- お役立ち記事
- The Manufacturing Process for Welding Masks and Improving Visibility
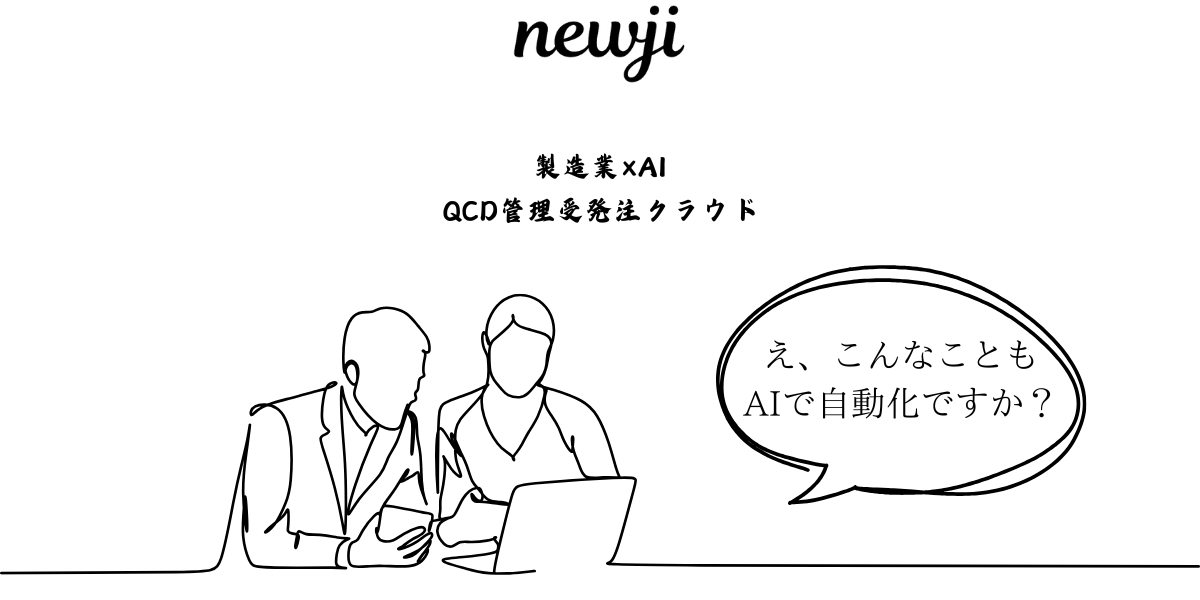
The Manufacturing Process for Welding Masks and Improving Visibility
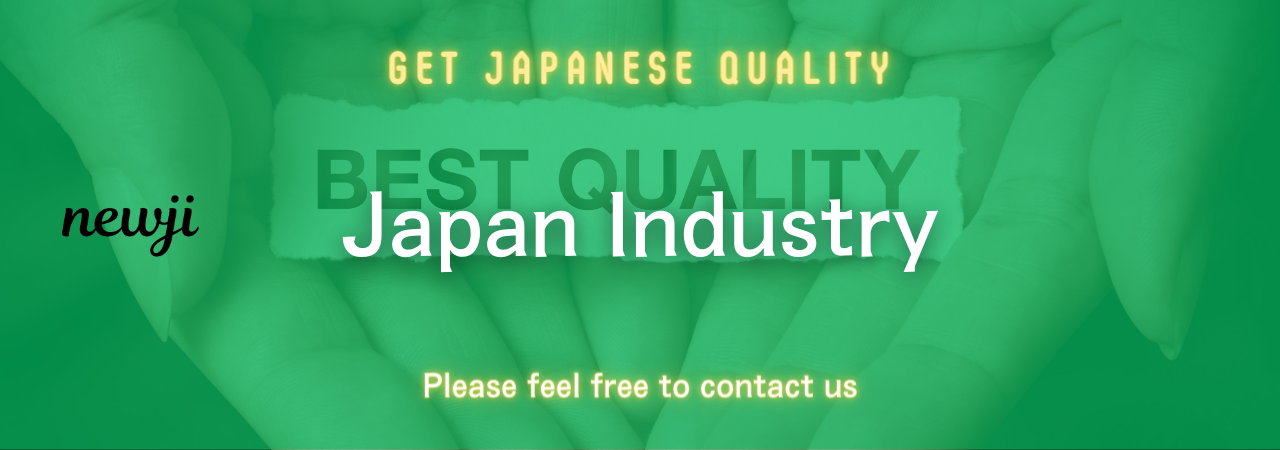
Welding masks are essential safety tools for professionals who work with welding equipment.
They protect the eyes and face from harmful sparks, intense light, and hazardous fumes.
In this article, we will examine the manufacturing process of welding masks and discuss methods to improve visibility while using them.
目次
Understanding Welding Masks
Welding masks, also known as welding helmets, are personal protective equipment designed to shield welders’ faces and eyes.
They come in various designs and are equipped with features such as auto-darkening lenses, adjustable headbands, and different shade options.
The primary function of a welding mask is to protect the eyes from the intense light produced during the welding process, which can cause severe eye damage, including “welder’s flash” or photokeratitis.
Raw Materials Used in Manufacturing
The manufacturing process of welding masks begins with selecting the appropriate raw materials.
The main components include:
Shell Material
The outer shell of the welding mask is typically made from thermoplastic or fiberglass.
Thermoplastic is lightweight, heat-resistant, and durable, making it an ideal choice for welding helmets.
Fiberglass offers additional strength and is often used in heavy-duty welding applications.
Lens Material
The lens or filter of the welding mask is made from polycarbonate or other high-impact-resistant materials.
Auto-darkening lenses have liquid crystal displays (LCDs) that adjust the shade level in response to the light intensity.
Headband Material
The headband is usually made from adjustable nylon or polyester straps to ensure a secure and comfortable fit.
Manufacturing Process
The production of welding masks involves several steps, from designing to final assembly.
Design and Prototyping
The first step in the manufacturing process is designing the welding mask.
Engineers and designers use computer-aided design (CAD) software to create detailed models of the mask.
These designs are then used to produce prototypes, which are tested for functionality, comfort, and safety.
Adjustments are made based on feedback, and the final design is approved for production.
Molding and Shaping the Shell
Once the design is finalized, the shell of the welding mask is manufactured using injection molding for thermoplastic materials or a layering process for fiberglass materials.
In injection molding, heated thermoplastic is injected into molds to form the shape of the mask.
For fiberglass shells, layers of fiberglass cloth are impregnated with resin and molded into shape.
These shells are then cured, providing strength and durability.
Production of the Lens
The lens is a critical component of the welding mask, and its production involves several steps.
For auto-darkening lenses, multiple layers of polarized and colored films are laminated together with liquid crystal cells sandwiched between them.
These layers are then encased in polycarbonate for protection and durability.
Assembling Components
Once all the individual components are produced, they are assembled to create the final welding mask.
The lens is securely mounted onto the shell, and the headband is attached.
Additional features such as padding, adjustment knobs, and vents are added to enhance comfort and usability.
Quality Control and Testing
Quality control is a crucial part of the manufacturing process.
Each welding mask undergoes rigorous testing to ensure it meets industry standards and safety regulations.
Tests include impact resistance, light transmission, and auto-darkening response time.
Masks that pass these tests are approved for distribution, while those that do not are sent back for adjustments.
Improving Visibility in Welding Masks
Visibility is a critical concern for welders, as it directly impacts the quality of their work and their safety.
Several methods can be employed to improve visibility in welding masks.
Auto-Darkening Filters
One of the most effective ways to enhance visibility is by using auto-darkening filters (ADF).
These lenses automatically adjust their shade level based on the intensity of the welding arc, providing optimal vision at all times.
Welders no longer need to flip their masks up and down, saving time and reducing strain on the neck.
Adjustable Sensitivity and Delay Settings
Many modern welding masks come with adjustable sensitivity and delay settings.
Sensitivity controls how quickly the mask darkens in response to the arc, while delay settings determine how long the lens stays dark after the arc stops.
These features allow welders to customize their masks based on their specific needs and work environment, improving overall visibility.
Clear Light Technology
Innovations such as clear light technology offer enhanced color clarity and contrast, allowing welders to see more clearly while working.
This technology improves visibility by providing a more natural and accurate view of the workspace, reducing eye strain and improving weld quality.
Anti-Fog and Anti-Scratch Coatings
To maintain clear visibility, it’s essential to keep the lens free from fog and scratches.
Anti-fog coatings prevent condensation from forming on the inside of the lens, while anti-scratch coatings protect the lens from damage over time.
These coatings extend the lifespan of the lens and ensure optimal visibility during welding tasks.
Conclusion
The manufacturing process of welding masks involves careful selection of materials, precise engineering, and rigorous testing to ensure safety and functionality.
By incorporating advanced technologies such as auto-darkening filters and clear light technology, manufacturers can significantly improve visibility for welders.
Whether you’re a professional welder or a hobbyist, using a high-quality welding mask is crucial for protecting your eyes and achieving the best welding results.
Stay safe and invest in a reliable welding mask that meets your needs and enhances your visibility.
資料ダウンロード
QCD調達購買管理クラウド「newji」は、調達購買部門で必要なQCD管理全てを備えた、現場特化型兼クラウド型の今世紀最高の購買管理システムとなります。
ユーザー登録
調達購買業務の効率化だけでなく、システムを導入することで、コスト削減や製品・資材のステータス可視化のほか、属人化していた購買情報の共有化による内部不正防止や統制にも役立ちます。
NEWJI DX
製造業に特化したデジタルトランスフォーメーション(DX)の実現を目指す請負開発型のコンサルティングサービスです。AI、iPaaS、および先端の技術を駆使して、製造プロセスの効率化、業務効率化、チームワーク強化、コスト削減、品質向上を実現します。このサービスは、製造業の課題を深く理解し、それに対する最適なデジタルソリューションを提供することで、企業が持続的な成長とイノベーションを達成できるようサポートします。
オンライン講座
製造業、主に購買・調達部門にお勤めの方々に向けた情報を配信しております。
新任の方やベテランの方、管理職を対象とした幅広いコンテンツをご用意しております。
お問い合わせ
コストダウンが利益に直結する術だと理解していても、なかなか前に進めることができない状況。そんな時は、newjiのコストダウン自動化機能で大きく利益貢献しよう!
(Β版非公開)