- お役立ち記事
- The Importance of Developing a Business Continuity Plan (BCP) in Global Procurement for Manufacturers
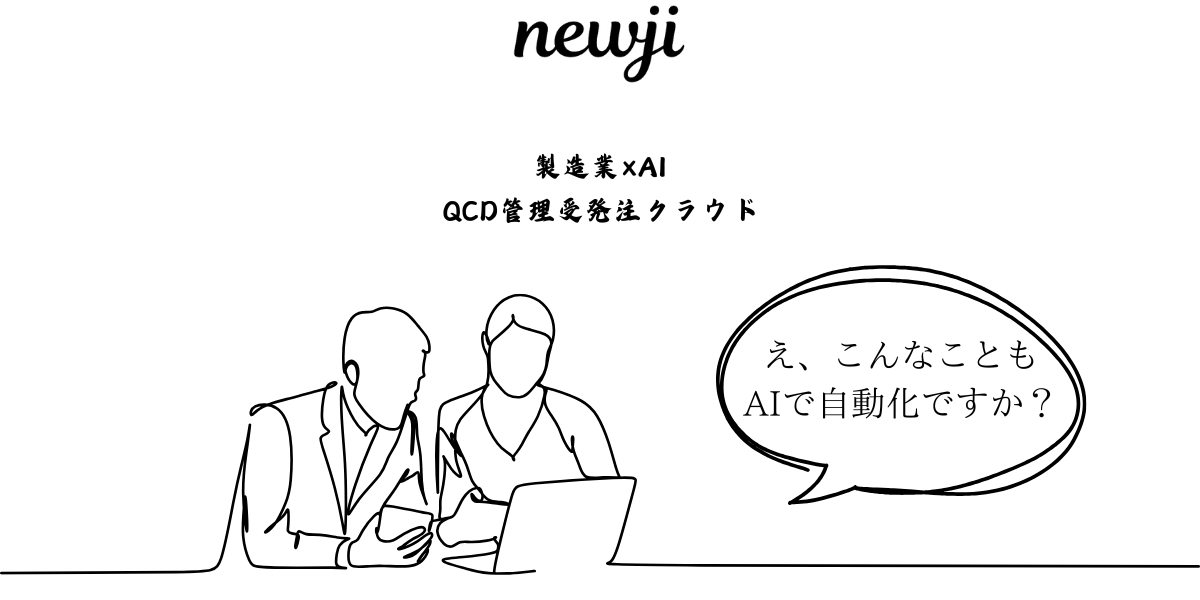
The Importance of Developing a Business Continuity Plan (BCP) in Global Procurement for Manufacturers
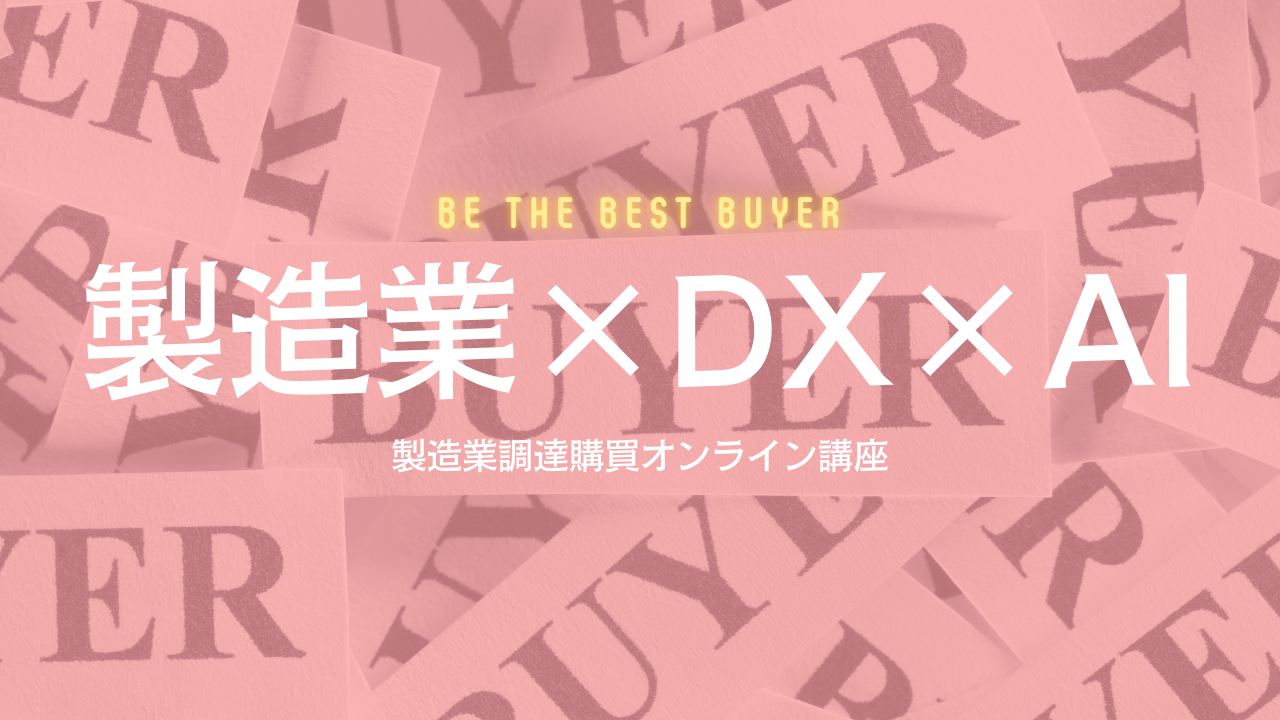
Most manufacturers rely heavily on global suppliers and partners to source raw materials, components, and services needed for production. However, disruptions in the global supply chain are becoming increasingly common due to geopolitical instability, natural disasters, pandemics, and other crises. The COVID-19 pandemic exposed weaknesses in many organizations’ supply chain resilience, leading to shortages and delays that impacted operations and revenue. Developing a robust business continuity plan (BCP) is critical for manufacturers to mitigate risks and maintain business operations during disruptive events.
A BCP outlines the strategies, processes, and resources manufacturers need to continue critical functions across their supply chain if a disruption occurs. The plan should identify single points of failure, develop alternative sourcing options, and prepare processes to shift production or sources rapidly if needed. Manufacturers must determine which suppliers are most critical and conduct risk assessments of their operations, locations, and industries. Single-source components or those with limited suppliers present the greatest risks if a disruption hits that source. By identifying alternatives beforehand, companies can move production or sourcing swiftly rather than scrambling in a crisis.
The BCP should also determine communication protocols for notifying suppliers, customers, and internal stakeholders swiftly regarding a disruption and the planned response. It is essential that everyone understands roles, expectations, and processes for shifting production plans or sourcing alternatives. Regular testing and training help ensure employees understand response plans and can execute them smoothly if needed. Communication channels and processes established beforehand build transparency and confidence with customers and partners during a crisis. Advance testing helps surface issues to improve the plan over time.
Supply chain mapping and inventory management are also key components of a strong manufacturer BCP. Mapping all tiers of suppliers, locations, transportation routes, and dependencies between different suppliers and production facilities provides visibility into potential weak links. It also aids rapid risk assessment of new suppliers. Maintaining higher inventory buffers of critical components mitigates risks of short-term disruptions, buying time to shift production plans or sources. Using forecasting to stagger larger inventory purchases over time balances costs and risks. Multi-site warehouse strategies distribute inventory to facilitate rapid shifts in sourcing or production.
Global manufacturers must also consider political and economic risks across countries in their BCP. Trade restrictions, conflicts, natural disasters, or health crises can impact major supplier nations or transportation hubs. The plan should identify alternative sourcing or transportation options if primary routes face disruptions. Where possible, balancing sourcing across different countries or continents distributes political and disaster risks. Understanding trade compliance and import/export complexities in different markets also supports rapid switching of sourcing nations if needed without delays. Broad global supplier networks strengthen supply chain resilience and provide viable alternatives when disruption hits specific areas.
Regular BCP training, testing, and updates are essential for global manufacturing organizations. Exercises help surface gaps or weaknesses in sourcing strategies, communication processes, or supplier relationships before a real crisis occurs. After-action reviews incorporate lessons learned to continuously strengthen the plans. New risks emerge constantly that require reassessing critical suppliers and markets. Evolving trade conditions, emerging diseases, supply constraints on raw materials, and geopolitical shifts all demand regular BCP reevaluation. Failure to maintain risk awareness and adapt plans leaves manufacturers vulnerable to disruptions that threaten revenue, market share and brand reputation. A robust, frequently updated BCP builds resilience against global supply chain disruptions and protects business continuity.
資料ダウンロード
QCD調達購買管理クラウド「newji」は、調達購買部門で必要なQCD管理全てを備えた、現場特化型兼クラウド型の今世紀最高の購買管理システムとなります。
ユーザー登録
調達購買業務の効率化だけでなく、システムを導入することで、コスト削減や製品・資材のステータス可視化のほか、属人化していた購買情報の共有化による内部不正防止や統制にも役立ちます。
NEWJI DX
製造業に特化したデジタルトランスフォーメーション(DX)の実現を目指す請負開発型のコンサルティングサービスです。AI、iPaaS、および先端の技術を駆使して、製造プロセスの効率化、業務効率化、チームワーク強化、コスト削減、品質向上を実現します。このサービスは、製造業の課題を深く理解し、それに対する最適なデジタルソリューションを提供することで、企業が持続的な成長とイノベーションを達成できるようサポートします。
オンライン講座
製造業、主に購買・調達部門にお勤めの方々に向けた情報を配信しております。
新任の方やベテランの方、管理職を対象とした幅広いコンテンツをご用意しております。
お問い合わせ
コストダウンが利益に直結する術だと理解していても、なかなか前に進めることができない状況。そんな時は、newjiのコストダウン自動化機能で大きく利益貢献しよう!
(Β版非公開)