- お役立ち記事
- The Manufacturing Process for Welding Machines and Enhancing Electrical Efficiency
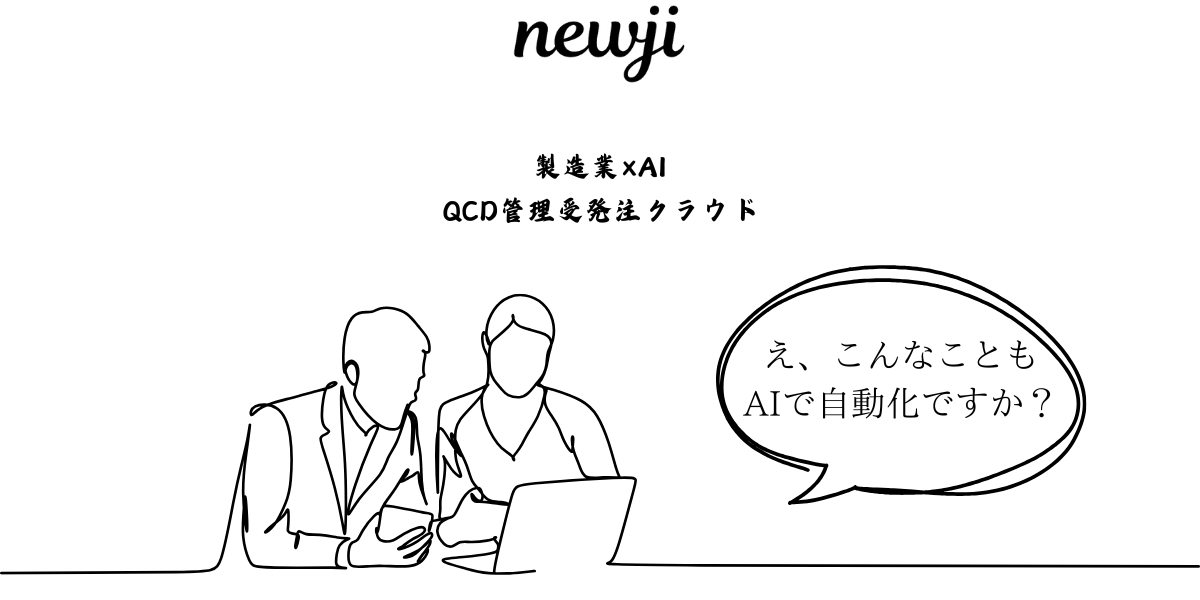
The Manufacturing Process for Welding Machines and Enhancing Electrical Efficiency
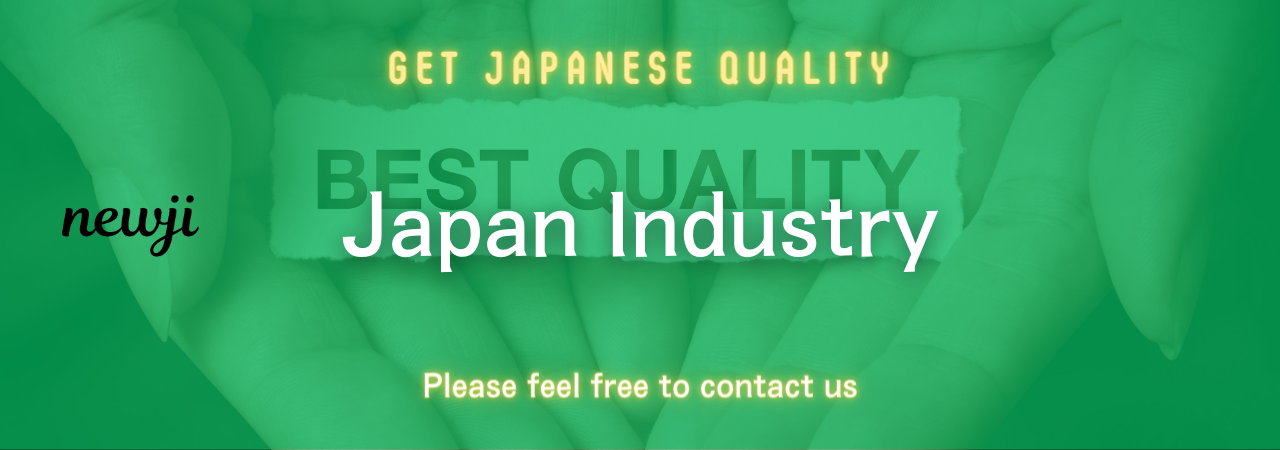
Welding machines are vital tools in manufacturing industries, playing a crucial role in binding materials together through the application of heat.
They are extensively utilized in construction, automotive industries, shipbuilding, and various other fields.
Let’s delve into the manufacturing process of welding machines and how enhancing electrical efficiency can significantly benefit users.
目次
The Basics of Welding Machines
Welding machines work by generating intense heat sufficient to melt metal parts, which are then fused upon cooling.
Different types of welding machines cater to varying needs, including MIG (Metal Inert Gas) welders, TIG (Tungsten Inert Gas) welders, and stick welders.
Each type serves a unique purpose and requires specific components to function effectively.
Primary Components of Welding Machines
Before discussing the manufacturing process, it is essential to understand the primary components of welding machines:
1. **Power Source:** The core element that provides the electric current necessary for welding.
2. **Electrode:** Conducts the electric current and melts to form the weld joint.
3. **Cooling System:** Prevents the machine from overheating during operation.
4. **Control System:** Allows the user to adjust the voltage and current settings.
5. **Wire Feed System:** Automatically feeds the welding wire into the weld pool in some types of welders.
These components play critical roles, and their quality and precision substantially impact the machine’s efficiency and effectiveness.
The Manufacturing Process of Welding Machines
The manufacturing of welding machines involves several key steps, each requiring meticulous attention to detail to ensure the final product is both efficient and reliable.
1. Designing and Engineering
The first step in manufacturing a welding machine is the design and engineering phase.
Engineers use computer-aided design (CAD) software to create detailed schematics and blueprints of the welding machine.
This phase includes determining the machine’s specifications, including voltage and current requirements, physical dimensions, and other technical parameters.
2. Procuring Raw Materials
Once the design is finalized, the next step involves procuring raw materials.
High-quality metals, alloys, and electronic components are sourced from reputable suppliers.
The selection of raw materials is critical, as it affects the machine’s durability and performance.
3. Fabrication of Core Components
In this phase, the core components, such as the power source, electrode holder, and cooling system, are fabricated.
Modern welding machine manufacturers often employ CNC (Computer Numerical Control) machinery and robotic systems to ensure precision and consistency.
Machining, cutting, and assembling the parts with high accuracy is essential to guarantee optimal performance.
4. Assembly Line Process
Following the fabrication of individual components, the assembly process begins.
Technicians and assembly line workers carefully put together the different parts, ensuring they fit accurately according to the design specifications.
Quality control checks are conducted at every stage of assembly to identify and rectify any defects.
5. Electrical Wiring and Integration
One of the most intricate phases of the manufacturing process is electrical wiring and integration.
Specialized technicians connect the internal wiring, control panels, and various sensors.
Proper insulation and secure connections are crucial to prevent short circuits and ensure user safety.
6. Testing and Quality Assurance
Once assembled, the welding machines undergo rigorous testing to ensure they meet industry standards and performance criteria.
The machines are tested under various conditions, including different voltage and current settings, to verify their reliability and efficiency.
Quality assurance teams conduct thorough inspections to detect any deviations from specifications and make the necessary adjustments.
7. Packaging and Distribution
After passing all quality checks, the welding machines receive protective packaging to safeguard against damage during transportation.
The machines are then shipped to distributors, retailers, and end-users.
Enhancing Electrical Efficiency in Welding Machines
Enhancing electrical efficiency in welding machines is beneficial for reducing operational costs, minimizing energy consumption, and extending the machine’s lifespan.
Here are some strategies to improve electrical efficiency:
1. Utilizing Inverter Technology
Traditional welding machines typically use transformer-based power sources, which can be bulky and less efficient in energy conversion.
In contrast, modern welding machines increasingly utilize inverter technology, which converts power more efficiently, reduces weight, and improves overall performance.
2. Implementing Energy-Saving Modes
Many contemporary welding machines come equipped with energy-saving modes that automatically adjust power usage based on the welding requirements.
These modes help reduce idle power consumption, thereby saving energy and lowering electricity bills.
3. Regular Maintenance
Regular maintenance of welding machines is critical for maintaining electrical efficiency.
This includes checking and replacing worn-out components, cleaning internal parts, and ensuring proper cooling system function.
Keeping the machine in optimal operating condition prevents energy wastage and prolongs its service life.
4. Using High-Quality Consumables
Using high-quality electrodes and other consumables can enhance the welding process’s efficiency.
Inferior consumables may lead to increased resistance and energy loss.
Investing in better-quality materials ensures smoother and more efficient welding operations.
5. Training and Skill Development
Proper training for operators can also play a significant role in enhancing electrical efficiency.
Skilled operators proficient in handling welding machines can optimize performance settings, reducing unnecessary energy usage and improving welding quality.
Conclusion
The process of manufacturing welding machines is intricate and demands high precision at every stage to ensure quality and reliability.
Understanding the primary components and manufacturing phases offers insight into the sophistication involved in creating these essential tools.
Furthermore, by implementing strategies to enhance electrical efficiency, users can significantly reduce operational costs, extend the lifespan of the machines, and contribute to energy conservation.
The continuous advancements in welding technology promise even greater efficiency and innovation in the future, benefiting industries worldwide.
資料ダウンロード
QCD調達購買管理クラウド「newji」は、調達購買部門で必要なQCD管理全てを備えた、現場特化型兼クラウド型の今世紀最高の購買管理システムとなります。
ユーザー登録
調達購買業務の効率化だけでなく、システムを導入することで、コスト削減や製品・資材のステータス可視化のほか、属人化していた購買情報の共有化による内部不正防止や統制にも役立ちます。
NEWJI DX
製造業に特化したデジタルトランスフォーメーション(DX)の実現を目指す請負開発型のコンサルティングサービスです。AI、iPaaS、および先端の技術を駆使して、製造プロセスの効率化、業務効率化、チームワーク強化、コスト削減、品質向上を実現します。このサービスは、製造業の課題を深く理解し、それに対する最適なデジタルソリューションを提供することで、企業が持続的な成長とイノベーションを達成できるようサポートします。
オンライン講座
製造業、主に購買・調達部門にお勤めの方々に向けた情報を配信しております。
新任の方やベテランの方、管理職を対象とした幅広いコンテンツをご用意しております。
お問い合わせ
コストダウンが利益に直結する術だと理解していても、なかなか前に進めることができない状況。そんな時は、newjiのコストダウン自動化機能で大きく利益貢献しよう!
(Β版非公開)