- お役立ち記事
- The secret to increasing factory productivity by sourcing new materials and optimizing purchasing costs
The secret to increasing factory productivity by sourcing new materials and optimizing purchasing costs
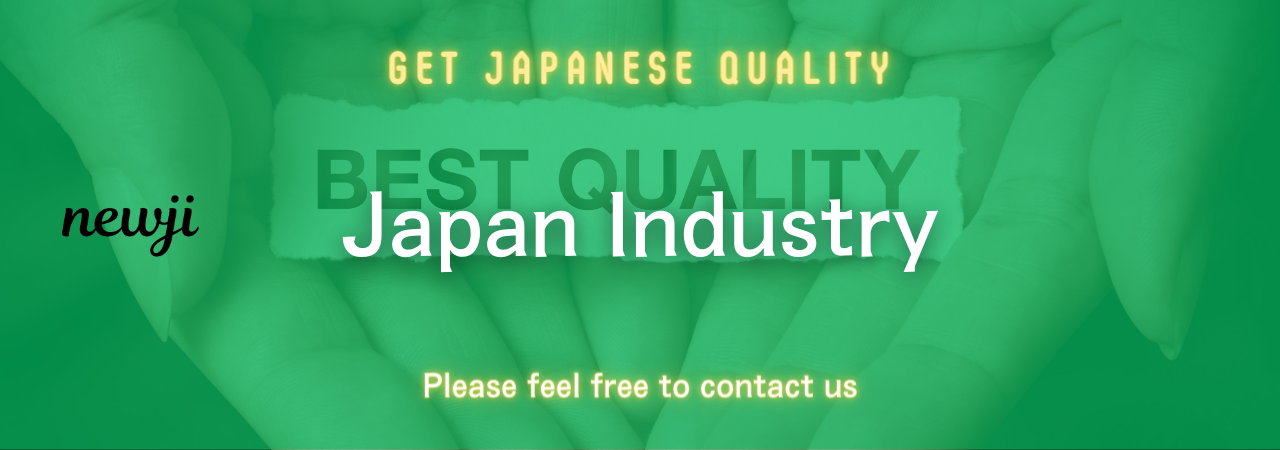
目次
Understanding the Importance of Sourcing New Materials
In the ever-evolving landscape of manufacturing, staying competitive is crucial.
One effective way to gain an edge is by sourcing new materials.
New materials can introduce numerous benefits to the production process.
They can enhance product quality, reduce costs, and improve overall efficiency.
By exploring and integrating innovative materials, factories can remain at the forefront of industry trends.
This proactive approach not only satisfies current demands but also anticipates future needs.
Benefits of Using New Materials
One significant benefit of using new materials is improvement in product quality.
Materials with superior properties can lead to products that are more durable, efficient, and appealing to consumers.
This can increase customer satisfaction and loyalty, directly impacting a factory’s bottom line.
Additionally, new materials often come with advancements in sustainability.
Eco-friendly materials can reduce the environmental footprint of manufacturing processes, aligning with global sustainability goals.
Another advantage is cost reduction.
Often, new materials can be more economically sourced or manufactured at lower costs than traditional ones.
This cost efficiency can be passed on to consumers or reinvested into further innovations.
In a market where margins can be tight, these savings are invaluable.
Challenges in Sourcing New Materials
Despite the clear benefits, sourcing new materials does come with challenges.
One primary concern is reliability.
New materials may not have the same track record or established supply chains as conventional materials.
This introduces an element of risk regarding their availability and consistency.
Moreover, integrating new materials may require changes in machinery or processes.
This can entail a substantial initial investment, which might be a hurdle for some manufacturers.
There is also the need for employee training to ensure that the workforce can effectively utilize the new materials.
Optimizing Purchasing Costs
While sourcing new materials can lead to direct improvements, optimizing purchasing costs is another vital part of increasing factory productivity.
Effective purchasing strategies focus on reducing costs while maintaining or improving quality.
This involves more than just negotiating lower prices.
It encompasses an entire strategy from supplier selection to improving supply chain efficiency.
Strategies for Cost Optimization
1. **Supplier Relationship Management**: Building strong relationships with suppliers can lead to more favorable terms.
Trust and good communication can foster partnerships, resulting in discounts, better payment terms, or priority during shortages.
2. **Bulk Purchasing**: Purchasing materials in bulk can significantly reduce costs.
Suppliers often offer discounts for larger orders, which can be a good strategy if storage is available.
3. **Leveraging Technology**: Utilizing technology in the purchasing process, such as ERP systems, can streamline operations.
These systems help in forecasting demand, managing inventories, and automating orders, reducing human error and inefficiencies.
4. **Diversifying Suppliers**: Relying on a single supplier can be risky.
By diversifying suppliers, a factory can ensure a steady supply and sometimes play suppliers against each other for better pricing.
The Role of Data in Purchasing Decisions
Data-driven decisions are crucial in optimizing purchasing costs.
Analyzing market trends, supplier performance, and purchase history can lead to better-informed choices that align with long-term business goals.
Tools and technologies that provide real-time data and insights help in understanding the nuances of supply and demand, allowing for strategic planning.
Integrating Strategies for Maximum Productivity
The true secret to increasing factory productivity lies in integrating the sourcing of new materials with optimized purchasing strategies.
By viewing these processes as interconnected rather than isolated, manufacturers can experience compounding benefits.
A holistic approach ensures that new materials not only improve product offerings but also align with cost-saving strategies.
The result is a more resilient and adaptive manufacturing process capable of tackling both current and future challenges.
Implementing Change
Implementing change is never easy, but it is necessary for growth.
Employing change management principles can help in smoothly integrating new materials and purchasing strategies.
This might include gradual implementation, piloting new processes, and gathering feedback from employees at all levels.
Training and development for staff are also integral to success.
Ensuring that employees are well-equipped to handle new materials and purchasing technologies supports a seamless transition and maximizes the benefits of these new strategies.
In conclusion, the secret to boosting factory productivity lies in adapting to new materials and optimizing purchasing costs.
By embracing change and strategically planning, manufacturers can unlock new levels of efficiency and profitability.
資料ダウンロード
QCD調達購買管理クラウド「newji」は、調達購買部門で必要なQCD管理全てを備えた、現場特化型兼クラウド型の今世紀最高の購買管理システムとなります。
ユーザー登録
調達購買業務の効率化だけでなく、システムを導入することで、コスト削減や製品・資材のステータス可視化のほか、属人化していた購買情報の共有化による内部不正防止や統制にも役立ちます。
NEWJI DX
製造業に特化したデジタルトランスフォーメーション(DX)の実現を目指す請負開発型のコンサルティングサービスです。AI、iPaaS、および先端の技術を駆使して、製造プロセスの効率化、業務効率化、チームワーク強化、コスト削減、品質向上を実現します。このサービスは、製造業の課題を深く理解し、それに対する最適なデジタルソリューションを提供することで、企業が持続的な成長とイノベーションを達成できるようサポートします。
オンライン講座
製造業、主に購買・調達部門にお勤めの方々に向けた情報を配信しております。
新任の方やベテランの方、管理職を対象とした幅広いコンテンツをご用意しております。
お問い合わせ
コストダウンが利益に直結する術だと理解していても、なかなか前に進めることができない状況。そんな時は、newjiのコストダウン自動化機能で大きく利益貢献しよう!
(Β版非公開)