- お役立ち記事
- The importance of quality control and delivery date management in the production of custom-made jigs and containers for measuring instruments
月間77,185名の
製造業ご担当者様が閲覧しています*
*2025年2月28日現在のGoogle Analyticsのデータより
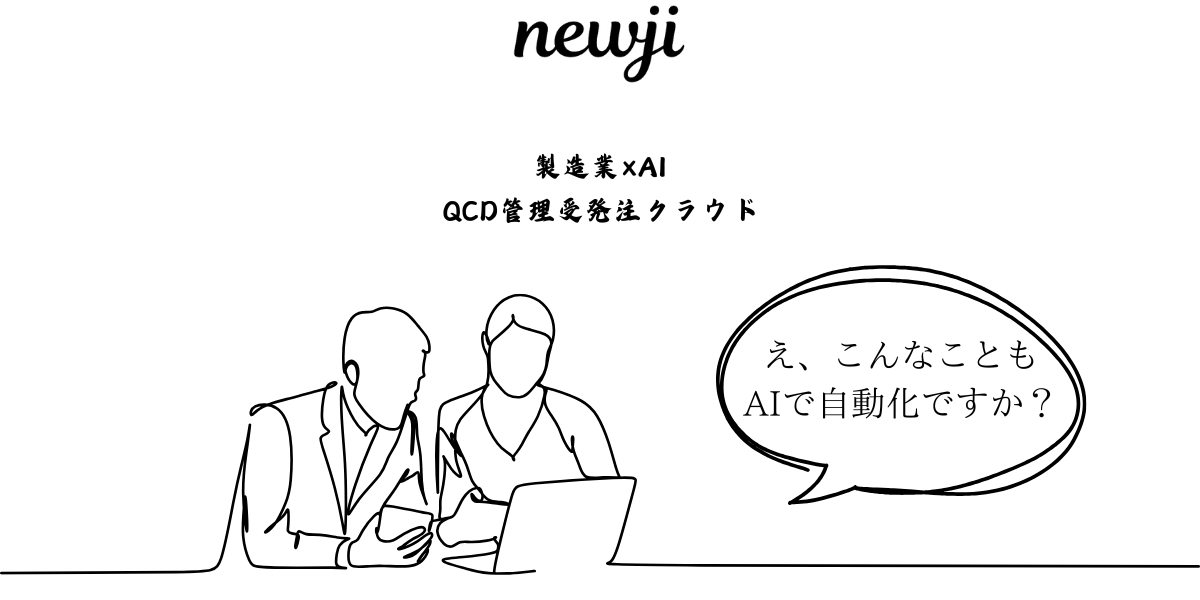
The importance of quality control and delivery date management in the production of custom-made jigs and containers for measuring instruments
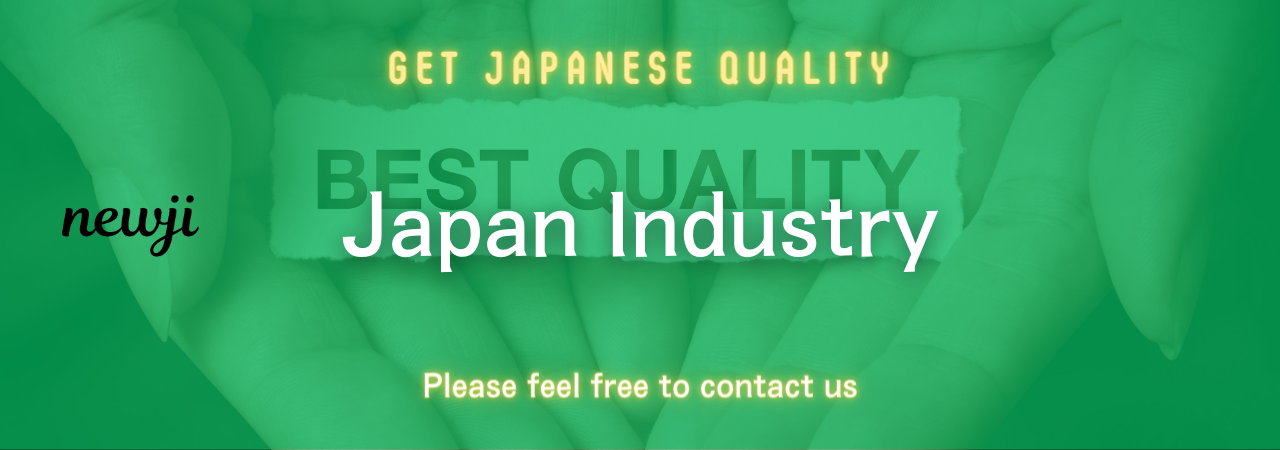
目次
The Role of Quality Control in Custom-Made Jigs and Containers
Quality control is a critical aspect in the production of custom-made jigs and containers, especially when these items are used for measuring instruments.
These specialized tools and containers must meet precise requirements to ensure accurate measurements and safe handling of sensitive equipment.
Quality control starts from the very first step of the production process.
This means selecting the appropriate materials that suit the specific needs of the measuring instruments.
High-quality materials are essential to provide durability and reliability, ensuring that the jigs and containers can withstand various environmental conditions and frequent usage without compromising their structural integrity.
Once the suitable materials are chosen, the design phase is where quality control plays another crucial role.
Each jig and container needs to be tailored to the specific dimensions and requirements of the instruments they will support or house.
This customization ensures a snug fit and optimal performance.
Designers and engineers collaborate closely to create precise blueprints that serve as a foundation for flawless production.
During the manufacturing process, rigorous testing and inspections are conducted at every stage.
From initial fabrication to final assembly, each component is scrutinized to ensure it meets predetermined quality standards.
Advanced techniques such as computer-aided inspection and 3D scanning may be employed to guarantee that each piece conforms to exact specifications.
Any deviation from the set standards can result in malfunctions or inaccuracies when the jigs or containers are used, which makes rigorous quality checks indispensable.
Moreover, the functionality of the finished product is a direct reflection of the quality control processes implemented throughout production.
Testing involves not only checking physical dimensions but also assessing the overall performance of the jigs and containers with the instruments they are designed to support.
This includes verifying that they do not interfere with the instrument’s precision and can hold up under expected operational conditions.
The Importance of Delivery Date Management
Delivery date management is another critical factor in the production of custom-made jigs and containers for measuring instruments.
Timeliness is essential, as delays can disrupt the entire workflow of the institution or facility that relies on these tools.
Effective delivery date management begins with accurate project planning.
Understanding client requirements and deadlines allows manufacturers to create realistic timelines that consider design, production, and quality control phases.
Communication with clients is crucial in this aspect to align production schedules with client timelines and expectations.
During production, manufacturers must monitor progress diligently to ensure every phase is on schedule.
Any potential disruptions or delays should be identified early so that corrective measures can be taken promptly.
Part of successful delivery date management also involves having contingency plans in place to address unforeseen issues that might arise.
Advanced software solutions can aid in tracking and managing production schedules.
These tools can provide real-time updates on every facet of the production process, from raw material procurement to shipping logistics.
Such transparency helps prevent bottlenecks and highlights areas where efficiency might be improved, ensuring that delivery dates are met consistently.
Furthermore, the consequences of delayed delivery can be significant.
For businesses, this might mean postponed product launches or increased downtime while awaiting the arrival of necessary tools.
For laboratories or technical environments, delays may impair experiments or data collection activities, leading to tangible setbacks.
Reliable delivery is not just about meeting client expectations but also about maintaining the manufacturer’s reputation.
A good track record of on-time delivery contributes to customer satisfaction and fosters long-term business relationships.
Balancing Quality and Timeliness
While both quality control and delivery date management are pivotal, balancing these two priorities is vital for success.
An overemphasis on either can lead to unwanted outcomes: compromising quality for speed can undermine the component’s performance, while excessive focus on quality can extend production time and delay delivery.
It is crucial to establish a harmonious workflow that ensures both quality and timeliness.
This means investing in skilled personnel and advanced technologies that streamline processes without cutting corners on quality.
Effective communication across all departments—from design to delivery—is essential to maintain this balance.
Teams must work collaboratively to address any challenges that arise, ensuring that quality standards are met without sacrificing the agreed-upon timeline.
Building strong relationships with suppliers is also a strategic part of balancing quality and timeliness.
Reliable suppliers provide quality materials promptly, reducing the risk of production delays and maintaining the overall quality of the product.
In conclusion, the integration of robust quality control and strategic delivery date management is essential in the production of custom-made jigs and containers for measuring instruments.
By focusing on these areas, manufacturers can deliver superior products that meet client expectations and support their operations efficiently.
資料ダウンロード
QCD管理受発注クラウド「newji」は、受発注部門で必要なQCD管理全てを備えた、現場特化型兼クラウド型の今世紀最高の受発注管理システムとなります。
ユーザー登録
受発注業務の効率化だけでなく、システムを導入することで、コスト削減や製品・資材のステータス可視化のほか、属人化していた受発注情報の共有化による内部不正防止や統制にも役立ちます。
NEWJI DX
製造業に特化したデジタルトランスフォーメーション(DX)の実現を目指す請負開発型のコンサルティングサービスです。AI、iPaaS、および先端の技術を駆使して、製造プロセスの効率化、業務効率化、チームワーク強化、コスト削減、品質向上を実現します。このサービスは、製造業の課題を深く理解し、それに対する最適なデジタルソリューションを提供することで、企業が持続的な成長とイノベーションを達成できるようサポートします。
製造業ニュース解説
製造業、主に購買・調達部門にお勤めの方々に向けた情報を配信しております。
新任の方やベテランの方、管理職を対象とした幅広いコンテンツをご用意しております。
お問い合わせ
コストダウンが利益に直結する術だと理解していても、なかなか前に進めることができない状況。そんな時は、newjiのコストダウン自動化機能で大きく利益貢献しよう!
(β版非公開)