- お役立ち記事
- Thermoplastic elastomer processing technology that new employees in the production technology department of the medical device manufacturing industry should learn
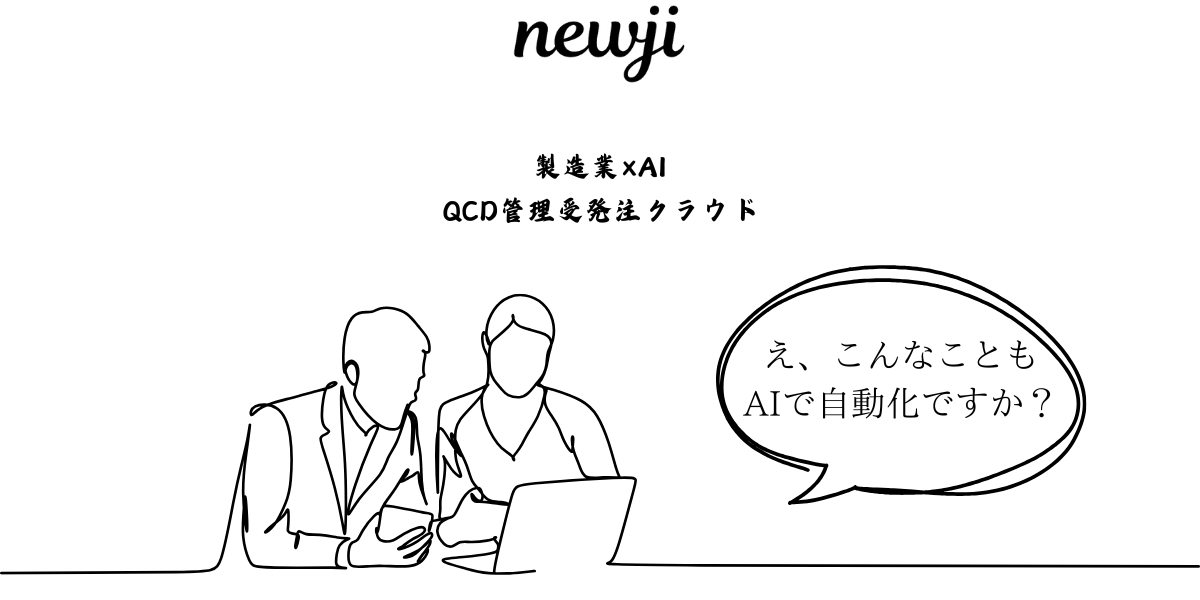
Thermoplastic elastomer processing technology that new employees in the production technology department of the medical device manufacturing industry should learn
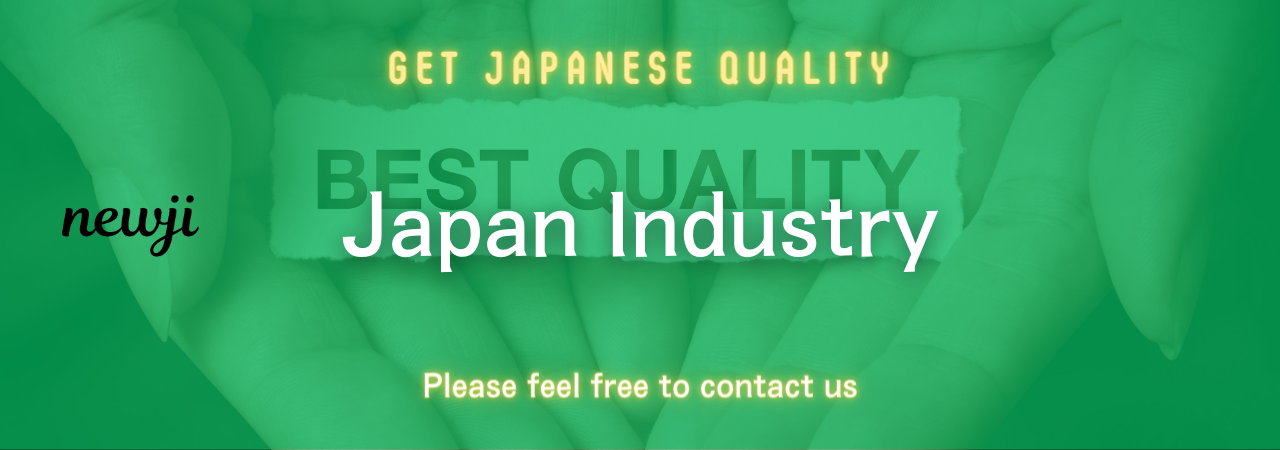
目次
Introduction to Thermoplastic Elastomers
Thermoplastic elastomers (TPEs) are a fascinating class of materials that combine the properties of both thermoplastics and elastomers.
This unique combination allows TPEs to be repeatedly stretched and return to their original shape, similar to rubber, while also being processed like plastics.
For new employees in the production technology department of the medical device manufacturing industry, understanding the processing technology of TPEs is essential.
This knowledge can help improve the quality and performance of medical devices.
Understanding Thermoplastic Elastomers
Properties of TPEs
The properties of thermoplastic elastomers make them highly desirable in various applications.
TPEs are known for their flexibility, resilience, and ability to withstand a wide range of temperatures.
They have excellent resistance to environmental factors, such as UV radiation and chemical exposure, which is crucial in the medical industry.
Their ability to be molded into complex shapes without the need for vulcanization or cross-linking also adds to their appeal.
Types of TPEs
There are several types of thermoplastic elastomers used in the medical device manufacturing industry.
These include styrenic block copolymers (SBCs), thermoplastic polyolefins (TPOs), thermoplastic vulcanizates (TPVs), and thermoplastic polyurethanes (TPUs).
Each type has its specific properties and applications.
For instance, TPUs are appreciated for their outstanding abrasion resistance and flexibility, while TPVs offer excellent elasticity and are often used in products that require long-term performance.
Importance of TPEs in the Medical Device Industry
Thermoplastic elastomers play a significant role in the medical device industry due to their versatile nature.
They are used in a variety of applications, from medical tubing and catheters to seals and gaskets.
The biocompatibility and sterilization capabilities of TPEs make them ideal for use in medical settings where hygiene and patient safety are of utmost importance.
Additionally, TPEs can be easily customized to meet specific medical performance requirements, allowing for innovation and advancement in medical device technology.
Processing Techniques for TPEs
Injection Molding
Injection molding is a common processing technique for thermoplastic elastomers.
This method involves injecting molten TPE into a mold cavity, where it cools and solidifies into the desired shape.
One of the main advantages of injection molding is its ability to produce complex parts with high precision and repeatability.
This technique is ideal for producing medical components that require intricate designs and accurate dimensions.
Extrusion
Extrusion is another widely used processing technique for TPEs.
In this process, the thermoplastic elastomer is melted and pushed through a die to create continuous lengths of a particular shape or profile.
Extrusion is especially useful for producing medical tubing and profiles that require uniform cross-sections.
It allows for efficient production of long, consistent product runs, which is essential in meeting the high demand for medical applications.
Blow Molding
Blow molding is used to fabricate hollow parts from TPEs.
This method involves creating a preform or parison of TPE, which is then inflated within a mold to form the final shape.
Blow molding is particularly valuable in manufacturing medical devices such as reservoirs, pouches, and other hollow components.
Its ability to produce lightweight, robust parts with uniform wall thickness makes it a preferred choice in certain medical applications.
Factors Affecting TPE Processing
Material Selection
Selecting the right type of thermoplastic elastomer is crucial for successful processing.
Each TPE has its unique properties, and understanding these characteristics can influence material performance and product quality.
Factors such as hardness, tensile strength, and thermal stability need to be considered when choosing a TPE for a specific medical application.
Proper material selection ensures that the finished product meets all functional and safety requirements.
Processing Conditions
Processing conditions play a pivotal role in the quality of TPE products.
These conditions include temperature, pressure, cooling rate, and cycle time.
Maintaining optimal conditions during processing is essential to avoid defects and inconsistencies in the final product.
For instance, incorrect temperatures can lead to issues such as warping, poor surface finish, or incomplete filling of molds.
Therefore, precise control of processing parameters is necessary for achieving high-quality TPE products.
Quality Control and Testing
In the medical device industry, stringent quality control and testing are critical to ensure product safety and performance.
Various tests are conducted on TPE products to evaluate their mechanical properties, biocompatibility, and resistance to environmental factors.
Testing protocols must comply with industry standards and regulations, ensuring that the final products are safe for medical use.
New employees in the production technology department should familiarize themselves with these quality control procedures to guarantee that all products meet the necessary specifications.
Conclusion
Thermoplastic elastomer processing technology is a vital aspect of medical device manufacturing.
For new employees in the production technology department, gaining a thorough understanding of TPE properties, processing techniques, and quality control measures can significantly impact the development and production of high-quality medical devices.
By mastering these skills, new employees can contribute to the advancement of innovative medical solutions that enhance patient care and safety.
資料ダウンロード
QCD調達購買管理クラウド「newji」は、調達購買部門で必要なQCD管理全てを備えた、現場特化型兼クラウド型の今世紀最高の購買管理システムとなります。
ユーザー登録
調達購買業務の効率化だけでなく、システムを導入することで、コスト削減や製品・資材のステータス可視化のほか、属人化していた購買情報の共有化による内部不正防止や統制にも役立ちます。
NEWJI DX
製造業に特化したデジタルトランスフォーメーション(DX)の実現を目指す請負開発型のコンサルティングサービスです。AI、iPaaS、および先端の技術を駆使して、製造プロセスの効率化、業務効率化、チームワーク強化、コスト削減、品質向上を実現します。このサービスは、製造業の課題を深く理解し、それに対する最適なデジタルソリューションを提供することで、企業が持続的な成長とイノベーションを達成できるようサポートします。
オンライン講座
製造業、主に購買・調達部門にお勤めの方々に向けた情報を配信しております。
新任の方やベテランの方、管理職を対象とした幅広いコンテンツをご用意しております。
お問い合わせ
コストダウンが利益に直結する術だと理解していても、なかなか前に進めることができない状況。そんな時は、newjiのコストダウン自動化機能で大きく利益貢献しよう!
(Β版非公開)