- お役立ち記事
- “The Evolution of Japanese Manufacturing: Innovations Driving Global Excellence”
“The Evolution of Japanese Manufacturing: Innovations Driving Global Excellence”
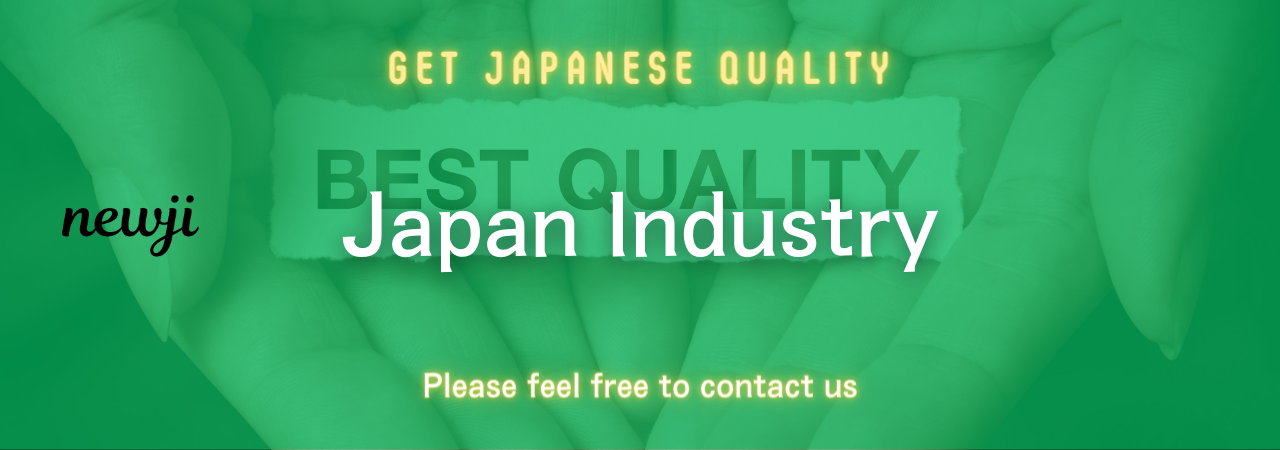
目次
Introduction to the Evolution of Japanese Manufacturing
Japanese manufacturing has long been synonymous with quality, innovation, and efficiency. Over the past few decades, Japan has continually transformed its manufacturing landscape, setting benchmarks for industries worldwide. This evolution is driven by a commitment to continuous improvement, technological advancements, and strategic procurement practices. Understanding the journey of Japanese manufacturing offers valuable insights for global businesses aiming to achieve excellence in their operations.
The Foundations of Japanese Manufacturing Excellence
Lean Manufacturing and the Toyota Production System
At the heart of Japanese manufacturing lies the Toyota Production System (TPS), a pioneering approach that emphasizes waste reduction, Just-In-Time (JIT) production, and continuous improvement, or Kaizen. Lean manufacturing principles derived from TPS have been adopted globally, revolutionizing production processes by enhancing efficiency and reducing costs.
Quality Control and Total Quality Management
Japanese manufacturers prioritize quality at every stage of production. Total Quality Management (TQM) integrates quality control into every organizational process, ensuring that products meet the highest standards. Techniques such as Statistical Process Control (SPC) and the use of quality circles empower employees to contribute to quality improvements actively.
Innovations Driving Japanese Manufacturing
Automation and Robotics
Japan has been at the forefront of automation and robotics, integrating advanced technologies to enhance precision and productivity. Automated systems reduce human error, increase production speed, and ensure consistency in product quality. Robotics also play a crucial role in sectors such as automotive and electronics, where precision is paramount.
Industry 4.0 and Smart Manufacturing
Embracing Industry 4.0, Japanese manufacturers are incorporating Internet of Things (IoT), artificial intelligence (AI), and big data analytics into their operations. Smart factories leverage these technologies to optimize supply chains, predict maintenance needs, and enable real-time decision-making, thereby increasing overall efficiency and responsiveness to market changes.
Procurement and Purchasing Strategies
Building Strong Supplier Relationships
In Japanese manufacturing, strong supplier relationships are essential. Companies engage in long-term partnerships with suppliers, fostering trust and collaboration. This approach ensures reliable supply chains, consistent quality, and the ability to innovate together. Regular communication and mutual support are key components of these relationships.
Strategic Sourcing and Supplier Integration
Strategic sourcing involves selecting suppliers based on their ability to contribute to the company’s long-term goals. Japanese manufacturers often integrate suppliers into their production processes, sharing information and collaborating on product development. This integration enhances efficiency, reduces lead times, and aligns suppliers’ capabilities with the company’s strategic objectives.
Advantages of Japanese Manufacturing Practices
High Quality and Reliability
Japanese manufacturing is renowned for its high-quality products. Rigorous quality control measures and a culture of continuous improvement ensure that products meet stringent standards. This reliability builds consumer trust and strengthens brand reputation globally.
Operational Efficiency
Lean manufacturing and automation drive operational efficiency in Japanese factories. By minimizing waste and optimizing processes, companies can produce more with fewer resources, reducing costs and increasing profitability.
Innovation and Adaptability
Japanese manufacturers excel in innovation, continuously adopting new technologies and methodologies. Their ability to adapt to changing market conditions and incorporate cutting-edge advancements keeps them competitive on the global stage.
Challenges and Disadvantages
High Initial Investment
Implementing advanced manufacturing technologies and maintaining high-quality standards require significant initial investments. Small and medium-sized enterprises (SMEs) may find it challenging to allocate the necessary resources for such investments.
Aging Workforce
Japan faces an aging workforce, which can impact manufacturing productivity and innovation. As experienced workers retire, there is a need for effective knowledge transfer and attracting younger talent to sustain the industry’s growth.
Global Competition
While Japanese manufacturers have a strong global presence, they face intense competition from emerging economies. Adapting to global market trends and maintaining cost competitiveness are ongoing challenges.
Supplier Negotiation Techniques
Win-Win Negotiations
Japanese negotiation techniques often focus on creating win-win situations. Emphasizing mutual benefits and long-term partnerships, negotiations aim to build trust and ensure both parties gain value from the agreement.
Consensus Building
Consensus is crucial in Japanese negotiations. Decision-making involves input from multiple stakeholders, ensuring that agreements are well-rounded and supported by all parties involved. This approach fosters collaboration and reduces conflicts.
Patience and Persistence
Patience is a key aspect of Japanese negotiation strategies. Building relationships and negotiating terms may take longer, but this persistence ensures solid and sustainable agreements that benefit both parties in the long term.
Market Conditions and Trends
Global Supply Chain Dynamics
Japanese manufacturers navigate complex global supply chains, balancing the benefits of international sourcing with the challenges of logistics and geopolitical uncertainties. Diversifying supply sources and enhancing supply chain resilience are ongoing strategies to manage these dynamics.
Sustainability and Green Manufacturing
Sustainability has become a significant focus in Japanese manufacturing. Companies are adopting eco-friendly practices, reducing carbon footprints, and developing sustainable products to meet increasing environmental regulations and consumer demand for green products.
Digital Transformation
The digital transformation trend is reshaping Japanese manufacturing. Integrating digital technologies into production processes enhances efficiency, enables data-driven decision-making, and supports the development of innovative products and services.
Best Practices in Japanese Manufacturing
Emphasizing Continuous Improvement (Kaizen)
Continuous improvement is embedded in Japanese manufacturing culture. Regularly reviewing and refining processes ensures ongoing enhancements in quality, efficiency, and productivity. Engaging employees at all levels in Kaizen initiatives fosters a culture of proactive problem-solving.
Employee Training and Development
Investing in employee training and development is a cornerstone of Japanese manufacturing. Skilled workers are essential for maintaining high-quality standards and implementing advanced manufacturing techniques. Ongoing training programs ensure that employees stay updated with the latest industry trends and technologies.
Lean Inventory Management
Japanese manufacturers excel in lean inventory management, minimizing excess inventory and reducing carrying costs. Techniques such as JIT production ensure that materials and components are available precisely when needed, enhancing cash flow and operational efficiency.
Impact of Technology on Procurement and Purchasing
Automation in Procurement Processes
Automation technologies streamline procurement processes, reducing manual tasks and increasing accuracy. Automated systems handle tasks such as order processing, invoice management, and supplier communications, freeing up resources for strategic activities.
Data-Driven Decision Making
Leveraging big data and analytics, Japanese manufacturers make informed procurement decisions. Analyzing market trends, supplier performance, and cost data enables companies to optimize sourcing strategies and negotiate better terms with suppliers.
Blockchain for Supply Chain Transparency
Blockchain technology enhances supply chain transparency by providing a secure and immutable record of transactions. This transparency builds trust with suppliers and customers, ensures compliance with regulations, and helps prevent fraud and counterfeiting.
Case Studies of Japanese Manufacturing Excellence
Automotive Industry: Toyota
Toyota is a prime example of Japanese manufacturing excellence. Through the implementation of TPS, Toyota has achieved unparalleled efficiency and quality in automobile production. The company’s focus on continuous improvement and strong supplier partnerships has set industry standards globally.
Electronics Industry: Sony
Sony has been a leader in the electronics industry, known for its innovative products and high-quality manufacturing processes. By investing in R&D and maintaining stringent quality controls, Sony has sustained its competitive edge in the global market.
Precision Machinery: Fanuc
Fanuc is renowned for its precision machinery and robotics. The company’s commitment to technological innovation and quality has made it a key player in the automation sector, supplying advanced machinery to industries worldwide.
Future Outlook for Japanese Manufacturing
Integration of Advanced Technologies
The future of Japanese manufacturing lies in the further integration of advanced technologies such as AI, IoT, and robotics. These technologies will continue to enhance productivity, quality, and flexibility in production processes.
Focus on Sustainability
Sustainability will remain a critical focus, with Japanese manufacturers adopting greener practices and developing environmentally friendly products. This commitment will not only meet regulatory requirements but also cater to the growing consumer demand for sustainable products.
Global Collaboration and Expansion
Japanese manufacturers will increasingly engage in global collaborations and expand their presence in emerging markets. Building strategic partnerships and adapting to diverse market needs will be essential for sustained growth and competitiveness.
Conclusion
The evolution of Japanese manufacturing is a testament to the power of innovation, quality, and strategic procurement practices. By embracing continuous improvement, leveraging advanced technologies, and fostering strong supplier relationships, Japanese manufacturers have achieved global excellence. As the industry continues to adapt to changing market conditions and technological advancements, the principles that underpin Japanese manufacturing will remain pivotal in shaping the future of global manufacturing.
資料ダウンロード
QCD調達購買管理クラウド「newji」は、調達購買部門で必要なQCD管理全てを備えた、現場特化型兼クラウド型の今世紀最高の購買管理システムとなります。
ユーザー登録
調達購買業務の効率化だけでなく、システムを導入することで、コスト削減や製品・資材のステータス可視化のほか、属人化していた購買情報の共有化による内部不正防止や統制にも役立ちます。
NEWJI DX
製造業に特化したデジタルトランスフォーメーション(DX)の実現を目指す請負開発型のコンサルティングサービスです。AI、iPaaS、および先端の技術を駆使して、製造プロセスの効率化、業務効率化、チームワーク強化、コスト削減、品質向上を実現します。このサービスは、製造業の課題を深く理解し、それに対する最適なデジタルソリューションを提供することで、企業が持続的な成長とイノベーションを達成できるようサポートします。
オンライン講座
製造業、主に購買・調達部門にお勤めの方々に向けた情報を配信しております。
新任の方やベテランの方、管理職を対象とした幅広いコンテンツをご用意しております。
お問い合わせ
コストダウンが利益に直結する術だと理解していても、なかなか前に進めることができない状況。そんな時は、newjiのコストダウン自動化機能で大きく利益貢献しよう!
(Β版非公開)