- お役立ち記事
- The Manufacturing Process for Coolers and Improving Cooling Technology
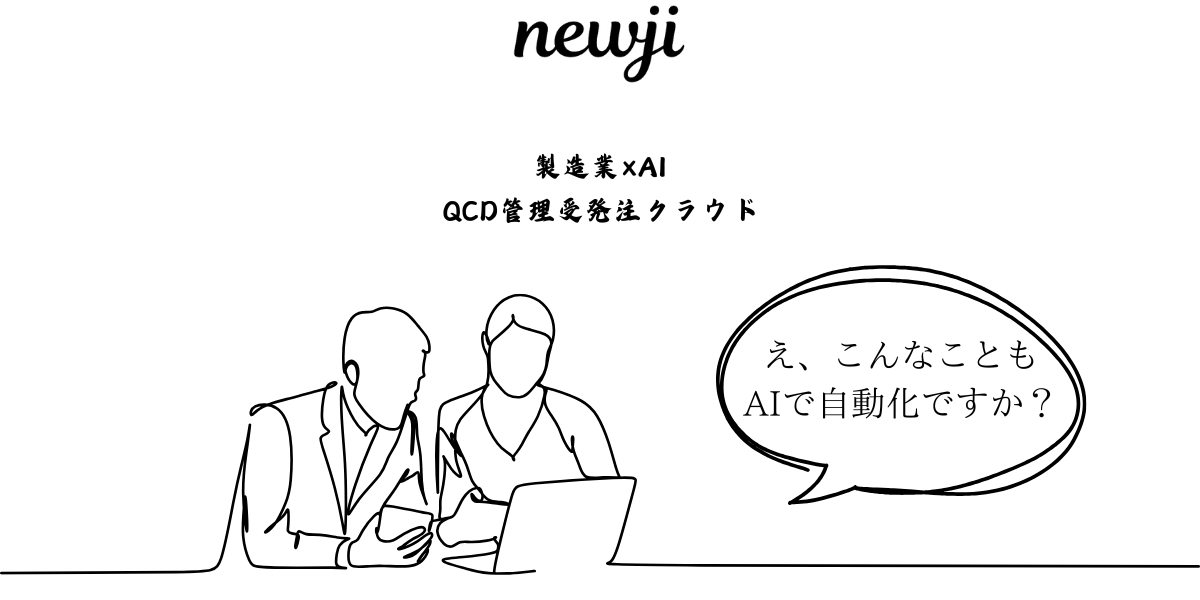
The Manufacturing Process for Coolers and Improving Cooling Technology
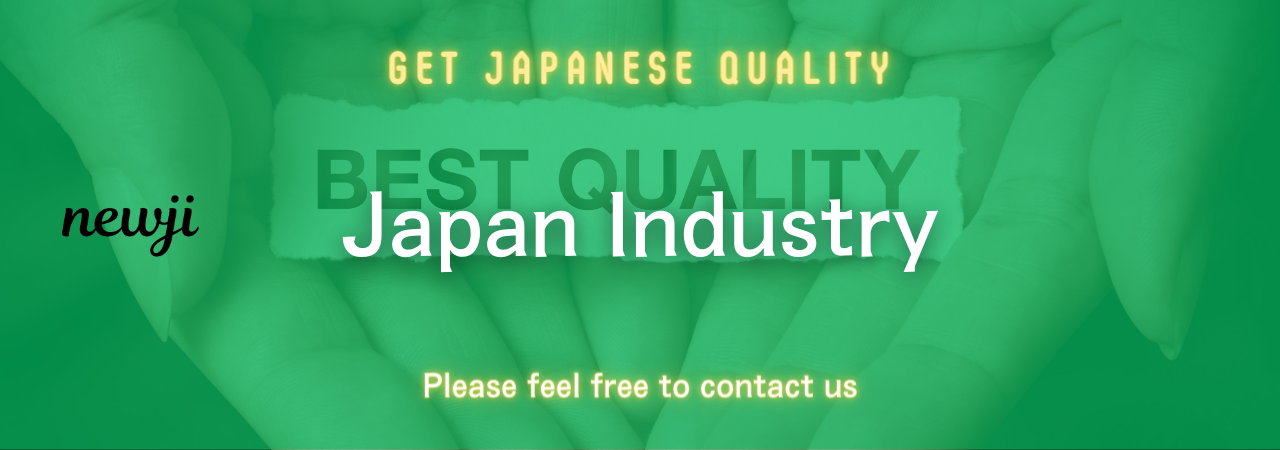
Coolers are essential items that help us keep our drinks and food fresh, especially during outdoor activities like picnics and camping.
But have you ever wondered how these handy devices are made?
In this article, we will explore the manufacturing process for coolers and discuss advancements in cooling technology.
目次
The Basics of Cooler Manufacturing
Coolers are designed to help keep contents cold using insulation and often ice packs or refrigerated blocks.
The manufacturing process involves multiple steps, from material selection to final assembly.
Each step is crucial for ensuring the longevity and efficiency of the cooler.
Material Selection
The first step in manufacturing a cooler is choosing the appropriate materials.
High-quality coolers are often made from plastic, metal, or a combination of both.
Plastic coolers tend to be lightweight, durable, and resistant to rust.
Metal coolers are typically more robust but heavier.
The interior of most coolers is made from a layer of insulation, generally polyurethane foam or expanded polystyrene (EPS).
Molding the Exterior
Once the materials are chosen, the exterior shell of the cooler is created using a process called blow molding or injection molding.
Blow molding involves inflating a heated plastic tube until it forms the shape of the cooler.
In contrast, injection molding involves injecting molten plastic into a mold to create the desired shape.
Both methods result in a strong, durable shell.
Insulating the Cooler
Insulation is critical in the manufacturing process because it determines how effectively the cooler can maintain its internal temperature.
After the exterior shell is molded, insulation material is added.
Most commonly, manufacturers use polyurethane foam because it has excellent insulating properties.
The foam is injected between the walls of the cooler and allowed to expand, filling up the gaps and ensuring uniform insulation.
This process not only boosts the cooler’s efficiency but also adds structural strength.
Sealing and Assembly
Once the insulation is in place, the next step is sealing the cooler.
A rubber gasket or silicone seal is installed around the lid to ensure an airtight seal when the cooler is closed.
This prevents warm air from entering and cold air from escaping.
After sealing, additional components such as handles, hinges, and lids are attached.
These parts are usually screwed or riveted into place, ensuring they can withstand the wear and tear of frequent use.
Quality Control and Testing
Manufacturers place a significant emphasis on quality control during the cooler production process to ensure each unit meets rigorous standards.
Coolers are subjected to various tests to check for strength, insulation efficiency, and durability.
Tests may include dropping the cooler from a certain height to ensure it can withstand impact and placing it in extreme conditions to assess performance.
Performance Testing
One critical aspect of quality control is performance testing.
Coolers are often tested by filling them with a specific amount of ice and monitoring how long it retains the ice before it melts.
Higher-end coolers may undergo even more rigorous testing, such as being exposed to direct sunlight for extended periods.
This helps manufacturers gauge the effectiveness of the insulation and the overall build quality.
Advancements in Cooling Technology
As technology advances, so do the methods and materials used to create coolers.
Modern coolers incorporate cutting-edge technologies to improve their efficiency and convenience.
Rotomolded Coolers
One of the most significant advancements in cooler manufacturing is the introduction of rotomolded coolers.
These coolers are made using a rotational molding process, where plastic is heated and rotated inside a mold.
This method creates a seamless, single-piece construction, making the cooler more durable and less prone to leaks.
Rotomolded coolers are known for their superior insulation capabilities and can keep ice for extended periods.
Thermoelectric Coolers
Thermoelectric coolers represent another leap in cooling technology.
Unlike traditional coolers that require ice, thermoelectric coolers use electricity to transfer heat from the interior to the exterior.
They operate on the Peltier effect, which creates a temperature difference by passing an electric current through two different types of conductors.
Thermoelectric coolers are perfect for long trips and areas where ice is not readily available, although they usually require a power source.
Smart Coolers
The rise of smart technology has also made its way into the world of coolers.
Smart coolers come equipped with features like built-in Bluetooth speakers, LED lights, and even USB ports for charging devices.
Some models offer integrated wheels and telescoping handles for easy transportation.
These added features enhance the convenience and versatility of the cooler, making it more than just a device to keep items cold.
Conclusion
Understanding the manufacturing process for coolers and advancements in cooling technology highlights the innovation and effort that goes into creating these essential items.
From material selection to the latest smart features, the modern cooler is a testament to engineering and design.
So the next time you enjoy a cold drink from your cooler, remember the extensive process that made it possible!
資料ダウンロード
QCD調達購買管理クラウド「newji」は、調達購買部門で必要なQCD管理全てを備えた、現場特化型兼クラウド型の今世紀最高の購買管理システムとなります。
ユーザー登録
調達購買業務の効率化だけでなく、システムを導入することで、コスト削減や製品・資材のステータス可視化のほか、属人化していた購買情報の共有化による内部不正防止や統制にも役立ちます。
NEWJI DX
製造業に特化したデジタルトランスフォーメーション(DX)の実現を目指す請負開発型のコンサルティングサービスです。AI、iPaaS、および先端の技術を駆使して、製造プロセスの効率化、業務効率化、チームワーク強化、コスト削減、品質向上を実現します。このサービスは、製造業の課題を深く理解し、それに対する最適なデジタルソリューションを提供することで、企業が持続的な成長とイノベーションを達成できるようサポートします。
オンライン講座
製造業、主に購買・調達部門にお勤めの方々に向けた情報を配信しております。
新任の方やベテランの方、管理職を対象とした幅広いコンテンツをご用意しております。
お問い合わせ
コストダウンが利益に直結する術だと理解していても、なかなか前に進めることができない状況。そんな時は、newjiのコストダウン自動化機能で大きく利益貢献しよう!
(Β版非公開)