- お役立ち記事
- Thermoplastic Troubleshooting: Common Manufacturing Issues and Solutions
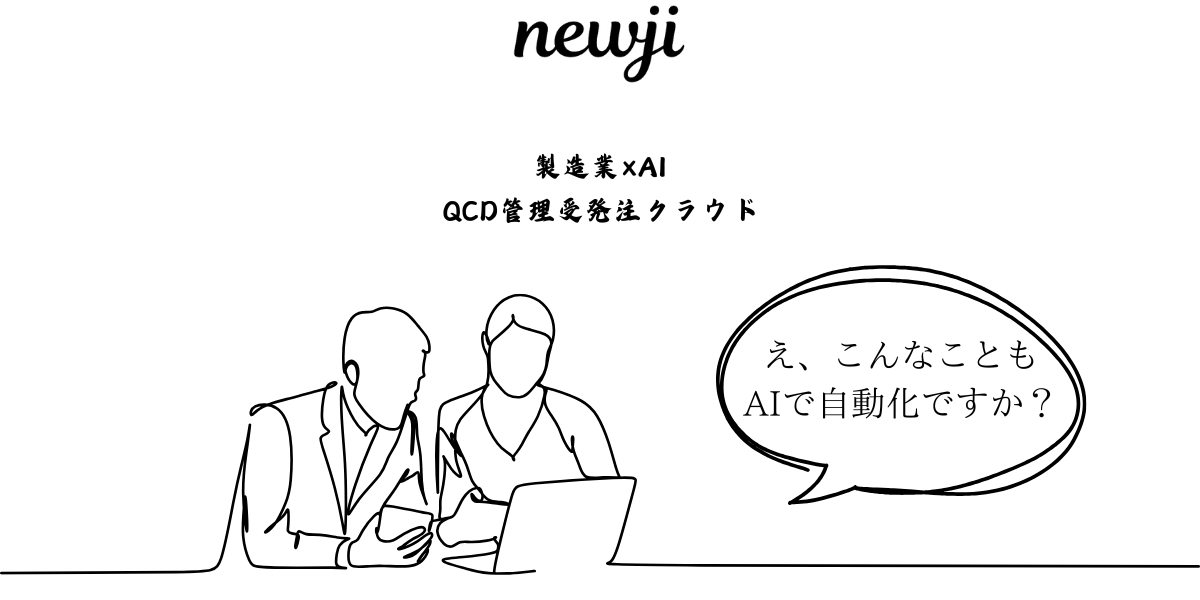
Thermoplastic Troubleshooting: Common Manufacturing Issues and Solutions
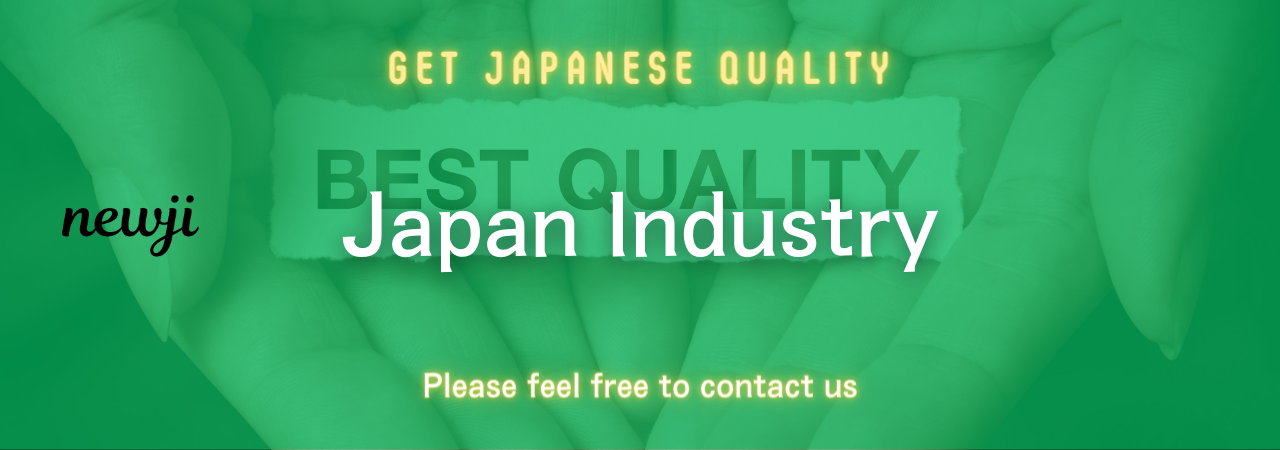
目次
Understanding Thermoplastic Manufacturing
Thermoplastics are a vital component in manufacturing due to their versatility and diverse applications, ranging from consumer goods to engineering products.
These materials can be melted and reformed, allowing for easy processing and recycling, which makes them ideal for various industries.
As demand grows, manufacturers must ensure efficient production processes to maintain quality and cost-effectiveness.
Common Manufacturing Issues
Despite their advantages, thermoplastics present specific challenges during the manufacturing process.
Identifying and addressing these issues can significantly enhance production efficiency and product quality.
1. Warping and Distortion
One of the most prevalent issues in thermoplastic manufacturing is warping or distortion, which can occur due to uneven cooling or incorrect mold design.
When thermoplastics cool unevenly, it leads to differential shrinkage rates, causing parts to warp or distort.
To mitigate this, manufacturers should focus on optimizing cooling times and ensuring uniform temperature distribution in molds.
Additionally, designing molds with even wall thickness can help prevent these issues.
2. Sink Marks
Sink marks appear as depressions or dimples on the surface of a thermoplastic product.
They usually occur in thick sections of parts where the plastic cools and contracts unevenly, leaving visible imperfections.
To resolve this problem, manufacturers should aim for uniform wall thickness or use core-out designs to minimize thick areas.
Moreover, adjusting the injection pressure and speed can help achieve a balanced filling of molds, reducing the risk of sink marks.
3. Flash
Flash occurs when excess plastic escapes the mold cavity, forming thin layers or ‘fins’ along the edges of a part.
This issue often arises from improper clamping force, high injection pressure, or worn molds.
Regularly maintaining and inspecting molds can help detect signs of wear early, preventing flash issues.
Ensure appropriate clamping force and injection pressure settings to keep the mold tightly sealed during the injection process.
4. Voids
Voids are air pockets or empty spaces within a thermoplastic part, typically caused by inadequate pressure during molding or rapid cooling of the material.
These voids can weaken the structural integrity of the product, leading to potential failure.
To avoid voids, manufacturers should increase the injection pressure and maintain consistent packing pressure to ensure complete mold filling.
Additionally, optimizing the cooling rate can help prevent the formation of voids.
5. Weld Lines
Weld lines appear where two or more plastic flows meet in the mold.
While they may not reduce structural strength significantly in some cases, weld lines often affect the appearance and can be points of weakness in high load-bearing applications.
Improving the mold design to allow smoother flow and eliminating dead zones can reduce the occurrence of weld lines.
Increasing the injection speed and temperature can also help minimize their appearance by ensuring the material remains hot and fluid when converging.
6. Bubbles and Blisters
Bubbles and blisters are caused by trapped air or gas within the thermoplastic material, often resulting from fast injection speeds or high temperatures that cause volatile substances in the resin to vaporize.
To tackle this issue, manufacturers should control injection speed and temperature settings carefully.
Using vacuum techniques during the molding process and ensuring materials are properly dried can also minimize the risk of bubbles and blisters.
Best Practices for Thermoplastic Manufacturing
Adopting best practices can help prevent common issues and improve the overall efficiency of thermoplastic manufacturing processes.
Material Selection
Selecting the right material for specific applications is crucial.
Consider the thermal properties, mechanical strength, and compatibility with molding techniques of the thermoplastic materials.
Mold Design
Investing in precise mold design and manufacturing is essential.
Experimenting with prototypes and simulations can highlight potential issues before the actual production stage, thereby saving time and resources.
Maintenance and Quality Control
Regular maintenance of equipment and molds ensures their longevity and reliability.
Implementing strict quality control measures throughout the production process can help detect and address issues proactively.
Employee Training and Expertise
Investing in employee training programs ensures that all personnel are knowledgeable about the best practices and latest advancements in thermoplastic manufacturing.
Skilled operators can effectively troubleshoot issues and optimize production quality.
Conclusion
Thermoplastic manufacturing holds immense potential, but it comes with its set of challenges.
By understanding common manufacturing issues and implementing proactive solutions, manufacturers can enhance their process efficiency and product quality.
Staying updated with the latest technological advancements and continuously refining best practices will further ensure success in the dynamic field of thermoplastic manufacturing.
資料ダウンロード
QCD調達購買管理クラウド「newji」は、調達購買部門で必要なQCD管理全てを備えた、現場特化型兼クラウド型の今世紀最高の購買管理システムとなります。
ユーザー登録
調達購買業務の効率化だけでなく、システムを導入することで、コスト削減や製品・資材のステータス可視化のほか、属人化していた購買情報の共有化による内部不正防止や統制にも役立ちます。
NEWJI DX
製造業に特化したデジタルトランスフォーメーション(DX)の実現を目指す請負開発型のコンサルティングサービスです。AI、iPaaS、および先端の技術を駆使して、製造プロセスの効率化、業務効率化、チームワーク強化、コスト削減、品質向上を実現します。このサービスは、製造業の課題を深く理解し、それに対する最適なデジタルソリューションを提供することで、企業が持続的な成長とイノベーションを達成できるようサポートします。
オンライン講座
製造業、主に購買・調達部門にお勤めの方々に向けた情報を配信しております。
新任の方やベテランの方、管理職を対象とした幅広いコンテンツをご用意しております。
お問い合わせ
コストダウンが利益に直結する術だと理解していても、なかなか前に進めることができない状況。そんな時は、newjiのコストダウン自動化機能で大きく利益貢献しよう!
(Β版非公開)