- お役立ち記事
- Thermal stress basics, analysis methods, and practical points for improving strength design reliability
月間77,185名の
製造業ご担当者様が閲覧しています*
*2025年2月28日現在のGoogle Analyticsのデータより
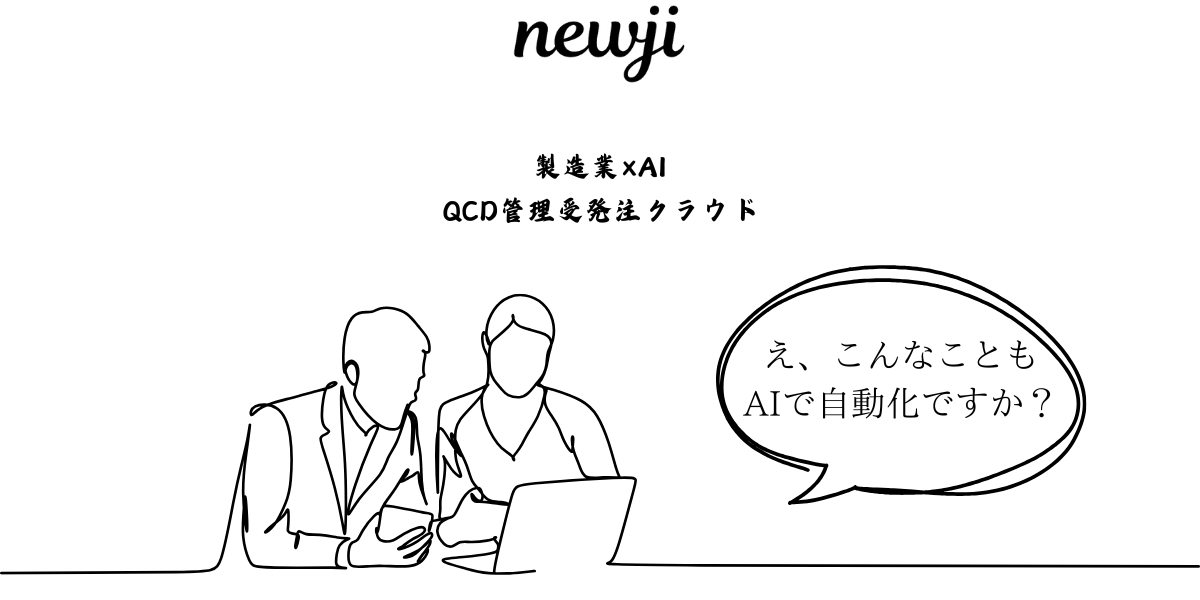
Thermal stress basics, analysis methods, and practical points for improving strength design reliability
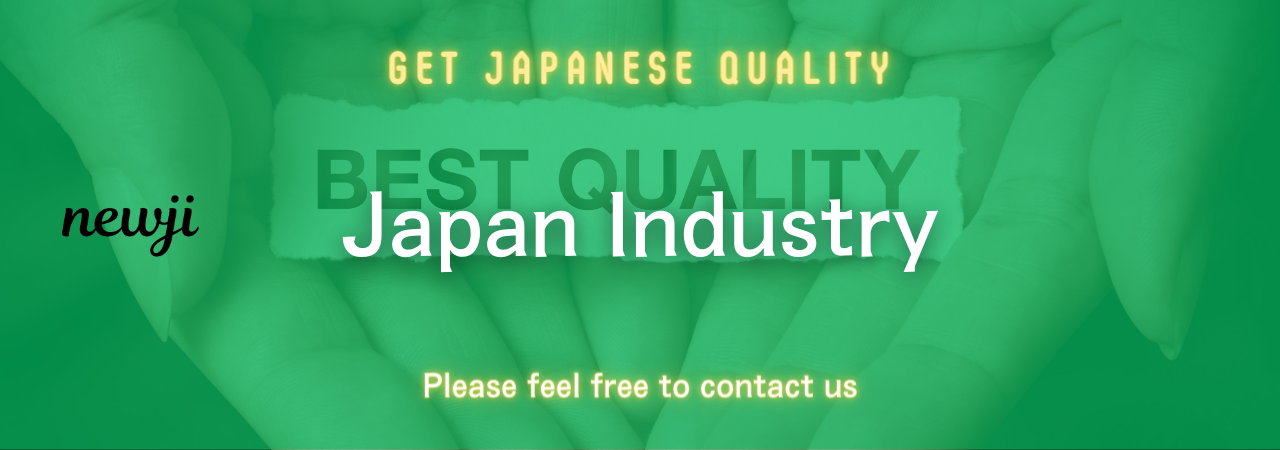
目次
Understanding Thermal Stress
Thermal stress occurs when a material experiences a change in temperature, leading to expansion or contraction.
This phenomenon can cause structural deformations or even failures if not properly managed.
It is essential to understand the fundamentals of thermal stress to develop reliable and effective designs, especially in industries such as construction, automotive, and aerospace where temperature variations are a common occurrence.
When a material is heated, the molecules within it move more vigorously, causing it to expand.
Conversely, when cooled, the material contracts.
If a structure is constrained and unable to expand or contract freely, stress will develop within the material.
The level of this stress depends on several factors, including the material’s coefficient of thermal expansion, the temperature change, and the presence of constraints.
The Importance of Analyzing Thermal Stress
Analyzing thermal stress is a crucial part of engineering and design processes.
Ignoring thermal stress can lead to damage such as cracking, warping, or even catastrophic failure in materials and structures.
By predicting how materials will react to temperature changes, engineers can create designs that are both effective and durable.
One major reason for analyzing thermal stress is to ensure structural integrity.
Over time, repeated thermal cycling (expansion and contraction due to temperature fluctuations) can weaken materials.
An advanced understanding of thermal stress enables the design of structures that accommodate expansion and contraction, minimizing the risk of failure.
Thermal stress analysis also plays a vital role in the performance of electronic devices.
Components in electronics often generate heat, and managing the thermal stress is critical in preventing damage and ensuring the longevity of the device.
Devices that overheat are not only less efficient but also prone to failure.
Methods of Thermal Stress Analysis
There are several methods available for analyzing thermal stress, each with its own strengths and applications.
Choosing the appropriate method depends on the complexity of the problem and the level of accuracy required.
Analytical Methods
Analytical methods involve using mathematical equations to predict thermal stress.
These methods are often used for simple, straight-line problems because of their efficiency.
Analytical solutions can provide a quick and general overview of expected thermal stresses, which is beneficial in the early design stages.
However, analytical methods can become complex and unwieldy for intricate geometries or composite materials where exact solutions are not easily derived.
Numerical Methods
Numerical methods, particularly the Finite Element Method (FEM), are widely used for more complex thermal stress analysis.
FEM divides a structure into smaller, manageable finite elements and then uses mathematical models to predict the stress and deformation of each element under thermal effects.
This method is highly beneficial for its precision and ability to handle complex geometries and boundary conditions.
The use of computer software makes it easier to simulate real-world scenarios and test different design conditions.
Experimental Methods
Experimental methods involve physical testing to directly observe the effects of thermal stress on materials or structures.
Techniques such as photoelasticity can be used to visualize stress patterns, while strain gauges measure deformation.
Although experimental methods can offer direct insights, they are often time-consuming and costly, making them more suitable for validating and refining the predictions generated by analytical and numerical methods.
Improving Strength Design Reliability
To improve the reliability of strength design concerning thermal stress, several practical points should be considered.
Material Selection
Choosing the right material is fundamental when addressing thermal stress.
Materials with a low coefficient of thermal expansion or those specifically designed to handle wide temperature ranges can be particularly advantageous.
Composite materials can also be tailored for improved thermal resistance, but one must consider the directional properties of these materials when making a selection.
Proper Design Techniques
Incorporating design features that allow for expansion and contraction can significantly reduce thermal stress.
This includes using expansion joints, designing flexible connections, and incorporating thermal barriers.
Another approach is to minimize the presence of sharp corners or notches in designs, as these features often become stress concentrators that can initiate material failure under thermal stress.
Regular Maintenance and Monitoring
Implementing a regular maintenance and monitoring program can help identify potential issues arising from thermal stress before they lead to damage.
Using technologies such as thermal imaging can detect regions with unusually high temperatures, helping to maintain optimal performance.
Implementing real-time monitoring systems can also alert operators to undesirable temperature rises, ensuring they can act quickly to mitigate potential failures.
Conclusion
Understanding and effectively managing thermal stress are critical components of producing reliable and durable designs.
As technology and materials continue to advance, the ability to predict and counteract the negative effects of thermal stress will become increasingly refined, ultimately leading to safer and more efficient structures and devices.
Creating a balance between the choice of materials, design strategy, and maintenance practices will ensure that thermal stress does not compromise the integrity and performance of a product or structure.
資料ダウンロード
QCD管理受発注クラウド「newji」は、受発注部門で必要なQCD管理全てを備えた、現場特化型兼クラウド型の今世紀最高の受発注管理システムとなります。
ユーザー登録
受発注業務の効率化だけでなく、システムを導入することで、コスト削減や製品・資材のステータス可視化のほか、属人化していた受発注情報の共有化による内部不正防止や統制にも役立ちます。
NEWJI DX
製造業に特化したデジタルトランスフォーメーション(DX)の実現を目指す請負開発型のコンサルティングサービスです。AI、iPaaS、および先端の技術を駆使して、製造プロセスの効率化、業務効率化、チームワーク強化、コスト削減、品質向上を実現します。このサービスは、製造業の課題を深く理解し、それに対する最適なデジタルソリューションを提供することで、企業が持続的な成長とイノベーションを達成できるようサポートします。
製造業ニュース解説
製造業、主に購買・調達部門にお勤めの方々に向けた情報を配信しております。
新任の方やベテランの方、管理職を対象とした幅広いコンテンツをご用意しております。
お問い合わせ
コストダウンが利益に直結する術だと理解していても、なかなか前に進めることができない状況。そんな時は、newjiのコストダウン自動化機能で大きく利益貢献しよう!
(β版非公開)