- お役立ち記事
- The front line of purchasing to prevent the risk of parts shortages at manufacturing sites
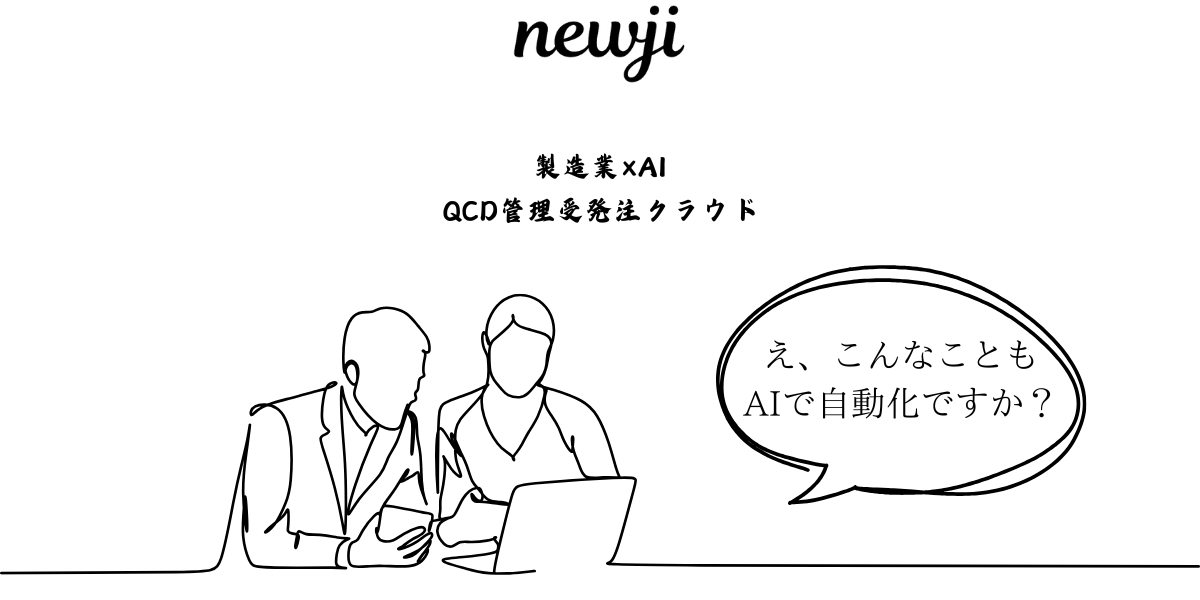
The front line of purchasing to prevent the risk of parts shortages at manufacturing sites
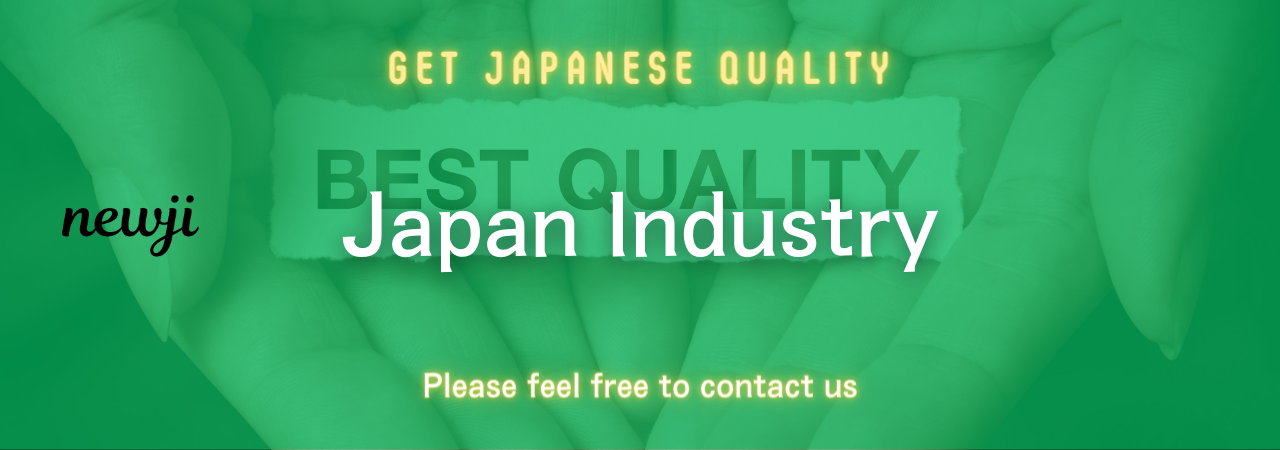
目次
Understanding the Parts Shortage Crisis
In today’s fast-paced manufacturing world, the availability of parts and components is crucial to maintaining smooth operations.
Yet, disruptions in supply chains have become more frequent, highlighting the need for effective purchasing strategies to mitigate risks related to parts shortages.
This involves foreseeing potential delays, understanding market dynamics, and developing contingency plans to ensure that manufacturing sites operate without interruption.
The Causes of Parts Shortages
Several factors contribute to the risk of parts shortages.
Global events such as natural disasters, political unrest, and pandemics can severely disrupt supply chains.
Similarly, constraints in logistics, such as shipping delays or port congestion, can impede the timely delivery of critical components.
Additionally, increased demand for certain products may outpace the supply capabilities of manufacturers.
For instance, the surge in electronics demand during the COVID-19 pandemic led to significant semiconductor shortages.
Understanding these causes is the first step towards developing a proactive purchasing strategy.
Effective Purchasing Strategies
Supplier Diversification
Relying on a single supplier for critical parts can be risky.
Diversifying suppliers reduces the dependency on any one vendor and provides alternate sources if one is unable to meet demand.
Purchasing managers should establish relationships with multiple suppliers across different geographical locations to enhance supply chain resilience.
Inventory Management
Maintaining an optimal level of inventory is another critical strategy.
This involves assessing the balance between having enough stock to manage potential delays and avoiding excessive overstock that could tie up valuable resources.
Implementing Just-In-Time (JIT) inventory systems can help manage this balance, ensuring components are available when needed without excessive storage costs.
Developing Strategic Partnerships
Establishing strategic partnerships with suppliers can result in benefits such as priority access to limited stock and collaborative problem-solving during disruptions.
By building strong relationships with key suppliers, purchasing managers can negotiate better terms, secure preferential treatment, and foster a shared interest in mutual success.
Leveraging Technology
Data Analytics
Utilizing data analytics tools enables manufacturers to gain insights into demand patterns and predict potential shortages.
Analyzing historical data can help identify trends and inform purchasing decisions.
This proactive approach allows purchasing teams to anticipate requirements and place orders ahead of time, avoiding last-minute scrambles for parts.
Supply Chain Visibility
Implementing technology solutions like supply chain management software provides real-time visibility into the status of parts throughout the supply chain.
This transparency facilitates quick decision-making and allows companies to react swiftly to delays or disruptions before they impact production.
Building a Resilient Supply Chain
Scenario Planning
Scenario planning involves anticipating various potential disruptions and devising strategies to address them.
By regularly conducting these exercises, companies can develop flexible responses and ensure preparedness for unexpected events.
Having pre-defined action plans allows for quick implementation during crises, minimizing their impact on manufacturing timelines.
Risk Assessment and Mitigation
Conducting thorough risk assessments can highlight vulnerabilities within the supply chain.
Once identified, companies can take steps to mitigate these risks, whether through alternative sourcing strategies, insurance, or contractual clauses with suppliers.
Regular assessments ensure that potential threats are addressed in a timely manner.
Collaboration and Communication
Internal Coordination
Effective communication between purchasing departments, manufacturing teams, and other stakeholders is essential for addressing parts shortages.
Coordinating efforts ensures everyone is aligned on priorities and can work collaboratively towards solutions.
Supplier Communication
Open and ongoing communication with suppliers is vital in managing expectations and developing effective partnerships.
Regular updates on production schedules and demand forecasts can help suppliers plan their operations more efficiently, reducing the likelihood of shortages.
Stay Informed
Purchasing managers must stay informed about global events and industry news that may impact the availability of parts.
Being aware of potential disruptions allows for timely adjustments to purchasing plans and helps maintain supply chain stability.
By implementing these strategies, companies can minimize the risk of parts shortages and ensure their manufacturing operations run smoothly even in the face of unforeseen challenges.
資料ダウンロード
QCD調達購買管理クラウド「newji」は、調達購買部門で必要なQCD管理全てを備えた、現場特化型兼クラウド型の今世紀最高の購買管理システムとなります。
ユーザー登録
調達購買業務の効率化だけでなく、システムを導入することで、コスト削減や製品・資材のステータス可視化のほか、属人化していた購買情報の共有化による内部不正防止や統制にも役立ちます。
NEWJI DX
製造業に特化したデジタルトランスフォーメーション(DX)の実現を目指す請負開発型のコンサルティングサービスです。AI、iPaaS、および先端の技術を駆使して、製造プロセスの効率化、業務効率化、チームワーク強化、コスト削減、品質向上を実現します。このサービスは、製造業の課題を深く理解し、それに対する最適なデジタルソリューションを提供することで、企業が持続的な成長とイノベーションを達成できるようサポートします。
オンライン講座
製造業、主に購買・調達部門にお勤めの方々に向けた情報を配信しております。
新任の方やベテランの方、管理職を対象とした幅広いコンテンツをご用意しております。
お問い合わせ
コストダウンが利益に直結する術だと理解していても、なかなか前に進めることができない状況。そんな時は、newjiのコストダウン自動化機能で大きく利益貢献しよう!
(Β版非公開)