent joints, welding offers unmatched durability and strength.
Understanding the characteristics and benefits of each process will help in making an informed decision, ensuring the best outcome for your specific requirements.
資料ダウンロード
QCD調達購買管理クラウド「newji」は、調達購買部門で必要なQCD管理全てを備えた、現場特化型兼クラウド型の今世紀最高の購買管理システムとなります。
ユーザー登録
調達購買業務の効率化だけでなく、システムを導入することで、コスト削減や製品・資材のステータス可視化のほか、属人化していた購買情報の共有化による内部不正防止や統制にも役立ちます。
NEWJI DX
製造業に特化したデジタルトランスフォーメーション(DX)の実現を目指す請負開発型のコンサルティングサービスです。AI、iPaaS、および先端の技術を駆使して、製造プロセスの効率化、業務効率化、チームワーク強化、コスト削減、品質向上を実現します。このサービスは、製造業の課題を深く理解し、それに対する最適なデジタルソリューションを提供することで、企業が持続的な成長とイノベーションを達成できるようサポートします。
オンライン講座
製造業、主に購買・調達部門にお勤めの方々に向けた情報を配信しております。
新任の方やベテランの方、管理職を対象とした幅広いコンテンツをご用意しております。
お問い合わせ
コストダウンが利益に直結する術だと理解していても、なかなか前に進めることができない状況。そんな時は、newjiのコストダウン自動化機能で大きく利益貢献しよう!
(Β版非公開)