- お役立ち記事
- The role of the purchasing department in improving procurement processes in the manufacturing industry
月間76,176名の
製造業ご担当者様が閲覧しています*
*2025年3月31日現在のGoogle Analyticsのデータより
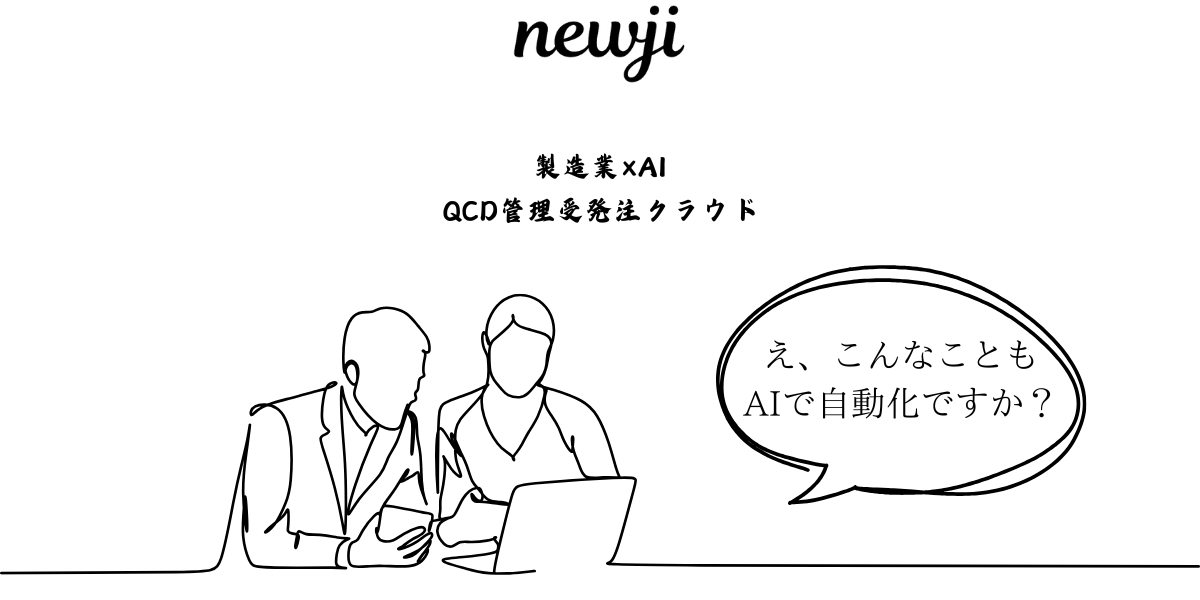
The role of the purchasing department in improving procurement processes in the manufacturing industry
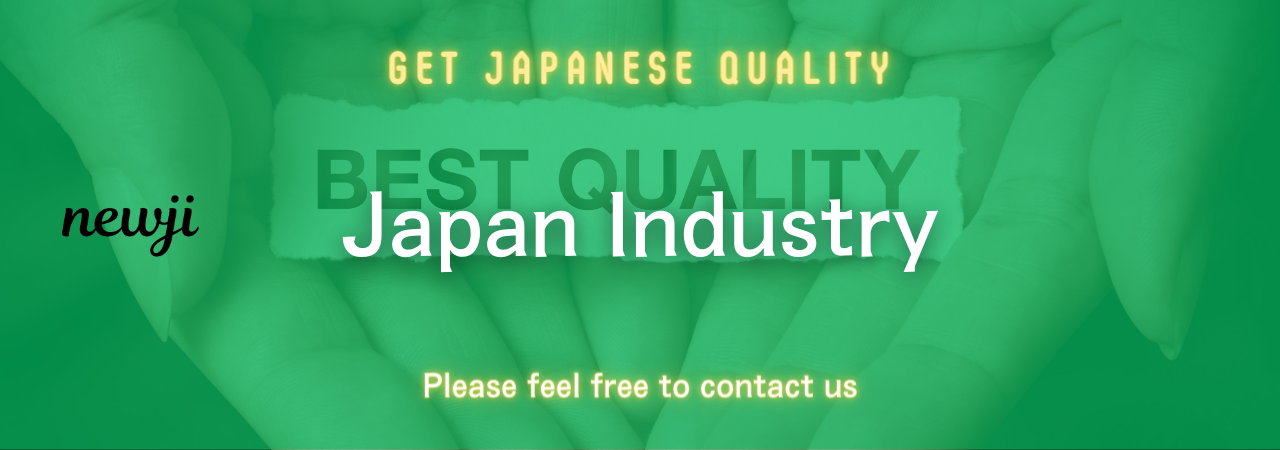
目次
Understanding the Purchasing Department
In the bustling world of manufacturing, the purchasing department stands as a crucial component in the overall operation of a company.
Its primary role is to procure the materials, supplies, and services needed for production.
This may sound simple enough, but the complexities involved in securing the best prices, quality, and delivery times from suppliers require adequate planning and expertise.
A well-functioning purchasing department ensures that the manufacturing process runs smoothly, efficiently, and economically.
It acts as a bridge between the company and external suppliers, negotiating terms before any transaction is made.
This guarantees that the company will have what it needs when it needs it, without surplus or shortage.
Key Functions of the Purchasing Department
The purchasing department has several key functions that contribute to the optimization of procurement processes.
Sourcing and Supplier Selection
One of the foremost tasks of the purchasing department is sourcing and selecting suppliers.
This involves identifying potential suppliers, evaluating them based on a range of criteria, and selecting those that offer the best mix of quality, cost, and reliability.
The selection process is thorough and involves assessing supplier capabilities, delivery performance, and financial stability.
Price Negotiation
Negotiating the best prices from suppliers is a fundamental responsibility of the purchasing department.
This doesn’t just mean securing the lowest prices; rather, it involves obtaining the best value for the company’s money.
Effective negotiation requires skill and knowledge of the market, as well as an understanding of the manufacturing company’s needs.
Order Management
Once suppliers have been selected and terms negotiated, the purchasing department is responsible for order management.
This includes placing purchase orders, tracking deliveries, and ensuring that the correct products are received in the right quantities.
Order management also involves resolving any issues that arise with orders or deliveries.
Supplier Relationship Management
Maintaining strong relationships with suppliers is crucial for any purchasing department.
These relationships play a significant role in the negotiation of future contracts and can lead to better deals, improved product availability, and priority in times of scarcity.
Building long-term, mutually beneficial relationships with suppliers can significantly enhance the efficiency and reliability of the procurement process.
Improving Procurement Processes
An efficient procurement process is essential for maintaining a competitive edge in the manufacturing industry.
The purchasing department can take several steps to improve these processes.
Implementation of Technology
Technology is a game-changer in the modern procurement landscape.
By implementing digital tools such as e-procurement systems and supplier management software, the purchasing department can streamline processes, reduce paperwork, and improve efficiency.
These tools also provide access to real-time data, which aids in decision-making and enhances transparency across the supply chain.
Emphasis on Sustainability
Today, sustainability has become a critical focus in procurement.
Purchasing departments are increasingly looking for ways to source materials and services that minimize environmental impact.
This can involve selecting suppliers with strong sustainability credentials or choosing materials that are recyclable or biodegradable.
By integrating sustainability into procurement processes, companies not only contribute to environmental protection but also align with consumer demand for greener products.
Training and Development
Ongoing training and development for purchasing staff ensure that they remain up-to-date with changes in industry standards, technology, and best practices.
Regular training sessions can enhance the skills of purchasing team members, equipping them with the tools necessary to navigate a rapidly evolving procurement environment.
Cost Analysis and Control
Regular cost analysis allows the purchasing department to identify opportunities for cost savings and to implement strategies for cost control.
By conducting spend analysis, the department can better understand purchasing habits and identify areas where cost improvements can be made, ultimately leading to more efficient procurement.
The Impact of an Effective Purchasing Department
An effective purchasing department can significantly impact a manufacturing company’s bottom line.
Cost Savings
Strategic procurement processes lead to considerable cost savings for a company.
By negotiating better terms with suppliers and optimizing inventory, the purchasing department can reduce expenses and improve profit margins.
Efficiency and Productivity
By ensuring that the right materials are available at the right time, the purchasing department helps maintain a steady production flow.
This minimizes downtime and enhances overall productivity, enabling the company to meet production targets and delivery deadlines consistently.
Risk Management
The purchasing department plays a vital role in risk management by diversifying suppliers and building buffer stocks where necessary.
This reduces dependency on a single supplier and mitigates risks such as supply chain disruptions or delays, ensuring business continuity.
Conclusion
In conclusion, the purchasing department is pivotal in optimizing procurement processes within the manufacturing industry.
Its responsibilities, ranging from supplier selection to price negotiation, directly affect a company’s efficiency, cost management, and competitive standing.
By embracing technology, focusing on sustainability, and continuously improving their skills, purchasing professionals can enhance procurement processes, leading to significant cost savings and operational efficiency.
Thus, a strategic, forward-thinking purchasing department is an invaluable asset to any manufacturing company aiming for long-term success.
資料ダウンロード
QCD管理受発注クラウド「newji」は、受発注部門で必要なQCD管理全てを備えた、現場特化型兼クラウド型の今世紀最高の受発注管理システムとなります。
ユーザー登録
受発注業務の効率化だけでなく、システムを導入することで、コスト削減や製品・資材のステータス可視化のほか、属人化していた受発注情報の共有化による内部不正防止や統制にも役立ちます。
NEWJI DX
製造業に特化したデジタルトランスフォーメーション(DX)の実現を目指す請負開発型のコンサルティングサービスです。AI、iPaaS、および先端の技術を駆使して、製造プロセスの効率化、業務効率化、チームワーク強化、コスト削減、品質向上を実現します。このサービスは、製造業の課題を深く理解し、それに対する最適なデジタルソリューションを提供することで、企業が持続的な成長とイノベーションを達成できるようサポートします。
製造業ニュース解説
製造業、主に購買・調達部門にお勤めの方々に向けた情報を配信しております。
新任の方やベテランの方、管理職を対象とした幅広いコンテンツをご用意しております。
お問い合わせ
コストダウンが利益に直結する術だと理解していても、なかなか前に進めることができない状況。そんな時は、newjiのコストダウン自動化機能で大きく利益貢献しよう!
(β版非公開)