- お役立ち記事
- The Use of Statistical Quality Control (SQC) in Manufacturing Quality Assurance
The Use of Statistical Quality Control (SQC) in Manufacturing Quality Assurance
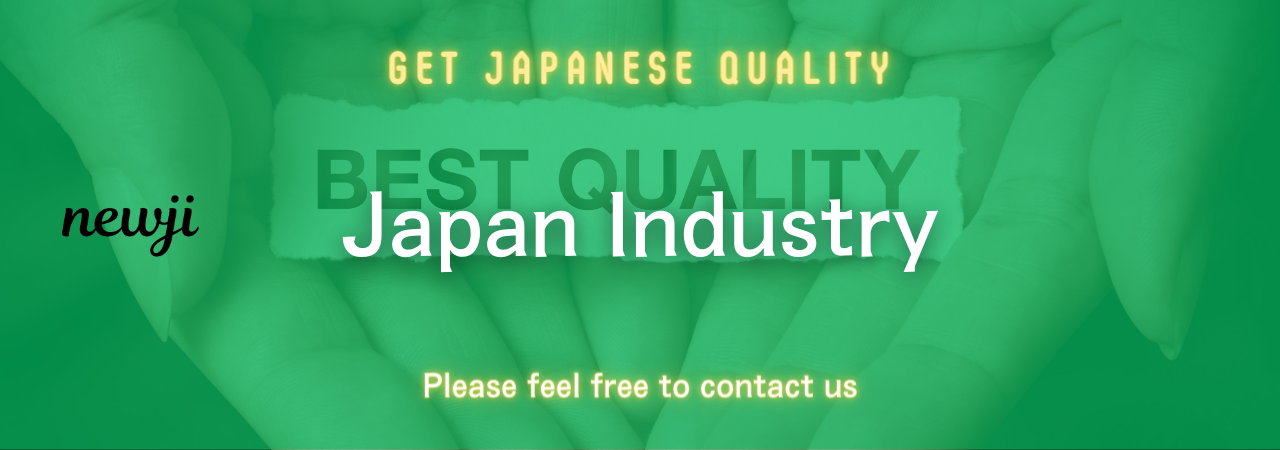
In today’s industrial landscape, ensuring the quality of manufactured products is crucial. Statistical Quality Control (SQC) offers a powerful toolkit for monitoring and maintaining this quality. SQC methodologies leverage statistical techniques to control and improve the manufacturing process. This approach not only helps in identifying defects but also aids in enhancing overall product quality.
目次
Understanding Statistical Quality Control
Statistical Quality Control is a scientific method used in manufacturing processes to ensure products meet specific quality standards. It involves the collection and analysis of data to monitor production quality. This is achieved through various statistical tools and techniques. Implementing SQC can detect problems early, reducing waste and inefficiencies.
Importance of SQC in Manufacturing
Manufacturing processes are complex and prone to variations. These variations can lead to defects and inconsistencies in the final product. By employing SQC, manufacturers can track and control these variations. This, in turn, helps maintain the highest quality standards. SQC tools also facilitate continuous improvement, making it an integral part of quality assurance.
Key Components of SQC
SQC comprises several key components that work together to ensure quality. These include control charts, process capability analysis, and design of experiments.
Control Charts
Control charts are essential tools in SQC. They display data over time and highlight any variations from the norm. By plotting data on a control chart, manufacturers can easily see when a process is going out of control. This allows for timely interventions to correct the issue. Common types of control charts include X-bar charts, R charts, and p-charts.
Process Capability Analysis
Process capability analysis evaluates the ability of a production process to produce items within specified limits. It compares the output of a process to its specifications using statistical measures. This helps in understanding whether the process is capable of producing defect-free products. Key metrics in process capability analysis include Cp, Cpk, and Ppk.
Design of Experiments (DOE)
Design of experiments involves conducting controlled tests to understand the relationship between factors affecting a process and its output. DOE helps identify the most significant variables and how they interact. By optimizing these variables, manufacturers can improve product quality and process efficiency. This systematic approach leads to data-driven decision-making, which is critical for quality assurance.
Implementation of SQC in Manufacturing
Successful implementation of SQC requires careful planning and execution. Here are some steps to ensure effective SQC deployment in manufacturing.
Define Objectives
The first step is to define clear objectives. Manufacturers must identify what they aim to achieve with SQC. This could be reducing defects, minimizing variation, or improving overall product quality. Clear goals provide direction and focus for the SQC program.
Data Collection
Accurate data collection is vital for SQC. Manufacturers need to gather data on various aspects of the production process. This includes data on raw materials, process parameters, and output quality. Reliable data is the foundation for effective statistical analysis.
Data Analysis
Once data is collected, the next step is analysis. Manufacturers should use statistical tools to analyze the data. This helps identify patterns and trends in the production process. Analyzing data also helps in pinpointing the root causes of defects and variations. This step is crucial for making informed decisions.
Implementing Changes
Based on the insights gained from data analysis, manufacturers can implement changes. These changes could involve altering process parameters or modifying production methods. The goal is to enhance process stability and improve product quality. It is important to monitor the impact of these changes to ensure they have the desired effect.
Continuous Improvement
SQC is not a one-time activity. It requires ongoing monitoring and continuous improvement. Manufacturers should regularly review and update their SQC practices. This helps in adapting to changes in the production environment and maintaining high quality standards. Continuous improvement is essential for long-term success in manufacturing.
Benefits of SQC in Manufacturing Quality Assurance
The advantages of implementing SQC in manufacturing are numerous. Here are some key benefits:
Improved Product Quality
By monitoring and controlling production processes, SQC enhances product quality. Detecting and addressing defects early ensures that the final product meets the highest standards. This results in better customer satisfaction and trust.
Reduced Costs
SQC helps identify inefficiencies and waste in the production process. By addressing these issues, manufacturers can reduce costs significantly. Lower defect rates mean less rework and scrap, leading to cost savings.
Better Decision Making
SQC provides a data-driven approach to quality assurance. Manufacturers can make informed decisions based on statistical analysis. This reduces guesswork and leads to more effective solutions.
Increased Efficiency
Efficient processes are less prone to variations and disruptions. SQC helps streamline production processes, making them more efficient. This leads to higher productivity and better resource utilization.
Compliance with Standards
Many industries have stringent quality standards. SQC helps manufacturers comply with these standards. This ensures that products meet regulatory requirements and industry benchmarks.
Conclusion
Incorporating Statistical Quality Control in manufacturing processes is essential for maintaining high-quality standards. SQC provides a structured approach to monitor and improve production quality. By leveraging statistical tools, manufacturers can detect problems early, reduce costs, and ensure customer satisfaction. Continuous improvement through SQC fosters a culture of excellence, driving long-term success in the competitive industrial landscape.
資料ダウンロード
QCD調達購買管理クラウド「newji」は、調達購買部門で必要なQCD管理全てを備えた、現場特化型兼クラウド型の今世紀最高の購買管理システムとなります。
ユーザー登録
調達購買業務の効率化だけでなく、システムを導入することで、コスト削減や製品・資材のステータス可視化のほか、属人化していた購買情報の共有化による内部不正防止や統制にも役立ちます。
NEWJI DX
製造業に特化したデジタルトランスフォーメーション(DX)の実現を目指す請負開発型のコンサルティングサービスです。AI、iPaaS、および先端の技術を駆使して、製造プロセスの効率化、業務効率化、チームワーク強化、コスト削減、品質向上を実現します。このサービスは、製造業の課題を深く理解し、それに対する最適なデジタルソリューションを提供することで、企業が持続的な成長とイノベーションを達成できるようサポートします。
オンライン講座
製造業、主に購買・調達部門にお勤めの方々に向けた情報を配信しております。
新任の方やベテランの方、管理職を対象とした幅広いコンテンツをご用意しております。
お問い合わせ
コストダウンが利益に直結する術だと理解していても、なかなか前に進めることができない状況。そんな時は、newjiのコストダウン自動化機能で大きく利益貢献しよう!
(Β版非公開)