- お役立ち記事
- The next step to improve productivity with rubber manufacturing mold technology
月間76,176名の
製造業ご担当者様が閲覧しています*
*2025年3月31日現在のGoogle Analyticsのデータより
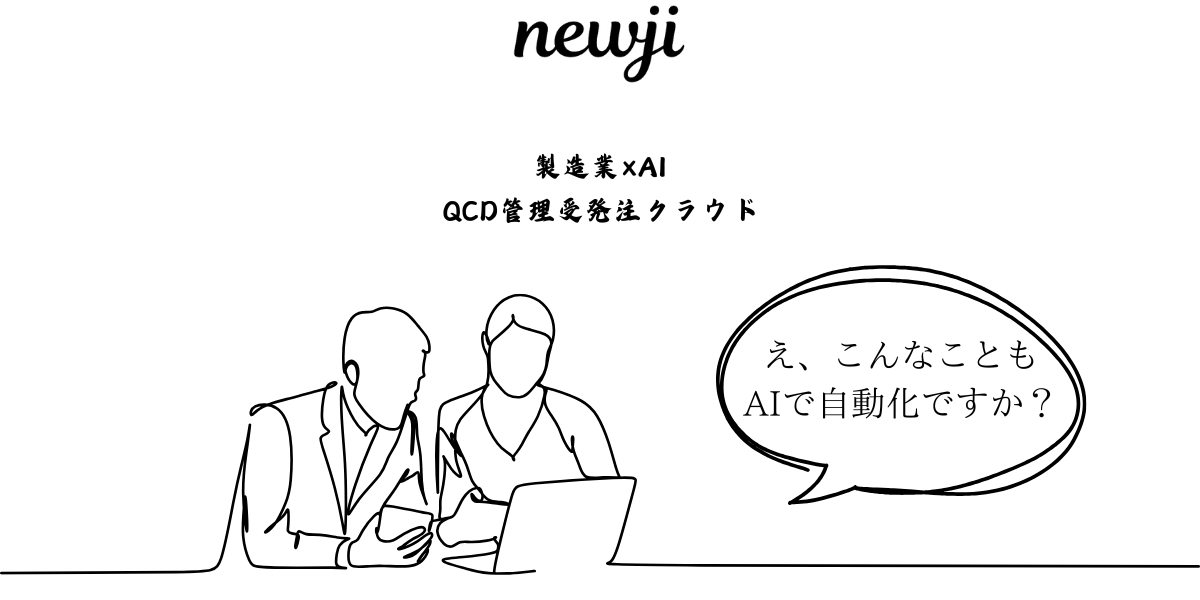
The next step to improve productivity with rubber manufacturing mold technology
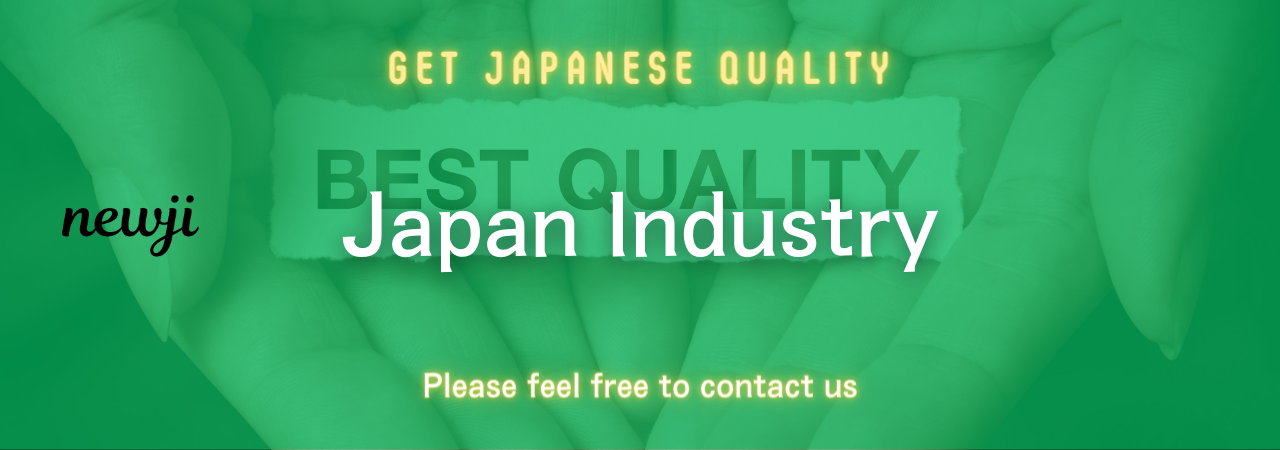
目次
Introduction to Rubber Manufacturing Mold Technology
Rubber manufacturing mold technology has undergone significant advancements in recent years, opening new avenues for enhancing productivity and efficiency in the industry.
As the demand for rubber products continues to rise across various sectors, from automotive to consumer goods, the need for improved manufacturing techniques becomes increasingly critical.
Understanding the technology behind rubber molds and its potential impacts offers valuable insights into the future of manufacturing.
Understanding Rubber Molding
Rubber molding is a predominant process in the manufacture of rubber products.
This technique involves shaping rubber by placing it into a mold cavity where it is heated to its curing temperature.
The curing process ensures that the rubber achieves its desired characteristics, such as elasticity and durability.
There are several types of rubber molding techniques, including compression molding, injection molding, and transfer molding, each with its unique advantages and applications.
Compression Molding
Compression molding is one of the oldest and most traditional methods used in rubber manufacturing.
In this process, preheated rubber is placed in a heated mold cavity and compressed to form the desired shape.
The pressure and heat allow the rubber to flow and fill the mold, after which it is cured.
This method is highly effective for producing large, durable rubber parts and is favored for its relatively simple setup and lower production costs.
Injection Molding
Injection molding is a more modern technique that has gained widespread acceptance due to its precision and efficiency.
In this process, rubber is heated to a molten state and injected into a closed mold under high pressure.
The rubber in this state fills the mold completely, ensuring high dimensional accuracy and repeatability.
Injection molding is ideal for producing complex and high-volume parts with consistent quality, making it a preferred choice for many manufacturers.
Transfer Molding
Transfer molding combines elements of both compression and injection molding.
Rubber is placed in a chamber and then pushed into the mold cavities through small openings.
This technique allows for intricate parts to be molded more easily compared to compression molding while maintaining lower costs typical of simpler manufacturing setups.
Transfer molding is often used in applications requiring a balance between complexity and cost-effectiveness.
Advancements in Mold Technology
Recent advancements in mold technology have significantly impacted the efficiency and productivity of rubber manufacturing processes.
These innovations focus on improving precision, reducing cycle times, and enhancing product quality.
3D Printing and Rapid Prototyping
The introduction of 3D printing and rapid prototyping in mold manufacturing has revolutionized the way prototypes are developed.
By using these technologies, manufacturers can create prototype molds quickly, allowing for immediate testing and iteration.
This rapid prototyping reduces the development time for new products and facilitates faster market entry.
3D printing also enables the creation of complex mold designs that were previously challenging or impossible to produce with traditional methods.
Automated Mold Design
Automation in mold design has led to greater accuracy and efficiency.
Computer-aided design (CAD) software now enables precise control over the mold features, allowing designers to optimize the flow and filling of rubber materials within the mold.
These advancements reduce material waste and improve product quality, ensuring that each part meets exact specifications.
Temperature and Pressure Control Innovations
Enhancements in temperature and pressure control during the molding process have brought about improvements in product consistency and quality.
Advanced sensors and control systems allow for real-time monitoring and adjustments, ensuring optimal curing and minimal defects.
These innovations help manufacturers achieve higher yields and reduce the frequency of defective parts, further boosting productivity.
Impacts on Productivity
The continuous evolution of rubber mold technology translates directly into increased productivity levels for manufacturers.
These improvements allow businesses to meet growing demands without sacrificing quality or increasing costs.
Increased Production Efficiency
Modern mold technologies reduce cycle times significantly, enabling faster turnaround on production runs.
This efficiency is particularly advantageous for high-volume manufacturing, where time savings accumulate and enhance overall productivity.
Manufacturers can respond more swiftly to market demands, ensuring that customer needs are met promptly.
Enhanced Product Quality
With better control over the molding process, manufacturers can produce higher quality products with fewer defects.
This consistency in quality enhances brand reputation and reduces the cost associated with rework and warranty claims.
High-quality products also lead to increased customer satisfaction and repeat business.
Cost Reduction
Innovations in mold technology contribute to cost reduction by minimizing waste and maximizing efficiency.
The ability to create precise molds with minimal material waste reduces raw material costs.
Furthermore, advancements in automated systems and rapid prototyping reduce labor costs associated with traditional mold-making processes.
Conclusion
The future of rubber manufacturing looks promising, with mold technology playing an instrumental role in boosting productivity and reducing costs.
The continued adoption of advanced techniques like automated mold design, 3D printing, and precise control measures will push the boundaries of what is possible in rubber manufacturing.
As the industry evolves, staying abreast of these technological advancements will be crucial for manufacturers seeking to maintain a competitive edge in an ever-growing market.
資料ダウンロード
QCD管理受発注クラウド「newji」は、受発注部門で必要なQCD管理全てを備えた、現場特化型兼クラウド型の今世紀最高の受発注管理システムとなります。
ユーザー登録
受発注業務の効率化だけでなく、システムを導入することで、コスト削減や製品・資材のステータス可視化のほか、属人化していた受発注情報の共有化による内部不正防止や統制にも役立ちます。
NEWJI DX
製造業に特化したデジタルトランスフォーメーション(DX)の実現を目指す請負開発型のコンサルティングサービスです。AI、iPaaS、および先端の技術を駆使して、製造プロセスの効率化、業務効率化、チームワーク強化、コスト削減、品質向上を実現します。このサービスは、製造業の課題を深く理解し、それに対する最適なデジタルソリューションを提供することで、企業が持続的な成長とイノベーションを達成できるようサポートします。
製造業ニュース解説
製造業、主に購買・調達部門にお勤めの方々に向けた情報を配信しております。
新任の方やベテランの方、管理職を対象とした幅広いコンテンツをご用意しております。
お問い合わせ
コストダウンが利益に直結する術だと理解していても、なかなか前に進めることができない状況。そんな時は、newjiのコストダウン自動化機能で大きく利益貢献しよう!
(β版非公開)