- お役立ち記事
- The secret to improving work efficiency with factory analysis tools
月間76,176名の
製造業ご担当者様が閲覧しています*
*2025年3月31日現在のGoogle Analyticsのデータより
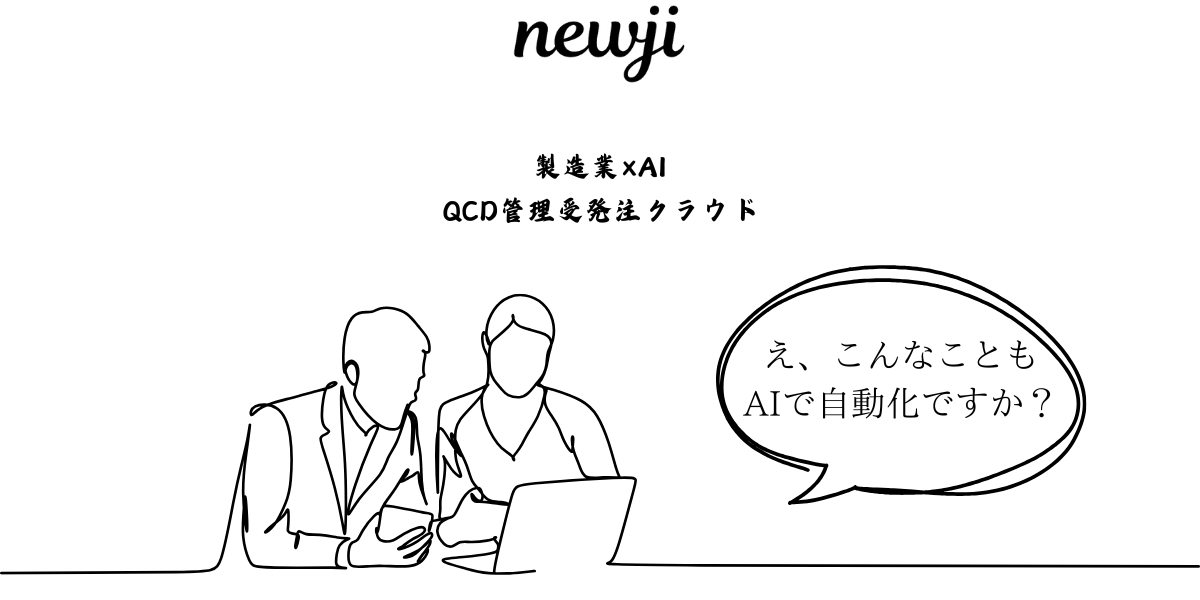
The secret to improving work efficiency with factory analysis tools
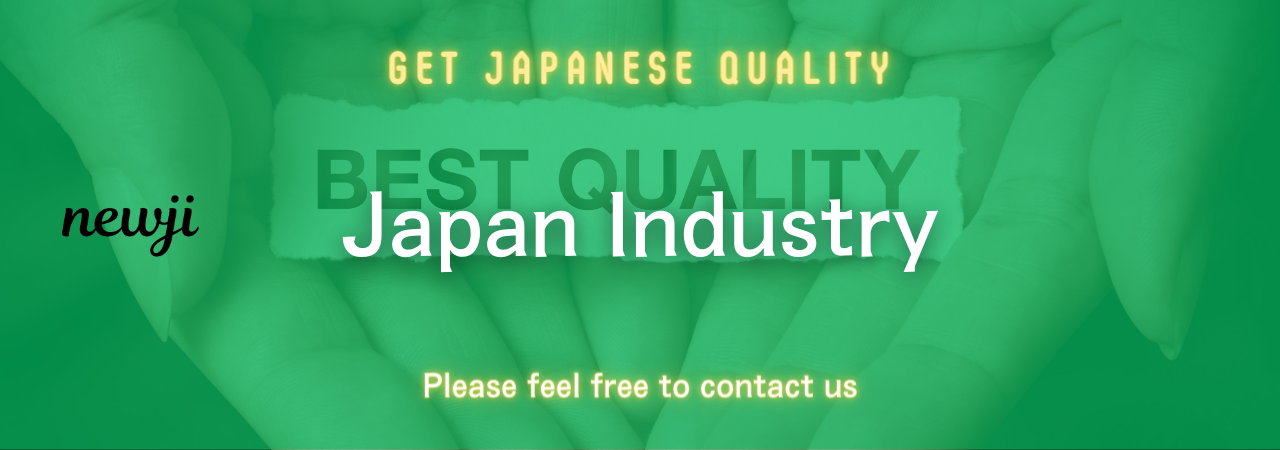
目次
Understanding Factory Analysis Tools
Factory analysis tools are specialized software and methodologies designed to help businesses assess and enhance the efficiency of their manufacturing processes.
These tools can provide valuable insights into every aspect of production, from raw material supply to finished goods.
By utilizing these tools, factories can not only streamline operations but also reduce waste, enhance product quality, and lower costs.
These tools often incorporate elements of data collection, statistics, and real-time monitoring.
They also assist in visualizing key production parameters, making it easier for managers and workers to identify bottlenecks or malfunctions that could hinder output.
By utilizing this data, factories can make informed decisions that advocate for better practices and increased efficiency.
Key Features of Factory Analysis Tools
The main features of factory analysis tools can vary significantly depending on the desired outcome and specific industry needs.
However, some core attributes are universally beneficial across different manufacturing sectors.
Real-Time Monitoring
Real-time monitoring is essential in maintaining optimal factory output.
With continuous updates, managers can receive immediate notifications about any fluctuations or deviations from the expected production ranges.
This feature allows factories to quickly address issues such as machinery malfunction, power outages, or disruptions in the supply chain.
By responding to these issues promptly, companies can minimize downtime and maintain efficient production schedules.
Data Collection and Analytics
Capturing and analyzing data is at the heart of any effective factory analysis tool.
Accurate data collection enables factories to gauge performance metrics effectively and identify trends over time.
Information such as production rates, machine efficacy, labor productivity, and defect rates provide an intricate picture of the overall manufacturing process.
Analytics then build on this data to forecast future outcomes, ensuring that factories are not just reacting to problems but are also proactively preparing for potential challenges.
How Factory Analysis Tools Improve Work Efficiency
Improving work efficiency in factories is a multifaceted task that involves enhancing various production components.
Factory analysis tools play a crucial role in facilitating these improvements in ways that are both direct and indirect.
Reducing Waste
One significant way that factory analysis tools enhance work efficiency is by focusing on waste reduction.
These tools can identify areas where raw materials are being overused or where defective products are consuming resources needlessly.
By precisely targeting these areas, factories can cut costs while also minimizing their environmental footprint.
Optimizing Resource Utilization
Factory analysis tools can also help optimize resource utilization by ensuring that machinery, manpower, and materials are used as effectively as possible.
By streamlining processes and eliminating inefficiencies, factories can achieve higher output levels without necessitating additional inputs or costs.
Efficient resource utilization not only contributes to increased work efficiency but also leads to a more sustainable manufacturing ecosystem.
Enhancing Product Quality
Quality control is another area where factory analysis tools make a critical impact.
By monitoring production in real time and analyzing historical data, factories can identify factors that contribute to product defects or inconsistencies.
This information helps in adjusting processes or machinery to maintain higher quality standards, meaning fewer defective products and more satisfied customers.
In the long run, superior product quality leads to a stronger brand reputation and increased profitability.
Steps to Implement Factory Analysis Tools
Successfully implementing factory analysis tools requires a thoughtful approach that involves several key steps.
These steps are designed to ensure seamless integration and maximum benefit from the tools.
Assess Factory Needs
Before choosing any specific tools, it’s important to assess the unique needs and challenges of the factory.
This involves identifying areas with the greatest potential for improvement, along with any existing inefficiencies that hinder performance.
A thorough assessment will form a solid foundation for all subsequent steps, guiding the selection and application of suitable factory analysis tools.
Select the Right Tools
Once the factory’s needs have been assessed, selecting the appropriate tools becomes crucial.
There is a wide variety of tools on the market, each with its unique features and capabilities.
Factors to consider include:
– Compatibility with existing systems
– Scalability to accommodate future growth
– Ease of use and training requirements
Choosing tools that align with these factors ensures that the factory can efficiently integrate them into daily operations.
Train the Workforce
Training your workforce is another critical component in maximizing the benefits of factory analysis tools.
Employees should be familiar with the tools and understand how to use them effectively.
Providing comprehensive training sessions and ongoing support can significantly alleviate any transition difficulties, thereby empowering the workforce to drive efficiency.
Monitor and Adjust
After implantation, continuous monitoring and adjustments are necessary to ensure that tools are delivering the desired improvements in efficiency.
Regular reviews of the impact and performance of the tools can help identify new areas of optimization and growth.
Adaptation to evolving industry standards and technologies is also imperative to maintain a competitive edge in the marketplace.
Conclusion
In an era where efficiency and productivity are more crucial than ever, factory analysis tools offer a secret weapon for improving work efficiency.
By leveraging their advanced capabilities, manufacturers can reduce waste, optimize resources, and enhance product quality, leading to improved profitability and sustainable operations.
These tools not only provide immediate improvements but also furnish factories with a strategic framework that enables long-term growth and adaptation.
As industries continue to evolve, those who embrace these technologies today will be well-positioned to lead in the world of tomorrow.
資料ダウンロード
QCD管理受発注クラウド「newji」は、受発注部門で必要なQCD管理全てを備えた、現場特化型兼クラウド型の今世紀最高の受発注管理システムとなります。
ユーザー登録
受発注業務の効率化だけでなく、システムを導入することで、コスト削減や製品・資材のステータス可視化のほか、属人化していた受発注情報の共有化による内部不正防止や統制にも役立ちます。
NEWJI DX
製造業に特化したデジタルトランスフォーメーション(DX)の実現を目指す請負開発型のコンサルティングサービスです。AI、iPaaS、および先端の技術を駆使して、製造プロセスの効率化、業務効率化、チームワーク強化、コスト削減、品質向上を実現します。このサービスは、製造業の課題を深く理解し、それに対する最適なデジタルソリューションを提供することで、企業が持続的な成長とイノベーションを達成できるようサポートします。
製造業ニュース解説
製造業、主に購買・調達部門にお勤めの方々に向けた情報を配信しております。
新任の方やベテランの方、管理職を対象とした幅広いコンテンツをご用意しております。
お問い合わせ
コストダウンが利益に直結する術だと理解していても、なかなか前に進めることができない状況。そんな時は、newjiのコストダウン自動化機能で大きく利益貢献しよう!
(β版非公開)