- お役立ち記事
- The Latest DX in NC Machining Significantly Reduces Machining Time
The Latest DX in NC Machining Significantly Reduces Machining Time
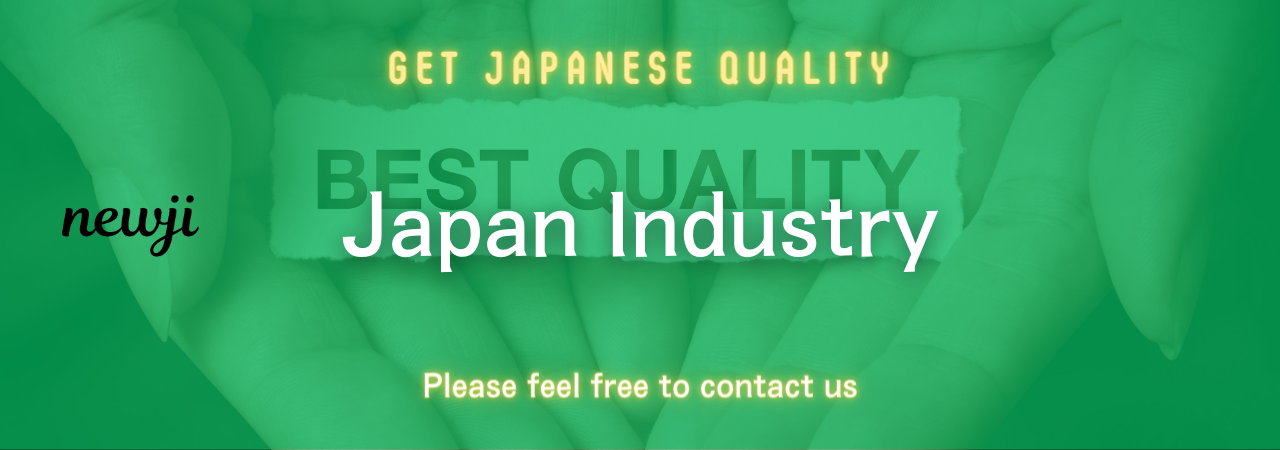
Digital transformation (DX) in CNC machining has revolutionized the manufacturing industry. By integrating advanced technologies, CNC machining now operates more efficiently, leading to reduced machining times, cost savings, and higher precision.
目次
Understanding CNC Machining
CNC, or Computer Numerical Control, machining is a manufacturing process. It uses pre-programmed software to control machining tools.
These tools can include lathes, mills, and routers. CNC machining allows for high precision and consistency. Manufacturers use this technology to make parts for various industries: automotive, aerospace, and medical.
The Role of Digital Transformation (DX)
Digital transformation (DX) involves integrating digital technology into all areas of a business.
It fundamentally changes how organizations operate and deliver value to customers. In CNC machining, DX encompasses various technologies. These include the Internet of Things (IoT), artificial intelligence (AI), and machine learning (ML).
IoT in CNC Machining
IoT connects different devices in a network. They can communicate and share data. In CNC machining, IoT sensors collect real-time information. This data includes machine performance, tool wear, and operational efficiency. This information helps in predictive maintenance. It reduces machine downtime and enhances productivity.
Artificial Intelligence and Machine Learning
AI and ML bring significant improvements to CNC machining. These technologies analyze data from machines and processes. They identify patterns and provide actionable insights. AI algorithms optimize machining parameters. This adjustment leads to reduced cycle times and improved quality. Moreover, ML models predict potential issues. Manufacturers can address these problems before they affect production.
Benefits of DX in CNC Machining
Adopting DX technologies offers several benefits. They significantly reduce machining times, leading to cost savings. Here are some key advantages:
Enhanced Precision and Quality
DX technologies improve the precision and quality of machined parts. Real-time data monitoring allows for immediate adjustments. Manufacturers can ensure consistent quality. AI algorithms fine-tune machining parameters, leading to more accurate parts.
Increased Efficiency
IoT sensors provide real-time data. This information helps optimize machine performance. Manufacturers can identify bottlenecks and streamline processes. It results in increased efficiency and reduced cycle times. AI-driven predictive maintenance minimizes unexpected downtimes.
Cost Savings
Reduced machining times translate into cost savings. Predictive maintenance reduces repair costs. DX also optimizes material usage. It minimizes waste and lowers material costs.
Case Studies: DX Enhancing CNC Machining
Several companies have successfully implemented DX in CNC machining. Here are a few examples:
Company A: Automotive Sector
Company A uses CNC machining to manufacture automotive parts. They integrated IoT sensors into their machines. These sensors monitor tool wear and machine performance. The data is analyzed using AI algorithms. The company experienced a 20% reduction in machining time. They also reported a significant improvement in part quality.
Company B: Aerospace Industry
Company B faced challenges with tool wear and machine downtime. They adopted a DX approach. IoT sensors collected real-time data on machine performance. AI algorithms analyzed this data. Predictive maintenance schedules were established. The company achieved a 30% reduction in unexpected downtimes. Their machining times were also significantly reduced.
Company C: Medical Device Manufacturing
Company C manufactures precision medical devices. They implemented machine learning models to optimize machining parameters. The AI algorithms provided real-time recommendations. The company saw a 15% improvement in precision and a 25% reduction in machining times.
Future Trends in DX and CNC Machining
The future of CNC machining looks promising with ongoing advancements in DX technologies. Some trends to watch include:
Advanced AI and ML Algorithms
AI and ML will continue to evolve. These technologies will bring more accurate predictions and recommendations. Manufacturers can expect further reductions in machining times and improvements in quality.
Edge Computing
Edge computing processes data closer to the source. It reduces latency and speeds up decision-making. In CNC machining, edge computing will enhance real-time monitoring and adjustments.
Digital Twins
Digital twins are virtual replicas of physical machines. They simulate machine behavior and performance. Manufacturers can test and optimize processes in a virtual environment. This technology will lead to more efficient CNC machining operations.
Conclusion
Digital transformation (DX) in CNC machining has brought about significant improvements. Technologies like IoT, AI, and ML have revolutionized the industry.
Manufacturers benefit from reduced machining times, cost savings, and enhanced precision.
As DX technologies continue to evolve, the future of CNC machining looks incredibly promising.
Embracing these advancements will be crucial for staying competitive in the ever-evolving manufacturing landscape.
資料ダウンロード
QCD調達購買管理クラウド「newji」は、調達購買部門で必要なQCD管理全てを備えた、現場特化型兼クラウド型の今世紀最高の購買管理システムとなります。
ユーザー登録
調達購買業務の効率化だけでなく、システムを導入することで、コスト削減や製品・資材のステータス可視化のほか、属人化していた購買情報の共有化による内部不正防止や統制にも役立ちます。
NEWJI DX
製造業に特化したデジタルトランスフォーメーション(DX)の実現を目指す請負開発型のコンサルティングサービスです。AI、iPaaS、および先端の技術を駆使して、製造プロセスの効率化、業務効率化、チームワーク強化、コスト削減、品質向上を実現します。このサービスは、製造業の課題を深く理解し、それに対する最適なデジタルソリューションを提供することで、企業が持続的な成長とイノベーションを達成できるようサポートします。
オンライン講座
製造業、主に購買・調達部門にお勤めの方々に向けた情報を配信しております。
新任の方やベテランの方、管理職を対象とした幅広いコンテンツをご用意しております。
お問い合わせ
コストダウンが利益に直結する術だと理解していても、なかなか前に進めることができない状況。そんな時は、newjiのコストダウン自動化機能で大きく利益貢献しよう!
(Β版非公開)