- お役立ち記事
- The Importance of Forming Simulation in Press Processing
The Importance of Forming Simulation in Press Processing
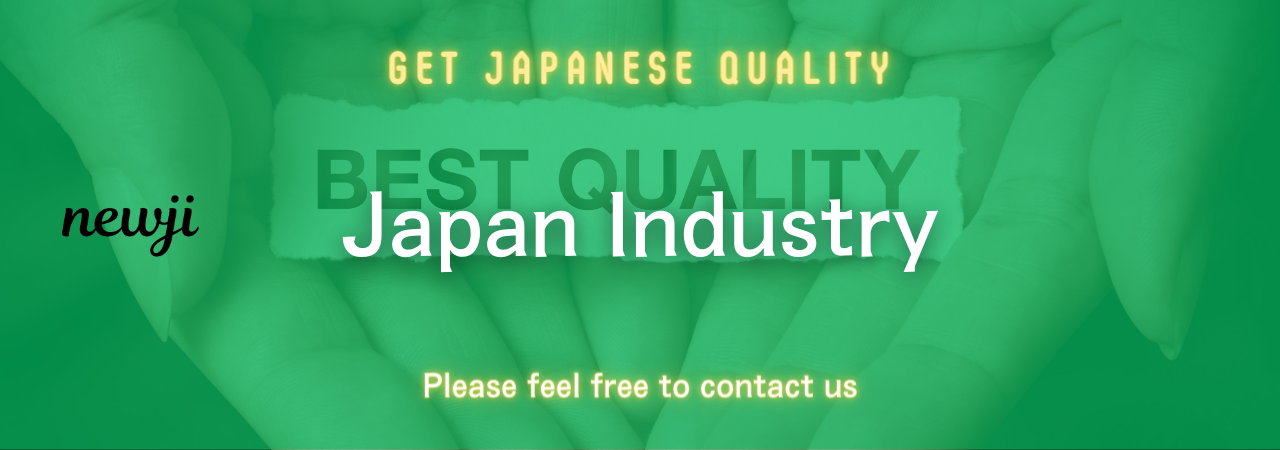
Press processing, commonly known as stamping, is a vital manufacturing process used to convert raw metal sheets into specific shapes and forms.
This process finds extensive applications across various industries, including automotive, aerospace, electronics, and consumer goods.
One of the key aspects that ensure the efficiency and precision of press processing is forming simulation.
目次
Understanding Forming Simulation
Forming simulation is a computational technique used to predict the behavior of materials during the press processing stage.
By using advanced software, manufacturers can simulate how a metal sheet will deform under specific conditions, such as applied forces, temperatures, and tool interactions.
This simulation helps in understanding the potential issues that might arise during the actual pressing operation.
The Role of Forming Simulation
Forming simulation plays a crucial role in press processing for several reasons.
Firstly, it reduces the need for physical prototypes, which can be both time-consuming and costly.
By accurately predicting the outcome of the forming process, manufacturers can optimize designs and processes before committing to physical production.
Additionally, forming simulation helps in identifying potential defects and problems that might occur during pressing.
Common issues such as wrinkling, tearing, and springback can be predicted and mitigated using simulation tools.
This ensures that the final product meets the required specifications and quality standards.
Advantages of Forming Simulation
There are numerous advantages to incorporating forming simulation into press processing workflows:
Improved Product Quality: By simulating the forming process, manufacturers can ensure that the final product meets precise tolerances and quality standards.
This leads to fewer defective parts and higher customer satisfaction.
Cost Savings: Forming simulation helps in minimizing material waste and reducing the need for trial-and-error in the production process.
This translates to significant cost savings in terms of materials, labor, and time.
Faster Time to Market: With simulation tools, manufacturers can quickly iterate on designs and processes, shortening the development cycle.
This enables businesses to bring products to market faster, gaining a competitive edge.
Enhanced Tool Life: Forming simulation allows for the optimization of tool design and usage.
By predicting wear and tear, manufacturers can extend the life of their tooling, reducing maintenance costs and downtime.
The Process of Forming Simulation
Forming simulation involves several steps to ensure accurate and reliable predictions.
Material Characterization
The first step in forming simulation is to gather accurate data on the material being used.
This includes information on the material’s mechanical properties, such as yield strength, Young’s modulus, and strain-hardening behavior.
Accurate material characterization ensures that the simulation results closely match real-world behavior.
Geometry and Tooling Design
Next, the geometry of the metal sheet and tooling design is defined within the simulation software.
This involves creating a digital replica of the workpiece and the tools that will be used in the press processing operation.
Accurate geometry and tooling design are essential for obtaining reliable simulation results.
Process Parameters
The simulation software requires input on various process parameters, such as the speed of the press, the applied forces, and the temperature conditions.
These parameters are crucial for accurately predicting the material’s response to the forming process.
Running the Simulation
Once all the necessary data and parameters are inputted into the simulation software, the simulation is run.
The software uses complex algorithms to simulate the deformation of the metal sheet under the defined conditions.
The output includes detailed information on how the material will behave, potential defects, and areas of concern.
Analyzing the Results
After the simulation is complete, the results are analyzed to identify any issues or areas for improvement.
This analysis helps in optimizing the design and process parameters to ensure a successful forming operation in the physical world.
Applications of Forming Simulation
Forming simulation finds applications across various industries, each with unique requirements and challenges.
Automotive Industry
In the automotive industry, forming simulation is used extensively to design and manufacture complex components such as car body panels, structural frames, and engine parts.
The ability to predict and mitigate potential defects is crucial for ensuring the safety and performance of automotive components.
Aerospace Industry
The aerospace industry relies on forming simulation to produce lightweight yet robust components for aircraft and spacecraft.
Simulation helps in achieving the precise tolerances required for aerospace applications, where even minor deviations can have significant consequences.
Electronics Industry
In the electronics industry, forming simulation is used to manufacture delicate and intricate components, such as connectors, housings, and heat sinks.
The ability to predict material behavior at small scales is essential for ensuring the functionality and reliability of electronic devices.
Consumer Goods Industry
The consumer goods industry utilizes forming simulation to produce a wide range of products, from kitchen appliances to furniture.
The simulation helps in achieving consistent quality and reducing production costs, ensuring that consumer products meet high standards.
Challenges and Future Trends
While forming simulation offers numerous benefits, it is not without its challenges.
The accuracy of simulation results depends heavily on the quality of input data, such as material properties and process parameters.
Additionally, the complexity of the simulation can lead to high computational costs and time requirements.
However, advancements in computing power and software algorithms are continually improving the accuracy and efficiency of forming simulation.
Technological trends such as artificial intelligence and machine learning are being integrated into simulation tools, enabling more sophisticated and accurate predictions.
Moreover, the use of digital twins – virtual replicas of physical systems – is becoming more prevalent.
Digital twins allow for real-time monitoring and optimization of the forming process, further enhancing the effectiveness of simulation.
In conclusion, forming simulation is an indispensable tool in the field of press processing.
It enables manufacturers to optimize designs, reduce costs, and ensure high-quality production.
As technology continues to evolve, the capabilities and applications of forming simulation will only expand, paving the way for more efficient and precise manufacturing processes.
資料ダウンロード
QCD調達購買管理クラウド「newji」は、調達購買部門で必要なQCD管理全てを備えた、現場特化型兼クラウド型の今世紀最高の購買管理システムとなります。
ユーザー登録
調達購買業務の効率化だけでなく、システムを導入することで、コスト削減や製品・資材のステータス可視化のほか、属人化していた購買情報の共有化による内部不正防止や統制にも役立ちます。
NEWJI DX
製造業に特化したデジタルトランスフォーメーション(DX)の実現を目指す請負開発型のコンサルティングサービスです。AI、iPaaS、および先端の技術を駆使して、製造プロセスの効率化、業務効率化、チームワーク強化、コスト削減、品質向上を実現します。このサービスは、製造業の課題を深く理解し、それに対する最適なデジタルソリューションを提供することで、企業が持続的な成長とイノベーションを達成できるようサポートします。
オンライン講座
製造業、主に購買・調達部門にお勤めの方々に向けた情報を配信しております。
新任の方やベテランの方、管理職を対象とした幅広いコンテンツをご用意しております。
お問い合わせ
コストダウンが利益に直結する術だと理解していても、なかなか前に進めることができない状況。そんな時は、newjiのコストダウン自動化機能で大きく利益貢献しよう!
(Β版非公開)