- お役立ち記事
- Theory and Practice of Grinding Processes and Automation Technologies
Theory and Practice of Grinding Processes and Automation Technologies
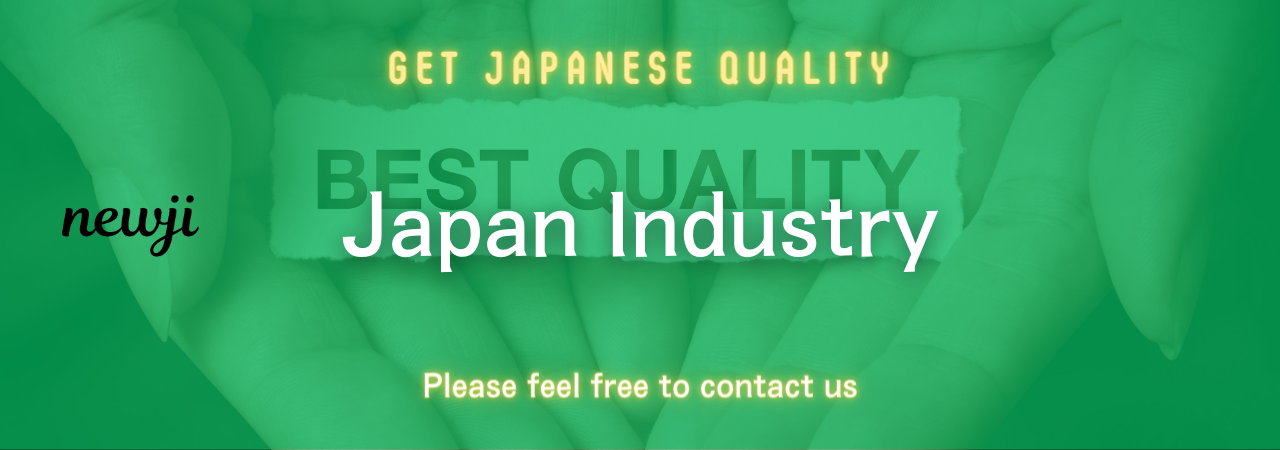
目次
Understanding Grinding Processes
Precision is key in the world of manufacturing, and one of the most important techniques to achieve this precision is grinding.
Grinding is a subtractive machining process that uses an abrasive wheel as the cutting tool.
This process can produce very smooth surfaces and fine finishes, essential for various industries, including automotive, aerospace, and electronics.
How Grinding Works
At the heart of the grinding process is the abrasive wheel.
This wheel spins at high speeds and comes in contact with the surface of the material you want to shape or smooth.
Tiny abrasive particles on the wheel remove material, much like how sandpaper works but on a much more precise scale.
The grinding wheel can be made from various materials, including aluminum oxide, silicon carbide, and diamonds.
Each type has its specific uses and advantages depending on the material being worked on.
The friction generated between the wheel and the workpiece creates heat.
Hence, a coolant is usually applied to manage the temperature and prevent damage.
Types of Grinding Processes
Numerous grinding processes cater to different needs and requirements.
Here are some of the most commonly used types:
Surface Grinding
Surface grinding involves grinding the surface of the material to make it smooth or to achieve a particular texture.
The workpiece remains stationary while the grinding wheel moves back and forth over its surface.
This is perfect for producing flat surfaces with high levels of accuracy.
Cylindrical Grinding
Cylindrical grinding is used for shaping the outside of an object.
The workpiece rotates while the grinding wheel removes material from its circumference.
This technique is ideal for creating round or cylindrical objects, such as rods and shafts.
Centerless Grinding
In centerless grinding, the workpiece is not held by any chucks or centers.
It is supported by a blade and guided between a grinding wheel and a regulating wheel.
This method is excellent for producing parts quickly and efficiently, especially when working with smaller components.
Internal Grinding
Internal grinding focuses on the inside diameter of a hole or a cylindrical cavity.
The grinding wheel is much smaller here and is inserted into the interior of the workpiece to perform its job.
This process is crucial for creating precise bores and holes in various parts.
Benefits of Grinding
The grind process offers numerous advantages that make it a go-to technique in various industries.
First and foremost, grinding can achieve extremely tight tolerances and fine surface finishes.
This makes it indispensable for high-precision components.
Another benefit is its versatility.
Grinding can work on a wide range of materials, including metals, plastics, and ceramics.
It’s also capable of removing material efficiently and quickly, making it a cost-effective solution for mass production.
Challenges in Grinding
Despite its benefits, grinding does come with its set of challenges.
One of the most common issues is the generation of excessive heat, which can damage the material.
Proper coolant application is crucial to mitigate this problem.
Another challenge is the wear and tear of grinding wheels.
Over time, abrasive particles on the wheel degrade, reducing its effectiveness.
Regular maintenance and dressing of the wheel are necessary to ensure consistent performance.
Automation Technologies in Grinding
With advancements in technology, grinding processes are becoming increasingly automated.
Automation in grinding involves using computers and robots to perform tasks that would otherwise require manual effort.
This shift not only enhances efficiency but also improves the quality of the finished product.
Computer Numerical Control (CNC) Grinding
CNC grinding is one of the most prominent examples of automation in grinding.
CNC machines use computerized controls to operate the grinding wheel and the workpiece.
This allows for extremely precise movements, producing exceptionally accurate parts.
In addition to precision, CNC grinding offers repeatability.
Once a program is set, the machine can produce identical parts repeatedly without manual intervention.
This is particularly beneficial for mass production runs.
Robotic Automation
Robotic automation is another exciting development in grinding.
Robots can handle tasks such as loading and unloading workpieces, applying coolant, and even changing grinding wheels.
This reduces the need for human intervention and increases overall productivity.
Robots are also highly adaptable.
They can be programmed to perform various tasks, making them valuable assets in a production environment that requires flexibility.
Machine Learning and Artificial Intelligence
The future of grinding processes will likely involve more advanced technologies like machine learning and artificial intelligence (AI).
These technologies can analyze vast amounts of data in real-time to optimize grinding parameters automatically.
AI can predict when a grinding wheel will wear out, allowing for preemptive maintenance and reducing downtime.
Machine learning algorithms can also improve the efficiency of the grinding process by continually learning from each operation and making adjustments to optimize performance.
Conclusion
The theory and practice of grinding are foundational to modern manufacturing.
Understanding the different types of grinding processes and their applications is crucial for achieving high-quality, precise materials.
With the advent of automation technologies like CNC grinding, robotic automation, and AI, the efficiency and precision of grinding processes are set to reach new heights.
Grinding is an indispensable technique in the manufacturing industry, providing a balance of precision, versatility, and efficiency.
As technology continues to evolve, so will the capabilities of grinding processes, making them even more integral to the future of manufacturing.
資料ダウンロード
QCD調達購買管理クラウド「newji」は、調達購買部門で必要なQCD管理全てを備えた、現場特化型兼クラウド型の今世紀最高の購買管理システムとなります。
ユーザー登録
調達購買業務の効率化だけでなく、システムを導入することで、コスト削減や製品・資材のステータス可視化のほか、属人化していた購買情報の共有化による内部不正防止や統制にも役立ちます。
NEWJI DX
製造業に特化したデジタルトランスフォーメーション(DX)の実現を目指す請負開発型のコンサルティングサービスです。AI、iPaaS、および先端の技術を駆使して、製造プロセスの効率化、業務効率化、チームワーク強化、コスト削減、品質向上を実現します。このサービスは、製造業の課題を深く理解し、それに対する最適なデジタルソリューションを提供することで、企業が持続的な成長とイノベーションを達成できるようサポートします。
オンライン講座
製造業、主に購買・調達部門にお勤めの方々に向けた情報を配信しております。
新任の方やベテランの方、管理職を対象とした幅広いコンテンツをご用意しております。
お問い合わせ
コストダウンが利益に直結する術だと理解していても、なかなか前に進めることができない状況。そんな時は、newjiのコストダウン自動化機能で大きく利益貢献しよう!
(Β版非公開)