- お役立ち記事
- The difference between Work Improvement and Process Improvement
月間76,176名の
製造業ご担当者様が閲覧しています*
*2025年3月31日現在のGoogle Analyticsのデータより
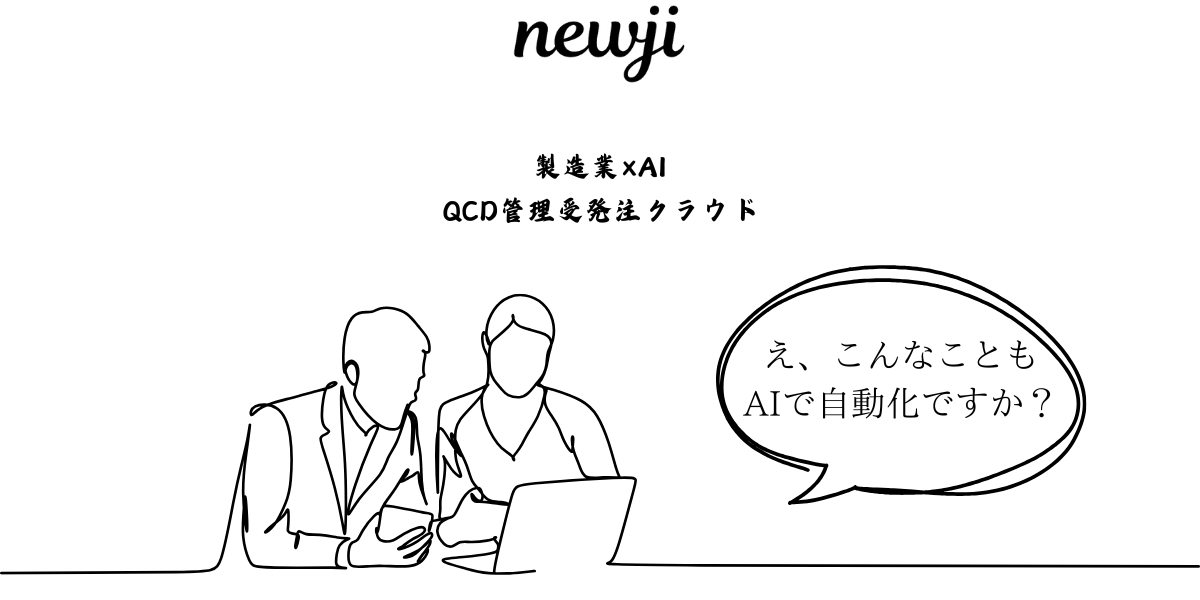
The difference between Work Improvement and Process Improvement
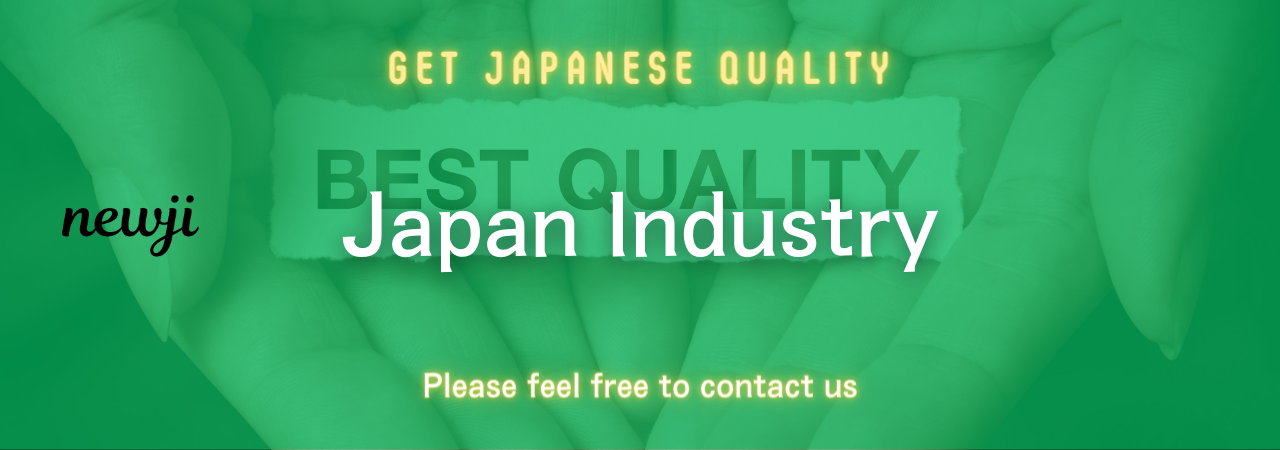
In today’s fast-paced business environment, staying competitive often means constantly seeking ways to improve.
While both work improvement and process improvement are essential efforts organizations undertake to enhance productivity and efficiency, they are not the same thing.
Understanding the difference between the two can help companies make more targeted changes that lead to significant, sustainable gains.
目次
Understanding Work Improvement
Work improvement typically focuses on individual tasks and how they are performed.
It aims to refine the execution of specific job duties to make them more effective and efficient.
Efforts often focus on enhancing the skills of employees or updating the tools and techniques they use.
The goal is to improve outcomes on a micro-level, one task, or role at a time.
Strategies for Work Improvement
– **Training Programs:** Offering comprehensive training and development programs can help employees acquire new skills or refine existing ones.
This can directly impact their job performance and improve overall productivity.
– **Feedback Processes:** Regular feedback sessions provide insights into areas where employees can improve, helping them fine-tune their methods.
– **Resource Upgrades:** Updating the tools, software, or equipment employees use can lead to more efficient task completion.
For example, switching to more advanced software can reduce the time needed for data entry tasks.
Examples of Work Improvement
Imagine a customer service representative who handles calls manually.
With a work improvement strategy, the company might invest in training to enhance their communication skills, upgrade their phone system, or introduce customer relationship management software.
These changes aim to directly impact the quality and speed of the representative’s work, leading to better customer satisfaction.
Understanding Process Improvement
Process improvement, on the other hand, focuses on the workflow and procedures within an organization.
It seeks to optimize entire processes to achieve greater efficiency and effectiveness.
Rather than concentrating on individual tasks, process improvement aims to refine how tasks interconnect and flow from one stage to another, often involving multiple employees or departments.
Strategies for Process Improvement
– **Mapping Processes:** Developing a detailed map of existing workflows can identify bottlenecks, redundancies, and inefficiencies.
By understanding the current state, companies can target specific areas for improvement.
– **Lean Methodology:** Lean process improvement focuses on eliminating waste and improving flow, often through techniques like Value Stream Mapping or the 5S system.
– **Automation:** Implementing automation technologies can streamline repetitive or complex processes, leading to faster and more accurate results.
Examples of Process Improvement
Consider a manufacturing company that wants to enhance its production line.
By analyzing the entire process from raw materials to final product, the company might identify steps that could be automated, such as inventory tracking or quality control.
Introducing a conveyor system to transport materials might speed up production and reduce labor costs, leading to significant improvements in overall process efficiency.
Key Differences between Work Improvement and Process Improvement
Scope
Work improvement is usually narrow-focused, targeting single tasks or individual roles.
Process improvement, however, has a broader scope and aims to enhance the entire workflow.
Objective
The primary objective of work improvement is to enhance the performance of specific tasks.
Process improvement aims to optimize entire workflows and eliminate inefficiencies.
Approach
Work improvement often involves training, feedback, and resource upgrades.
In contrast, process improvement focuses on mapping workflows, employing Lean methodologies, and implementing automation.
Impact
Work improvement can lead to noticeable gains in individual productivity, whereas process improvement can result in more substantial, organization-wide enhancements.
When to Focus on Work Improvement
Work improvement initiatives are particularly beneficial when:
– **Skill Gaps Exist:** When employees need to enhance specific skills to meet job requirements.
– **Performance Is Inconsistent:** If individual performance varies significantly, targeted improvement can address these disparities.
– **Tools Are Outdated:** Updating resources and tools can lead to immediate productivity gains.
When to Focus on Process Improvement
Process improvement efforts are most effective when:
– **Workflows Are Inefficient:** If the current processes have bottlenecks, delays, or redundant steps, optimizing these can lead to significant improvements.
– **Cross-Departmental Issues Arise:** When challenges span multiple areas of the organization, addressing the overall process can yield better results.
– **Scaling Is Necessary:** For growing companies, scalable processes are essential to handle increased workload effectively.
Combining Both for Maximum Impact
While distinguishing between work and process improvement is essential, the most impactful approach often involves a combination of both.
Focusing solely on work improvement may not address underlying process inefficiencies, and vice versa.
A balanced strategy ensures that individual tasks and broader workflows are both optimized.
Integrated Approaches
– **Employee Training with Process Redesign:** Combining skills training with a review and redesign of relevant processes can lead to more effective implementation of new skills.
– **Automation with Task Optimization:** Implementing automated solutions while simultaneously refining individual tasks ensures that technology complements and enhances human efforts.
Conclusion
Understanding the difference between work improvement and process improvement allows organizations to apply the right strategies for the desired outcome.
While work improvement focuses on individual tasks and roles, process improvement aims to optimize entire workflows.
By addressing both aspects, companies can achieve comprehensive improvements that boost efficiency and productivity across the board.
Balancing efforts in both areas can help create a more dynamic, effective, and competitive organization.
資料ダウンロード
QCD管理受発注クラウド「newji」は、受発注部門で必要なQCD管理全てを備えた、現場特化型兼クラウド型の今世紀最高の受発注管理システムとなります。
ユーザー登録
受発注業務の効率化だけでなく、システムを導入することで、コスト削減や製品・資材のステータス可視化のほか、属人化していた受発注情報の共有化による内部不正防止や統制にも役立ちます。
NEWJI DX
製造業に特化したデジタルトランスフォーメーション(DX)の実現を目指す請負開発型のコンサルティングサービスです。AI、iPaaS、および先端の技術を駆使して、製造プロセスの効率化、業務効率化、チームワーク強化、コスト削減、品質向上を実現します。このサービスは、製造業の課題を深く理解し、それに対する最適なデジタルソリューションを提供することで、企業が持続的な成長とイノベーションを達成できるようサポートします。
製造業ニュース解説
製造業、主に購買・調達部門にお勤めの方々に向けた情報を配信しております。
新任の方やベテランの方、管理職を対象とした幅広いコンテンツをご用意しております。
お問い合わせ
コストダウンが利益に直結する術だと理解していても、なかなか前に進めることができない状況。そんな時は、newjiのコストダウン自動化機能で大きく利益貢献しよう!
(β版非公開)