- お役立ち記事
- The Ultimate Guide to Manufacturing Stainless Steel Wire: Unveiling Techniques and Innovations
The Ultimate Guide to Manufacturing Stainless Steel Wire: Unveiling Techniques and Innovations
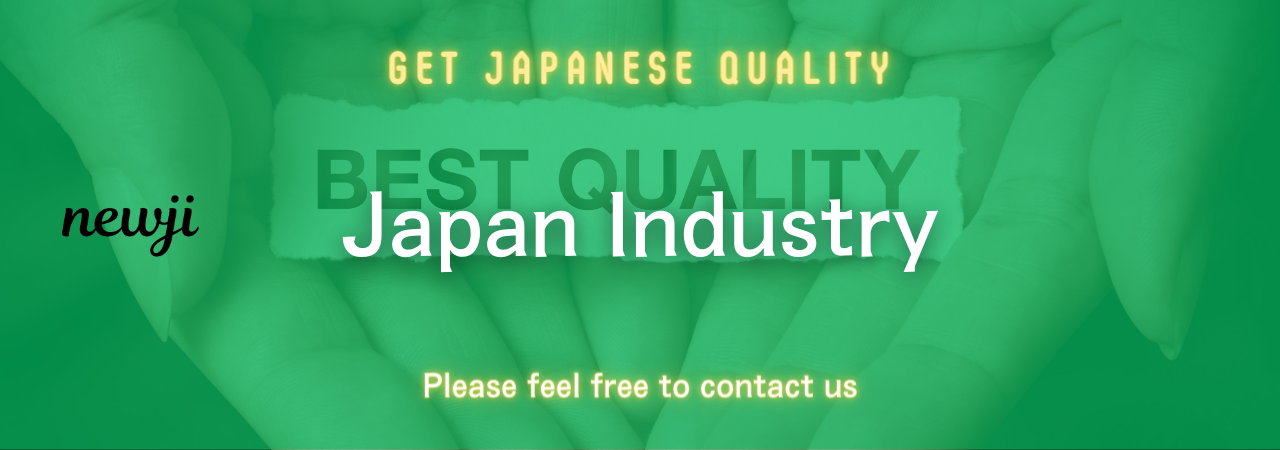
目次
Introduction to Stainless Steel Wire Manufacturing
Stainless steel wire is a crucial component in various industries, from construction to aerospace.
The manufacturing process of stainless steel wire involves numerous steps that ensure the product is strong, durable, and reliable.
In this guide, we will delve into the detailed techniques and innovative methods used in the production of stainless steel wire.
The Basic Components of Stainless Steel
Understanding the Alloy
Stainless steel is an alloy composed primarily of iron, with a significant percentage of chromium.
The chromium gives the steel its corrosion-resistant properties, which are necessary for creating durable stainless steel wire.
Other elements like nickel, molybdenum, and nitrogen can also be added to enhance specific features.
The Importance of Quality Raw Materials
The quality of the final stainless steel wire depends significantly on the raw materials used in its production.
High-grade metals and precise measurements ensure the wire will meet industry standards and perform adequately in demanding environments.
Step-by-Step Manufacturing Process
Melting and Casting
The first step in manufacturing stainless steel wire is melting the raw materials in an electric arc furnace.
This process involves heating the metals to high temperatures, allowing them to melt and combine thoroughly.
Once the metal is molten, it’s poured into a casting mold to form billets or slabs, which are then cooled and solidified.
Hot Rolling
After casting, the billets undergo hot rolling, a process where they are heated again and passed through rollers to reduce their thickness.
This step is crucial as it shapes the material into a more workable form, often called a rod.
Hot rolling also helps to eliminate any internal stresses and ensures consistency in the metal structure.
Cold Drawing
Once the rods are prepared, they undergo a process called cold drawing.
This involves pulling the rods through a series of dies to reduce their diameter and create the final wire.
Cold drawing is done at room temperature, allowing for precise control over the wire’s dimensions and properties.
Annealing
To achieve the desired mechanical properties and improve the ductility of the wire, annealing is applied.
This heat treatment involves heating the wire to a specific temperature and then cooling it slowly.
Annealing softens the wire, making it easier to work with in subsequent processes.
Surface Treatment
After annealing, the wire undergoes surface treatment to remove any scale or oxide layer formed during the manufacturing process.
Pickling, passivation, and coating are common techniques used to give the wire a clean and smooth surface.
These treatments not only enhance the appearance but also improve the wire’s resistance to corrosion.
Final Inspection and Quality Control
The final step involves a thorough inspection and quality control.
This stage ensures that the stainless steel wire meets all the specified requirements.
It includes checks for dimensions, surface finish, tensile strength, and other mechanical properties.
Once the wire passes all inspections, it is packaged and ready for delivery.
Innovations in Stainless Steel Wire Manufacturing
Advanced Metallurgical Techniques
Recent advancements in metallurgy have led to the development of specialized alloys that offer superior performance.
These innovations include the introduction of high-performance stainless steels that provide enhanced strength, corrosion resistance, and longevity.
Automation and Robotics
The integration of automation and robotics in manufacturing facilities has significantly increased production efficiency and consistency.
Automated systems can handle complex tasks with precision, reducing human error and ensuring high-quality output.
Robotic arms and automated handling systems also contribute to safer working environments.
Eco-Friendly Manufacturing
Environmental sustainability is becoming increasingly important in manufacturing.
Innovations such as energy-efficient furnaces, waste recycling, and eco-friendly pickling solutions are being adopted industry-wide.
These practices reduce the environmental footprint of stainless steel wire manufacturing and contribute to a more sustainable industry.
3D Printing and Additive Manufacturing
The advent of 3D printing and additive manufacturing has opened new avenues for creating complex wire forms.
These technologies allow for the design and production of intricate shapes that were previously difficult to achieve using traditional methods.
They offer greater flexibility and customization in wire production.
Applications of Stainless Steel Wire
Industrial Applications
Stainless steel wire is widely used in various industrial applications, including construction, automotive, and aerospace sectors.
Its strength, durability, and resistance to corrosion make it ideal for use in environments where performance is critical.
Medical and Healthcare
In the medical field, stainless steel wire is used in surgical instruments, orthopedic implants, and dental procedures.
The biocompatibility and sterilization resistance of stainless steel make it suitable for medical applications.
Consumer Goods
Household items such as kitchen utensils, appliances, and furniture often contain stainless steel wire components.
It’s valued for its aesthetic appeal and longevity, ensuring that consumer products remain functional and visually appealing over time.
Conclusion
The manufacturing of stainless steel wire is a complex process involving multiple stages and advanced techniques.
From melting and casting to cold drawing and surface treatment, each step plays a crucial role in producing high-quality stainless steel wire.
Innovations in metallurgy, automation, eco-friendly practices, and 3D printing continue to transform the industry, offering improved performance and sustainability.
Understanding these processes and staying updated with technological advancements is essential for anyone involved in the field.
Stainless steel wire’s versatility and durability ensure its continued importance across various industries.
In summary, mastering the techniques and innovations in stainless steel wire manufacturing can significantly enhance production efficiency and product quality.
資料ダウンロード
QCD調達購買管理クラウド「newji」は、調達購買部門で必要なQCD管理全てを備えた、現場特化型兼クラウド型の今世紀最高の購買管理システムとなります。
ユーザー登録
調達購買業務の効率化だけでなく、システムを導入することで、コスト削減や製品・資材のステータス可視化のほか、属人化していた購買情報の共有化による内部不正防止や統制にも役立ちます。
NEWJI DX
製造業に特化したデジタルトランスフォーメーション(DX)の実現を目指す請負開発型のコンサルティングサービスです。AI、iPaaS、および先端の技術を駆使して、製造プロセスの効率化、業務効率化、チームワーク強化、コスト削減、品質向上を実現します。このサービスは、製造業の課題を深く理解し、それに対する最適なデジタルソリューションを提供することで、企業が持続的な成長とイノベーションを達成できるようサポートします。
オンライン講座
製造業、主に購買・調達部門にお勤めの方々に向けた情報を配信しております。
新任の方やベテランの方、管理職を対象とした幅広いコンテンツをご用意しております。
お問い合わせ
コストダウンが利益に直結する術だと理解していても、なかなか前に進めることができない状況。そんな時は、newjiのコストダウン自動化機能で大きく利益貢献しよう!
(Β版非公開)