- お役立ち記事
- The section manager of the equipment maintenance department can’t miss it! Approaches to comply with safety standards and prevent accidents
The section manager of the equipment maintenance department can’t miss it! Approaches to comply with safety standards and prevent accidents
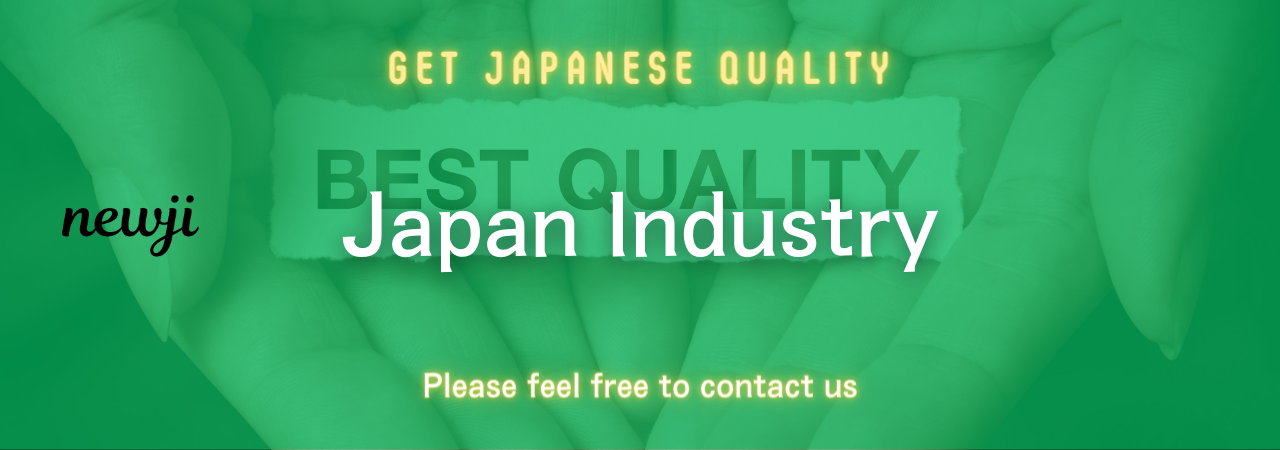
目次
Understanding Safety Standards
Safety standards play a crucial role in maintaining a safe working environment, especially in departments like equipment maintenance.
These standards are guidelines and regulations set by various authorities to ensure that workplaces pose minimal risk to employees and equipment.
For section managers, knowing the applicable safety standards is the first step in preventing accidents.
It involves understanding regulations, such as OSHA in the United States or local equivalents in other countries.
Recognizing the different categories of safety standards is important.
General industry standards often cover mechanical and physical aspects, while others may focus on chemical, electrical, or environmental risks.
Each type has specific measures and guidelines, which section managers need to integrate into their maintenance operations.
Implementing Safety Protocols
Implementing safety protocols is essential for compliance with safety standards.
This involves creating a comprehensive safety plan tailored to the specific needs of the department.
The plan should include emergency procedures, safety inspections, and routine maintenance checks.
Regular training sessions for the maintenance team are crucial to ensure everyone is up-to-date with the latest safety practices.
Section managers should also focus on communication.
Clear and open communication channels among team members help in identifying potential hazards early.
Encourage workers to report unsafe conditions without fear of retribution.
Regular safety meetings can be instrumental in discussing safety updates and reinforcing safety culture.
Equipment Inspection and Maintenance
A cornerstone of accident prevention in the maintenance department is regular equipment inspection and maintenance.
Section managers must establish a schedule for routine inspections to identify wear and tear, potential malfunctions, or any safety hazards.
Proper documentation of these inspections is vital for compliance.
Effective maintenance procedures can extend equipment life and prevent unexpected breakdowns.
It’s crucial to follow manufacturer guidelines and safety standards during equipment repairs or adjustments.
Encourage technicians to use proper tools and personal protective equipment (PPE) to minimize risks.
Training and Educating Staff
Regular training and education are key components in maintaining a safety-conscious workforce.
Section managers should develop a training program that includes both theoretical knowledge of safety standards and practical assessments.
Training should cover emergency response, the use of safety equipment, hazard identification, and the importance of PPE.
New hires require thorough orientation training to familiarize themselves with safety protocols before beginning work.
For existing staff, periodic refresher courses help reinforce their skills and keep them informed about any changes in safety standards or procedures.
Promoting a Safety Culture
Creating a strong safety culture within the equipment maintenance department is an ongoing effort.
Section managers play a pivotal role in fostering this culture by leading by example.
When managers prioritize safety, it sets the tone for the rest of the team.
Encourage a mindset where safety is everyone’s responsibility, and empower employees to take an active role in enhancing workplace safety.
Recognition of safe practices and positive reinforcement can motivate the team to remain vigilant about safety.
Utilizing Technology for Safety
Incorporating technology into safety measures can significantly enhance compliance and accident prevention.
Utilize digital platforms for maintaining records, conducting inspections, or managing maintenance schedules efficiently.
Technological tools can also be used for safety training, offering virtual simulations and interactive modules that provide hands-on experience without exposing workers to real-world risks.
Using predictive maintenance software can help anticipate failures before they happen, thereby reducing the risk of accidents.
Sensors and IoT devices can monitor equipment conditions in real time, alerting staff to potential issues immediately.
Conducting Risk Assessments
Risk assessments are essential for identifying potential hazards in the maintenance environment.
A systematic approach to risk assessments can help section managers and their teams understand where the greatest risks lie.
Begin by analyzing each maintenance task and the equipment involved to determine possible accident scenarios.
Rate the severity and likelihood of each risk, and identify control measures to mitigate them.
Continuous monitoring and regular reassessments ensure that new risks are identified and addressed promptly.
Accident Investigation and Response
Despite all precautions, accidents may still occur.
Having an effective accident investigation and response plan is necessary for minimizing damage and preventing future incidents.
When an accident occurs, the immediate response should focus on securing the area and providing aid to those affected.
After addressing immediate concerns, a thorough investigation is required to determine the root cause of the accident.
This involves collecting data, interviewing witnesses, inspecting the scene, and analyzing any equipment involved.
Once the investigation is complete, develop corrective actions to prevent recurrence.
Sharing findings and improvements with the team reinforces a culture of transparency and learning.
Conclusion
For section managers in equipment maintenance departments, staying compliant with safety standards and preventing accidents is a critical responsibility.
By understanding and implementing safety standards, fostering a safety culture, utilizing technology, and conducting thorough risk assessments, managers can effectively protect their teams and equipment.
Continuous improvement and adaptability are key to managing the ever-evolving landscape of workplace safety, ensuring that employees return home safely every day.
資料ダウンロード
QCD調達購買管理クラウド「newji」は、調達購買部門で必要なQCD管理全てを備えた、現場特化型兼クラウド型の今世紀最高の購買管理システムとなります。
ユーザー登録
調達購買業務の効率化だけでなく、システムを導入することで、コスト削減や製品・資材のステータス可視化のほか、属人化していた購買情報の共有化による内部不正防止や統制にも役立ちます。
NEWJI DX
製造業に特化したデジタルトランスフォーメーション(DX)の実現を目指す請負開発型のコンサルティングサービスです。AI、iPaaS、および先端の技術を駆使して、製造プロセスの効率化、業務効率化、チームワーク強化、コスト削減、品質向上を実現します。このサービスは、製造業の課題を深く理解し、それに対する最適なデジタルソリューションを提供することで、企業が持続的な成長とイノベーションを達成できるようサポートします。
オンライン講座
製造業、主に購買・調達部門にお勤めの方々に向けた情報を配信しております。
新任の方やベテランの方、管理職を対象とした幅広いコンテンツをご用意しております。
お問い合わせ
コストダウンが利益に直結する術だと理解していても、なかなか前に進めることができない状況。そんな時は、newjiのコストダウン自動化機能で大きく利益貢献しよう!
(Β版非公開)