- お役立ち記事
- The difference between Work Standards and Work Manual
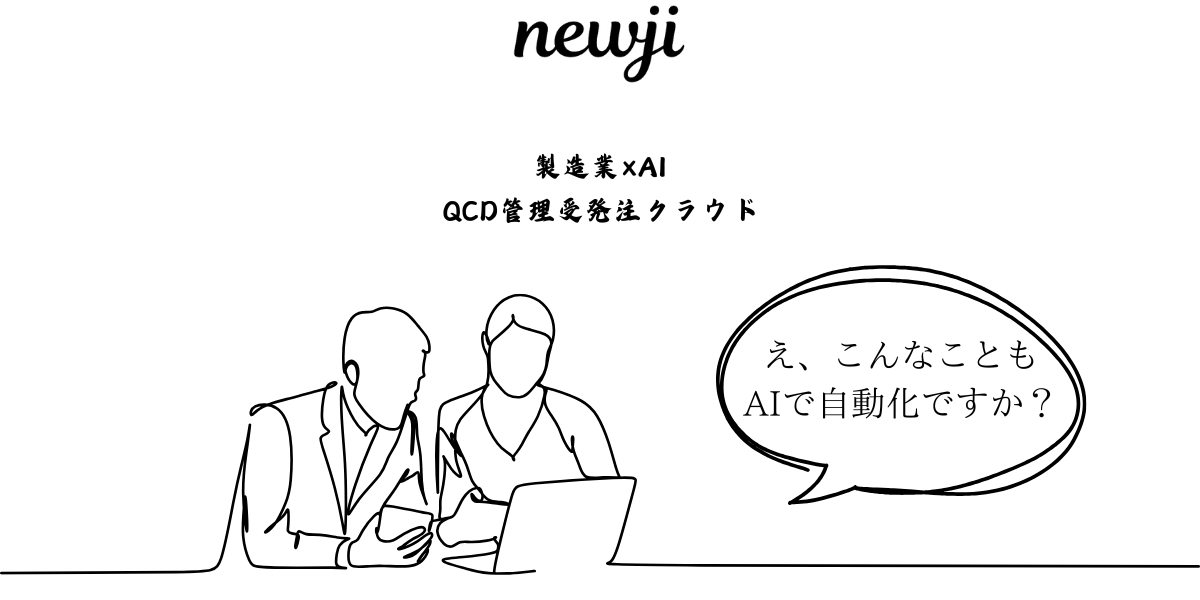
The difference between Work Standards and Work Manual
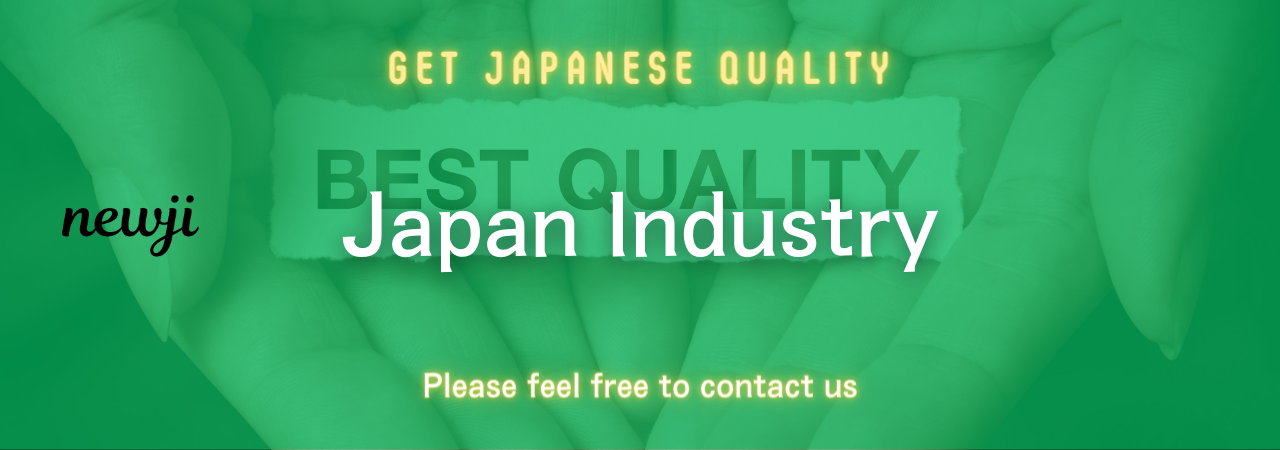
When it comes to ensuring smooth operations and consistency in any organization, understanding the difference between work standards and work manuals is essential.
Both tools serve distinct purposes, and knowing how to utilize them can greatly enhance productivity and maintain quality control.
Let’s dive into the specifics of work standards and work manuals to illuminate their unique roles.
目次
What Are Work Standards?
Work standards can be thought of as the benchmarks for performance.
They set the expected levels of quality, time, and efficiency for tasks within an organization.
Key Features of Work Standards
Work standards are concise and focus on the end results.
They outline the ideal performance that employees should aim for, ensuring that everyone in the organization understands what constitutes acceptable work.
For example, a work standard in a manufacturing setting might specify that a certain product must be produced within five minutes while adhering to specific quality guidelines.
These standards don’t typically dive into the step-by-step process; rather, they highlight what the outcome should look like.
Benefits of Work Standards
One of the primary benefits of work standards is that they provide clear expectations for employees.
When everyone knows what is expected, it’s easier to measure performance and identify areas that need improvement.
Work standards also help in maintaining consistency across the board.
When each employee knows the benchmark, the quality of work is more likely to be uniform, reducing the risk of errors and enhancing customer satisfaction.
What Are Work Manuals?
Unlike work standards, work manuals are comprehensive guides that describe how to perform tasks.
They offer step-by-step instructions to ensure that employees follow the correct procedures.
Key Features of Work Manuals
Work manuals are detailed and instructional.
They include all the necessary information an employee might need to complete a task, from starting steps to final touches.
For instance, a work manual for a customer service representative might cover how to answer calls, log information, address customer concerns, and escalate issues if needed.
This guide ensures that every employee receives the same training and follows the same procedures.
Benefits of Work Manuals
The main advantage of work manuals is that they enable employees to perform tasks correctly and efficiently, even if they have minimal prior experience.
When a clear guide is available, new hires can quickly get up to speed without needing constant supervision.
Moreover, work manuals help maintain quality by standardizing procedures.
This consistency is vital in industries where precision and uniformity are crucial, such as healthcare, manufacturing, and finance.
The Relationship Between Work Standards and Work Manuals
While work standards and work manuals serve different purposes, they are inherently connected.
Work standards set the goals, and work manuals provide the methods to achieve those goals.
In essence, if work standards define the “what,” work manuals explain the “how.”
Implementing Both for Maximum Efficiency
For an organization to function seamlessly, it’s beneficial to have both work standards and work manuals in place.
Work standards establish clear expectations, while work manuals ensure that all employees have the information they need to meet those expectations.
When combined, these tools can lead to higher productivity, better quality control, and more streamlined operations.
Examples of Work Standards and Work Manuals in Different Industries
To further clarify the distinction, let’s look at how work standards and work manuals might be used in various industries.
Manufacturing
In a manufacturing plant, work standards might specify that a widget must be produced within 10 minutes and pass five quality checks before shipment.
The work manual would then provide detailed steps on how to operate the machinery, perform quality checks, and package the widget.
Healthcare
In a hospital, a work standard might state that patient vitals should be checked every hour.
The work manual would detail how to take a patient’s blood pressure, temperature, and heart rate, as well as how to record these measurements accurately.
Customer Service
For a customer service department, work standards could dictate response times.
For example, every customer inquiry must be addressed within 24 hours.
The work manual would outline how to log into the support system, access customer records, and provide suitable responses based on different scenarios.
Creating Effective Work Standards and Work Manuals
Both tools should be clear, comprehensive, and periodically reviewed to ensure they remain relevant and effective.
Tips for Developing Work Standards
When creating work standards, focus on clarity and achievability.
Set realistic benchmarks that reflect both the company’s goals and the capabilities of your workforce.
Involve employees in the creation process.
Their input can provide valuable insights into what is practical and achievable.
Tips for Developing Work Manuals
Your work manuals should be detailed and easy to understand.
Include visuals such as diagrams or screenshots if necessary to aid comprehension.
Regularly update the manuals to incorporate new processes or address any identified issues.
Ensure that the language used is straightforward to make the manuals user-friendly.
This will help in training new employees and providing a quick reference for existing ones.
Conclusion
Understanding and utilizing both work standards and work manuals are key to fostering an efficient and high-performing workplace.
While work standards set the goals and benchmarks for performance, work manuals provide the necessary instructions to achieve those goals.
Together, they create a framework that ensures consistency, quality, and continuous improvement.
By implementing clear work standards and comprehensive work manuals, organizations can enhance productivity, reduce errors, and maintain a high level of quality in their operations.
資料ダウンロード
QCD調達購買管理クラウド「newji」は、調達購買部門で必要なQCD管理全てを備えた、現場特化型兼クラウド型の今世紀最高の購買管理システムとなります。
ユーザー登録
調達購買業務の効率化だけでなく、システムを導入することで、コスト削減や製品・資材のステータス可視化のほか、属人化していた購買情報の共有化による内部不正防止や統制にも役立ちます。
NEWJI DX
製造業に特化したデジタルトランスフォーメーション(DX)の実現を目指す請負開発型のコンサルティングサービスです。AI、iPaaS、および先端の技術を駆使して、製造プロセスの効率化、業務効率化、チームワーク強化、コスト削減、品質向上を実現します。このサービスは、製造業の課題を深く理解し、それに対する最適なデジタルソリューションを提供することで、企業が持続的な成長とイノベーションを達成できるようサポートします。
オンライン講座
製造業、主に購買・調達部門にお勤めの方々に向けた情報を配信しております。
新任の方やベテランの方、管理職を対象とした幅広いコンテンツをご用意しております。
お問い合わせ
コストダウンが利益に直結する術だと理解していても、なかなか前に進めることができない状況。そんな時は、newjiのコストダウン自動化機能で大きく利益貢献しよう!
(Β版非公開)