- お役立ち記事
- The difference between Total Productive Maintenance (TPM) and Total Quality Management (TQM)
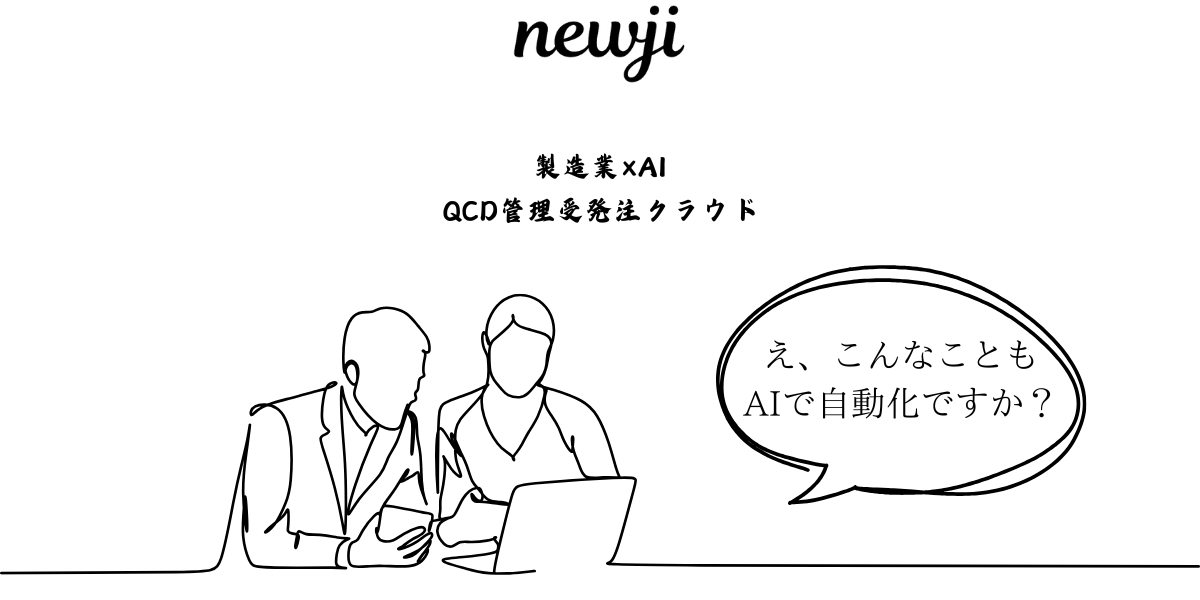
The difference between Total Productive Maintenance (TPM) and Total Quality Management (TQM)
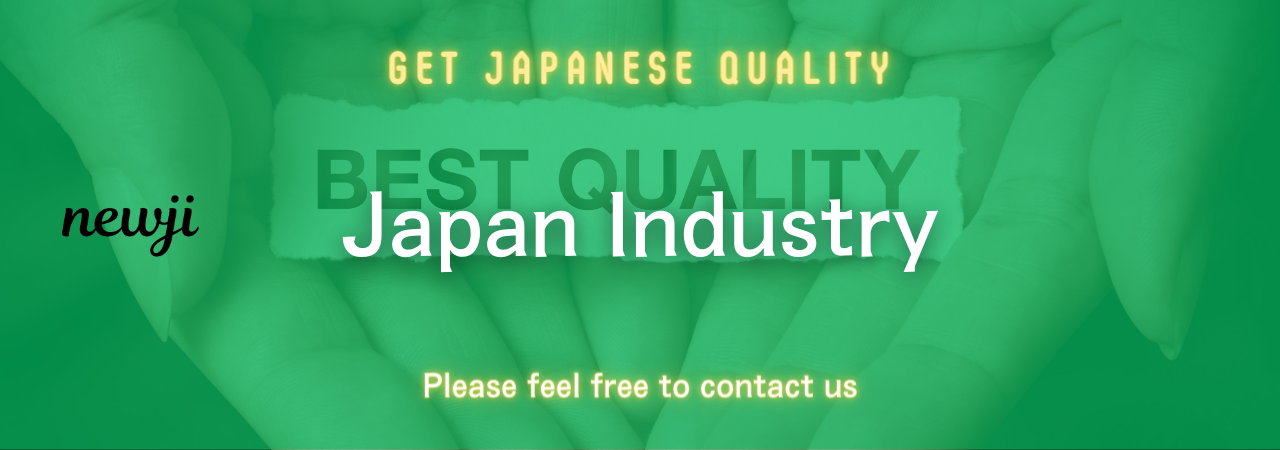
In today’s competitive business environment, organizations are continuously seeking ways to improve their processes and enhance overall efficiency.
Two methodologies that firms often turn to are Total Productive Maintenance (TPM) and Total Quality Management (TQM).
While they both aim to improve organizational performance, the two approaches focus on different aspects and utilize distinct strategies.
目次
What is Total Productive Maintenance (TPM)?
TPM stands for Total Productive Maintenance.
It is a holistic approach to equipment maintenance that strives to achieve perfect production.
This involves no breakdowns, no small stops or slow running, no defects, and no accidents.
TPM aims to maximize the overall effectiveness of equipment and machinery by involving all employees from top management to the shop floor workers.
Goals of TPM
– Improve productivity by minimizing downtime and equipment failures.
– Reduce maintenance costs.
– Enhance job satisfaction by involving frontline operators in maintenance tasks.
– Create a safer work environment.
Pillars of TPM
TPM is built on several key pillars that each focus on different aspects of equipment maintenance and efficiency:
1. Autonomous Maintenance
Operators are given the responsibility to maintain their own equipment.
This involves basic tasks such as cleaning, lubrication, and minor adjustments which help prevent minor issues from escalating into major problems.
2. Planned Maintenance
This involves scheduling maintenance activities based on historical data and performance metrics.
The aim is to predict and prevent failures before they occur.
3. Quality Maintenance
QM focuses on designing processes that ensure quality is maintained from the beginning of the production process.
This involves thorough inspections and process audits to prevent defects.
4. Focused Improvement
Teams are formed to identify and eliminate losses that occur in the production processes.
The focus is on continuous improvement and problem-solving.
5. Early Equipment Management
Insights gained from maintenance activities are used to design and install new equipment.
The goal is to ensure that new machines are easier to maintain and operate efficiently.
What is Total Quality Management (TQM)?
TQM, or Total Quality Management, is an organization-wide approach to continuous improvement that seeks to improve the quality of products and services through ongoing refinements in response to continuous feedback.
TQM aims to enhance customer satisfaction and operational efficiency.
Principles of TQM
TQM revolves around several core principles that guide organizations toward improved quality:
1. Customer Focus
The primary aim of TQM is to meet and exceed customer expectations.
This involves understanding customer needs and ensuring that the organization’s products or services fulfill those needs.
2. Total Employee Involvement
Everyone in the organization, from top management to the frontline workers, is involved in and committed to achieving the goals set by TQM.
3. Process-Centered Approach
TQM emphasizes improving processes to enhance quality.
This involves identifying critical processes, monitoring them, and making ongoing improvements.
4. Integrated System
All departments and sectors of the organization work together as a single, integrated system to achieve quality objectives.
5. Continuous Improvement
Organizations adopting TQM are committed to continuous improvement.
They measure performance, analyze results, and use the data to drive ongoing enhancements.
6. Fact-Based Decision Making
Decisions are made based on data and analysis rather than intuition or anecdotal evidence.
This ensures that changes lead to genuine improvements.
Difference Between TPM and TQM
Both TPM and TQM have their unique approaches and areas of focus.
Understanding the differences can help organizations implement the right strategy that aligns with their goals.
1. Core Focus
TPM primarily focuses on optimizing equipment performance and maintenance.
Its goal is to ensure machines and equipment are efficient, reliable, and capable of producing quality products.
On the other hand, TQM is more concerned with quality across the entire organization.
Its objective is to improve overall quality and customer satisfaction through continuous process enhancements.
2. Employee Involvement
Both TPM and TQM emphasize employee involvement, but in different contexts.
TPM involves operators in maintenance tasks and encourages them to take ownership of their equipment.
TQM focuses on involving employees in quality improvement initiatives across all processes.
3. Implementation Approach
TPM employs structured pillars such as autonomous maintenance, planned maintenance, and quality maintenance.
These pillars guide the implementation process.
TQM utilizes principles like customer focus, total employee involvement, and continuous improvement to shape its methodology.
The implementation of TQM is often broader and includes a wide range of quality-related activities.
4. Measurement and Analysis
In TPM, key performance indicators (KPIs) like overall equipment effectiveness (OEE) are used to measure success.
The focus is on equipment performance metrics.
TQM relies on a variety of metrics, including customer satisfaction, defect rates, and process efficiency.
It takes a more holistic approach to performance measurement.
5. Scope of Application
TPM is typically more specific to manufacturing and industries where equipment plays a crucial role in production.
TQM is applicable to a wider range of industries, including service sectors, where quality improvement is pertinent to all processes.
Conclusion
In summary, while both TPM and TQM aim to enhance organizational performance and efficiency, they differ significantly in their focus and approach.
TPM zeroes in on maximizing the efficiency and reliability of equipment through proactive maintenance involving all employees.
On the other hand, TQM aims to improve overall quality and customer satisfaction through continuous process improvement involving everyone in the organization.
Understanding these differences allows organizations to better select and implement the methodology that aligns best with their goals and operational needs.
By integrating elements from both TPM and TQM, organizations can create a comprehensive strategy that enhances both equipment performance and overall quality.
This holistic approach can lead to improved productivity, reduced costs, and higher customer satisfaction, propelling the organization toward sustained success in the competitive market.
資料ダウンロード
QCD調達購買管理クラウド「newji」は、調達購買部門で必要なQCD管理全てを備えた、現場特化型兼クラウド型の今世紀最高の購買管理システムとなります。
ユーザー登録
調達購買業務の効率化だけでなく、システムを導入することで、コスト削減や製品・資材のステータス可視化のほか、属人化していた購買情報の共有化による内部不正防止や統制にも役立ちます。
NEWJI DX
製造業に特化したデジタルトランスフォーメーション(DX)の実現を目指す請負開発型のコンサルティングサービスです。AI、iPaaS、および先端の技術を駆使して、製造プロセスの効率化、業務効率化、チームワーク強化、コスト削減、品質向上を実現します。このサービスは、製造業の課題を深く理解し、それに対する最適なデジタルソリューションを提供することで、企業が持続的な成長とイノベーションを達成できるようサポートします。
オンライン講座
製造業、主に購買・調達部門にお勤めの方々に向けた情報を配信しております。
新任の方やベテランの方、管理職を対象とした幅広いコンテンツをご用意しております。
お問い合わせ
コストダウンが利益に直結する術だと理解していても、なかなか前に進めることができない状況。そんな時は、newjiのコストダウン自動化機能で大きく利益貢献しよう!
(Β版非公開)