- お役立ち記事
- The Evolution of Micro-Machining Technology and Its Impact on Manufacturing: Achieving Precision and Efficiency
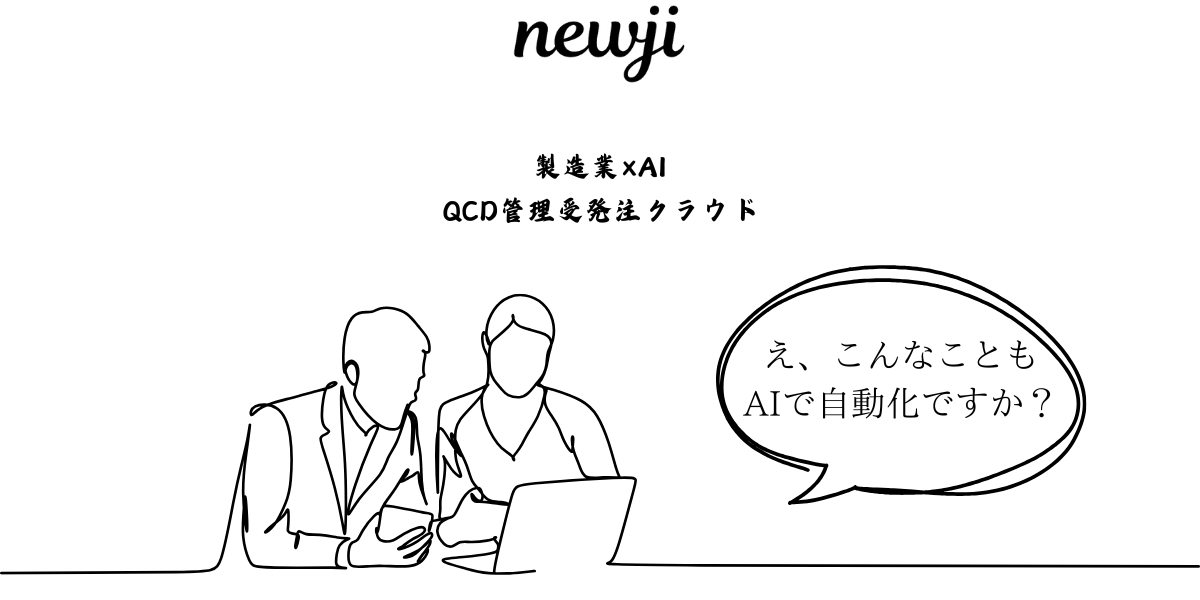
The Evolution of Micro-Machining Technology and Its Impact on Manufacturing: Achieving Precision and Efficiency
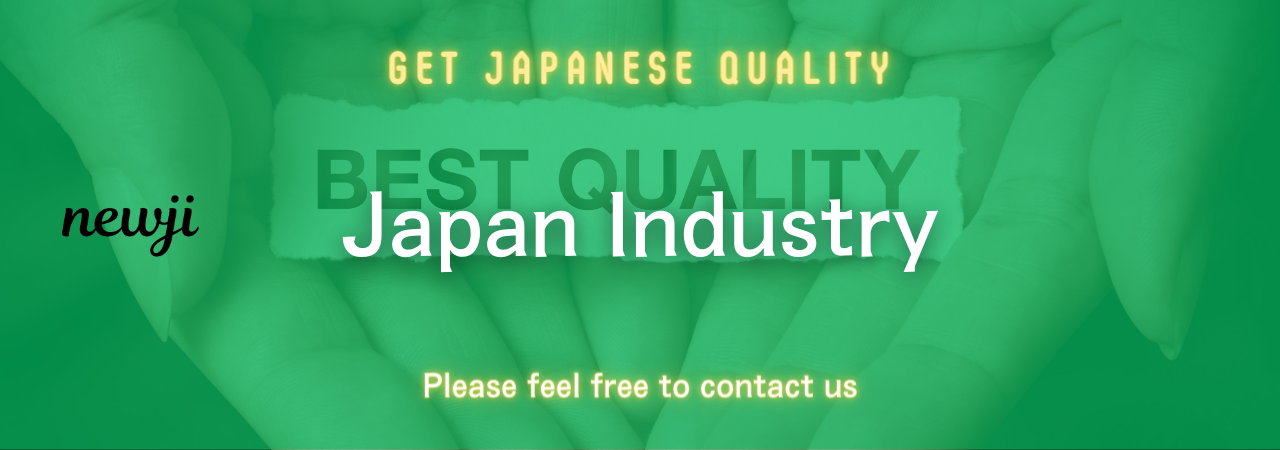
Micro-machining technology has undergone significant advancements over the years, profoundly impacting the manufacturing industry.
This evolution has led to enhanced precision, efficiency, and the ability to produce smaller and more complex components.
Understanding the historical context, technological advancements, applications, and future prospects of micro-machining is crucial for appreciating its role in modern manufacturing.
目次
Understanding Micro-Machining Technology
Micro-machining refers to the process of creating microscale features on a workpiece using various mechanical, electrical, and chemical methods.
Unlike traditional machining, which deals with larger components, micro-machining operates at much smaller scales, often in the range of micrometers.
This technology is fundamental for producing components used in electronics, medical devices, and aerospace industries, among others.
Historical Context
The origins of micro-machining technology can be traced back to the development of precision engineering in the mid-20th century.
Initial efforts focused on improving the accuracy of traditional machining processes.
However, as technology advanced, the need for even smaller and more precise components became evident.
With the advent of computer numerical control (CNC) machines, micro-machining saw a significant leap in capability.
CNC machines allowed for greater control and precision, paving the way for modern micro-machining techniques.
The integration of computer systems enabled intricate patterns and designs to be executed with unparalleled accuracy.
Key Technological Advancements
Several technological advancements have driven the evolution of micro-machining, each contributing to its heightened precision and efficiency.
One of the most notable developments is the refinement of micro-drilling and micro-milling tools.
These tools are designed to handle the high demands of micro-scale machining, allowing for the creation of extremely fine features.
The introduction of diamond-coated tools and the use of carbide materials have further enhanced tool durability and performance.
Laser micro-machining has also revolutionized the industry.
By utilizing focused laser beams, manufacturers can achieve precise cuts and engravings with minimal thermal impact on the workpiece.
This method is particularly useful for processing delicate materials that are susceptible to damage from traditional machining methods.
Another significant advancement is the development of electrochemical machining (ECM) techniques.
ECM uses electrical energy to remove material from a workpiece, offering a high degree of control and precision.
This technique is particularly effective for machining hard-to-cut materials and can produce intricate geometries that would be challenging or impossible to achieve with other methods.
Applications of Micro-Machining Technology
Micro-machining technology has found applications across a wide range of industries, thanks to its ability to produce precise and complex components.
Electronics Industry
In the electronics industry, micro-machining is essential for manufacturing components such as microprocessors, integrated circuits, and micro-electromechanical systems (MEMS).
These components require extremely fine features and tight tolerances, which micro-machining can reliably deliver.
The ability to produce smaller, more powerful electronic devices has driven innovation and performance in consumer electronics, telecommunications, and computing.
Medical Devices
The medical field has also greatly benefited from micro-machining technology.
Micro-machining is used to create intricate components for medical devices, such as stents, catheters, and surgical instruments.
These components often need to be small, precise, and biocompatible, making micro-machining an ideal manufacturing solution.
Advancements in this area have led to the development of minimally invasive surgical techniques and improved patient outcomes.
Aerospace Industry
In the aerospace industry, micro-machining is used to produce components for aircraft, satellites, and space exploration equipment.
The demand for lightweight and highly precise parts makes micro-machining an invaluable tool for aerospace engineers.
By enabling the production of complex geometries and reducing the weight of components, micro-machining contributes to the overall efficiency and performance of aerospace systems.
Future Prospects of Micro-Machining Technology
The future of micro-machining technology looks promising, with ongoing research and development poised to push the boundaries of what can be achieved.
Nanotechnology Integration
One exciting prospect is the integration of nanotechnology with micro-machining.
By combining these two fields, manufacturers can create even smaller and more precise components with enhanced functionalities.
Nanotechnology has the potential to revolutionize industries such as electronics, medicine, and materials science, opening up new possibilities for innovation.
Advanced Materials
The development of advanced materials with superior properties, such as high strength, light weight, and biocompatibility, will further enhance the capabilities of micro-machining.
These materials will enable the production of components that can withstand extreme conditions and perform at higher levels than ever before.
Artificial Intelligence and Machine Learning
The integration of artificial intelligence (AI) and machine learning into micro-machining processes holds great promise for improving efficiency and precision.
AI algorithms can optimize machining parameters in real time, reducing the need for manual intervention and minimizing errors.
This will lead to faster production cycles, lower costs, and higher quality components.
Conclusion
The evolution of micro-machining technology has had a profound impact on the manufacturing industry, enabling the production of highly precise and complex components.
From its historical roots to the latest technological advancements, micro-machining continues to drive innovation and efficiency across various sectors.
As we look to the future, the integration of nanotechnology, advanced materials, and artificial intelligence promises to further expand the capabilities of micro-machining.
By staying at the forefront of these developments, manufacturers can continue to push the boundaries of what is possible, creating a brighter, more advanced future for all.
資料ダウンロード
QCD調達購買管理クラウド「newji」は、調達購買部門で必要なQCD管理全てを備えた、現場特化型兼クラウド型の今世紀最高の購買管理システムとなります。
ユーザー登録
調達購買業務の効率化だけでなく、システムを導入することで、コスト削減や製品・資材のステータス可視化のほか、属人化していた購買情報の共有化による内部不正防止や統制にも役立ちます。
NEWJI DX
製造業に特化したデジタルトランスフォーメーション(DX)の実現を目指す請負開発型のコンサルティングサービスです。AI、iPaaS、および先端の技術を駆使して、製造プロセスの効率化、業務効率化、チームワーク強化、コスト削減、品質向上を実現します。このサービスは、製造業の課題を深く理解し、それに対する最適なデジタルソリューションを提供することで、企業が持続的な成長とイノベーションを達成できるようサポートします。
オンライン講座
製造業、主に購買・調達部門にお勤めの方々に向けた情報を配信しております。
新任の方やベテランの方、管理職を対象とした幅広いコンテンツをご用意しております。
お問い合わせ
コストダウンが利益に直結する術だと理解していても、なかなか前に進めることができない状況。そんな時は、newjiのコストダウン自動化機能で大きく利益貢献しよう!
(Β版非公開)