- お役立ち記事
- The difference between Vacuum Deposition and Sputtering
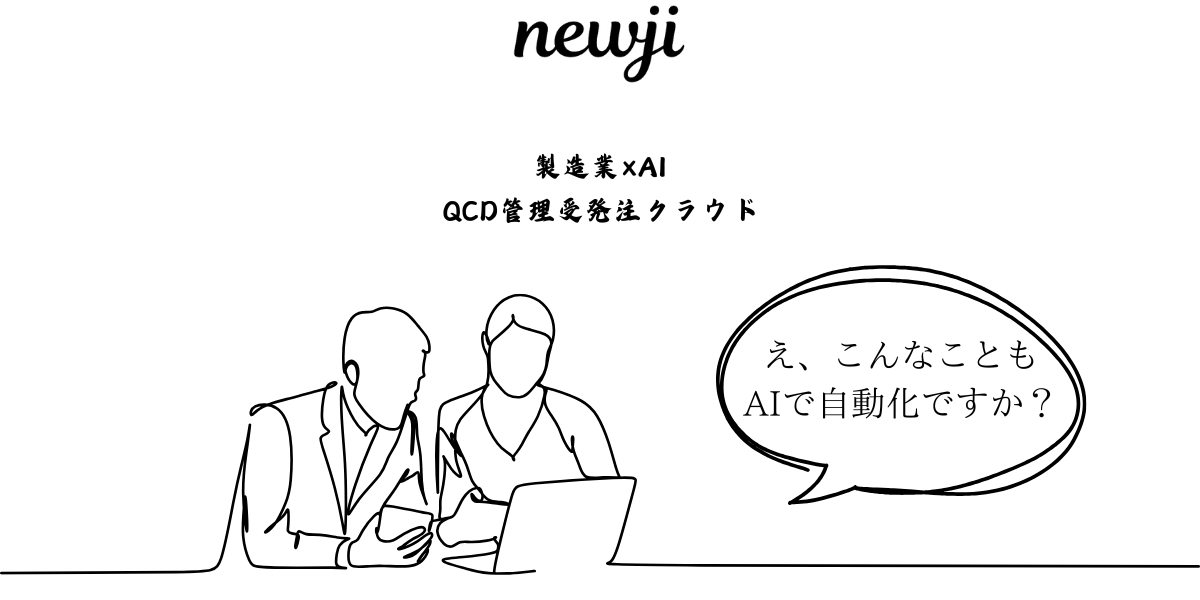
The difference between Vacuum Deposition and Sputtering
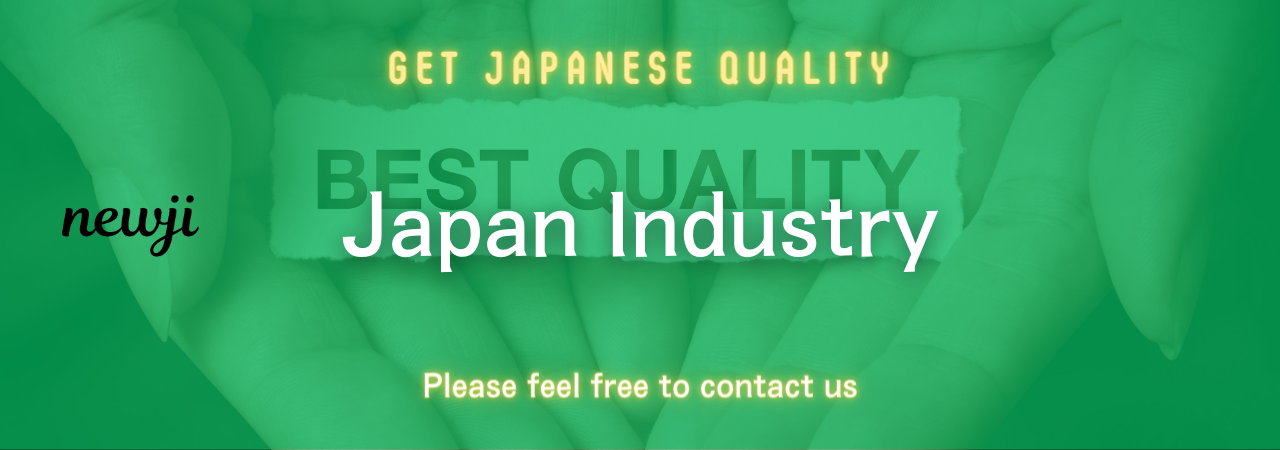
Vacuum deposition and sputtering are two widely used techniques in the field of thin film coating technologies.
These processes are essential in industries ranging from electronics to optics, providing the means to create advanced materials with specific properties.
Despite their common goal, they operate through distinct mechanisms.
Understanding the distinction between the two can help in selecting the most suitable technique for a particular application.
目次
What is Vacuum Deposition?
Vacuum deposition is a process used to create thin films and coatings by vaporizing a material and then allowing it to condense onto a substrate.
The key characteristic of vacuum deposition is that it takes place in a highly controlled environment, typically in a vacuum chamber.
This minimizes contamination and allows for precise control over the film’s properties.
Types of Vacuum Deposition
There are several types of vacuum deposition methods, the most common being Physical Vapor Deposition (PVD) and Chemical Vapor Deposition (CVD).
Physical Vapor Deposition (PVD)
PVD involves physical processes to deposit thin films.
It typically includes techniques like evaporation and sputtering, wherein the source material is physically vaporized and then condensed onto the substrate.
Chemical Vapor Deposition (CVD)
CVD, on the other hand, involves chemical reactions to produce a thin film.
In this method, gaseous reactants form a solid material that coats the substrate through a series of chemical reactions.
CVD is particularly useful for creating very thin, high-quality films.
What is Sputtering?
Sputtering is a specific type of PVD technique used to deposit thin films by means of sputtering a target material.
During sputtering, ions (often from an inert gas like argon) bombard the target material, causing atoms to eject from the target.
These ejected atoms then travel to and deposit on the substrate, forming a thin film.
How Sputtering Works
The sputtering process takes place in a vacuum chamber to ensure a controlled environment.
An electrical potential is applied to create a plasma from the inert gas, usually argon.
The positively charged ions from the plasma collide with the negatively charged target material, knocking atoms loose.
These free atoms then condense onto the substrate as a thin film.
Key Differences Between Vacuum Deposition and Sputtering
Understanding the differences between vacuum deposition and sputtering can help determine which process is more suitable for specific applications.
Method of Film Creation
In vacuum deposition, the material is typically vaporized either through physical means (as in PVD) or through chemical reactions (as in CVD).
Sputtering, on the other hand, relies on the physical ejection of atoms from a target material due to ion bombardment.
Material Suitability
Both techniques can be used with a wide range of materials, but they have their particular strengths.
Vacuum deposition, particularly CVD, is better suited for creating very thin and uniform films of certain complex materials.
Sputtering excels at depositing metals and alloys with high precision and is ideal for creating films with specific properties like electrical conductivity.
Film Thickness and Uniformity
Vacuum deposition methods often allow for more uniform and thinner films.
This is particularly true for CVD processes, which can produce films at the atomic level.
Sputtering is also capable of creating very thin films, but it might not always achieve the same level of uniformity as CVD.
Cost and Practicality
The cost of implementing these techniques can vary.
Vacuum deposition setups, especially for CVD, can be more expensive due to the need for precise control and complex machinery.
Sputtering systems can be more straightforward and less costly, although this depends on the specific requirements of the film being deposited.
Applications
Both vacuum deposition and sputtering find applications in different industries.
Vacuum deposition is extensively used in semiconductor manufacturing, solar cells, and protective coatings.
Sputtering is widely used in the production of electronic components, data storage devices, and decorative coatings.
Overlap and Integration
In many instances, the techniques can be used in tandem or in a hybrid manner to achieve desired film characteristics.
For example, initial layers might be deposited using a vacuum deposition technique followed by sputtering for additional layers with different properties.
Future Trends
As technology evolves, the lines between these methods can blur, with ongoing research pushing the boundaries of what is possible.
New materials and more sophisticated control systems continue to expand the applications for both vacuum deposition and sputtering.
Understanding both methods allows for better decision-making and innovation in material science.
Conclusion
Vacuum deposition and sputtering are both essential in the realm of thin film technologies, each with its unique advantages and applications.
Vacuum deposition, encompassing both PVD and CVD, offers benefits in terms of material versatility and film uniformity.
Sputtering stands out for its precision in depositing metals and alloys.
Choosing the right method depends on the specific requirements of the application, including material type, film thickness, uniformity, and cost considerations.
Both techniques will continue to play critical roles in technological advancements, making it essential for professionals to understand their distinct characteristics and potential overlaps.
資料ダウンロード
QCD調達購買管理クラウド「newji」は、調達購買部門で必要なQCD管理全てを備えた、現場特化型兼クラウド型の今世紀最高の購買管理システムとなります。
ユーザー登録
調達購買業務の効率化だけでなく、システムを導入することで、コスト削減や製品・資材のステータス可視化のほか、属人化していた購買情報の共有化による内部不正防止や統制にも役立ちます。
NEWJI DX
製造業に特化したデジタルトランスフォーメーション(DX)の実現を目指す請負開発型のコンサルティングサービスです。AI、iPaaS、および先端の技術を駆使して、製造プロセスの効率化、業務効率化、チームワーク強化、コスト削減、品質向上を実現します。このサービスは、製造業の課題を深く理解し、それに対する最適なデジタルソリューションを提供することで、企業が持続的な成長とイノベーションを達成できるようサポートします。
オンライン講座
製造業、主に購買・調達部門にお勤めの方々に向けた情報を配信しております。
新任の方やベテランの方、管理職を対象とした幅広いコンテンツをご用意しております。
お問い合わせ
コストダウンが利益に直結する術だと理解していても、なかなか前に進めることができない状況。そんな時は、newjiのコストダウン自動化機能で大きく利益貢献しよう!
(Β版非公開)