- お役立ち記事
- The difference between Yield Improvement and Defect Reduction
The difference between Yield Improvement and Defect Reduction
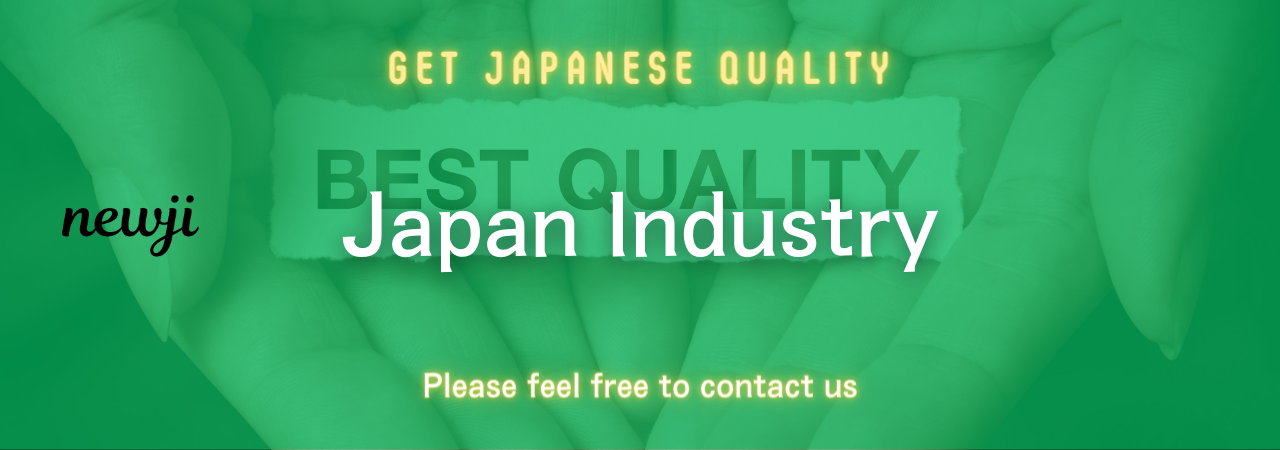
目次
Understanding Yield Improvement
Yield improvement is a term often used in manufacturing and production industries.
It refers to the process of increasing the number of products that meet quality standards, thus enhancing the overall efficiency of the production line.
When you aim for yield improvement, you’re focusing on producing more sellable or usable products.
This might involve refining procedures, updating machinery, or training workers to perform tasks more effectively.
Yield improvement is particularly important because it directly impacts a company’s bottom line.
Higher yields mean more products are available for sale, translating to higher revenue.
Additionally, improving yield can help a company remain competitive in a market where efficiency is key to success.
For instance, if a factory produces 100 units of a product and 90 units meet the set quality standards, the yield is 90%.
By implementing yield improvement techniques, the factory could potentially increase the number of quality units to 95 or even 98, thereby raising their yield percentage significantly.
Techniques for Yield Improvement
There are several techniques commonly employed to improve yield in a production setting.
Among these are:
1. **Process Optimization:** This involves analyzing and refining every stage of the production process to eliminate waste and inefficiencies.
It can include everything from adjusting temperatures and timings to ensuring that machinery is operating at peak performance.
2. **Quality Control Systems:** Implementing rigorous quality control checks throughout the production process can help identify defects early.
By catching problems early, you can prevent defective units from making it further down the line, thus improving the yield.
3. **Training and Development:** Ensuring that workers are properly trained in the latest techniques and technologies can also have a significant impact on yield improvement.
Well-trained employees are more likely to perform tasks correctly and efficiently, leading to fewer mistakes and higher-quality products.
Understanding Defect Reduction
Defect reduction, while closely related to yield improvement, focuses on minimizing the number of products that do not meet quality standards.
When a product is found to be defective, it typically cannot be sold and may need to be reworked or discarded.
Reducing defects is essential not only for improving yield but also for maintaining a company’s reputation for quality.
Defect reduction requires a thorough understanding of what causes defects in the first place.
These causes can range from machine malfunctions and human errors to material inconsistencies and design flaws.
By identifying and addressing the root causes of defects, companies can significantly reduce their occurrence.
Techniques for Defect Reduction
Here are some common strategies used to reduce defects in production:
1. **Root Cause Analysis:** This method involves identifying the underlying reasons for defects and addressing them at their source.
Techniques like the “5 Whys” or Fishbone Diagram can help teams drill down into the specific issues causing defects and develop targeted solutions.
2. **Statistical Process Control (SPC):** SPC involves monitoring production processes using statistical methods to promptly detect and correct issues.
By using control charts and other analytical tools, companies can identify variations that may lead to defects and take corrective action before they escalate.
3. **Preventive Maintenance:** Regular maintenance of machinery and equipment can prevent defects caused by wear and tear or unexpected breakdowns.
A proactive maintenance schedule ensures that machines operate smoothly and reduces the likelihood of defects due to equipment failure.
Comparing Yield Improvement and Defect Reduction
Though both yield improvement and defect reduction aim to enhance the quality and quantity of output, they focus on different aspects of the production process.
Yield improvement looks at the overall efficiency and output of the production line, aiming to boost the number of sellable units.
Defect reduction, on the other hand, concentrates on minimizing the number of defective products.
In many cases, efforts to improve yield and reduce defects will overlap.
For instance, enhancing worker training can lead to both higher yields and fewer defects.
Similarly, process optimization can contribute to both goals by making the production process more efficient and reducing inconsistencies that cause defects.
Balancing Both Approaches
For optimal results, it’s essential to balance efforts between yield improvement and defect reduction.
A singular focus on one area can lead to missed opportunities in the other.
For instance, solely focusing on yield improvement by ramping up production rates might lead to an increased number of defects if quality control is not proportionally enhanced.
Conversely, an exclusive focus on defect reduction could slow down production processes, negatively impacting yield.
By implementing a balanced approach, companies can ensure that they are producing the highest number of quality products in the most efficient manner possible.
This balance not only helps in maintaining high standards but also boosts profitability by reducing waste and optimizing resource utilization.
Practical Applications in the Industry
Yield improvement and defect reduction are crucial in various industries, from electronics manufacturing to food production.
In the semiconductor industry, for instance, yield improvement can mean the difference between profitability and loss.
Given the high cost and complexity of producing semiconductors, even a small increase in yield can result in substantial financial benefits.
In food production, defect reduction ensures that products are safe for consumption and meet regulatory standards.
Reducing defects in food production can involve everything from better storage conditions to more accurate measurements in recipes.
The result is a safer product and a stronger brand reputation for quality and reliability.
Case Study: Automotive Manufacturing
Consider an automotive manufacturing plant that produces car engines.
The company might use yield improvement techniques like process automation to increase the number of engines produced daily.
Simultaneously, they could employ defect reduction strategies like enhanced quality inspections and root cause analysis to reduce the number of faulty engines.
In this way, the company benefits from both higher yields and fewer defects, leading to better financial performance and customer satisfaction.
Conclusion
Understanding the difference between yield improvement and defect reduction is vital for any production-oriented business.
While yield improvement focuses on increasing the quantity of quality products, defect reduction aims to minimize the number of defective ones.
Both strategies are essential for achieving optimal results in terms of efficiency, quality, and profitability.
By implementing a balanced approach that incorporates techniques from both areas, companies can ensure that they are making the most of their resources and delivering high-quality products to their customers.
Whether you are in electronics, automotive, food, or any other industry, mastering these concepts can be the key to long-term success and competitiveness.
資料ダウンロード
QCD調達購買管理クラウド「newji」は、調達購買部門で必要なQCD管理全てを備えた、現場特化型兼クラウド型の今世紀最高の購買管理システムとなります。
ユーザー登録
調達購買業務の効率化だけでなく、システムを導入することで、コスト削減や製品・資材のステータス可視化のほか、属人化していた購買情報の共有化による内部不正防止や統制にも役立ちます。
NEWJI DX
製造業に特化したデジタルトランスフォーメーション(DX)の実現を目指す請負開発型のコンサルティングサービスです。AI、iPaaS、および先端の技術を駆使して、製造プロセスの効率化、業務効率化、チームワーク強化、コスト削減、品質向上を実現します。このサービスは、製造業の課題を深く理解し、それに対する最適なデジタルソリューションを提供することで、企業が持続的な成長とイノベーションを達成できるようサポートします。
オンライン講座
製造業、主に購買・調達部門にお勤めの方々に向けた情報を配信しております。
新任の方やベテランの方、管理職を対象とした幅広いコンテンツをご用意しております。
お問い合わせ
コストダウンが利益に直結する術だと理解していても、なかなか前に進めることができない状況。そんな時は、newjiのコストダウン自動化機能で大きく利益貢献しよう!
(Β版非公開)