- お役立ち記事
- The Importance of OT and Management Methods: Optimizing Operational Technology in Manufacturing
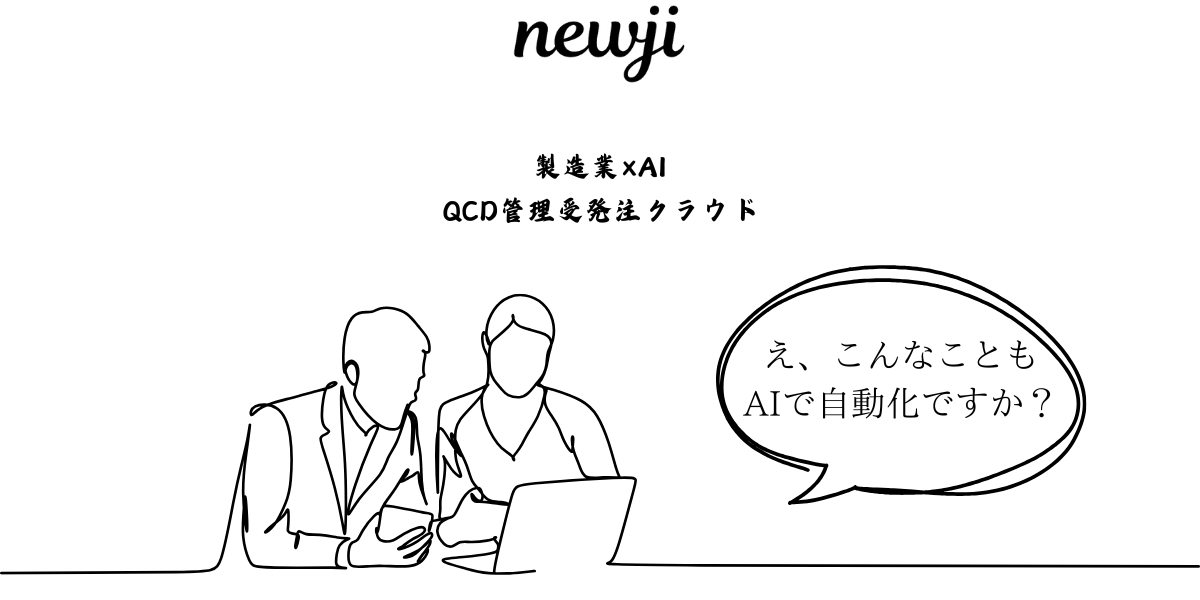
The Importance of OT and Management Methods: Optimizing Operational Technology in Manufacturing
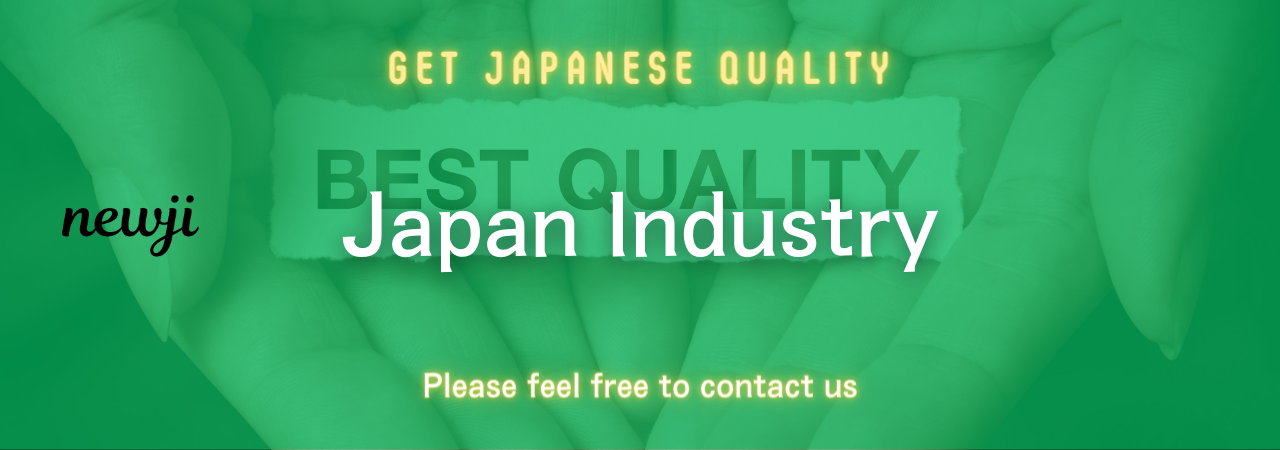
Operational Technology (OT) is a vital component in the world of manufacturing.
Without it, many of the machines and processes that produce goods wouldn’t function efficiently.
Understanding and optimizing OT is essential for any manufacturing business that wants to stay competitive and productive in today’s fast-paced market.
目次
What is Operational Technology (OT)?
Operational Technology, often referred to as OT, encompasses the hardware and software systems that monitor and control industrial processes.
These processes can be found in manufacturing, energy production, and other industrial areas.
OT is crucial in ensuring that machinery and equipment operate smoothly and safely.
Without proper OT, factories and production facilities would face significant challenges in maintaining efficiency and productivity.
OT vs. IT: Understanding the Difference
It’s important to differentiate between Operational Technology (OT) and Information Technology (IT).
While IT deals with data processing, communications, and storage, OT focuses on physical processes.
For instance, IT systems manage email servers, databases, and business applications.
In contrast, OT systems might control a robot arm on an assembly line or regulate the temperature in a chemical plant.
Both IT and OT are essential, but they serve different purposes and require specific expertise.
Why is Optimizing OT Important?
Optimizing OT can lead to numerous benefits for a manufacturing business.
From increased efficiency and productivity to reduced costs and improved safety, the advantages are considerable.
Here are some of the key reasons why optimizing OT is critical:
Increased Efficiency and Productivity
One of the main goals of optimizing OT is to enhance efficiency and productivity.
When machinery and processes are running smoothly, production times are reduced, and output is maximized.
Efficient OT systems can help identify bottlenecks in the production process, allowing manufacturers to address these issues promptly.
As a result, downtime is minimized, and the overall production cycle becomes more streamlined.
Reduced Costs
Optimizing OT can also lead to significant cost savings.
By ensuring that machinery and equipment operate at peak efficiency, manufacturers can reduce energy consumption and minimize wear and tear on assets.
Predictive maintenance, which involves using data analysis to predict when equipment will need repairs, can help avoid costly unplanned downtime.
Furthermore, by automating certain processes, businesses can reduce labor costs and increase production capacity without the need for additional staff.
Improved Safety
Safety is paramount in any manufacturing environment.
Optimized OT systems include various safety measures to protect workers and equipment.
For instance, sensors can detect hazardous conditions and shut down machinery to prevent accidents.
Automation can reduce the need for human intervention in dangerous tasks, further enhancing safety.
By prioritizing safety, manufacturers can avoid costly accidents and ensure a healthy working environment for their employees.
Data-Driven Decision Making
Modern OT systems often include data collection and analysis capabilities.
By gathering and analyzing data from machinery and processes, manufacturers can make informed decisions to improve operations.
For example, data might reveal that a particular machine is underperforming, prompting maintenance or replacement.
This data-driven approach ensures that decisions are based on facts rather than intuition, leading to more accurate and effective strategies.
Methods to Optimize OT in Manufacturing
There are several methods and strategies that manufacturers can use to optimize their OT systems.
Implementing these methods can help businesses reap the benefits discussed earlier, leading to a more efficient and productive operation.
Regular Maintenance and Upgrades
One of the simplest yet most effective ways to optimize OT is to conduct regular maintenance and upgrades.
Ensuring that machinery and equipment are well-maintained can prevent unexpected breakdowns and extend their lifespan.
Additionally, upgrading outdated systems can enhance performance and introduce new capabilities.
Adopting a proactive maintenance schedule can help identify potential issues before they become serious problems, reducing downtime and maintenance costs.
Implementing Automation
Automation is a key component of modern OT optimization.
By automating repetitive and time-consuming tasks, manufacturers can reduce human error and increase efficiency.
For example, robotic arms can be used for assembly tasks, while automated sensors can monitor and adjust environmental conditions.
When implementing automation, it’s important to choose systems that integrate seamlessly with existing OT infrastructure to avoid compatibility issues.
Training and Skill Development
Investing in training and skill development for employees is crucial for successful OT optimization.
Workers need to understand how to operate and maintain new systems effectively.
Providing regular training sessions ensures that staff are up-to-date with the latest technologies and best practices.
Furthermore, skilled operators can identify potential improvements and suggest innovative solutions, contributing to overall optimization efforts.
Leveraging IoT and Data Analytics
The Internet of Things (IoT) and data analytics play a significant role in optimizing OT.
IoT devices can collect real-time data from machinery and equipment, providing valuable insights into operational performance.
By analyzing this data, manufacturers can identify trends, predict maintenance needs, and optimize production processes.
Integrating IoT and data analytics into OT systems enables a more proactive and informed approach to managing manufacturing operations.
Challenges in OT Optimization
While the benefits of optimizing OT are clear, it’s important to acknowledge the challenges that manufacturers may face.
Addressing these challenges is essential to ensure successful optimization efforts.
Integration with Legacy Systems
Many manufacturing facilities still rely on legacy systems which can be challenging to integrate with modern OT solutions.
These outdated systems may not be compatible with new technologies, requiring significant modifications or replacements.
Working with experienced professionals and investing in suitable solutions can help overcome these integration challenges.
Cybersecurity Threats
As OT systems become more connected and integrated with IT networks, they become more vulnerable to cybersecurity threats.
Protecting sensitive data and ensuring the security of OT systems is crucial.
Implementing robust cybersecurity measures such as firewalls, encryption, and regular security audits can help mitigate these risks.
High Initial Costs
The initial costs of optimizing OT can be high, particularly when upgrading equipment or implementing new automation systems.
However, the long-term benefits and cost savings often outweigh these initial expenses.
Companies should consider the return on investment (ROI) when planning OT optimization projects and allocate resources accordingly.
Concluding, optimizing Operational Technology in manufacturing is essential for boosting efficiency, reducing costs, increasing safety, and making data-driven decisions.
By understanding the importance of OT and implementing effective optimization methods, manufacturers can enhance their operations and maintain a competitive edge in the industry.
Despite potential challenges, the rewards of a well-optimized OT system make the effort worthwhile.
Through regular maintenance, automation, employee training, and the adoption of IoT and data analytics, manufacturing businesses can achieve significant improvements in their processes and results.
資料ダウンロード
QCD調達購買管理クラウド「newji」は、調達購買部門で必要なQCD管理全てを備えた、現場特化型兼クラウド型の今世紀最高の購買管理システムとなります。
ユーザー登録
調達購買業務の効率化だけでなく、システムを導入することで、コスト削減や製品・資材のステータス可視化のほか、属人化していた購買情報の共有化による内部不正防止や統制にも役立ちます。
NEWJI DX
製造業に特化したデジタルトランスフォーメーション(DX)の実現を目指す請負開発型のコンサルティングサービスです。AI、iPaaS、および先端の技術を駆使して、製造プロセスの効率化、業務効率化、チームワーク強化、コスト削減、品質向上を実現します。このサービスは、製造業の課題を深く理解し、それに対する最適なデジタルソリューションを提供することで、企業が持続的な成長とイノベーションを達成できるようサポートします。
オンライン講座
製造業、主に購買・調達部門にお勤めの方々に向けた情報を配信しております。
新任の方やベテランの方、管理職を対象とした幅広いコンテンツをご用意しております。
お問い合わせ
コストダウンが利益に直結する術だと理解していても、なかなか前に進めることができない状況。そんな時は、newjiのコストダウン自動化機能で大きく利益貢献しよう!
(Β版非公開)