- お役立ち記事
- Thermal Fatigue: Basics of high-temperature fatigue and techniques to ensure reliability and countermeasures.
月間77,185名の
製造業ご担当者様が閲覧しています*
*2025年2月28日現在のGoogle Analyticsのデータより
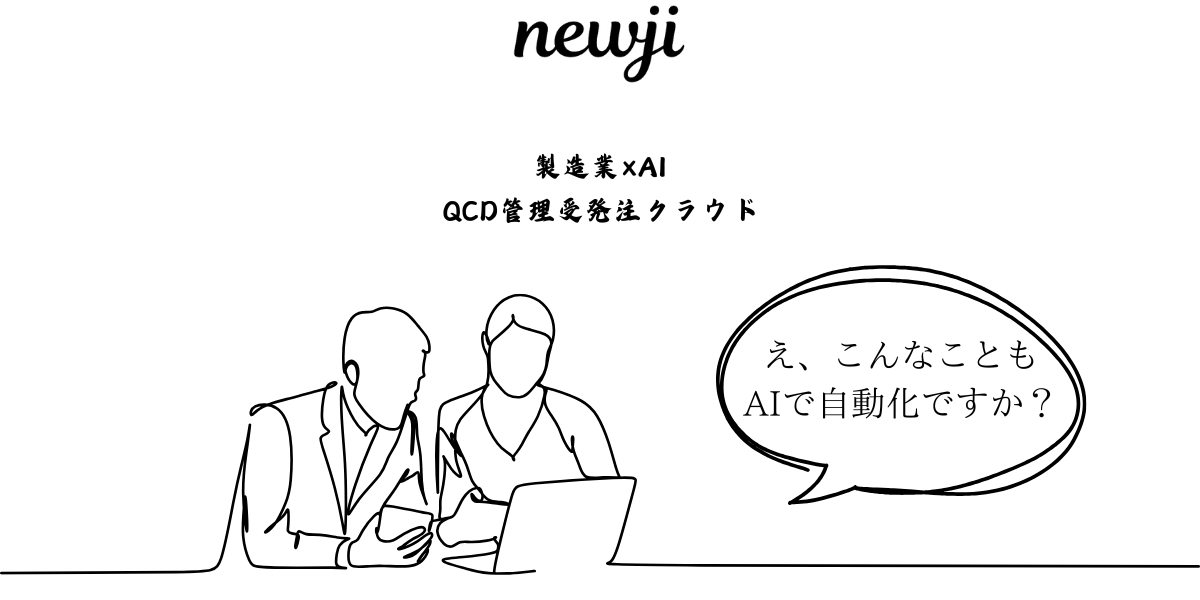
Thermal Fatigue: Basics of high-temperature fatigue and techniques to ensure reliability and countermeasures.
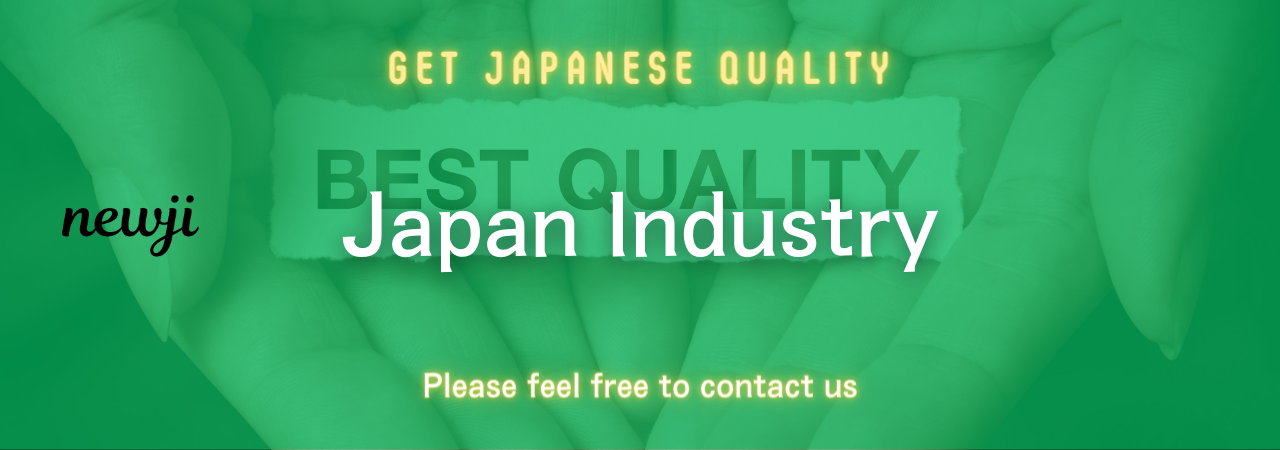
目次
Understanding Thermal Fatigue
Thermal fatigue is a phenomenon that occurs in materials exposed to cyclic changes in temperature.
This process causes materials to expand and contract, which can eventually lead to the formation of cracks and failure.
Understanding the basics of high-temperature fatigue and employing techniques to ensure reliability are critical for industries such as automotive, aerospace, and manufacturing.
What is Thermal Fatigue?
Thermal fatigue arises from the repetitive expansion and contraction of materials when subjected to fluctuating temperatures.
Each cycle of heating and cooling induces stress within the material, and over time, these stresses can cause the development of micro-cracks.
The continued exposure to cyclical temperature changes exacerbates these cracks, leading to larger fractures and ultimately, material failure.
The severity of thermal fatigue is influenced by several factors including the temperature range, the rate of temperature change, and the material type.
Common Environments for Thermal Fatigue
Several environments are particularly prone to thermal fatigue due to their inherent exposure to high or cyclic temperatures.
Industrial furnaces and engines, for instance, frequently experience temperature fluctuations.
Exhaust components in automobiles and turbines in aircraft engines are also typical examples where thermal fatigue is a concern.
These components endure extreme temperature changes daily, necessitating robust design and material selection to ensure longevity and reliability.
Factors Affecting Thermal Fatigue
1. **Temperature Range:** The greater the difference between the minimum and maximum temperatures experienced by a material, the higher the thermal stress.
Materials that can withstand broader temperature variations are less susceptible to thermal fatigue.
2. **Thermal Conductivity:** Materials with higher thermal conductivity can more evenly distribute heat, reducing stress concentrations and improving resistance to thermal fatigue.
3. **Material Composition:** Different materials have varying responses to temperature changes.
Metals such as steel and aluminum, commonly used in high-heat environments, require specific treatments or alloy compositions to enhance their thermal fatigue resistance.
4. **Cycle Frequency:** The frequency of the temperature cycles can also impact material durability.
More frequent cycling increases the likelihood of fatigue and degradation over time.
Techniques to Ensure Reliability
Industries use several methods and strategies to mitigate the risk of thermal fatigue and enhance the durability of components.
Material Selection and Design
Selecting materials that inherently possess better resistance to thermal fatigue is critical.
Using alloys with high creep resistance can significantly extend the life of components exposed to cyclic temperatures.
Moreover, designs that minimize stress concentrations, such as avoiding sharp corners and reducing thickness variations, can help distribute thermal stress more evenly.
Thermal Insulation
Employing thermal insulation is another effective technique to manage thermal fatigue.
Insulating materials can help reduce the rate of temperature change and lessen the thermal stresses involved.
This is particularly beneficial in environments where rapid temperature changes are unavoidable.
Surface Treatments and Coatings
Applying surface treatments or coatings can improve a material’s resistance to thermal fatigue.
Processes like nitriding or carburizing, which harden the surface, can enhance the wear resistance of metal parts.
Thermal barrier coatings can provide an additional layer of protection, reducing heat exposure and increasing overall component durability.
Regular Inspection and Maintenance
Incorporating a routine inspection and maintenance schedule can help identify early signs of thermal fatigue before they lead to failure.
Non-destructive testing methods, such as thermal imaging and ultrasound, can detect internal cracks and surface irregularities.
Timely repairs and part replacements based on inspection findings can prevent costly downtime and ensure operational safety.
Countermeasures for Thermal Fatigue
Industries implement various countermeasures to reduce the impact of thermal fatigue, ensuring the reliability and longevity of high-temperature components.
Design Modifications
Design modifications aim to reduce thermal stress and improve component life.
This includes changes such as using corrugated surfaces to allow for expansion, employing slots to redirect stress, and using materials with lower thermal expansion coefficients.
Advanced Manufacturing Techniques
Advanced techniques, like additive manufacturing, allow for the creation of components with complex geometries and internal structures optimized for thermal management.
These techniques offer greater flexibility in material distribution, enabling better thermal fatigue resistance.
Temperature Control Systems
Installing temperature control systems that regulate and stabilize operation temperatures can significantly reduce thermal cycling effects.
These systems enhance the ability to manage heat more efficiently, ensuring a stable working environment for sensitive components.
Proactive Monitoring
Utilizing modern monitoring tools that provide real-time data on temperature and stress cycles can aid in early detection and intervention.
Adopting predictive maintenance practices based on data analytics can preemptively address issues arising from thermal fatigue, ensuring continuous and safe operation.
In conclusion, understanding thermal fatigue and applying appropriate countermeasures is essential for industries dealing with high-temperature processes.
By integrating innovative design, material selection, and advanced technologies, thermal fatigue’s impact can be minimized, enhancing safety and reliability in critical applications.
資料ダウンロード
QCD管理受発注クラウド「newji」は、受発注部門で必要なQCD管理全てを備えた、現場特化型兼クラウド型の今世紀最高の受発注管理システムとなります。
ユーザー登録
受発注業務の効率化だけでなく、システムを導入することで、コスト削減や製品・資材のステータス可視化のほか、属人化していた受発注情報の共有化による内部不正防止や統制にも役立ちます。
NEWJI DX
製造業に特化したデジタルトランスフォーメーション(DX)の実現を目指す請負開発型のコンサルティングサービスです。AI、iPaaS、および先端の技術を駆使して、製造プロセスの効率化、業務効率化、チームワーク強化、コスト削減、品質向上を実現します。このサービスは、製造業の課題を深く理解し、それに対する最適なデジタルソリューションを提供することで、企業が持続的な成長とイノベーションを達成できるようサポートします。
製造業ニュース解説
製造業、主に購買・調達部門にお勤めの方々に向けた情報を配信しております。
新任の方やベテランの方、管理職を対象とした幅広いコンテンツをご用意しております。
お問い合わせ
コストダウンが利益に直結する術だと理解していても、なかなか前に進めることができない状況。そんな時は、newjiのコストダウン自動化機能で大きく利益貢献しよう!
(β版非公開)