- お役立ち記事
- [The type of cutting oil is the deciding factor] Improving the precision of difficult-to-cut materials by using different types of oil during prototyping
月間76,176名の
製造業ご担当者様が閲覧しています*
*2025年3月31日現在のGoogle Analyticsのデータより
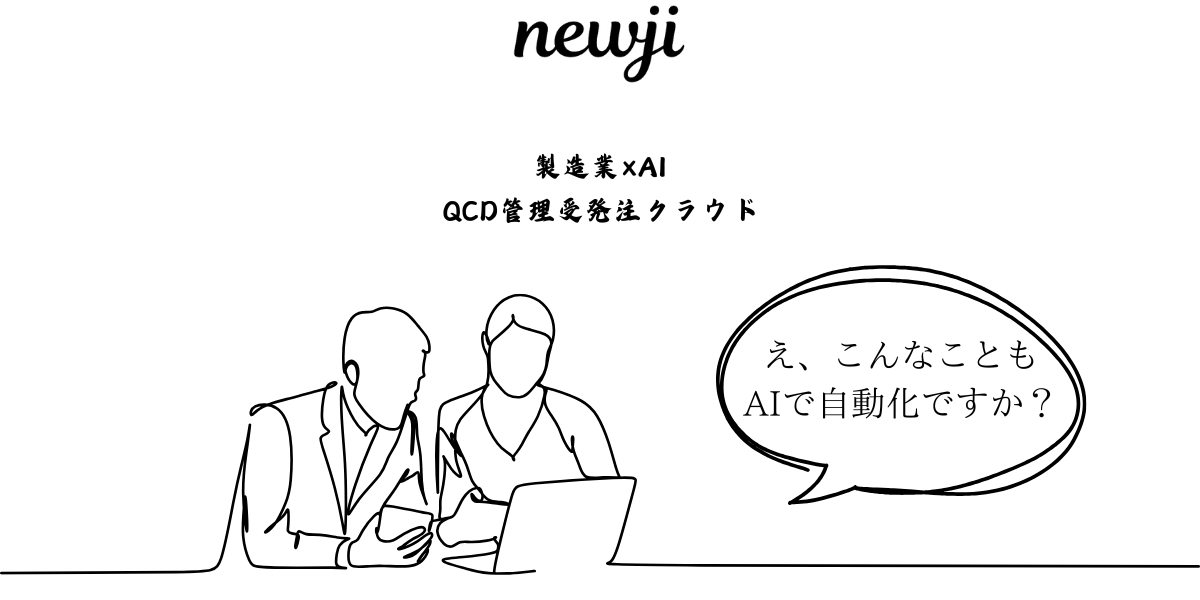
[The type of cutting oil is the deciding factor] Improving the precision of difficult-to-cut materials by using different types of oil during prototyping
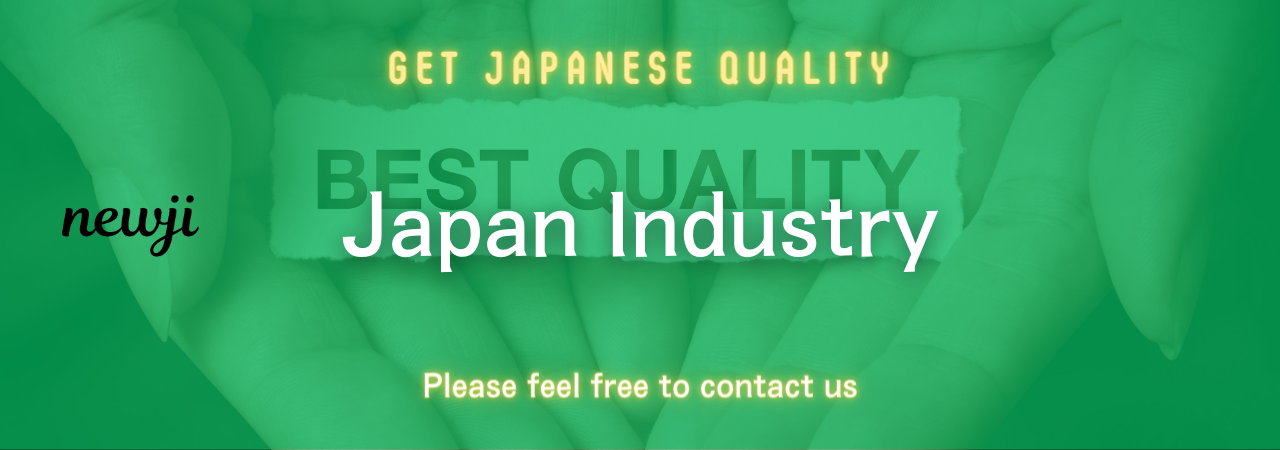
目次
Understanding Cutting Oils
Cutting oils play a crucial role in the machining process, especially when dealing with difficult-to-cut materials.
They help reduce friction, provide lubrication, and cool down the cutting surfaces, ultimately enhancing the precision of the machining process.
Selecting the right type of cutting oil can significantly impact the output quality and durability of machined products.
There are various types of cutting oils, each with distinct properties that make them suitable for different cutting tasks.
The three primary categories are mineral oils, synthetic oils, and semi-synthetic oils.
Each of these oils has its advantages and specific applications in machining.
Mineral Oils
Mineral oils are derived from refining crude oil and are among the most commonly used cutting fluids.
They are typically chosen for their excellent lubrication properties.
These oils can be straight oils, without any additives, or enhanced with special additives to improve their performance under extreme conditions.
Straight mineral oils are often used for operations that require high precision and are favored for their ability to provide superior surface finishes.
These oils are excellent for use with difficult-to-cut materials, as they help in reducing heat and wear on the cutting tool.
Additive-rich mineral oils can offer enhanced performance by including sulfur, chlorine, or phosphorus, which help improve the oil’s anti-wear and extreme pressure properties.
They are particularly useful in heavy-duty machining processes where high pressures and temperatures are involved.
Synthetic Oils
Synthetic cutting oils are chemically engineered to offer properties that natural oils cannot provide.
These oils are known for their excellent cooling capabilities, oxidation stability, and cleanliness.
They are often used in high-precision machining operations where exacting tolerances are required.
Because synthetic oils can remain stable under high temperatures, they are ideal for cutting hard-to-machine materials.
They minimize the thermal deformation of the workpiece, thus maintaining the integrity and precision of the material.
Additionally, synthetic oils are less prone to form residues, making them preferable for industries where cleanliness is critical, such as aerospace and electronics.
Semi-Synthetic Oils
Semi-synthetic oils are a blend of mineral and synthetic oils, aiming to combine the advantages of both.
These oils offer balanced lubrication and cooling properties, making them versatile for various machining operations.
Semi-synthetic oils provide better lubrication than pure synthetic oils while also offering enhanced cooling compared to straight mineral oils.
This balance makes them suitable for a wide range of applications, from simple to more complicated machining processes involving difficult-to-cut materials.
These oils are often chosen for their economic and performance advantages, providing good value while still meeting the specific demands of the machining process.
Choosing the Right Oil for Prototyping
When working with difficult-to-cut materials during the prototyping phase, selecting the right cutting oil is essential for achieving high precision and quality.
Understanding the specific requirements of the material and process is key.
For instance, if the material is sensitive to heat, a synthetic oil with superior cooling properties might be required to prevent thermal deformation.
On the other hand, if the operation involves extremely high pressures, a mineral oil enhanced with extreme pressure additives could be more effective.
It’s also important to consider the environmental and health impacts of the cutting oil chosen.
Modern manufacturing practices demand cutting oils that are not only effective but also environmentally friendly and safe for workers to handle.
Enhancing Machining Precision
Using the right type of cutting oil can greatly enhance the precision of machining difficult-to-cut materials.
Proper lubrication reduces tool wear and tear, prolonging the tool’s lifespan and ensuring that the cutting process remains accurate and consistent.
Moreover, adequate cooling prevents thermal expansion of the workpiece, maintaining the integrity of its dimensions and ensuring the final product meets precise specifications.
Machining with an unsuitable oil can lead to poor surface finishes, tool breakdowns, and inaccuracies in the final product, which could potentially lead to costly rework.
Conclusion
In conclusion, the type of cutting oil used in the machining of difficult-to-cut materials is a crucial factor determining the success of the process.
By understanding the properties and applications of each type of cutting oil, manufacturers can select the most appropriate one for their specific needs.
The right cutting oil not only helps achieve superior finishes and precision but also extends tool life and contributes to a safer working environment.
Ultimately, a careful selection and application of cutting oils can make a significant difference in the quality and efficiency of prototyping operations.
資料ダウンロード
QCD管理受発注クラウド「newji」は、受発注部門で必要なQCD管理全てを備えた、現場特化型兼クラウド型の今世紀最高の受発注管理システムとなります。
ユーザー登録
受発注業務の効率化だけでなく、システムを導入することで、コスト削減や製品・資材のステータス可視化のほか、属人化していた受発注情報の共有化による内部不正防止や統制にも役立ちます。
NEWJI DX
製造業に特化したデジタルトランスフォーメーション(DX)の実現を目指す請負開発型のコンサルティングサービスです。AI、iPaaS、および先端の技術を駆使して、製造プロセスの効率化、業務効率化、チームワーク強化、コスト削減、品質向上を実現します。このサービスは、製造業の課題を深く理解し、それに対する最適なデジタルソリューションを提供することで、企業が持続的な成長とイノベーションを達成できるようサポートします。
製造業ニュース解説
製造業、主に購買・調達部門にお勤めの方々に向けた情報を配信しております。
新任の方やベテランの方、管理職を対象とした幅広いコンテンツをご用意しております。
お問い合わせ
コストダウンが利益に直結する術だと理解していても、なかなか前に進めることができない状況。そんな時は、newjiのコストダウン自動化機能で大きく利益貢献しよう!
(β版非公開)