- お役立ち記事
- The impact of purchasing management optimization on the entire SME value chain
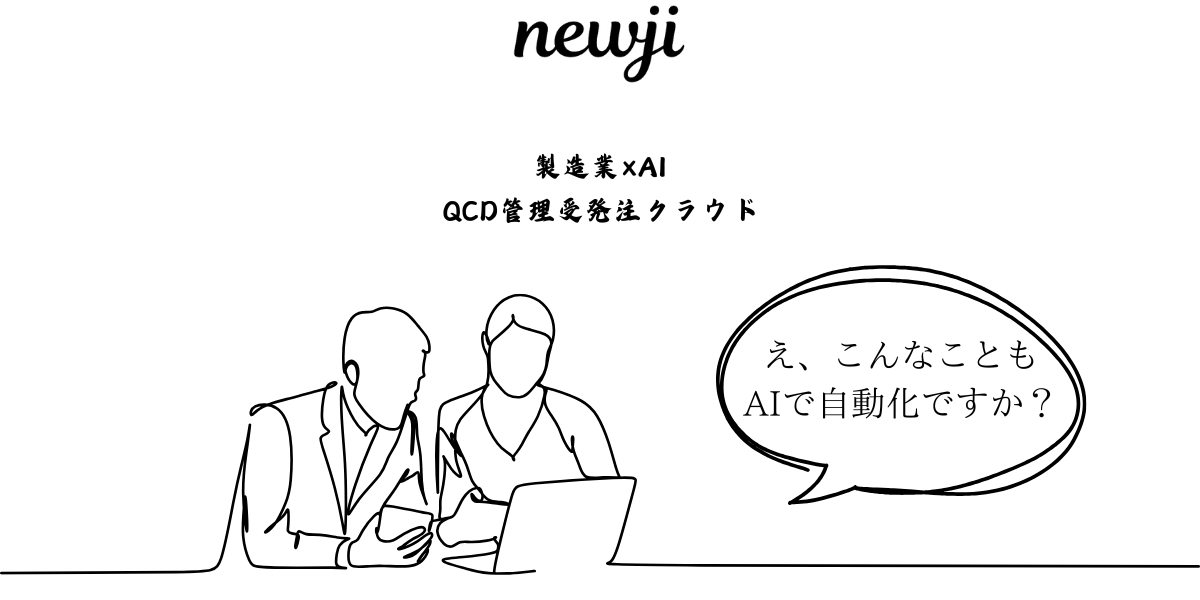
The impact of purchasing management optimization on the entire SME value chain
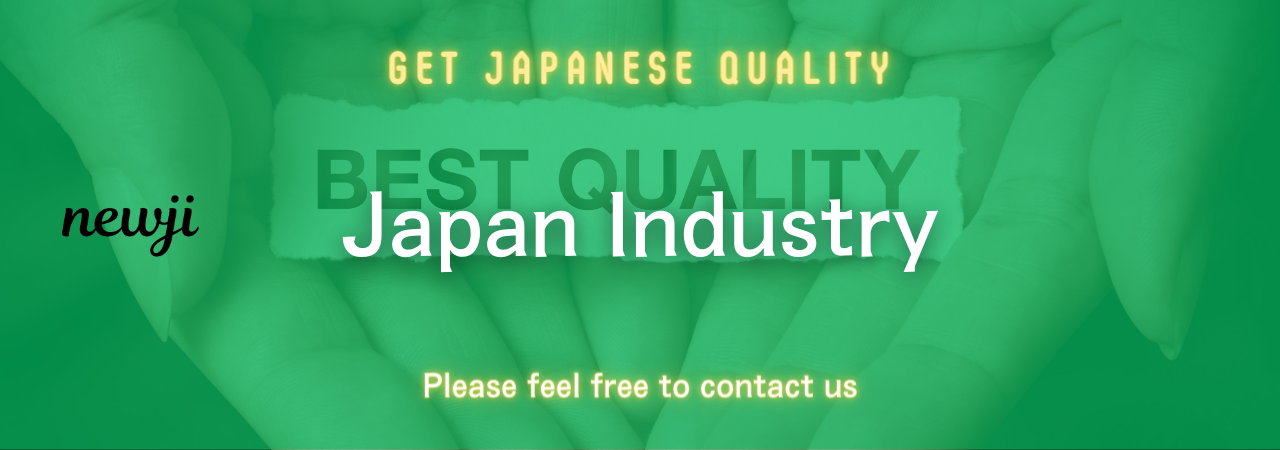
Purchasing management is crucial for small and medium-sized enterprises (SMEs).
When optimized, it touches every part of the value chain.
This improvement can transform the way an SME operates, creating a ripple effect that leads to overall business growth.
目次
Understanding Purchasing Management
Purchasing management involves the process of sourcing, acquiring, and managing the goods and services an organization needs.
For SMEs, this involves negotiating with suppliers, managing inventory, and ensuring the timely delivery of materials.
Effective purchasing management helps in reducing costs and improving product quality.
The Function of Procurement
Procurement is the heart of purchasing management.
It involves identifying what the company needs and finding the best suppliers to meet those needs.
A well-organized procurement process ensures that materials are of high quality and are acquired at competitive prices.
For SMEs, this means getting value for every dollar spent.
The Benefits of Optimization
Cost Efficiency
One of the primary benefits of optimizing purchasing management is cost efficiency.
SMEs often operate under tight budgets.
By negotiating better deals with suppliers and managing inventory effectively, significant savings can be achieved.
This allows the company to allocate resources to other essential areas, such as marketing and development.
Improved Supplier Relationships
Optimized purchasing management leads to better relationships with suppliers.
When SMEs maintain clear, consistent communication with their suppliers, they build trust.
This relationship can result in better terms, faster delivery times, and priority service during high-demand periods.
Enhanced Product Quality
When the procurement process is well managed, it ensures that only high-quality materials are used.
This directly impacts the final product’s quality.
Customers are more likely to be satisfied with products that meet their expectations, leading to repeat business and customer loyalty.
Inventory Management
Effective purchasing management also involves good inventory management.
Overstocking ties up capital that could be used elsewhere, while understocking can stall production.
Optimizing this balance ensures that there are enough materials to meet demand without overspending.
Effects on the Entire SME Value Chain
Production Efficiency
When purchasing management is optimized, the production process becomes more efficient.
Having the right materials at the right time allows production to run smoothly without delays.
This efficiency reduces downtime and increases productivity.
Quality Control
Quality control starts with the materials used in production.
By ensuring that high-quality materials are always available, the number of defects decreases.
This means fewer returns and higher customer satisfaction.
Operational Flexibility
SMEs often need to adapt quickly to market changes.
Optimized purchasing management provides the flexibility to respond to these changes promptly.
For example, being able to quickly source new materials allows an SME to pivot to new products or market demands efficiently.
Support for Sales and Marketing
Sales and marketing efforts are more effective when supported by a well-managed purchasing department.
With a consistent supply of quality products, marketing teams can confidently promote offerings.
Sales teams, in turn, have fewer concerns about stock levels, enabling them to focus on closing deals.
Implementing Optimization Strategies
Analyzing Current Processes
The first step in optimizing purchasing management is to analyze the current processes.
This involves looking into how materials are sourced, negotiating with suppliers, and how inventory is managed.
Identifying bottlenecks and inefficiencies provides a clear picture of where improvements are needed.
Training and Development
Investing in the training and development of purchasing staff is crucial.
Employees should be equipped with the skills to negotiate effectively, manage inventory, and understand market trends.
Training ensures that everyone involved in the purchasing process can contribute to its optimization.
Leveraging Technology
Technology can significantly enhance purchasing management.
Procurement software helps in tracking orders, managing supplier relationships, and predicting inventory needs.
Using technology allows for data-driven decisions, reducing the chances of errors and improving efficiency.
Building Strong Supplier Relationships
Maintaining strong relationships with suppliers is beneficial.
Regular communication helps in understanding supplier capacities and challenges.
This relationship builds trust and ensures that the SME can rely on its suppliers even during challenging times.
Challenges to Be Aware Of
Resistance to Change
One of the common challenges in optimizing purchasing management is resistance to change.
Employees may be accustomed to the existing processes and hesitant to adopt new methods.
Addressing these concerns through training and clear communication can ease the transition.
Cost of Implementation
While the benefits are significant, the cost of implementing new technologies and training programs can be a hurdle.
However, viewing these costs as investments in the future profitability and efficiency of the company can help in justifying them.
Supply Chain Disruptions
External factors such as natural disasters or political instability can disrupt the supply chain.
Having contingency plans in place and diversifying the supplier base can mitigate these risks.
Conclusion
Optimizing purchasing management in an SME has a profound impact on the entire value chain.
From cost efficiency and improved relationships to enhanced product quality and operational flexibility, the benefits are substantial.
By implementing strategic changes and leveraging technology, SMEs can ensure their purchasing processes contribute positively to overall business success.
While challenges exist, they can be navigated through thoughtful planning and investment.
Ultimately, optimized purchasing management paves the way for sustainable growth and competitive advantage.
資料ダウンロード
QCD調達購買管理クラウド「newji」は、調達購買部門で必要なQCD管理全てを備えた、現場特化型兼クラウド型の今世紀最高の購買管理システムとなります。
ユーザー登録
調達購買業務の効率化だけでなく、システムを導入することで、コスト削減や製品・資材のステータス可視化のほか、属人化していた購買情報の共有化による内部不正防止や統制にも役立ちます。
NEWJI DX
製造業に特化したデジタルトランスフォーメーション(DX)の実現を目指す請負開発型のコンサルティングサービスです。AI、iPaaS、および先端の技術を駆使して、製造プロセスの効率化、業務効率化、チームワーク強化、コスト削減、品質向上を実現します。このサービスは、製造業の課題を深く理解し、それに対する最適なデジタルソリューションを提供することで、企業が持続的な成長とイノベーションを達成できるようサポートします。
オンライン講座
製造業、主に購買・調達部門にお勤めの方々に向けた情報を配信しております。
新任の方やベテランの方、管理職を対象とした幅広いコンテンツをご用意しております。
お問い合わせ
コストダウンが利益に直結する術だと理解していても、なかなか前に進めることができない状況。そんな時は、newjiのコストダウン自動化機能で大きく利益貢献しよう!
(Β版非公開)