- お役立ち記事
- The latest method for raw material price fluctuation risk management recommended by purchasing departments
月間76,176名の
製造業ご担当者様が閲覧しています*
*2025年3月31日現在のGoogle Analyticsのデータより
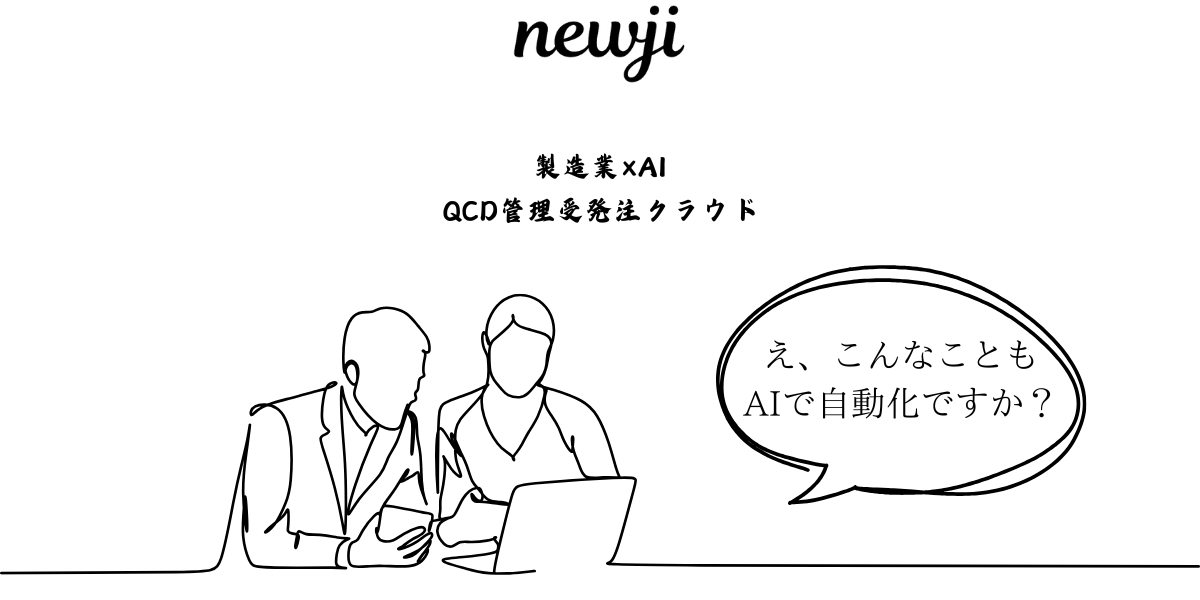
The latest method for raw material price fluctuation risk management recommended by purchasing departments
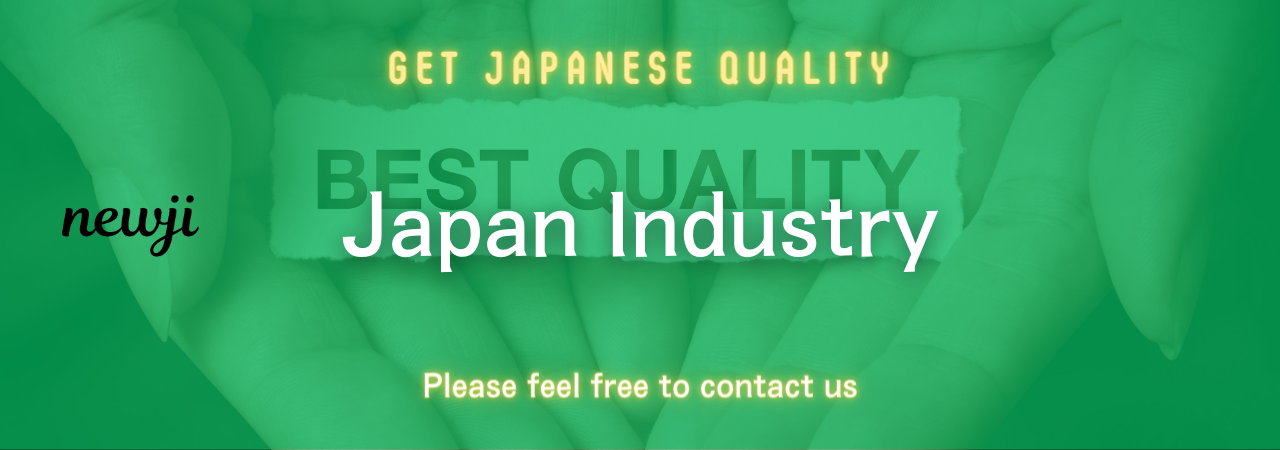
目次
Understanding Raw Material Price Fluctuation
Raw material prices are constantly on the move, influenced by various global and local factors.
These fluctuations can create significant challenges for purchasing departments, which need stable cost predictions to maintain profitability and operational efficiency.
Understanding the root causes of price changes is the first step in managing these fluctuations effectively.
Several factors drive raw material price changes.
Economic conditions, such as inflation or recession, can alter supply and demand dynamics.
Additionally, geopolitical tensions can cause sudden shifts in availability or pricing.
Currency exchange rates also play a crucial role, particularly for companies sourcing materials internationally.
The Importance of Strategic Risk Management
Effective risk management is essential for purchasing departments dealing with raw material price fluctuations.
Without a solid strategy, companies face increased production costs, compressed profit margins, and potentially, a loss of competitive advantage.
Thus, crafting a comprehensive risk management plan should be a priority.
Risk management strategies should be both proactive and reactive.
A proactive approach involves anticipating potential price changes and implementing measures before they occur.
Reactive strategies involve having a plan ready to mitigate adverse impacts when price changes happen.
Data Analytics: The Modern Solution
One of the latest and most powerful tools in managing raw material price fluctuations is data analytics.
By harnessing the power of big data, purchasing departments can gain valuable insights into market trends and potential price changes.
Data analytics can predict shifts in commodity prices by analyzing historical data, market trends, and various influencing factors.
This predictive ability allows purchasing departments to make informed decisions about when to buy, how much to stock, and at what price.
Moreover, machine learning algorithms can process vast amounts of data quickly, identifying patterns and correlations that humans might miss.
This technological advancement offers a significant advantage in staying ahead of market trends.
Hedging as a Risk Management Tool
Hedging is another effective method for managing raw material price fluctuation risks.
It involves the use of financial instruments to offset potential losses from price changes.
Futures contracts are a popular hedging method, allowing companies to lock in prices for raw materials at a future date.
By doing so, firms can secure a stable cost base, protecting themselves from adverse price movements.
Options contracts provide another hedging avenue.
They offer the right, but not the obligation, to purchase materials at a set price, providing flexibility in volatile markets.
Both futures and options require a thorough understanding and careful planning to ensure they align with the company’s operational needs and financial goals.
Building Strong Supplier Relationships
Managing raw material price fluctuations isn’t only about financial strategies.
Strong relationships with suppliers also play a crucial role.
By building and maintaining good relations with suppliers, companies can negotiate more favorable terms and secure better pricing.
Suppliers may offer volume discounts, extended payment terms, or early alerts for upcoming price changes.
Collaborative partnerships with suppliers can lead to better communication and more flexible arrangements, significantly mitigating the risk of price volatility.
Developing Internal Capabilities
Another essential component of effective risk management is developing internal capabilities to react quickly to potential price changes.
This development involves training staff to understand market dynamics, investing in technology tools for analysis, and establishing clear procedures for decision-making.
With a skilled team and robust processes, companies can respond swiftly to market changes, minimizing potential disruptions.
Continuous Monitoring and Adjustment
Risk management is not a one-off activity but requires continuous monitoring and adjustment.
Markets and economic conditions are dynamic, so strategies that work today might need recalibration tomorrow.
Regularly reviewing market data, adjusting forecasts, and revisiting hedging strategies keep a company agile and responsive.
Staying informed about new methods and tools in risk management also provides a competitive edge.
Conclusion
Managing raw material price fluctuation is a complex but essential task for purchasing departments.
By leveraging data analytics, employing hedging tactics, forging strong supplier relationships, and continuously monitoring the market, companies can effectively mitigate risks associated with price volatility.
These strategies not only protect against adverse cost impacts but also enhance a company’s ability to remain competitive and profitable in an ever-changing market landscape.
Adapting to these modern methods ensures that purchasing departments are well-prepared to face the challenges of today’s global economy.
資料ダウンロード
QCD管理受発注クラウド「newji」は、受発注部門で必要なQCD管理全てを備えた、現場特化型兼クラウド型の今世紀最高の受発注管理システムとなります。
ユーザー登録
受発注業務の効率化だけでなく、システムを導入することで、コスト削減や製品・資材のステータス可視化のほか、属人化していた受発注情報の共有化による内部不正防止や統制にも役立ちます。
NEWJI DX
製造業に特化したデジタルトランスフォーメーション(DX)の実現を目指す請負開発型のコンサルティングサービスです。AI、iPaaS、および先端の技術を駆使して、製造プロセスの効率化、業務効率化、チームワーク強化、コスト削減、品質向上を実現します。このサービスは、製造業の課題を深く理解し、それに対する最適なデジタルソリューションを提供することで、企業が持続的な成長とイノベーションを達成できるようサポートします。
製造業ニュース解説
製造業、主に購買・調達部門にお勤めの方々に向けた情報を配信しております。
新任の方やベテランの方、管理職を対象とした幅広いコンテンツをご用意しております。
お問い合わせ
コストダウンが利益に直結する術だと理解していても、なかなか前に進めることができない状況。そんな時は、newjiのコストダウン自動化機能で大きく利益貢献しよう!
(β版非公開)