- お役立ち記事
- The Evolution of Monitoring Systems and Their Use in Manufacturing
月間76,176名の
製造業ご担当者様が閲覧しています*
*2025年3月31日現在のGoogle Analyticsのデータより
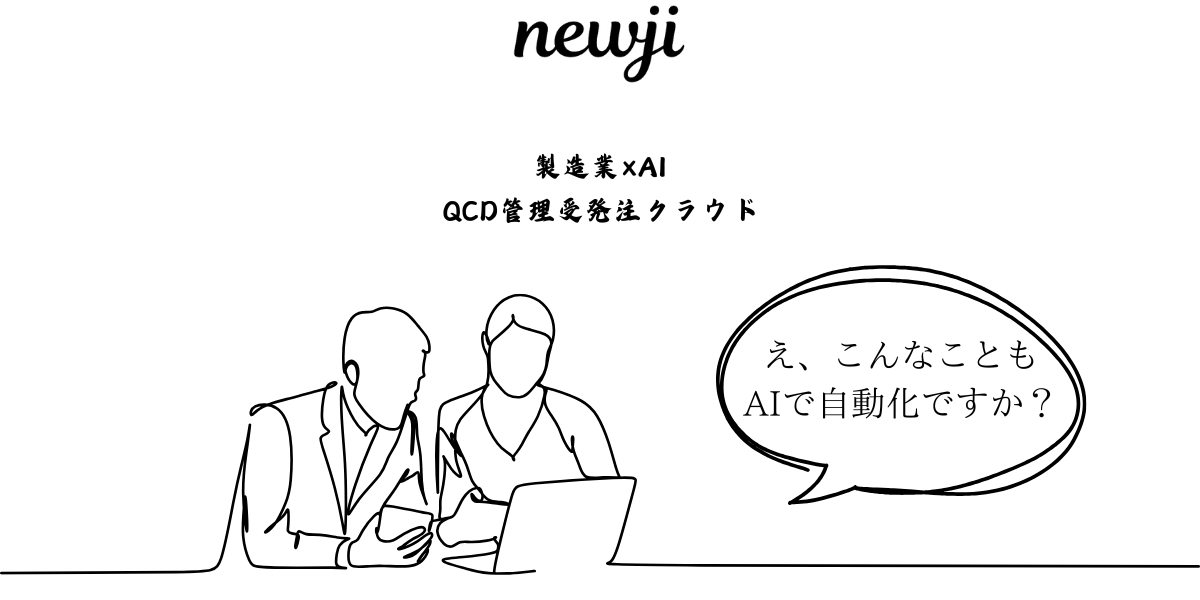
The Evolution of Monitoring Systems and Their Use in Manufacturing
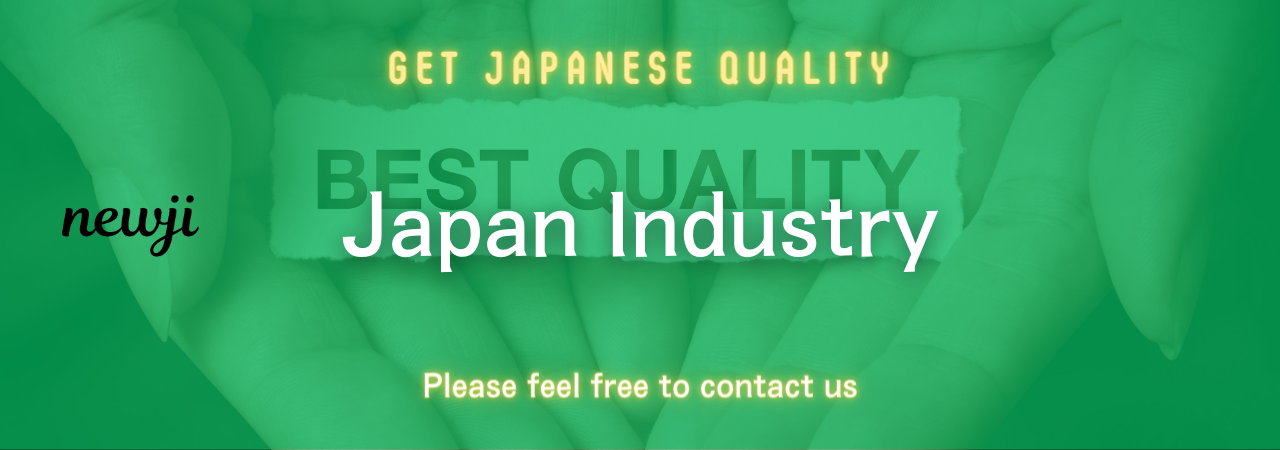
Monitoring systems have significantly evolved over the years, becoming essential tools in the manufacturing industry.
These systems ensure that operations remain efficient, safe, and productive.
Understanding how they have developed and their current uses can give us insight into their importance in modern manufacturing.
目次
The Early Days of Monitoring Systems
In the early days of manufacturing, monitoring systems were manual and rudimentary.
Workers relied on simple tools like gauges and dials to track machine performance.
These methods were time-consuming and often prone to human error.
Despite their limitations, they laid the foundation for more advanced monitoring techniques.
Manual Inspections and Basic Tools
Before the advent of digital technology, factories used basic tools for inspections.
Workers conducted visual checks and used mechanical instruments to measure parameters like pressure and temperature.
These tools provided valuable data but required constant supervision and interpretation by skilled personnel.
The Role of Human Labor
Human labor was integral to early monitoring systems.
Workers had to be vigilant, making rounds to inspect equipment and log data manually.
This dependence on human oversight meant that errors were common, and identifying issues early was challenging.
The Rise of Automated Monitoring
As technology progressed, the manufacturing industry began to adopt automated monitoring systems.
These innovations reduced the need for manual inspections and enhanced the accuracy and reliability of data collection.
The Introduction of Sensors
The introduction of sensors marked a significant turning point.
These devices could monitor various parameters continuously and send real-time data to central systems.
Sensors like thermocouples for temperature measurement and strain gauges for detecting stress in materials became commonplace in factories.
Programmable Logic Controllers (PLCs)
Programmable Logic Controllers (PLCs) revolutionized manufacturing monitoring.
PLCs are computer-based systems designed to manage industrial processes.
They can receive input from sensors, process the data, and control machinery accordingly.
This automation reduced human error and increased efficiency across manufacturing processes.
Modern Monitoring Systems
Today, monitoring systems have reached new heights with advancements in technology, offering unprecedented capabilities.
Internet of Things (IoT) Integration
The Internet of Things (IoT) has transformed monitoring systems in manufacturing.
IoT-enabled devices can connect and communicate over the internet, providing a seamless flow of data.
This connectivity allows for real-time monitoring and remote management of manufacturing operations.
IoT sensors can track a wide range of parameters, from machine performance to environmental conditions, enhancing productivity and safety.
Big Data and Analytics
The use of big data and analytics plays a crucial role in modern monitoring systems.
By collecting vast amounts of data from various sources, manufacturers can gain valuable insights into their operations.
Advanced analytics tools can identify patterns, predict failures, and optimize processes.
This data-driven approach allows for proactive maintenance, reducing downtime and increasing efficiency.
Artificial Intelligence (AI) and Machine Learning
Artificial Intelligence (AI) and machine learning have further enhanced monitoring systems.
AI algorithms can analyze data in real time, making decisions and adjustments to optimize operations.
Machine learning models can learn from historical data, improving accuracy and adapting to changing conditions.
These technologies enable predictive maintenance, where potential issues are identified and addressed before they cause disruptions.
The Benefits of Modern Monitoring Systems
The evolution of monitoring systems has brought numerous benefits to the manufacturing industry, driving improvements in efficiency, safety, and profitability.
Increased Efficiency
Modern monitoring systems enable manufacturers to optimize their processes and reduce waste.
Real-time data allows for immediate adjustments to ensure machinery operates at peak performance.
Automated systems reduce the need for manual interventions, allowing workers to focus on more value-added tasks.
Enhanced Safety
Safety is a critical concern in manufacturing.
Modern monitoring systems can detect unsafe conditions and alert operators to take corrective actions.
For example, sensors can identify overheating or unusual vibrations in machinery, preventing potential accidents.
These systems ensure a safer working environment for employees.
Cost Savings
By optimizing operations and preventing equipment failures, modern monitoring systems can significantly reduce costs.
Predictive maintenance minimizes downtime and extends the lifespan of machinery.
Energy-efficient practices, driven by data insights, lower utility bills and environmental impact.
The Future of Monitoring Systems in Manufacturing
The future holds exciting possibilities for monitoring systems, driven by ongoing technological advancements.
Edge Computing
Edge computing is set to play a significant role in the future of monitoring systems.
This technology processes data locally, closer to the source, rather than relying on centralized servers.
Edge computing reduces latency and allows for faster decision-making, essential for real-time monitoring and control.
Integration with Digital Twins
Digital twins are virtual replicas of physical assets or systems.
By integrating monitoring systems with digital twins, manufacturers can simulate and analyze various scenarios.
This approach provides a deeper understanding of operations and facilitates better decision-making.
Enhanced AI Capabilities
As AI continues to evolve, its capabilities in monitoring systems will expand.
Advanced AI algorithms will improve predictive maintenance accuracy and enable autonomous decision-making.
These developments will further reduce human intervention and enhance overall efficiency.
Monitoring systems have come a long way from their humble beginnings to their current state of advanced technology.
Their evolution has transformed the manufacturing industry, bringing significant benefits in efficiency, safety, and cost savings.
As technology continues to advance, future monitoring systems promise even greater innovations, driving the industry towards new heights of productivity and success.
Understanding this evolution helps us appreciate the vital role these systems play in modern manufacturing and their potential for future impact.
資料ダウンロード
QCD管理受発注クラウド「newji」は、受発注部門で必要なQCD管理全てを備えた、現場特化型兼クラウド型の今世紀最高の受発注管理システムとなります。
ユーザー登録
受発注業務の効率化だけでなく、システムを導入することで、コスト削減や製品・資材のステータス可視化のほか、属人化していた受発注情報の共有化による内部不正防止や統制にも役立ちます。
NEWJI DX
製造業に特化したデジタルトランスフォーメーション(DX)の実現を目指す請負開発型のコンサルティングサービスです。AI、iPaaS、および先端の技術を駆使して、製造プロセスの効率化、業務効率化、チームワーク強化、コスト削減、品質向上を実現します。このサービスは、製造業の課題を深く理解し、それに対する最適なデジタルソリューションを提供することで、企業が持続的な成長とイノベーションを達成できるようサポートします。
製造業ニュース解説
製造業、主に購買・調達部門にお勤めの方々に向けた情報を配信しております。
新任の方やベテランの方、管理職を対象とした幅広いコンテンツをご用意しております。
お問い合わせ
コストダウンが利益に直結する術だと理解していても、なかなか前に進めることができない状況。そんな時は、newjiのコストダウン自動化機能で大きく利益貢献しよう!
(β版非公開)