- お役立ち記事
- The Evolution of Micro Machining Technology and Its Impact on Manufacturing: Enhancing Precision and Efficiency
月間76,176名の
製造業ご担当者様が閲覧しています*
*2025年3月31日現在のGoogle Analyticsのデータより
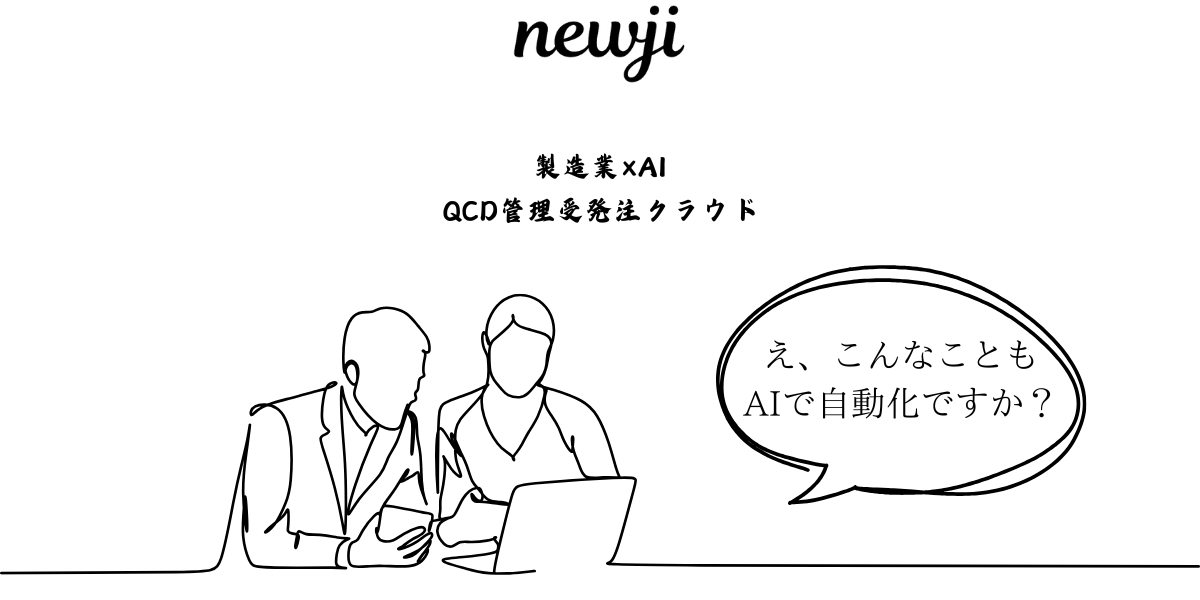
The Evolution of Micro Machining Technology and Its Impact on Manufacturing: Enhancing Precision and Efficiency
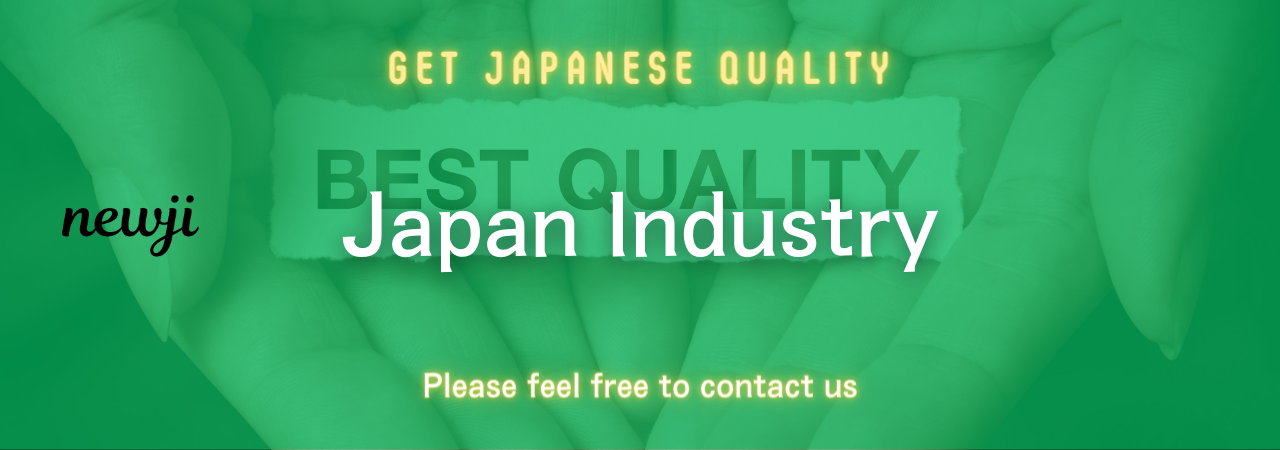
Micro machining technology has undergone significant advancements in recent years, revolutionizing the manufacturing industry.
This evolution has brought about remarkable improvements in precision, efficiency, and the ability to produce highly intricate components.
In this article, we will delve into the history, development, and current state of micro machining technology, as well as its substantial impact on manufacturing practices.
目次
The History of Micro Machining Technology
Micro machining dates back several decades and has roots deeply intertwined with advancements in technology and materials science.
The initial stages of micro machining development were fueled by the need for more precise tools in the electronics and aerospace industries.
Researchers in the 1950s and 1960s began exploring ways to achieve higher precision in their machinery, ultimately leading to the birth of micro machining.
Early methods included processes such as photolithography and mechanical micro machining, which laid the foundation for modern techniques.
The Development of Modern Micro Machining Techniques
The evolution of micro machining technology has been marked by several significant milestones.
The 1980s and 1990s witnessed the rise of computer numerically controlled (CNC) machines, which allowed for highly accurate and automated machining processes.
This era also saw advancements in electro-discharge machining (EDM) and laser machining, enhancing the capability to create intricate designs.
One of the most notable modern techniques is the use of femtosecond lasers, which can create incredibly precise cuts on a microscopic scale.
These lasers, operating at extremely short pulse durations, minimize thermal damage to the material, resulting in cleaner and more precise cuts.
Similarly, advancements in additive manufacturing (3D printing) have enabled the creation of micro-scale components with unprecedented accuracy.
Key Applications of Micro Machining in Manufacturing
Micro machining technology has found applications in a wide range of industries, each benefiting from its precision and efficiency.
Electronics
The electronics industry heavily relies on micro machining for the production of small-scale components such as microchips, printed circuit boards (PCBs), and sensors.
The ability to create intricate patterns with high precision is crucial for the functionality and miniaturization of electronic devices.
Medical Devices
In the medical field, micro machining is essential for the production of implants, surgical instruments, and diagnostic equipment.
The technology enables the creation of devices with intricate geometries that are vital for minimally invasive procedures and high-precision diagnostics.
Aerospace
Aerospace companies utilize micro machining to manufacture lightweight and high-strength components for aircraft and spacecraft.
The precision offered by micro machining enables the production of parts that meet stringent industry standards for both performance and safety.
The Benefits of Advanced Micro Machining Techniques
The advancements in micro machining technology have brought numerous benefits to the manufacturing sector.
Enhanced Precision
One of the primary advantages of modern micro machining techniques is the level of precision they offer.
This high precision is essential for applications where even the smallest error can lead to significant performance issues.
Improved Efficiency
Automation and the use of CNC machines have greatly improved the efficiency of micro machining processes.
Manufacturers can now produce complex components at a faster rate, reducing lead times and increasing overall productivity.
Cost Savings
Despite the high initial investment in advanced micro machining technology, the long-term cost savings are substantial.
The reduced material waste, lower error rates, and faster production times all contribute to cost efficiencies.
Challenges in Micro Machining Technology
Despite its many benefits, micro machining technology also faces certain challenges.
One of the primary obstacles is the need for highly specialized equipment and skilled operators.
The complexity of micro machining processes requires meticulous control and monitoring to ensure high-quality outcomes.
Additionally, the miniaturization of components can lead to challenges in terms of material properties and structural integrity.
Researchers and manufacturers must continuously explore new materials and techniques to overcome these limitations.
Future Trends in Micro Machining Technology
The future of micro machining technology looks promising, with continuous research and development paving the way for new innovations.
One emerging trend is the integration of artificial intelligence (AI) and machine learning into micro machining processes.
AI can optimize machining parameters in real time, enhancing efficiency and precision.
Another promising area is the development of new materials specifically designed for micro machining applications.
These materials can possess unique properties that make them more suitable for creating micro-scale components.
Furthermore, advancements in nano machining are pushing the boundaries even further, enabling the production of components at the atomic level.
This level of precision has the potential to revolutionize fields such as nanotechnology and quantum computing.
In conclusion, the evolution of micro machining technology has had a profound impact on the manufacturing industry.
From its humble beginnings to the advanced techniques of today, micro machining has brought about significant improvements in precision, efficiency, and the ability to create intricate components.
As technology continues to advance, the future of micro machining holds exciting possibilities, promising even greater innovations and applications across various industries.
資料ダウンロード
QCD管理受発注クラウド「newji」は、受発注部門で必要なQCD管理全てを備えた、現場特化型兼クラウド型の今世紀最高の受発注管理システムとなります。
ユーザー登録
受発注業務の効率化だけでなく、システムを導入することで、コスト削減や製品・資材のステータス可視化のほか、属人化していた受発注情報の共有化による内部不正防止や統制にも役立ちます。
NEWJI DX
製造業に特化したデジタルトランスフォーメーション(DX)の実現を目指す請負開発型のコンサルティングサービスです。AI、iPaaS、および先端の技術を駆使して、製造プロセスの効率化、業務効率化、チームワーク強化、コスト削減、品質向上を実現します。このサービスは、製造業の課題を深く理解し、それに対する最適なデジタルソリューションを提供することで、企業が持続的な成長とイノベーションを達成できるようサポートします。
製造業ニュース解説
製造業、主に購買・調達部門にお勤めの方々に向けた情報を配信しております。
新任の方やベテランの方、管理職を対象とした幅広いコンテンツをご用意しております。
お問い合わせ
コストダウンが利益に直結する術だと理解していても、なかなか前に進めることができない状況。そんな時は、newjiのコストダウン自動化機能で大きく利益貢献しよう!
(β版非公開)