- お役立ち記事
- Thoroughly Managing Manufacturing Costs Using the Total Cost Model
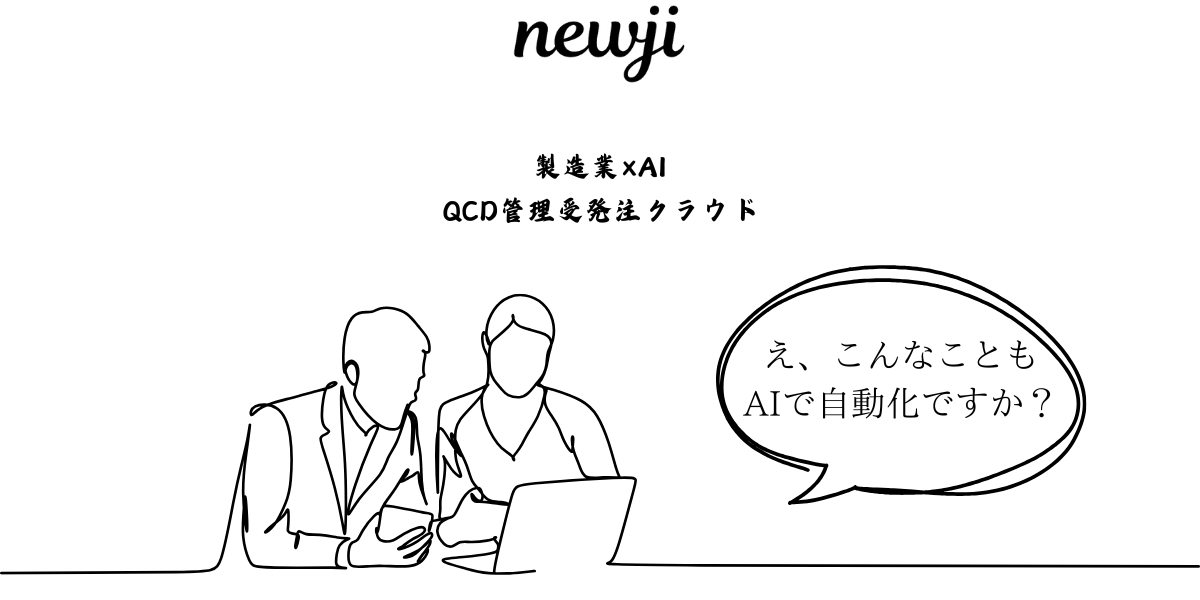
Thoroughly Managing Manufacturing Costs Using the Total Cost Model
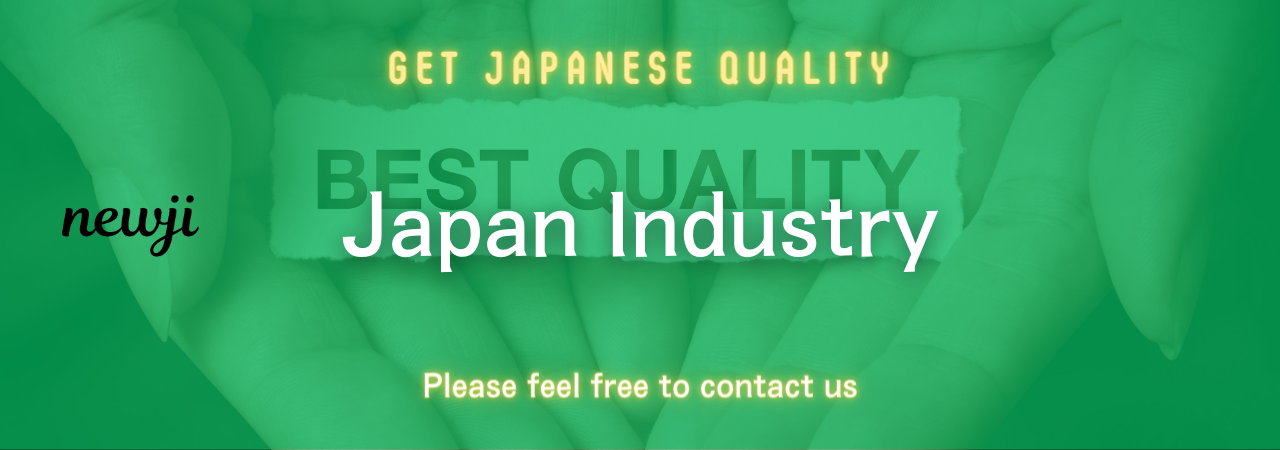
In the world of manufacturing, keeping costs under control is crucial for a business’s success.
One effective way to manage these expenses is by using the Total Cost Model.
This model helps companies understand where their money is going and how they can save more of it.
By following these guidelines, manufacturers can make smarter decisions and improve their bottom line.
目次
What is the Total Cost Model?
The Total Cost Model is a method that allows businesses to calculate all the costs associated with manufacturing a product.
This includes direct costs like materials and labor, as well as indirect costs such as overhead and maintenance.
By tallying up these expenses, manufacturers get a clear picture of what it truly costs to produce their items.
Why is the Total Cost Model Important?
Managing costs effectively is essential for staying competitive.
With the Total Cost Model, companies can identify areas where they might be overspending.
This knowledge enables them to make adjustments that can lead to significant savings.
For example, if a business discovers that they are paying too much for raw materials, they can look for alternative suppliers or negotiate better prices.
Boosting Profit Margins
One of the primary goals of any business is to increase profit margins.
By understanding all the costs involved in manufacturing, companies can set more accurate prices for their products.
This ensures that they are not only covering their expenses but also making a profit.
In turn, this makes the business more sustainable and able to grow.
Improving Efficiency
The Total Cost Model also helps identify inefficiencies in the production process.
For instance, if labor costs are higher than expected, it could mean that workers are spending too much time on certain tasks.
By pinpointing these issues, businesses can streamline their operations, reducing waste and boosting productivity.
Components of the Total Cost Model
To effectively use the Total Cost Model, it’s essential to understand its components.
Here are the key elements to consider:
Direct Costs
Direct costs are those that can be directly linked to the production of a product.
They include:
– **Materials**: The raw materials used to create the product.
– **Labor**: The wages paid to workers who are directly involved in manufacturing.
Understanding direct costs is crucial as they often make up a significant portion of the total expenses.
Indirect Costs
Indirect costs are expenses that are not directly tied to the production process but still contribute to the overall cost.
These can be more challenging to quantify but are equally important.
They include:
– **Overhead**: Costs like utilities, rent, and administrative salaries.
– **Maintenance**: Expenses related to keeping equipment in good working condition.
Other Considerations
There are additional factors that might influence the total cost, such as:
– **Shipping and Handling**: The cost of transporting materials and finished products.
– **Insurance and Taxes**: Various insurances and taxes that a business must pay.
Implementing the Total Cost Model
To put the Total Cost Model into practice, companies need to follow a structured approach.
Here are some essential steps:
1. Gather Data
The first step is collecting all relevant data.
This includes invoices, receipts, and payroll records.
Accurate data is vital for precise calculations.
2. Categorize Costs
Once the data is collected, the next step is to categorize the costs into direct and indirect expenses.
This helps in understanding where the money is going and makes it easier to analyze.
3. Calculate Total Costs
After categorizing, sum up all the costs.
This will give you the total cost of manufacturing a product.
It’s essential to be as detailed as possible to ensure accuracy.
4. Analyze and Adjust
With the total cost calculated, analyze the data to find areas where you can reduce expenses.
For instance, look for ways to cut down on material costs or improve labor efficiency.
Implement changes and monitor the results to see if they lead to savings.
Advantages of Using the Total Cost Model
There are numerous benefits to adopting the Total Cost Model in manufacturing:
Informed Decision Making
Having a clear understanding of all costs allows manufacturers to make informed decisions.
They can accurately price their products, plan budgets, and forecast future expenses.
This helps in setting realistic financial goals and avoiding unexpected expenses.
Improved Negotiations
With detailed cost data, businesses are in a better position to negotiate with suppliers.
They can push for better deals on materials and services, leading to cost savings.
Enhanced Competitiveness
By controlling costs, companies can offer competitive prices for their products without compromising on quality.
This makes them more attractive to customers and increases their market share.
Challenges in Using the Total Cost Model
While the Total Cost Model offers many benefits, it also comes with challenges.
Here are some potential issues to be aware of:
Data Accuracy
The model relies heavily on accurate data.
Any errors or omissions can lead to incorrect calculations.
It’s crucial to maintain accurate records and regularly update the data.
Time-Consuming
Calculating total costs can be a time-consuming process, especially for large operations.
It requires careful planning and coordination.
However, the benefits often outweigh the time invested.
Complexity
The Total Cost Model can be complex, particularly when dealing with indirect costs.
Businesses may need the help of accountants or financial experts to ensure accurate calculations.
Despite these challenges, the Total Cost Model remains a powerful tool for managing manufacturing costs.
By carefully implementing it, businesses can achieve significant savings and improve their overall efficiency.
In summary, the Total Cost Model is an invaluable asset for manufacturers looking to control their expenses.
By providing a comprehensive view of all costs, it enables businesses to make informed decisions and enhance their profitability.
Although it requires time and effort, the benefits it offers make it well worth the investment.
資料ダウンロード
QCD調達購買管理クラウド「newji」は、調達購買部門で必要なQCD管理全てを備えた、現場特化型兼クラウド型の今世紀最高の購買管理システムとなります。
ユーザー登録
調達購買業務の効率化だけでなく、システムを導入することで、コスト削減や製品・資材のステータス可視化のほか、属人化していた購買情報の共有化による内部不正防止や統制にも役立ちます。
NEWJI DX
製造業に特化したデジタルトランスフォーメーション(DX)の実現を目指す請負開発型のコンサルティングサービスです。AI、iPaaS、および先端の技術を駆使して、製造プロセスの効率化、業務効率化、チームワーク強化、コスト削減、品質向上を実現します。このサービスは、製造業の課題を深く理解し、それに対する最適なデジタルソリューションを提供することで、企業が持続的な成長とイノベーションを達成できるようサポートします。
オンライン講座
製造業、主に購買・調達部門にお勤めの方々に向けた情報を配信しております。
新任の方やベテランの方、管理職を対象とした幅広いコンテンツをご用意しております。
お問い合わせ
コストダウンが利益に直結する術だと理解していても、なかなか前に進めることができない状況。そんな時は、newjiのコストダウン自動化機能で大きく利益貢献しよう!
(Β版非公開)