- お役立ち記事
- The Pros and Cons of Compression Molding: What SMEs Should Know
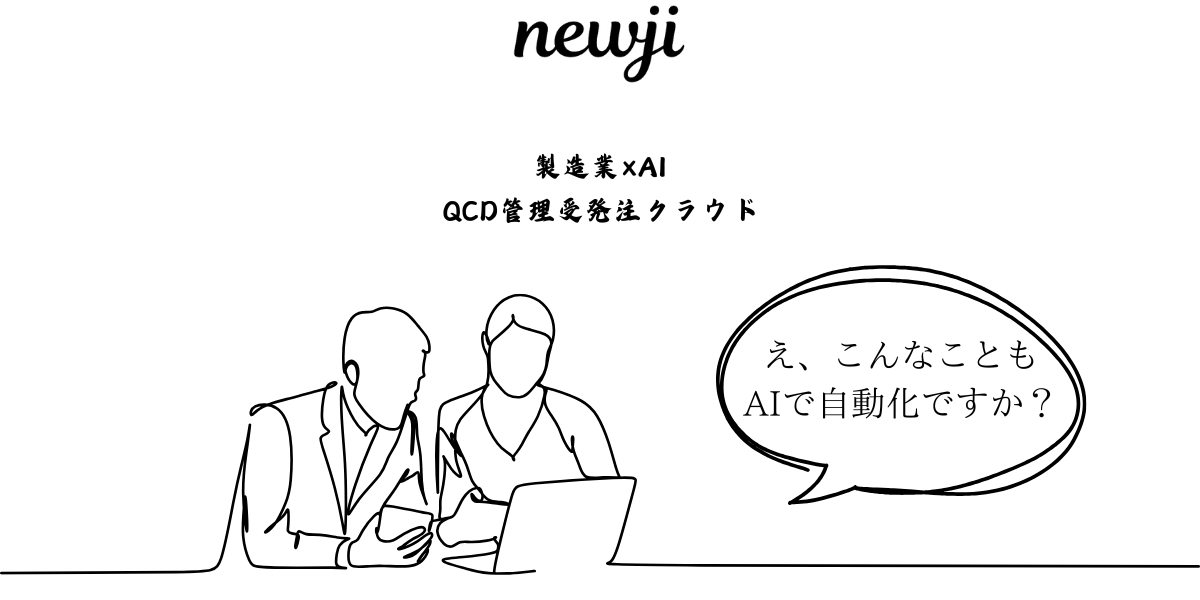
The Pros and Cons of Compression Molding: What SMEs Should Know
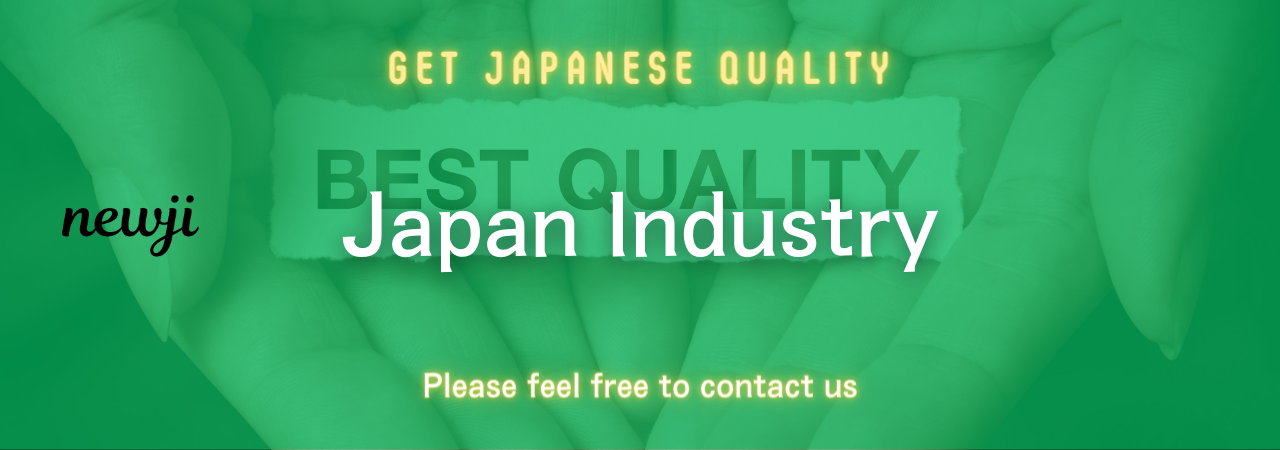
目次
Understanding Compression Molding
Compression molding is a manufacturing process widely used across various industries due to its versatility and cost-effectiveness.
This method involves placing a pre-measured amount of raw material, usually a polymer, into a heated mold cavity.
The mold then closes, compressing the material into the desired shape as it cures and solidifies.
While it might seem straightforward, there are several pros and cons to consider, especially for Small and Medium-sized Enterprises (SMEs) looking to implement or expand their use of this technique.
The Advantages of Compression Molding
Cost-Effectiveness
One of the primary benefits of compression molding is its cost-effectiveness.
For SMEs with tight budgets, this process can be a financially savvy option.
The molds are generally less expensive compared to those used in injection and transfer molding, reducing initial setup costs.
Additionally, it requires less energy and labor to operate, further cutting down expenses.
Versatility in Design
Compression molding is highly versatile in terms of the materials it can handle.
This allows for a wide range of product designs and applications.
Employing materials like thermosetting plastics, rubber, and composite materials, SMEs can produce everything from automotive parts to consumer goods.
Superior Strength and Durability
Parts created through compression molding are known for their superior strength and durability.
This is because the process allows for uniform pressure distribution and better material bonding.
Products are often able to withstand harsh environments, making them ideal for industrial applications.
Simplicity and Efficiency
The simplicity of the compression molding process is a significant advantage.
With fewer moving parts compared to other molding methods, it decreases the likelihood of mechanical failures.
For SMEs with limited resources, the efficiency of production with minimal downtime can be very beneficial.
The Disadvantages of Compression Molding
Limited Material Options
While compression molding is versatile, it does have some limitations regarding the types of materials it can effectively utilize.
The process is more suited to thermosetting polymers, and not ideal for all thermoplastics, which could limit design possibilities for certain products.
Surface Quality Considerations
Products manufactured through compression molding may often require additional finishing due to surface imperfections.
This can increase production time and cost for SMEs, potentially negating some of the method’s cost advantages.
Longer Cycle Times
Compared to other molding processes, compression molding generally has longer cycle times because it involves a curing phase while the material solidifies.
For SMEs that need to produce large quantities quickly, this aspect might become a bottleneck, impacting efficiency and timelines.
High Initial Tooling Costs
While the process itself is cost-effective, the initial costs of developing and fabricating molds can be high.
This could be a significant investment for SMEs, especially when engaging in small-production runs or when frequently changing designs.
When to Choose Compression Molding
Compression molding is ideally suited for volume production where the emphasis is on strong and durable parts.
SMEs in industries like automotive, aerospace, and consumer electronics often benefit from this method.
When deciding whether to use compression molding, it is crucial for SMEs to weigh the initial tooling costs against the efficiency and durability of the end-products.
For businesses focused on producing simple, robust components where the emphasis on surface aesthetics is minimal, compression molding can be an excellent choice.
It’s also fitting when a company plans to grow production and needs a method that’s scalable without extensive overhead.
Making an Informed Decision
Small and Medium Enterprises must conduct a thorough analysis before integrating compression molding into their production processes.
A detailed cost-benefit analysis should be conducted, emphasizing factors such as material costs, anticipated production volume, and end-use requirements of the products.
Partnering with experienced toolmakers and molders can help SMEs navigate the complexities and make informed decisions.
Considering streamlined operations and the importance of product durability can guide SMEs in opting for compression molding when aligned with their business goals.
Conclusion: Balancing Pros and Cons
Compression molding presents a variety of advantages that make it attractive to SMEs, particularly those focused on producing durable, high-strength products.
However, potential downsides like cycle times, material limitations, and surface imperfections require careful consideration.
SMEs should evaluate their specific needs and product requirements, along with conducting market research, to determine if compression molding aligns with their strategic objectives.
By doing so, they can harness the strengths of this versatile manufacturing process while mitigating its limitations, optimizing their operations for success.
資料ダウンロード
QCD調達購買管理クラウド「newji」は、調達購買部門で必要なQCD管理全てを備えた、現場特化型兼クラウド型の今世紀最高の購買管理システムとなります。
ユーザー登録
調達購買業務の効率化だけでなく、システムを導入することで、コスト削減や製品・資材のステータス可視化のほか、属人化していた購買情報の共有化による内部不正防止や統制にも役立ちます。
NEWJI DX
製造業に特化したデジタルトランスフォーメーション(DX)の実現を目指す請負開発型のコンサルティングサービスです。AI、iPaaS、および先端の技術を駆使して、製造プロセスの効率化、業務効率化、チームワーク強化、コスト削減、品質向上を実現します。このサービスは、製造業の課題を深く理解し、それに対する最適なデジタルソリューションを提供することで、企業が持続的な成長とイノベーションを達成できるようサポートします。
オンライン講座
製造業、主に購買・調達部門にお勤めの方々に向けた情報を配信しております。
新任の方やベテランの方、管理職を対象とした幅広いコンテンツをご用意しております。
お問い合わせ
コストダウンが利益に直結する術だと理解していても、なかなか前に進めることができない状況。そんな時は、newjiのコストダウン自動化機能で大きく利益貢献しよう!
(Β版非公開)