- お役立ち記事
- The Importance of Clock Signals and Their Use in Manufacturing
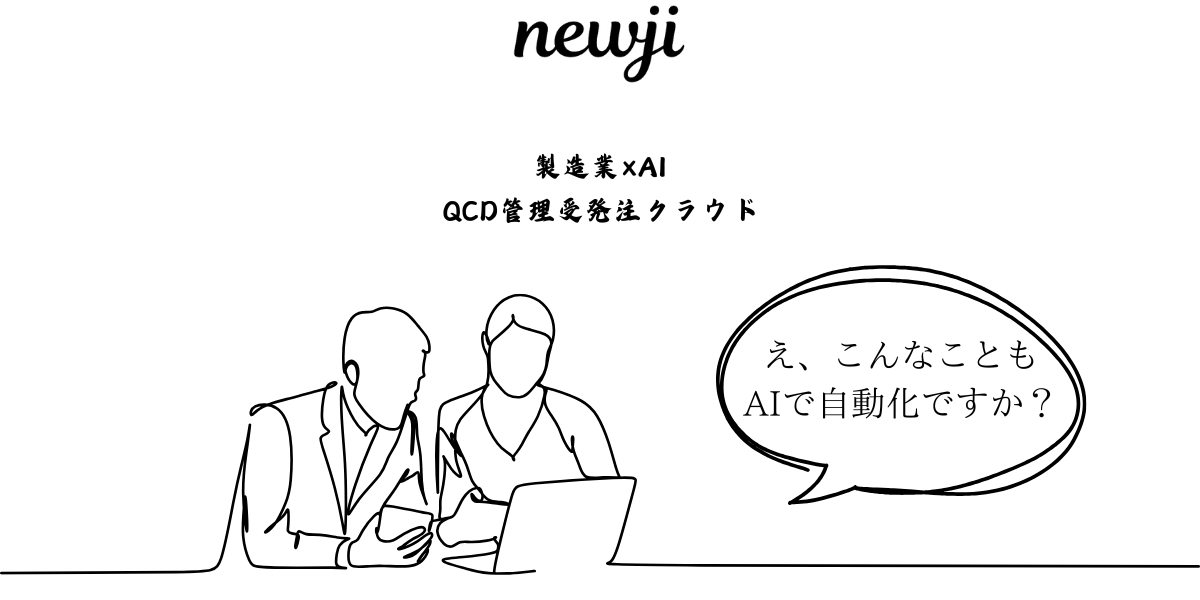
The Importance of Clock Signals and Their Use in Manufacturing
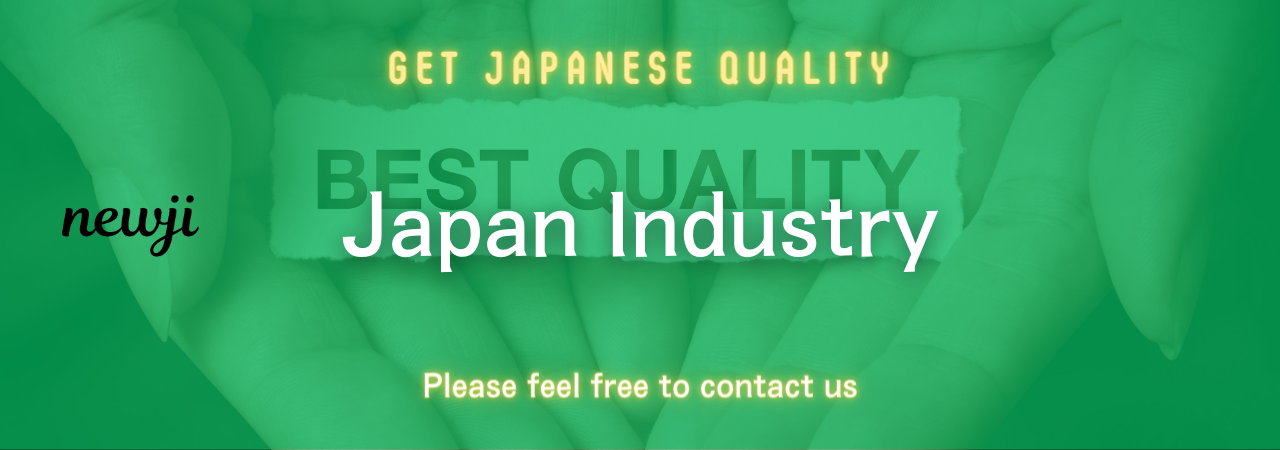
In today’s fast-paced world, where technology penetrates every aspect of our lives, clock signals quietly play a pivotal role in the functioning of various devices.
These signals serve as the heartbeat of digital systems, ensuring everything operates in sync.
Clock signals are especially crucial in the manufacturing industry, where precision and timing can make or break the effectiveness of production processes.
目次
What Are Clock Signals?
Clock signals are synchronized pulses emitted at regular intervals.
They are used to coordinate the actions of electronic components within a system.
In simpler terms, think of it as a metronome for musicians.
Just as a metronome ensures musicians play in unison, clock signals ensure that manufactured products come together perfectly, step-by-step.
These clock signals are generated by a clock generator, which produces a consistent time reference for the entire system.
The frequency of these signals is measured in Hertz (Hz), which indicates cycles per second.
For example, a clock signal at 1 MHz completes one million cycles every second.
The Role of Clock Signals in Manufacturing
Within the manufacturing industry, clock signals are indispensable, particularly in automated production lines.
Here are some key roles they play:
Coordination of Processes
In manufacturing, multiple processes need to happen simultaneously.
From aligning parts to ensuring machinery moves in a synchronized manner, clock signals keep everything in harmony.
They provide a common time reference, allowing different parts of the system to communicate and operate efficiently.
Precision and Accuracy
Manufacturing precision is paramount, as even a minor deviation can lead to product defects.
Clock signals ensure that each operation occurs at the exact moment required.
For instance, in semiconductor manufacturing, precise timing determines the placement of silicon layers, ensuring high-performance microchips.
Increased Productivity
By synchronizing machinery and processes, clock signals help in minimizing downtimes.
This synchronization translates to faster production rates and maximizes the uptime of assembly lines.
Therefore, the overall productivity of a manufacturing plant can significantly increase.
Types of Clock Signals Used in Manufacturing
Crystal Oscillators
Crystal oscillators use the mechanical resonance of vibrating crystals made of quartz.
These oscillators are known for their stability and precision, making them suitable for high-accuracy applications.
In manufacturing, they are used in timing circuits and control systems.
Phase-Locked Loops (PLLs)
PLLs are feedback systems that synchronize an output signal with a reference input signal.
They are essential for maintaining the stability of high-frequency clock signals.
PLLs are widely used in telecommunication equipment and precision instruments found in manufacturing settings.
Programmable Clock Generators
These are versatile devices that allow customization of clock frequencies based on the specific needs of manufacturing processes.
Programmable clock generators can be easily integrated into various systems, providing flexibility and reducing the need for multiple clock sources.
Challenges in Managing Clock Signals
Despite their importance, managing clock signals comes with its own set of challenges:
Signal Integrity
Maintaining the integrity of clock signals over long distances or across different components is a major challenge.
Signal degradation can lead to timing mismatches and operational errors, affecting the quality of the manufactured product.
Power Consumption
High-frequency clock signals consume significant power.
In manufacturing, where energy efficiency is a concern, balancing the need for precise timing with power consumption is crucial.
Electromagnetic Interference (EMI)
Clock signals can sometimes cause electromagnetic interference, disrupting nearby electronic components.
This interference can lead to inaccuracies and impact the performance of manufacturing machinery.
Innovations in Clock Signal Management
Advanced Signal Processing
Sophisticated algorithms and advanced signal processing techniques are being deployed to manage clock signals more efficiently.
These innovative methods help in minimizing signal degradation and coping with electromagnetic interference issues, ensuring smoother manufacturing processes.
Low-Power Clock Solutions
To address power consumption concerns, low-power clock solutions are being developed.
These solutions use less energy while maintaining high precision, making them ideal for energy-sensitive manufacturing operations.
Integration with IoT
The Internet of Things (IoT) enables intelligent monitoring of clock signals in manufacturing environments.
Real-time data collection and analytics provide insights into signal performance, allowing for proactive adjustments and continuous improvements in production lines.
The Future of Clock Signals in Manufacturing
As manufacturing becomes increasingly digitized and automated, the importance of clock signals will continue to grow.
Companies are investing in research and development to produce more reliable and efficient clock generators.
Future advancements may include quantum-based clock sources, providing unparalleled precision and stability.
Furthermore, with the rise of smart factories and Industry 4.0, integrating clock signals with artificial intelligence and machine learning algorithms could revolutionize manufacturing.
Predictive maintenance, real-time process optimization, and enhanced communication between machines are just a few possibilities on the horizon.
Clock signals, though often operating in the background, are indispensable for modern manufacturing.
Their ability to coordinate processes, ensure precision, and boost productivity underscores their significance.
By understanding and managing these signals effectively, manufacturers can enhance their operations and pave the way for future innovations.
資料ダウンロード
QCD調達購買管理クラウド「newji」は、調達購買部門で必要なQCD管理全てを備えた、現場特化型兼クラウド型の今世紀最高の購買管理システムとなります。
ユーザー登録
調達購買業務の効率化だけでなく、システムを導入することで、コスト削減や製品・資材のステータス可視化のほか、属人化していた購買情報の共有化による内部不正防止や統制にも役立ちます。
NEWJI DX
製造業に特化したデジタルトランスフォーメーション(DX)の実現を目指す請負開発型のコンサルティングサービスです。AI、iPaaS、および先端の技術を駆使して、製造プロセスの効率化、業務効率化、チームワーク強化、コスト削減、品質向上を実現します。このサービスは、製造業の課題を深く理解し、それに対する最適なデジタルソリューションを提供することで、企業が持続的な成長とイノベーションを達成できるようサポートします。
オンライン講座
製造業、主に購買・調達部門にお勤めの方々に向けた情報を配信しております。
新任の方やベテランの方、管理職を対象とした幅広いコンテンツをご用意しております。
お問い合わせ
コストダウンが利益に直結する術だと理解していても、なかなか前に進めることができない状況。そんな時は、newjiのコストダウン自動化機能で大きく利益貢献しよう!
(Β版非公開)