- お役立ち記事
- The Key to Quality in Japanese Manufacturing: Understanding Random Sampling (無作為抜取り) Techniques
月間76,176名の
製造業ご担当者様が閲覧しています*
*2025年3月31日現在のGoogle Analyticsのデータより
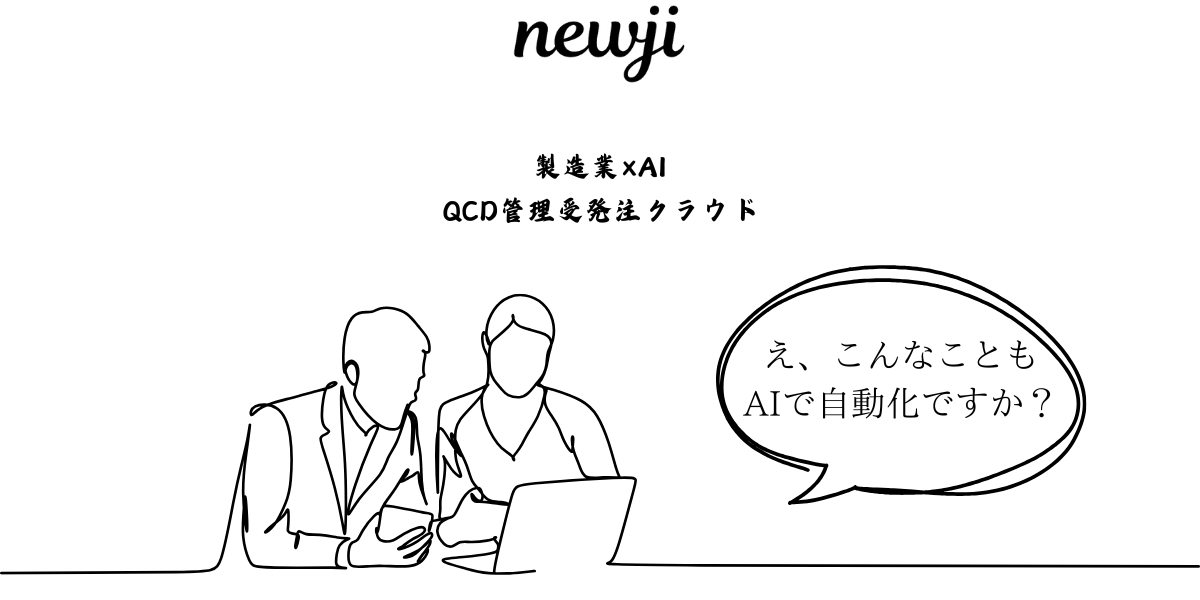
The Key to Quality in Japanese Manufacturing: Understanding Random Sampling (無作為抜取り) Techniques
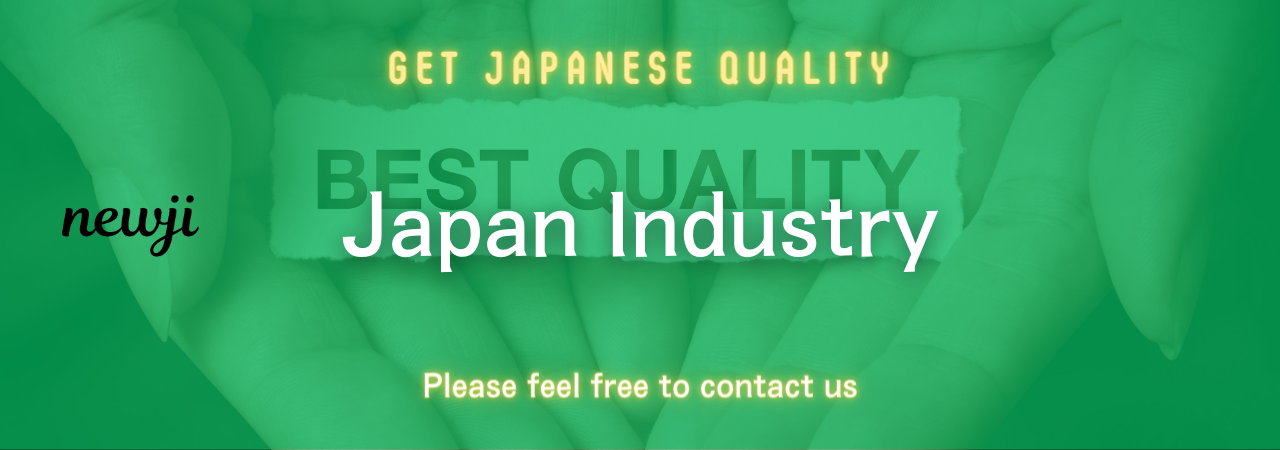
Understanding the quality of Japanese manufacturing requires diving into one of their core quality control methodologies: random sampling, or 無作為抜取り (musakui-nukidori). This method, crucial for ensuring high standards, is a cornerstone in Japanese manufacturing processes. Below, we explore its practicality, advantages, disadvantages, and its imperative role in international procurement.
目次
Introduction to Random Sampling in Japanese Manufacturing
Random sampling is a statistical method utilized in quality control to assess the quality of a batch without having to inspect each individual item. Japanese manufacturers have refined this technique over decades, aligning it with their cultural emphasis on precision and perfection.
Sampling methods in Japan have become synonymous with high quality and reliability.
Manufacturers employ it to predict how a larger batch will perform based on a smaller sample, ensuring high quality and reducing waste.
Practical Aspects of Random Sampling
Selection Criteria for Sampling
The selection of a representative sample is key in deriving meaningful insights. Japanese manufacturers utilize several criteria to determine the sample’s relevance:
– **Randomization:** Ensures that each item in the batch has an equal chance of being selected.
– **Sample Size:** Determined based on batch size, critical defect rate, and acceptable quality level (AQL).
This meticulous approach ensures that the sample accurately reflects the batch’s overall quality.
Types of Random Sampling
Several methods are standardized in Japanese manufacturing to suit different contexts:
– **Simple Random Sampling:** Each item is chosen purely by chance.
– **Systematic Sampling:** Items are selected at regular intervals.
– **Stratified Sampling:** The batch is divided into strata, and random samples are taken from each.
These diverse techniques enable manufacturers to maintain stringent quality checks efficiently.
Data Collection and Analysis
Once the sample is collected, data analysis follows. Japanese manufacturers employ advanced statistical tools and software for this purpose. This helps in:
– **Identifying Defects:** Spotting patterns and frequency of defects.
– **Predicting Performance:** Estimating the overall batch quality.
– **Making Improvements:** Data-driven changes to the production process to eliminate recurring defects.
Regular audits and continuous monitoring play a pivotal role, aligning with the Japanese principle of Kaizen (continuous improvement).
Advantages of Random Sampling in Japanese Manufacturing
High Accuracy and Reduced Bias
By eliminating biases, random sampling provides an accurate snapshot of the batch quality. This precision is crucial in maintaining Japan’s global reputation for superior manufacturing standards.
Cost-Efficiency
Inspecting a smaller, representative sample reduces the need for exhaustive and costly batch-wide inspections. This efficiency is financially beneficial without compromising on quality.
Time-Saving
Random sampling significantly reduces the time required for quality inspections, thus speeding up production timelines and delivery.
Disadvantages and Challenges
Risk of Non-representative Sampling
There is always a risk that the sample may not perfectly represent the entire batch, especially with heterogeneous products. Incorrect conclusions can affect the batch quality judgment.
Initial Setup Complexity
Setting up a robust random sampling process is complex, requiring technical expertise and advanced statistical knowledge. This initial cost and resource investment can be a barrier.
Dependency on Quality of Tools and Processes
The effectiveness of random sampling heavily relies on the quality of statistical tools and data collection methods used. Poor tools or processes can skew results and weaken the purpose of sampling.
Effective Supplier Negotiation Using Random Sampling Data
Leveraging Data in Negotiations
Data collected from random sampling provides solid grounds for negotiations with Japanese suppliers. Highlighting quality trends and defect rates can lead to discussions on improving standards or adjusting costs.
Establishing Long-term Relationships
Bringing transparent data to the table reinforces trust and reliability, key components in building strong supplier relationships. Japanese suppliers value data-backed negotiations as it aligns with their quality-centric ethos.
Benchmarking and Continuous Improvement
Consistently applying random sampling data for performance assessment establishes benchmarks. This fosters a culture of continuous improvement, keeping both buyers and suppliers aligned on quality expectations.
Market Conditions and Best Practices
Current Market Conditions
The global push for high-quality goods has led many international procurers to seek partnerships with Japanese manufacturers. Leveraging random sampling techniques enhances this pursuit by ensuring dependable quality.
Best Practices for Random Sampling
International companies dealing with Japanese suppliers can implement several best practices to optimize the benefits of random sampling:
– **Regular Training:** Continuously educating teams on statistical methods and tools improves sampling accuracy.
– **Technological Integration:** Employing advanced software for data collection and analysis streamlines the sampling process.
– **Clear Communication:** Transparent data sharing with suppliers ensures mutual understanding and facilitates collaboration.
– **Periodic Reviews:** Regularly reviewing and updating sampling techniques maintains alignment with evolving quality standards.
Conclusion
Understanding and implementing random sampling techniques is crucial when dealing with Japanese manufacturers. These methods not only assure high product quality but also offer cost-efficiency, time savings, and enhanced supplier relationships. Although challenges exist, the strategic advantages outweigh the drawbacks, making random sampling an indispensable tool in international procurement from Japan. By adhering to best practices and continuous improvement, companies can leverage the precision and reliability of Japanese manufacturing to achieve excellence in product quality.
資料ダウンロード
QCD管理受発注クラウド「newji」は、受発注部門で必要なQCD管理全てを備えた、現場特化型兼クラウド型の今世紀最高の受発注管理システムとなります。
ユーザー登録
受発注業務の効率化だけでなく、システムを導入することで、コスト削減や製品・資材のステータス可視化のほか、属人化していた受発注情報の共有化による内部不正防止や統制にも役立ちます。
NEWJI DX
製造業に特化したデジタルトランスフォーメーション(DX)の実現を目指す請負開発型のコンサルティングサービスです。AI、iPaaS、および先端の技術を駆使して、製造プロセスの効率化、業務効率化、チームワーク強化、コスト削減、品質向上を実現します。このサービスは、製造業の課題を深く理解し、それに対する最適なデジタルソリューションを提供することで、企業が持続的な成長とイノベーションを達成できるようサポートします。
製造業ニュース解説
製造業、主に購買・調達部門にお勤めの方々に向けた情報を配信しております。
新任の方やベテランの方、管理職を対象とした幅広いコンテンツをご用意しております。
お問い合わせ
コストダウンが利益に直結する術だと理解していても、なかなか前に進めることができない状況。そんな時は、newjiのコストダウン自動化機能で大きく利益貢献しよう!
(β版非公開)