- お役立ち記事
- The importance of cost control in the supply chain and the role of the purchasing department
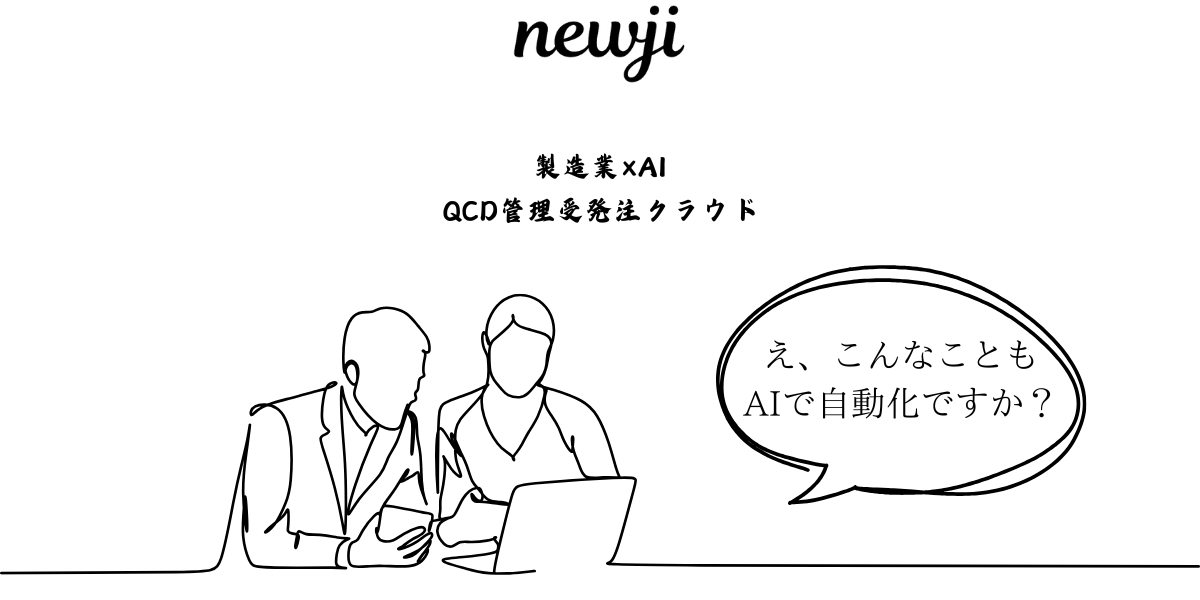
The importance of cost control in the supply chain and the role of the purchasing department
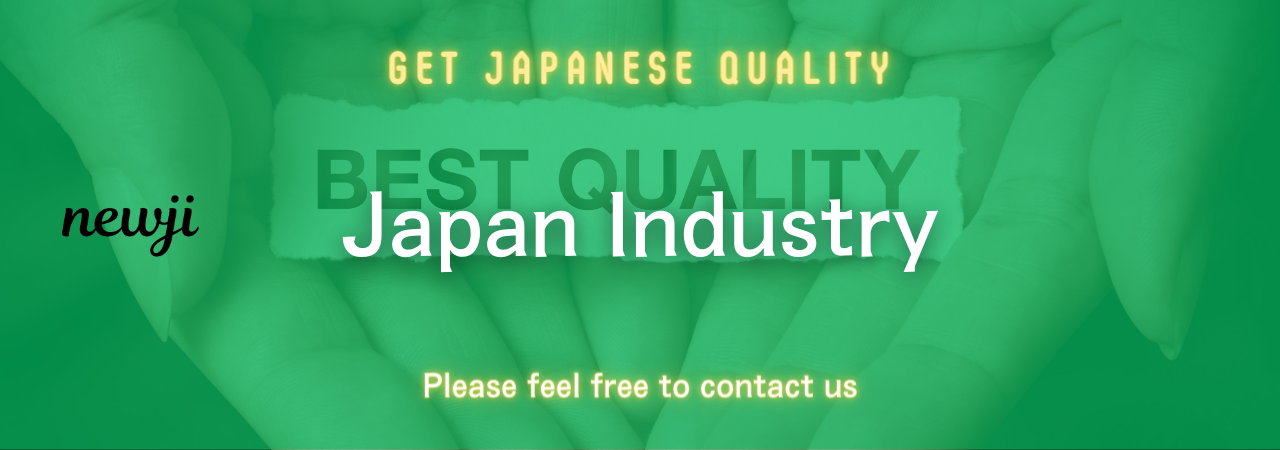
目次
Understanding Supply Chain Cost Control
The concept of cost control in the supply chain is more important than ever in today’s competitive business environment.
Supply chains are complex networks consisting of multiple stakeholders, processes, and products.
Effectively managing costs within this intricate ecosystem can significantly impact a company’s bottom line.
Cost control refers to strategic efforts to manage expenditures and reduce unnecessary expenses without compromising the quality or efficiency of operations.
In the context of supply chains, it involves monitoring, analyzing, and optimizing costs related to procurement, production, transportation, warehousing, and distribution.
Why is Cost Control Important?
Cost control is vital for several reasons.
Firstly, it allows a company to maintain a healthy profit margin despite market fluctuations.
Secondly, efficient cost control can enhance a company’s competitiveness by enabling it to offer competitive prices without sacrificing profitability.
Moreover, it ensures sustainability by minimizing waste and maximizing resource utilization.
All these aspects contribute to the long-term success and operational efficiency of a company.
The Role of the Purchasing Department
The purchasing department plays a pivotal role in managing supply chain costs.
It is responsible for procuring goods and services necessary for production and operations.
An efficient purchasing department can directly influence cost control by negotiating better terms with suppliers, ensuring the quality of materials, and maintaining efficient inventory levels.
Effective Supplier Management
A key responsibility of the purchasing department is managing supplier relationships.
By building strong partnerships with suppliers, the purchasing team can negotiate cost-effective deals, secure favorable payment terms, and ensure timely delivery of quality materials.
These relationships also pave the way for collaborative cost-reduction initiatives like supplier consolidation or bulk purchasing, which can significantly lower expenses.
Inventory Management
In the realm of cost control, inventory management is critical.
The purchasing department must strike a balance between having enough stock to meet demand and minimizing excess inventory that ties up capital and increases holding costs.
Techniques such as Just-In-Time (JIT) inventory can reduce costs by minimizing storage needs and reducing waste due to obsolescence.
Accurate demand forecasting and inventory optimization tools are essential to achieve these objectives.
Leveraging Technology
Technology plays an indispensable role in modern cost control strategies.
The purchasing department can utilize advanced software solutions to analyze spending patterns, track supplier performance, and automate repetitive procurement processes.
These technologies improve efficiency, reduce human error, and provide valuable insights that guide decision-making.
Furthermore, they enable real-time collaboration and data exchange with suppliers, enhancing transparency and accountability.
Strategies for Effective Cost Control
To effectively manage supply chain costs, companies should consider implementing a combination of strategies.
Here are some proven approaches:
Unified Procurement Processes
Creating standardized procurement processes across the organization can streamline operations and reduce costs.
This involves adopting uniform policies, procedures, and systems that ensure consistent and efficient purchasing practices.
Standardization also enhances transparency and accountability, making it easier to identify areas for potential cost savings.
Supplier Performance Evaluation
Regularly evaluating supplier performance is crucial to ensure they meet contractual obligations and deliver value.
Assessments should focus on key performance indicators such as delivery times, quality, cost, and reliability.
By establishing performance benchmarks, companies can identify underperforming suppliers and take corrective actions, such as renegotiating terms or seeking alternative partners.
Dynamic Pricing and Cost Transparency
Incorporating dynamic pricing strategies and cost transparency into the supply chain can help businesses adapt to market fluctuations and maintain competitiveness.
Dynamic pricing involves adjusting prices based on demand, competition, and other factors to maximize revenue.
Cost transparency, on the other hand, involves openly sharing cost-related information with suppliers to improve collaboration and encourage joint cost-saving efforts.
Continuous Improvement Programs
Implementing continuous improvement programs based on methodologies like Lean and Six Sigma can drive cost reduction efforts.
These programs identify inefficiencies, eliminate waste, and enhance process efficiency, leading to substantial cost savings.
Encouraging a culture of continuous improvement within the purchasing department fosters innovation and empowers employees to discover new cost-saving opportunities.
The Role of Data and Analytics
Data and analytics have become essential tools in managing supply chain costs effectively.
By leveraging data-driven insights, businesses can make informed decisions about procurement, inventory management, and supplier relationships.
Analyzing Spending Patterns
By analyzing spending patterns, companies can identify significant cost drivers and areas where savings can be achieved.
Spend analysis tools categorize and examine expenses, revealing trends and patterns that help in strategic planning and budgeting.
This information is invaluable in negotiating better terms with suppliers and creating more efficient procurement strategies.
Predictive Analytics
Predictive analytics leverages historical data to forecast future trends and demand.
This enables companies to anticipate potential disruptions and adjust their procurement strategies accordingly.
For instance, if predictive models show an increase in demand, the purchasing department can proactively secure additional inventory at favorable prices before market rates rise.
Performance Monitoring
Through data analytics, companies can continuously monitor supplier performance and track compliance with agreed-upon terms.
This real-time visibility allows for quick identification of issues and ensures that suppliers consistently meet performance expectations.
By addressing problems promptly, businesses can maintain smooth operations and avoid costly disruptions.
Conclusion
In conclusion, cost control within the supply chain is a critical component of maintaining competitiveness and profitability.
The purchasing department plays a fundamental role in achieving this by effectively managing suppliers, optimizing inventory, and leveraging technology.
By implementing proven strategies and utilizing data-driven insights, companies can significantly enhance their cost control efforts.
Ultimately, a well-managed supply chain fosters operational efficiency, sustainability, and long-term success for the organization.
資料ダウンロード
QCD調達購買管理クラウド「newji」は、調達購買部門で必要なQCD管理全てを備えた、現場特化型兼クラウド型の今世紀最高の購買管理システムとなります。
ユーザー登録
調達購買業務の効率化だけでなく、システムを導入することで、コスト削減や製品・資材のステータス可視化のほか、属人化していた購買情報の共有化による内部不正防止や統制にも役立ちます。
NEWJI DX
製造業に特化したデジタルトランスフォーメーション(DX)の実現を目指す請負開発型のコンサルティングサービスです。AI、iPaaS、および先端の技術を駆使して、製造プロセスの効率化、業務効率化、チームワーク強化、コスト削減、品質向上を実現します。このサービスは、製造業の課題を深く理解し、それに対する最適なデジタルソリューションを提供することで、企業が持続的な成長とイノベーションを達成できるようサポートします。
オンライン講座
製造業、主に購買・調達部門にお勤めの方々に向けた情報を配信しております。
新任の方やベテランの方、管理職を対象とした幅広いコンテンツをご用意しております。
お問い合わせ
コストダウンが利益に直結する術だと理解していても、なかなか前に進めることができない状況。そんな時は、newjiのコストダウン自動化機能で大きく利益貢献しよう!
(Β版非公開)