- お役立ち記事
- The foundation and implementation of integrated BOMs and applications to smart factory
月間76,176名の
製造業ご担当者様が閲覧しています*
*2025年3月31日現在のGoogle Analyticsのデータより
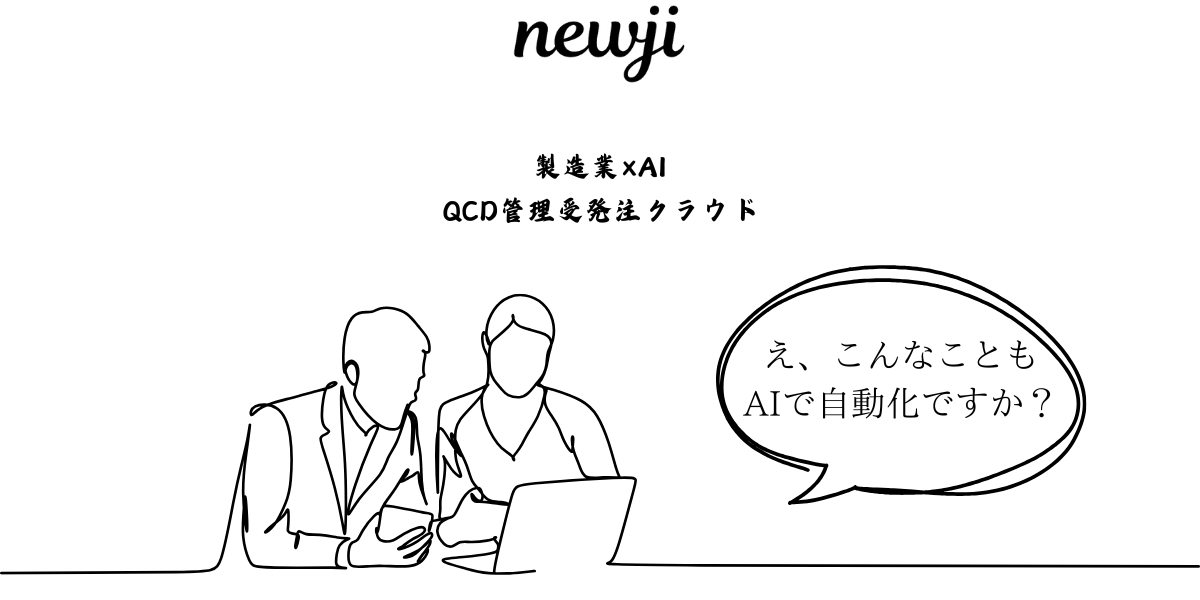
The foundation and implementation of integrated BOMs and applications to smart factory
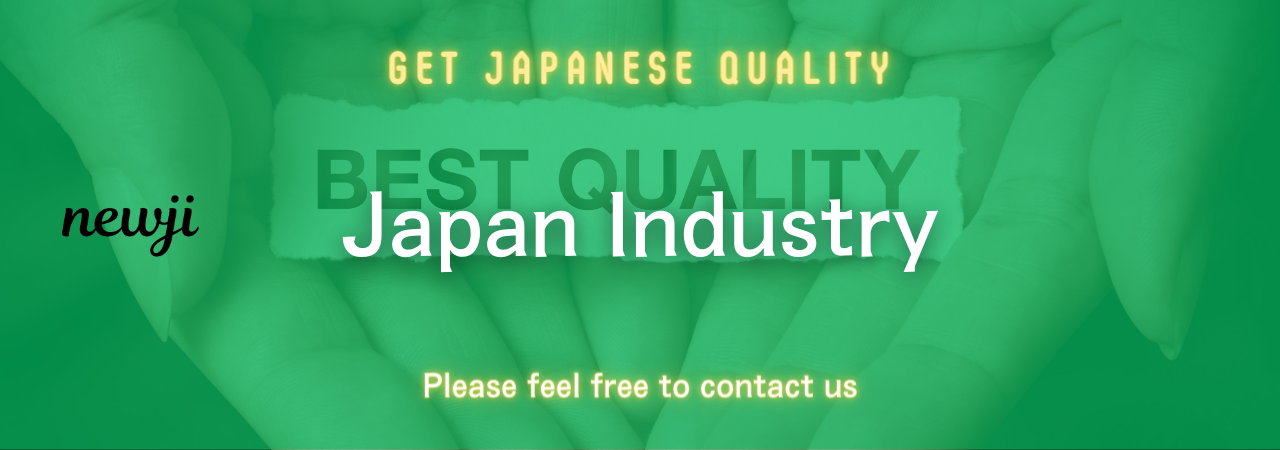
目次
Understanding the Basics: What is a BOM?
Before diving into the complexities of Integrated Bill of Materials (BOMs) and their applications in smart factories, it’s important to understand what a BOM is.
A Bill of Materials is a comprehensive list of raw materials, components, and instructions required to manufacture, construct, or repair a product or service.
Basically, it serves as a recipe for manufacturing, detailing everything needed to complete the end product, from nuts and bolts to instructions on assembly.
Although that sounds simple enough, managing a BOM effectively involves complex coordination between various departments within an organization, namely engineering, manufacturing, purchasing, and customer service.
The Evolution of Integrated BOMs
As traditional manufacturing has evolved, so too have the methods for managing BOMs.
Integrated BOMs have emerged to address the limitations of traditional BOMs.
Unlike separate systems for different departments, integrated BOMs consolidate information across various departments into a single, cohesive platform.
They offer better collaboration, consistency, and visibility.
With integrated BOMs, data discrepancies are minimized, leading to fewer errors and more streamlined operations.
These systems can dynamically adjust to changes in design, supply availability, and production requirements, making them ideal for the agile manufacturing methods seen in smart factories.
Implementing Integrated BOMs in Smart Factories
Smart factories represent the future of manufacturing.
They leverage smart technology such as IoT, AI, and robotics to make factories more efficient and responsive.
In such environments, integrated BOMs are crucial.
Here’s how they can be implemented:
Digital Transformation and Integration
Digital transformation is a prerequisite for the integration of BOMs in smart factories.
This involves shifting from paper-based systems to digital platforms.
By digitizing this information, it becomes more accessible and easier to update in real-time.
Additionally, integrating this digital information into existing IT infrastructure allows seamless communication between different departments.
Utilizing IoT for Data Collection
Internet of Things (IoT) devices play a pivotal role in smart factories by collecting data from machinery and the environment.
This data can include machine status, environmental conditions, material usage, and more.
Integrating IoT insights with BOMs ensures that the manufacturing process always has the most current and relevant information.
This data-driven approach helps prevent material shortages and optimize production schedules.
AI and Predictive Analytics
AI can analyze the vast amounts of data collected in real-time from various facets of the production process.
By using predictive analytics, it can forecast potential issues, allowing proactive measures to be taken.
This predictive ability is integrated into the BOM, ensuring that downstream processes are not disrupted.
A simple example is predictive maintenance.
AI can predict when a machine will likely fail and adjust the BOM accordingly, scheduling maintenance at the least disruptive time.
Collaborative Platforms
Integrated BOMs thrive in collaborative environments where different departments and suppliers can effortlessly interact.
Cloud-based platforms provide a centralized space where all stakeholders can access, modify, and update BO information as needed.
This ensures that everyone is on the same page, thereby improving coordination and reducing bottlenecks in the manufacturing process.
Benefits of Integrated BOMs in Smart Manufacturing
The integration of BOMs into smart manufacturing facilities provides numerous benefits that enhance productivity and profitability.
Increased Efficiency and Productivity
By minimizing data discrepancies and ensuring all operations are working from the same set of information, integrated BOMs enable faster decision-making and greater efficiency in production.
Streamlined processes result in faster time-to-market for products and increased output levels.
Improved Quality Control
With complete visibility into every component and stage of the production process, quality control is significantly enhanced.
Integrated BOMs ensure that defects are quickly identified and rectified, preserving the integrity of the final product.
Cost Reduction
Automation and data-driven decision-making help to reduce waste, lower operational costs, and optimize resource usage.
By predicting resource requirements and preventing overproduction, smart factories save both time and materials, improving their bottom line.
Enhanced Agility and Innovation
Smart factories must be agile to adapt to changing market demands.
Integrated BOMs allow quick adjustments to manufacturing schedules, material sourcing, and other critical factors.
This dynamic nature fosters an innovative environment, encouraging constant improvement and adaptation.
Challenges in Implementing Integrated BOMs
While undeniably beneficial, implementing integrated BOMs does come with its own set of challenges:
Technical Complexity
Integrating multiple systems into a cohesive whole involves varying technical challenges, requiring expertise in IT infrastructure, software engineering, and data management.
High Initial Investment
The initial outlay for digital transformation and equipment outfitted with IoT capabilities can be significant.
However, the cost savings through improved efficiency and reduced waste can offer a substantial return on investment in the long run.
Cultural Resistance
Transition to a smart, integrated system requires a cultural shift in thinking and approach throughout an organization.
It’s important for management to educate employees on the benefits and efficiencies garnered from integrated BOMs, in order to obtain the necessary buy-in.
Conclusion
The foundation and implementation of integrated BOMs in smart factories signify a pivotal advancement in the manufacturing industry.
Although such transformations do involve certain challenges, the resulting efficiencies, cost savings, and innovative capabilities undeniably enhance a company’s competitive edge in the global market.
These state-of-the-art systems are quickly becoming a cornerstone of smart manufacturing, paving the way for a future where factories operate with unprecedented levels of precision, sustainability, and agility.
資料ダウンロード
QCD管理受発注クラウド「newji」は、受発注部門で必要なQCD管理全てを備えた、現場特化型兼クラウド型の今世紀最高の受発注管理システムとなります。
ユーザー登録
受発注業務の効率化だけでなく、システムを導入することで、コスト削減や製品・資材のステータス可視化のほか、属人化していた受発注情報の共有化による内部不正防止や統制にも役立ちます。
NEWJI DX
製造業に特化したデジタルトランスフォーメーション(DX)の実現を目指す請負開発型のコンサルティングサービスです。AI、iPaaS、および先端の技術を駆使して、製造プロセスの効率化、業務効率化、チームワーク強化、コスト削減、品質向上を実現します。このサービスは、製造業の課題を深く理解し、それに対する最適なデジタルソリューションを提供することで、企業が持続的な成長とイノベーションを達成できるようサポートします。
製造業ニュース解説
製造業、主に購買・調達部門にお勤めの方々に向けた情報を配信しております。
新任の方やベテランの方、管理職を対象とした幅広いコンテンツをご用意しております。
お問い合わせ
コストダウンが利益に直結する術だと理解していても、なかなか前に進めることができない状況。そんな時は、newjiのコストダウン自動化機能で大きく利益貢献しよう!
(β版非公開)