- お役立ち記事
- The Role of Ultrasonic Cleaners in Revolutionizing Japanese Manufacturing
The Role of Ultrasonic Cleaners in Revolutionizing Japanese Manufacturing
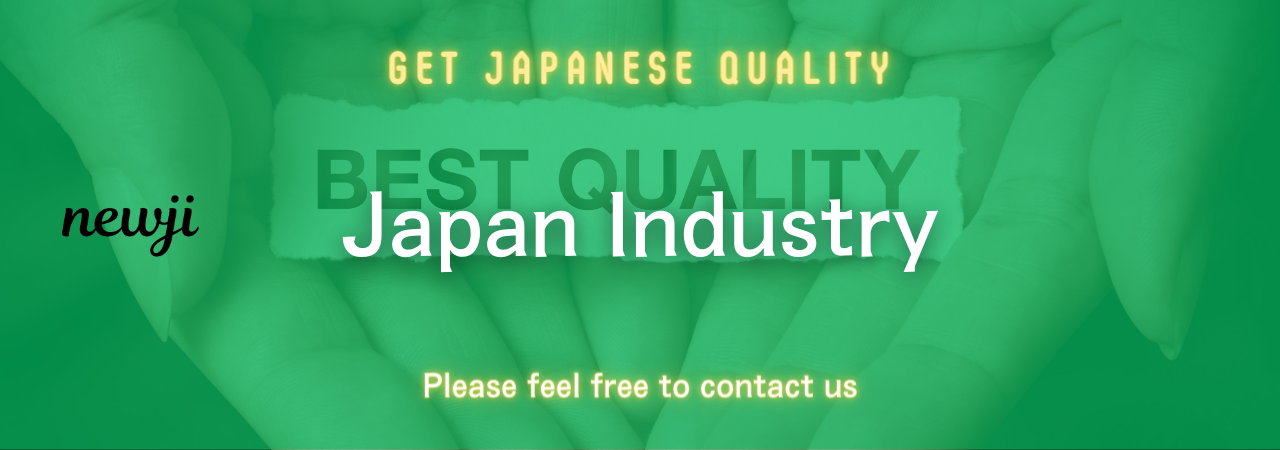
目次
The Rise of Ultrasonic Cleaners in Japanese Manufacturing
Manufacturing in Japan has long been synonymous with high precision, innovation, and an unwavering commitment to quality. Essential to this success has been the integration of advanced technologies that improve efficiency and product quality. Among these technologies, ultrasonic cleaners have played a significant role in revolutionizing various sectors of Japanese manufacturing.
Understanding Ultrasonic Cleaners
Ultrasonic cleaners employ high-frequency sound waves, typically in the range of 20 kHz to 40 kHz, to create microscopic cavitation bubbles in a cleaning solution. These bubbles implode upon contact with surfaces, effectively dislodging contaminants without damaging the material. Whether it’s grease, oil, dust, or other pollutants, ultrasonic cleaning offers a non-abrasive yet thorough cleaning method.
Practical Applications in Japanese Manufacturing
Precision Components
Japan’s manufacturing landscape is known for its high-precision components, particularly in industries such as automotive, electronics, and aerospace. Ultrasonic cleaners are invaluable in maintaining the cleanliness and precision of these components. The ability to clean complex geometries and delicate materials without mechanical abrasion enhances both performance and lifespan.
Medical Equipment
The medical device manufacturing industry in Japan adheres to stringent sanitation standards. Ultrasonic cleaners help ensure that medical instruments and devices are thoroughly cleaned and disinfected, minimizing the risk of contamination. This not only meets regulatory requirements but also bolsters Japan’s reputation for producing high-quality medical equipment.
Semiconductor Industry
The semiconductor industry, which forms the backbone of Japan’s tech sector, requires ultra-clean environments. Ultrasonic cleaner technology allows manufacturers to remove even the tiniest particles from semiconductor wafers and components. This level of precision is crucial for maintaining the efficacy and reliability of semiconductors.
Advantages of Ultrasonic Cleaners
Enhanced Cleaning Efficiency
Ultrasonic cleaners offer a higher level of cleaning efficiency compared to traditional methods. The cavitation bubbles can reach incredibly small crevices and complex surfaces, ensuring a comprehensive clean.
Non-Abrasive Cleaning
One of the primary advantages is that ultrasonic cleaning does not rely on mechanical scrubbing. As a result, delicate components are cleaned without the risk of abrasion or damage, which is particularly important for precision instruments.
Environmental Sustainability
Ultrasonic cleaning requires fewer harsh chemicals, making it a more environmentally friendly option. Additionally, the longevity of cleaning solutions can be extended, reducing chemical waste.
Time and Cost Savings
Due to the efficiency and thoroughness of ultrasonic cleaners, manufacturers can save invaluable time and reduce labor costs. Faster processing times and fewer touchpoints in the cleaning procedure streamline production workflows.
Challenges and Disadvantages
Initial Investment
One of the primary barriers to adopting ultrasonic cleaners is the initial investment required. High-quality equipment and the necessary cleaning solutions can be costly upfront, although these expenses are often mitigated over time through operational savings.
Maintenance and Operation
While ultrasonic cleaners are effective, they require regular maintenance to ensure peak performance. Components like transducers may need periodic replacement, and the cleaning solution will need regular replenishment.
Material Limitations
Not all materials are suitable for ultrasonic cleaning. Certain plastics, for example, may suffer damage. It’s essential to conduct compatibility tests to ensure that the materials being cleaned are not adversely affected.
Best Practices for Implementing Ultrasonic Cleaners
Supplier Selection
Choosing a reliable supplier for ultrasonic cleaning equipment is vital. Suppliers should offer robust customer support, provide detailed product information, and ideally, a comprehensive warranty. Experienced suppliers often offer valuable insights into the optimal usage and maintenance of their equipment, contributing to long-term value.
Optimal Frequency Settings
The effectiveness of ultrasonic cleaning can vary significantly depending on the frequency used. Higher frequencies are generally suited for delicate cleaning, while lower frequencies are more effective for removing heavier contaminants. Adjusting the frequency settings according to the specific cleaning requirements will yield the best results.
Regular Monitoring and Maintenance
Regular monitoring of the equipment’s performance can prevent unexpected downtimes. Frequent checks of the ultrasonic tank’s fluid levels, solution cleanliness, and transducer functionality are essential for maintaining efficiency.
Training and Education
Employees should be well-trained in the operation of ultrasonic cleaning equipment. Proper handling and an understanding of the equipment’s capabilities will maximize the benefits while reducing the risk of damage or inappropriate usage.
Future Prospects of Ultrasonic Cleaners in Japanese Manufacturing
The future of ultrasonic cleaning within Japanese manufacturing looks promising. As sectors continue to demand higher precision and cleanliness standards, ultrasonic technology will likely become even more integral. What’s more, advancements in the technology—such as higher frequency ranges and integration with automation—could lead to even more efficient and cost-effective cleaning solutions.
Conclusion
In summary, ultrasonic cleaners have revolutionized Japanese manufacturing by providing an efficient, non-abrasive, and environmentally friendly cleaning solution. The technology’s application across various sectors—from precision components to medical devices and semiconductors—shows its versatility and effectiveness.
While the initial investment and material limitations present challenges, the long-term benefits of incorporating ultrasonic cleaning are substantial. With careful implementation and ongoing maintenance, Japanese manufacturers can continue to achieve the high standards of quality and innovation for which they are renowned.
Understanding and adopting best practices—such as selecting the right supplier, optimizing frequency settings, and investing in training—will ensure that the full potential of ultrasonic cleaners is realized. As the technology evolves, so too will its role in maintaining Japan’s position at the forefront of global manufacturing excellence.
資料ダウンロード
QCD調達購買管理クラウド「newji」は、調達購買部門で必要なQCD管理全てを備えた、現場特化型兼クラウド型の今世紀最高の購買管理システムとなります。
ユーザー登録
調達購買業務の効率化だけでなく、システムを導入することで、コスト削減や製品・資材のステータス可視化のほか、属人化していた購買情報の共有化による内部不正防止や統制にも役立ちます。
NEWJI DX
製造業に特化したデジタルトランスフォーメーション(DX)の実現を目指す請負開発型のコンサルティングサービスです。AI、iPaaS、および先端の技術を駆使して、製造プロセスの効率化、業務効率化、チームワーク強化、コスト削減、品質向上を実現します。このサービスは、製造業の課題を深く理解し、それに対する最適なデジタルソリューションを提供することで、企業が持続的な成長とイノベーションを達成できるようサポートします。
オンライン講座
製造業、主に購買・調達部門にお勤めの方々に向けた情報を配信しております。
新任の方やベテランの方、管理職を対象とした幅広いコンテンツをご用意しております。
お問い合わせ
コストダウンが利益に直結する術だと理解していても、なかなか前に進めることができない状況。そんな時は、newjiのコストダウン自動化機能で大きく利益貢献しよう!
(Β版非公開)