- お役立ち記事
- The latest technology to optimize production line design and the key to successful implementation
月間76,176名の
製造業ご担当者様が閲覧しています*
*2025年3月31日現在のGoogle Analyticsのデータより
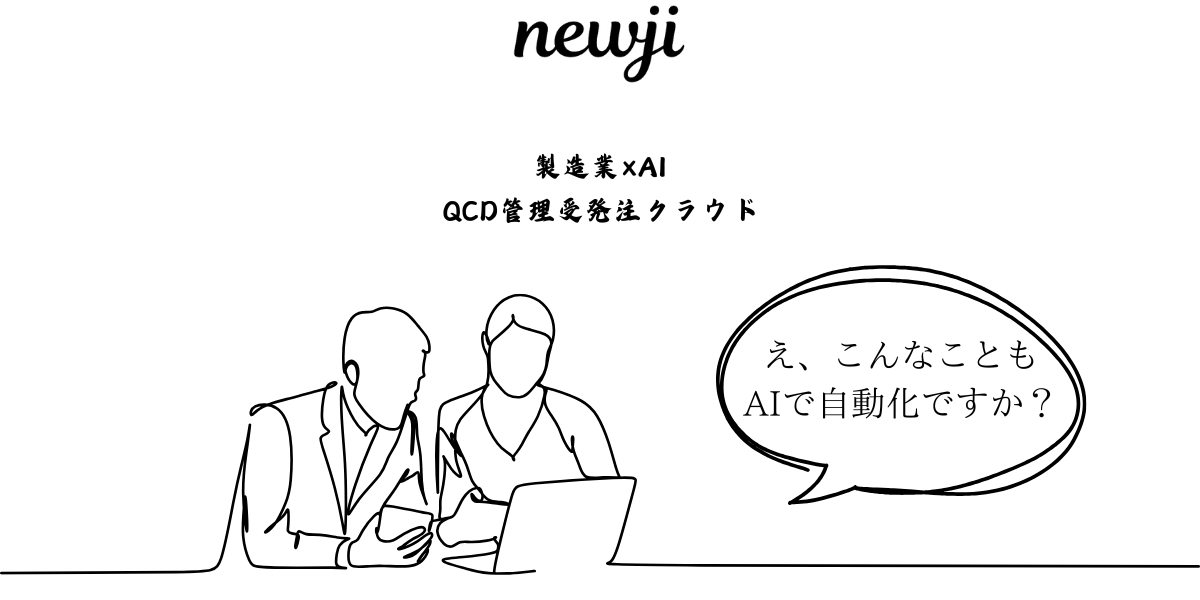
The latest technology to optimize production line design and the key to successful implementation
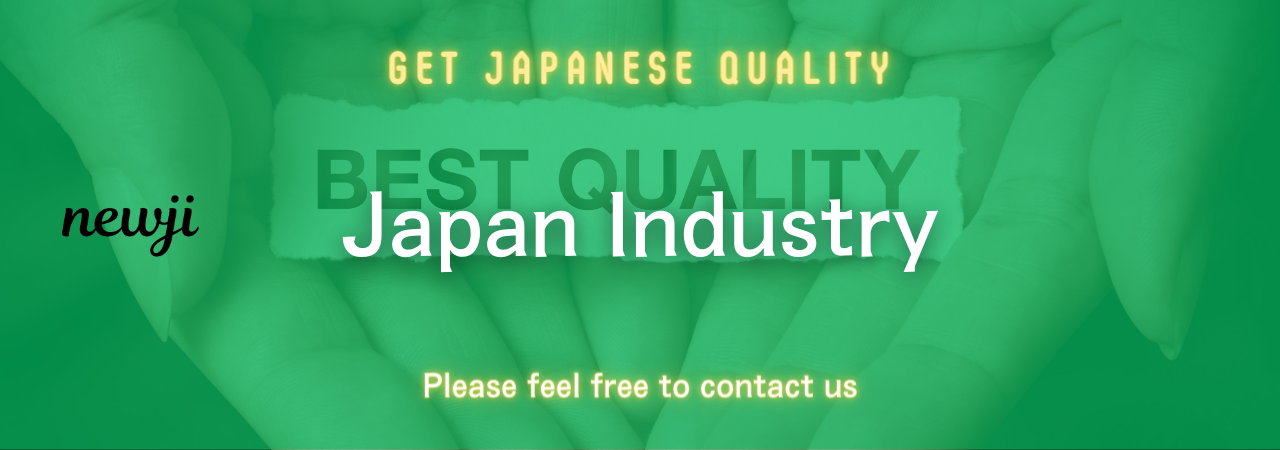
目次
Understanding Production Line Optimization
Optimizing a production line is a vital part of manufacturing that aims to improve efficiency, reduce costs, and boost overall productivity.
With the advancement of technology, the methods and tools used for production line optimization have evolved significantly, offering innovative solutions that can transform the way production lines are designed and implemented.
The Role of Technology in Production Line Design
Modern technology plays a crucial role in the design and execution of efficient production lines.
Digital tools and software have made it possible to simulate production processes before they even begin, enabling engineers to tweak and test different scenarios without the cost or disruption of physical trials.
Computer-aided design (CAD) systems are widely used for creating detailed 2D or 3D models of production lines.
These models help in visualizing the layout, identifying potential bottlenecks, and planning the sequence of operations.
By using CAD, manufacturers can optimize the use of space, labor, and resources, leading to higher efficiency and cost savings.
Additionally, software solutions for production line planning and scheduling are now equipped with artificial intelligence (AI) capabilities.
AI can analyze vast amounts of data to forecast demand, predict maintenance needs, and optimize production schedules.
This leads to minimized wait times, reduced waste, and improved throughput.
Internet of Things (IoT) Integration
The Internet of Things (IoT) is transforming production lines by connecting equipment and machinery to the Internet, enabling real-time data collection and analysis.
Sensors placed throughout the production line can monitor the status of machines, track inventory levels, and ensure quality control.
IoT devices offer predictive maintenance capabilities by providing insights into equipment health.
This allows technicians to perform maintenance tasks before machinery breaks down, thus avoiding unexpected downtime and expensive repair costs.
Moreover, IoT can improve efficiency by automating the adjustment of machinery settings in response to data inputs, which optimizes energy usage and reduces waste.
Automation and Robotics
Automation and robotics are integral to modern production line optimization strategies.
Automating repetitive tasks, such as assembly or packaging, can significantly increase production speed and consistency while reducing the chance for human error.
Robots are often used in environments that are too dangerous or complex for humans, enhancing safety and efficiency.
Moreover, collaborative robots—often known as cobots—are designed to work alongside humans, learning tasks quickly and enhancing productivity without the need for extensive reconfiguration of the production line.
Automated guided vehicles (AGVs) and drones are being used to transport raw materials and products within production facilities, streamlining logistic operations and reducing manual handling errors.
Data Analytics
Data analytics is a powerful tool for optimizing production lines.
By collecting data from various parts of the manufacturing process, companies can gain valuable insights into production performance, identify bottlenecks, and uncover areas for improvement.
Advanced analytics can track key performance indicators (KPIs) such as throughput rates, machine utilization, and cycle times.
With these insights, manufacturers can make data-driven decisions to adjust processes, improve productivity, and reduce operational costs.
Furthermore, integrating data analytics with machine learning models can enable the adaptation of production processes in real-time, ensuring a constant alignment with market demand and production capabilities.
Key Steps to Implement Successful Production Line Optimization
Assess Current Processes
Before implementing new technologies, it’s crucial to assess the existing production line.
Conduct a thorough analysis of the current processes to identify inefficiencies and areas that require improvement.
Engage with employees who work on the production line to gain insights into daily operational challenges.
Their feedback is invaluable in understanding practical issues that may not be immediately visible through data alone.
Define Objectives and Goals
Clearly define the objectives and goals of the production line optimization project.
Whether it’s reducing production time, lowering costs, improving quality, or increasing output, having clear goals will guide the decision-making process and measure the success of the optimization efforts.
Choose the Right Technologies
Evaluate and select the right technologies that align with your project’s goals and objectives.
Consider the scalability, compatibility, and return on investment (ROI) of each technology.
It’s important to choose solutions that can grow with your business and seamlessly integrate with existing systems.
Train and Engage Staff
Successful implementation relies heavily on the workforce’s ability to adapt to new technologies and processes.
Invest in comprehensive training programs to equip employees with the necessary skills to operate and maintain new systems.
Engaging staff throughout the implementation process fosters a culture of teamwork and innovation, ensuring that everyone is aligned with the project’s goals.
Monitor, Evaluate, and Adapt
Once the new technologies and processes are in place, continuously monitor the production line for performance metrics.
Use data analytics to evaluate the effectiveness of the optimization strategies and make necessary adjustments.
Being flexible and responsive to the data-driven insights ensures optimal performance and continuous improvement.
Conclusion
The latest technologies for optimizing production line design offer unprecedented opportunities for manufacturers to enhance efficiency and productivity.
By understanding and leveraging these technologies, companies can remain competitive in an ever-evolving market.
Successful implementation requires a well-thought-out approach, including assessing current processes, setting clear objectives, selecting appropriate technologies, training staff, and continuously evaluating results.
As technology continues to evolve, it’s essential for manufacturers to stay informed and adopt innovative solutions that drive operational excellence and business growth.
資料ダウンロード
QCD管理受発注クラウド「newji」は、受発注部門で必要なQCD管理全てを備えた、現場特化型兼クラウド型の今世紀最高の受発注管理システムとなります。
ユーザー登録
受発注業務の効率化だけでなく、システムを導入することで、コスト削減や製品・資材のステータス可視化のほか、属人化していた受発注情報の共有化による内部不正防止や統制にも役立ちます。
NEWJI DX
製造業に特化したデジタルトランスフォーメーション(DX)の実現を目指す請負開発型のコンサルティングサービスです。AI、iPaaS、および先端の技術を駆使して、製造プロセスの効率化、業務効率化、チームワーク強化、コスト削減、品質向上を実現します。このサービスは、製造業の課題を深く理解し、それに対する最適なデジタルソリューションを提供することで、企業が持続的な成長とイノベーションを達成できるようサポートします。
製造業ニュース解説
製造業、主に購買・調達部門にお勤めの方々に向けた情報を配信しております。
新任の方やベテランの方、管理職を対象とした幅広いコンテンツをご用意しております。
お問い合わせ
コストダウンが利益に直結する術だと理解していても、なかなか前に進めることができない状況。そんな時は、newjiのコストダウン自動化機能で大きく利益貢献しよう!
(β版非公開)