- お役立ち記事
- The importance of “on-time delivery rate” and its evaluation method for purchasing departments
月間76,176名の
製造業ご担当者様が閲覧しています*
*2025年3月31日現在のGoogle Analyticsのデータより
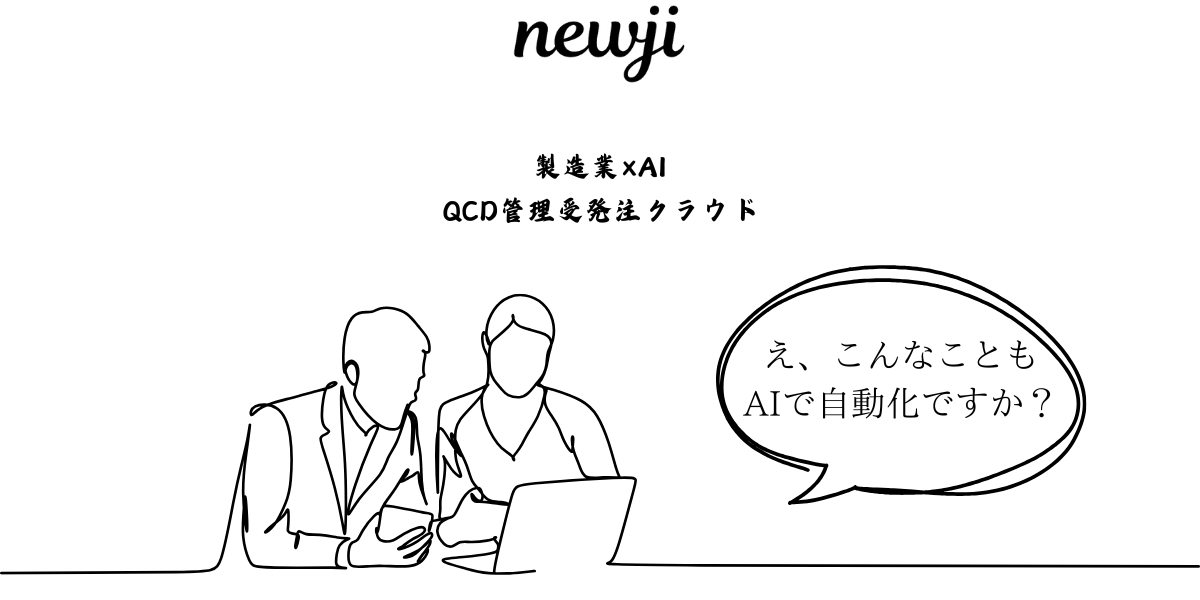
The importance of “on-time delivery rate” and its evaluation method for purchasing departments
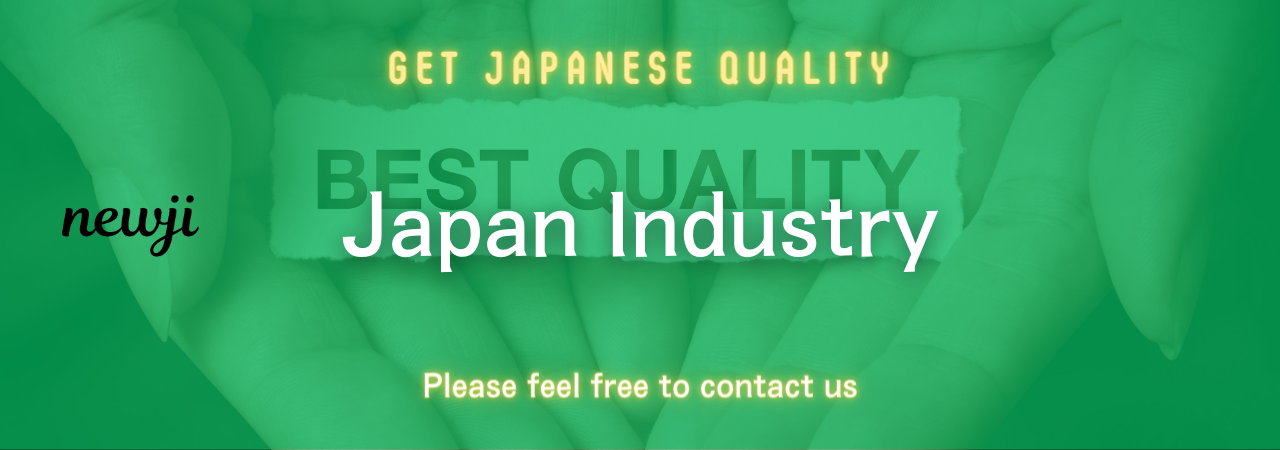
目次
Understanding On-Time Delivery Rate
On-time delivery rate is a crucial metric in the world of purchasing and supply chain management.
It is a measure of a supplier’s ability to deliver products or services by the agreed-upon deadline.
Maintaining a high on-time delivery rate ensures that the business runs smoothly and can meet its own commitments to customers.
This metric plays a significant role in evaluating supplier performance, planning future orders, and fostering strong business relationships.
Why On-Time Delivery Rate Matters
The importance of on-time delivery in purchasing departments cannot be overstated.
Timely delivery of goods and services is essential for several reasons:
1. **Customer Satisfaction:** Customers expect products and services to be delivered when promised.
Any delay can lead to dissatisfaction, loss of trust, and potential loss of business.
2. **Inventory Management:** Accurate delivery times help maintain optimal inventory levels.
Purchasing departments can avoid overstocking or running into shortages with precise delivery schedules.
3. **Operational Efficiency:** On-time deliveries ensure that production lines and business operations run smoothly.
Any delays can disrupt operational flow and result in increased costs.
4. **Cost Control:** Late deliveries can lead to additional costs such as expedited shipping fees or penalties for not meeting contract terms.
5. **Reputation Management:** Consistent on-time delivery enhances a company’s reputation as a reliable partner.
This is especially important in industries where time-to-market is crucial.
Factors Influencing On-Time Delivery Rate
Several factors can impact a supplier’s ability to deliver on time:
1. **Supplier Reliability:** A supplier’s track record in delivering on commitments plays a crucial role in on-time delivery rates.
2. **Logistics and Transportation:** Efficient logistics systems and reliable transportation networks contribute significantly to timely deliveries.
3. **Order Size and Complexity:** Larger, more complex orders may take longer to process and deliver, affecting the on-time delivery rate.
4. **External Factors:** Weather conditions, political issues, and economic factors can all affect transportation and delivery schedules.
5. **Communication and Coordination:** Effective communication between the purchasing department, supplier, and logistics partners is essential for timely deliveries.
Evaluating On-Time Delivery Rate
Evaluating the on-time delivery rate involves calculating the percentage of orders delivered by the expected date.
Here’s a simple method to evaluate it:
1. **Data Collection:** Gather data on the total number of deliveries and those delivered on time within a specific period.
This could be monthly, quarterly, or annually, depending on the analysis required.
2. **Calculation:** Use the formula:
On-Time Delivery Rate (%) = (Number of On-Time Deliveries / Total Number of Deliveries) * 100
3. **Analysis:** Compare the on-time delivery rate with industry benchmarks or historical data to gauge performance.
4. **Root Cause Analysis:** Identify reasons for late deliveries, whether they are due to internal processes, supplier issues, or external factors.
5. **Improvement Plans:** Develop and implement strategies to address identified issues and improve future delivery performance.
Improving On-Time Delivery Rate
Improving the on-time delivery rate requires a strategic approach and collaboration across departments and with suppliers:
1. **Supplier Relationship Management:** Build strong relationships with suppliers to ensure commitment and open communication.
This can include regular performance evaluations and constructive feedback.
2. **Process Optimization:** Streamline internal processes to reduce lead times and improve coordination.
Implementing technology solutions like supply chain management software can help automate and optimize processes.
3. **Contractual Agreements:** Clearly define delivery expectations in supplier contracts, including penalties for non-compliance.
4. **Inventory Management:** Use demand forecasting and real-time inventory systems to ensure accurate order planning.
This reduces the chance of last-minute changes that disrupt delivery schedules.
5. **Risk Management:** Develop contingency plans for unforeseen disruptions.
This can include alternate supplier arrangements and flexible delivery options.
Measuring Success in On-Time Delivery
Successful measurement of the on-time delivery rate involves setting realistic and achievable goals, regularly reviewing performance, and adapting strategies as needed.
Key performance indicators (KPIs) can help track progress and identify areas for improvement.
– **Benchmarking:** Compare your on-time delivery rate with industry standards and leaders to identify competitive gaps.
– **Regular Reviews:** Conduct regular reviews of delivery performance, encouraging continuous improvement.
– **Feedback Loops:** Create systems for customer feedback on delivery performance, and use this information to refine processes.
By prioritizing on-time delivery rates, purchasing departments can enhance supply chain efficiency and maintain strong customer relationships.
A proactive approach to managing and improving delivery schedules can lead to significant business advantages and long-term sustainability.
In conclusion, the on-time delivery rate is more than just a logistical metric.
It is a vital indicator of a company’s reliability, efficiency, and reputation.
By understanding its importance and implementing effective evaluation and improvement strategies, purchasing departments can drive organizational success and customer satisfaction.
資料ダウンロード
QCD管理受発注クラウド「newji」は、受発注部門で必要なQCD管理全てを備えた、現場特化型兼クラウド型の今世紀最高の受発注管理システムとなります。
ユーザー登録
受発注業務の効率化だけでなく、システムを導入することで、コスト削減や製品・資材のステータス可視化のほか、属人化していた受発注情報の共有化による内部不正防止や統制にも役立ちます。
NEWJI DX
製造業に特化したデジタルトランスフォーメーション(DX)の実現を目指す請負開発型のコンサルティングサービスです。AI、iPaaS、および先端の技術を駆使して、製造プロセスの効率化、業務効率化、チームワーク強化、コスト削減、品質向上を実現します。このサービスは、製造業の課題を深く理解し、それに対する最適なデジタルソリューションを提供することで、企業が持続的な成長とイノベーションを達成できるようサポートします。
製造業ニュース解説
製造業、主に購買・調達部門にお勤めの方々に向けた情報を配信しております。
新任の方やベテランの方、管理職を対象とした幅広いコンテンツをご用意しております。
お問い合わせ
コストダウンが利益に直結する術だと理解していても、なかなか前に進めることができない状況。そんな時は、newjiのコストダウン自動化機能で大きく利益貢献しよう!
(β版非公開)