- お役立ち記事
- The entire process of parts improvement that takes advantage of the experience of using the actual machine – an evaluation method that provides peace of mind to the client and achieves short delivery times
月間76,176名の
製造業ご担当者様が閲覧しています*
*2025年3月31日現在のGoogle Analyticsのデータより
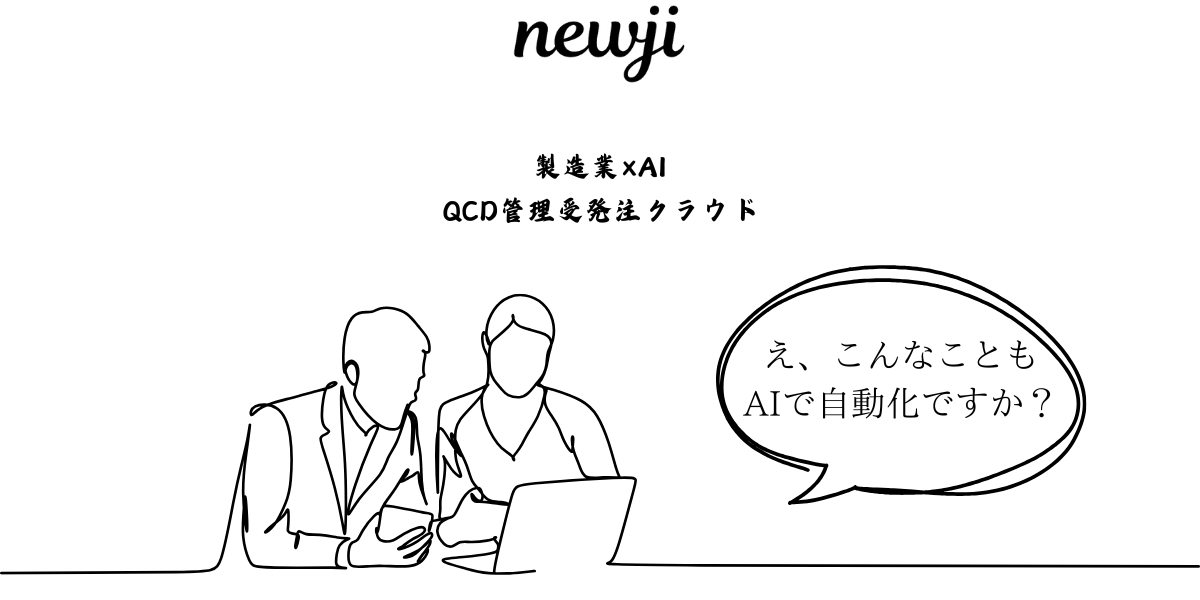
The entire process of parts improvement that takes advantage of the experience of using the actual machine – an evaluation method that provides peace of mind to the client and achieves short delivery times
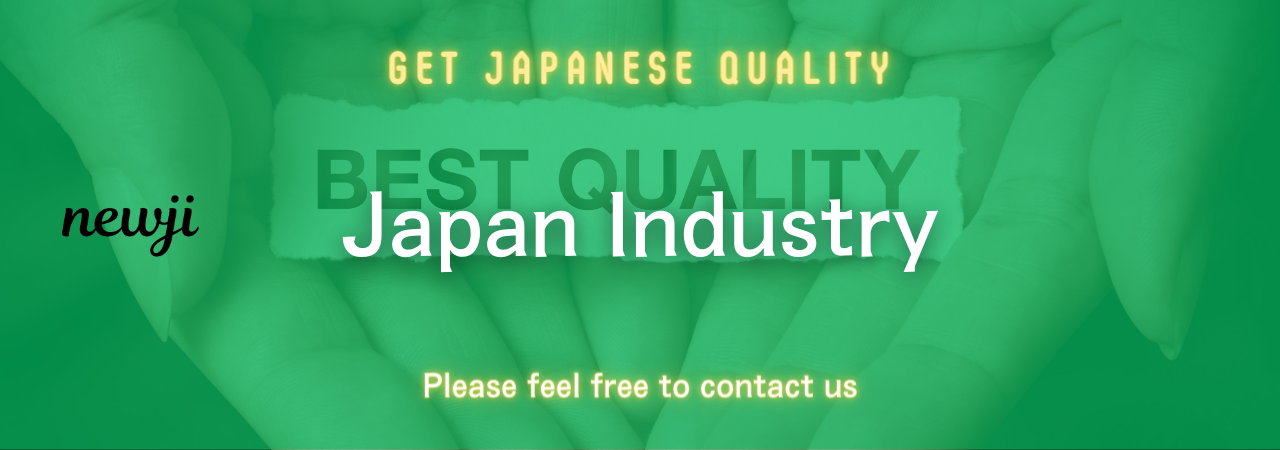
Understanding Parts Improvement Through Real-Life Experience
When it comes to manufacturing and engineering, the longevity and reliability of parts are crucial.
One effective way to ensure these attributes is the continuous improvement of parts based on real-life usage experiences.
The process not only assures quality but also enhances the overall performance of the machinery.
The Importance of Real-Life Experience in Parts Improvement
Understanding how a part functions under actual operating conditions provides insights that are often overlooked during the design phase.
This real-world data is essential in identifying weaknesses, wear points, and failure modes that weren’t apparent during initial testing.
Such firsthand experience with the machine allows engineers to develop solutions that specifically address observed issues.
The outcome is parts that are more durable, efficient, and better suited to their intended application.
Key Steps in the Parts Improvement Process
1. **Data Collection:** The first step involves meticulously gathering data from the machinery under various conditions.
This includes operational data, failure reports, and maintenance records.
The objective is to understand how often parts fail and under what conditions these failures generally occur.
2. **Analysis of Data:** After collecting data, it is crucial to analyze it effectively.
By examining patterns and identifying recurring problems, manufacturers can pinpoint which parts require improvement.
Statistics and predictive modeling are often employed to forecast future failures and improve design accordingly.
3. **Prototyping and Testing:** Once potential improvements are identified, the next step is prototyping new parts.
These prototypes undergo rigorous testing under simulated real-world conditions.
It aims to ensure that the proposed improvements will indeed enhance part performance.
4. **Implementation of Improvements:** If testing proves successful, improvements are then integrated into the production line.
This step is critical as it translates theoretical improvements into tangible benefits.
5. **Client Feedback:** Post-implementation, feedback from clients plays a vital role in validating performance improvements.
This ongoing dialog ensures that the parts meet client expectations and any additional issues can be quickly addressed.
Evaluating Parts Improvements for Reliability Assurance
Evaluation is integral to parts improvement as it measures the effectiveness of the enhancements.
For clients to have peace of mind, thorough verification is necessary.
This involves several phases:
– **Performance Metrics Assessment:** Determining whether the improvements have achieved the desired performance enhancements.
Key performance indicators include durability, efficiency, and functionality.
– **Reliability Testing:** Validation through stress tests ensures the part withstands extreme conditions beyond regular use.
– **Comparative Analysis:** Evaluating the improved part against its predecessor to quantify technological advancement.
This can involve direct comparisons in performance, life span, and maintenance needs.
Benefits of Parts Improvement for Short Delivery Times
The structured approach to parts improvement aids in shortening delivery times.
Here’s how:
– **Efficient Problem Resolution:** By addressing issues based on real-world data, solutions are more precise and effective.
This minimizes delays caused by unexpected failures or suboptimal performance.
– **Streamlined Production Processes:** As improvements become standardized, manufacturers can streamline their processes, accelerating time-to-market for new parts.
– **Enhanced Predictive Maintenance:** Improved parts contribute to a reduced need for emergency repairs, allowing for planned maintenance schedules that ensure machinery operates smoothly.
– **Client Confidence and Retention:** By delivering consistent quality and enhanced performance, client trust grows, translating into repeat business and strong industry reputation.
Conclusion
The integration of real-life experience into parts improvement is a crucial step in ensuring machinery reliability.
Through a well-structured process that includes data collection, analysis, prototyping, testing, and client feedback, improvements become both quantifiable and effective.
When manufacturers focus on experience-driven enhancements, they not only achieve greater operational efficiency but also foster trust with their clients.
This strategy not only reassures clients but also allows for shorter delivery times and a more robust market presence.
資料ダウンロード
QCD管理受発注クラウド「newji」は、受発注部門で必要なQCD管理全てを備えた、現場特化型兼クラウド型の今世紀最高の受発注管理システムとなります。
ユーザー登録
受発注業務の効率化だけでなく、システムを導入することで、コスト削減や製品・資材のステータス可視化のほか、属人化していた受発注情報の共有化による内部不正防止や統制にも役立ちます。
NEWJI DX
製造業に特化したデジタルトランスフォーメーション(DX)の実現を目指す請負開発型のコンサルティングサービスです。AI、iPaaS、および先端の技術を駆使して、製造プロセスの効率化、業務効率化、チームワーク強化、コスト削減、品質向上を実現します。このサービスは、製造業の課題を深く理解し、それに対する最適なデジタルソリューションを提供することで、企業が持続的な成長とイノベーションを達成できるようサポートします。
製造業ニュース解説
製造業、主に購買・調達部門にお勤めの方々に向けた情報を配信しております。
新任の方やベテランの方、管理職を対象とした幅広いコンテンツをご用意しております。
お問い合わせ
コストダウンが利益に直結する術だと理解していても、なかなか前に進めることができない状況。そんな時は、newjiのコストダウン自動化機能で大きく利益貢献しよう!
(β版非公開)