- お役立ち記事
- The Path to a Smart Factory: A New Era Opened by Manufacturing DX
月間76,176名の
製造業ご担当者様が閲覧しています*
*2025年3月31日現在のGoogle Analyticsのデータより
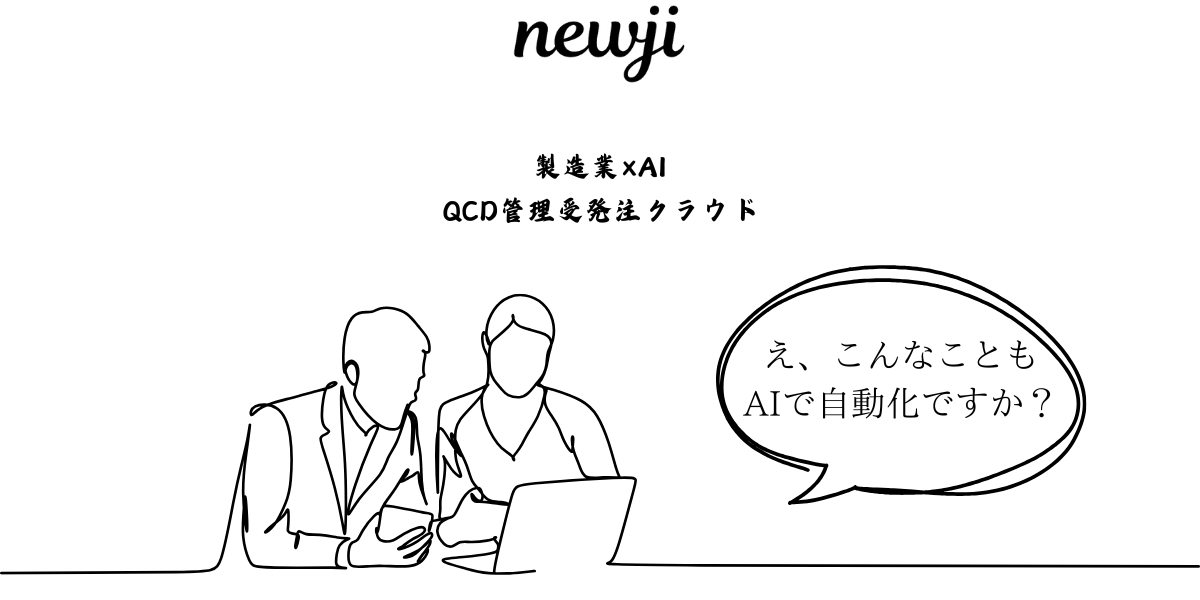
The Path to a Smart Factory: A New Era Opened by Manufacturing DX
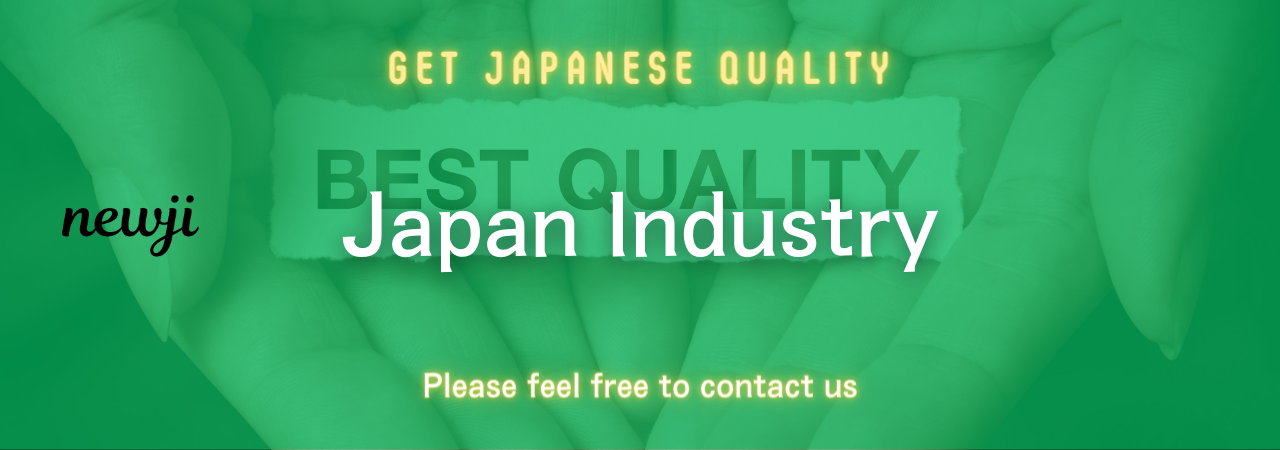
The world of manufacturing is changing rapidly as industries embrace digital transformation (DX) to create smart factories.
This revolution is transforming traditional manufacturing processes, creating more efficient, agile, and responsive operations.
Let’s explore what manufacturing DX is, why it’s important, and how it’s making smart factories a reality.
目次
Understanding Manufacturing DX
Manufacturing Digital Transformation, often abbreviated as DX, involves integrating advanced digital technologies into manufacturing processes.
This transformation is more than just using new technologies, it’s about rethinking and reshaping how manufacturing is done.
The goal of manufacturing DX is to improve efficiency, reduce costs, enhance product quality, and make operations more flexible and scalable.
This is achieved by automating processes, using data analytics, and leveraging the Internet of Things (IoT) among other technologies.
The Role of Automation
Automation is a cornerstone of manufacturing DX.
By automating repetitive tasks, manufacturers can reduce human error, lower labor costs, and increase production speed.
Robotic process automation (RPA) and advanced robotics are making significant strides in this area.
Robots can work around the clock without fatigue, performing tasks with a level of precision that humans often cannot match.
This not only boosts productivity but also allows human workers to focus on more complex and strategic activities.
Data Analytics and Machine Learning
Data is the new oil, and in the context of manufacturing, it’s an invaluable resource.
Manufacturing DX harnesses vast amounts of data generated by modern production processes.
Advanced data analytics and machine learning algorithms can analyze this data to provide insights that drive better decision-making.
Predictive maintenance is a great example of how data analytics can be utilized.
By analyzing machine performance data, manufacturers can predict when a machine will fail and perform maintenance before it breaks down.
This minimizes downtime and maximizes efficiency.
The Internet of Things (IoT)
The Internet of Things (IoT) connects machines, devices, and systems in a network that enables communication and data exchange.
In manufacturing, IoT plays a crucial role in creating smart factories.
IoT sensors can monitor machinery, collect data in real-time, and send alerts if there are any issues.
This real-time monitoring allows for immediate action, reducing delays and preventing potential problems from escalating.
IoT can also enhance supply chain management by providing real-time visibility into inventory levels, shipment status, and demand forecasting.
Benefits of Smart Factories
The transition to smart factories driven by manufacturing DX offers numerous benefits.
These include improved efficiency, higher quality products, greater flexibility, and enhanced sustainability.
Increased Efficiency
Smart factories are incredibly efficient.
Automation speeds up production processes, minimizes waste, and ensures consistency.
Data analytics help identify bottlenecks and inefficiencies, allowing for continuous improvement.
This all translates to higher output at lower costs.
Enhanced Product Quality
With the precision and consistency that automation and data analytics provide, product quality can significantly improve.
Machine learning algorithms can detect defects that may be imperceptible to the human eye.
This ensures that only the highest quality products make it to the market.
Greater Flexibility
Smart factories are designed to be agile.
They can quickly adapt to changing demands and production requirements.
For instance, if there is a sudden spike in demand for a particular product, smart factories can scale up production quickly.
This flexibility is crucial in today’s fast-paced markets.
Enhanced Sustainability
Sustainability is becoming increasingly important in manufacturing.
Smart factories can reduce energy consumption and waste through more efficient processes.
Real-time monitoring allows for better resource management and optimization, leading to a smaller environmental footprint.
Challenges in Implementing Manufacturing DX
While the benefits of manufacturing DX are clear, the path to achieving a smart factory isn’t without challenges.
It requires significant investment, a cultural shift, and overcoming technical hurdles.
Investment Costs
Implementing advanced technologies can be expensive.
There are costs associated with purchasing new equipment, training employees, and maintaining new systems.
However, many companies find that the long-term benefits such as cost savings, improved productivity, and enhanced competitiveness justify the initial investment.
Cultural Shift
Transitioning to a smart factory requires a cultural shift within the organization.
Employees must be open to change and ready to embrace new ways of working.
Leaders need to foster a culture of innovation and continuous improvement.
This can be achieved through proper training and effective change management strategies.
Technical Challenges
Integrating new technologies with existing systems can be technically challenging.
There may be compatibility issues or a lack of technical expertise within the organization.
Working with experienced technology partners and investing in employee training can help overcome these challenges.
The Future of Manufacturing
The journey towards smart factories is an ongoing process.
As technology continues to evolve, so too will manufacturing practices.
Future advancements such as artificial intelligence (AI), 5G connectivity, and blockchain technology promise to further revolutionize the industry.
AI can take data analytics to the next level, providing even deeper insights and enabling more sophisticated automation.
5G connectivity will enhance the capabilities of IoT, allowing for faster and more reliable data transmission.
Blockchain can improve supply chain transparency and security, ensuring that data is immutable and trustworthy.
In conclusion, manufacturing DX and the advent of smart factories are ushering in a new era in the manufacturing industry.
While the transformation comes with its challenges, the benefits in terms of efficiency, product quality, flexibility, and sustainability are undeniable.
As companies continue to embrace digital transformation, the future of manufacturing looks smarter and more innovative than ever before.
資料ダウンロード
QCD管理受発注クラウド「newji」は、受発注部門で必要なQCD管理全てを備えた、現場特化型兼クラウド型の今世紀最高の受発注管理システムとなります。
ユーザー登録
受発注業務の効率化だけでなく、システムを導入することで、コスト削減や製品・資材のステータス可視化のほか、属人化していた受発注情報の共有化による内部不正防止や統制にも役立ちます。
NEWJI DX
製造業に特化したデジタルトランスフォーメーション(DX)の実現を目指す請負開発型のコンサルティングサービスです。AI、iPaaS、および先端の技術を駆使して、製造プロセスの効率化、業務効率化、チームワーク強化、コスト削減、品質向上を実現します。このサービスは、製造業の課題を深く理解し、それに対する最適なデジタルソリューションを提供することで、企業が持続的な成長とイノベーションを達成できるようサポートします。
製造業ニュース解説
製造業、主に購買・調達部門にお勤めの方々に向けた情報を配信しております。
新任の方やベテランの方、管理職を対象とした幅広いコンテンツをご用意しております。
お問い合わせ
コストダウンが利益に直結する術だと理解していても、なかなか前に進めることができない状況。そんな時は、newjiのコストダウン自動化機能で大きく利益貢献しよう!
(β版非公開)